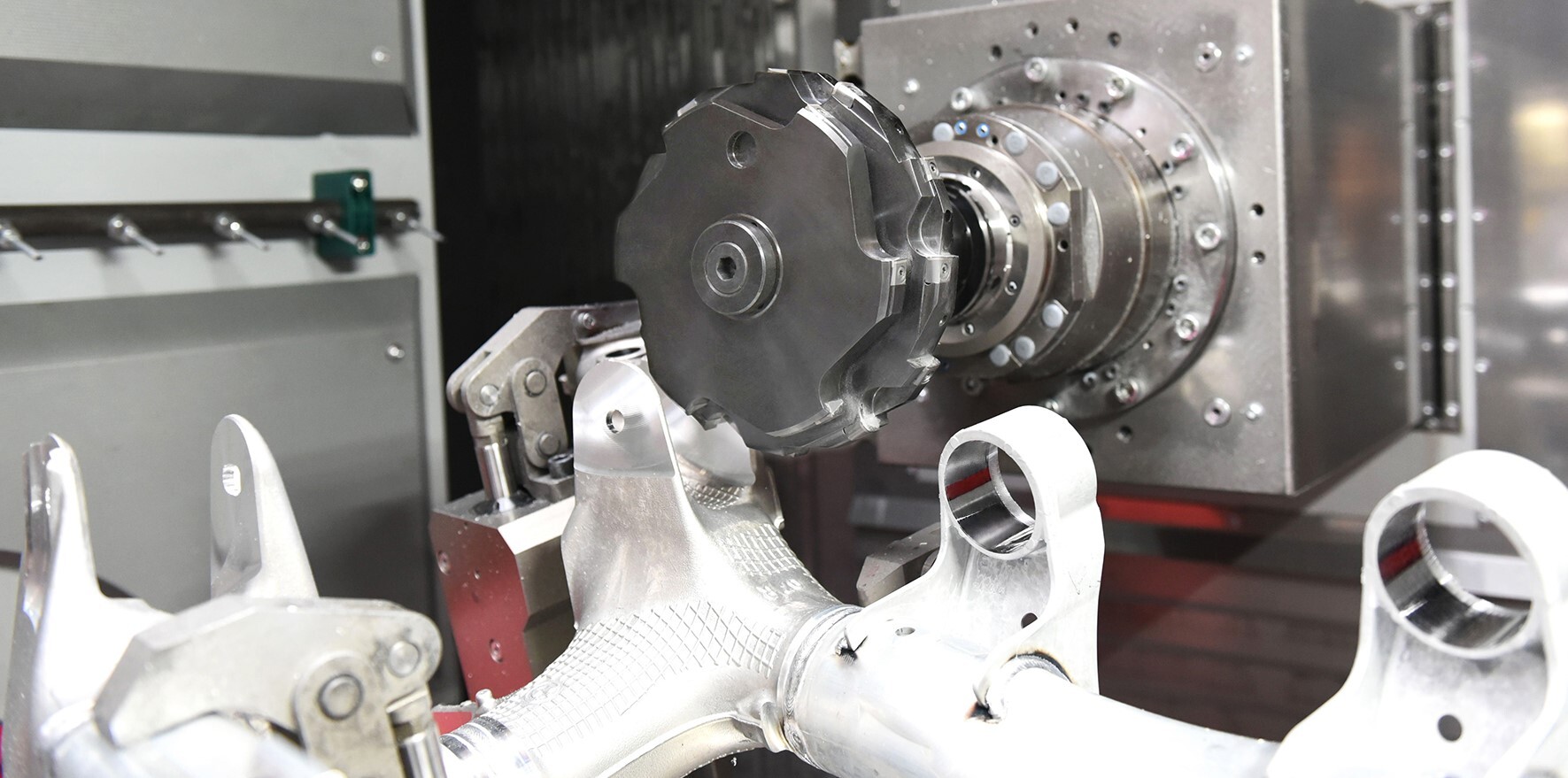
Leichtbau, komplexe Bearbeitungsstrategien, E-Mobilität – die Welt der Metallzerspanung ist extrem innovativ und unterliegt dem stetigen Wandel und den immer höher werdenden Anforderungen der Automobilisten. Zwei Unternehmen mit Tradition, die den Sprung in die Zukunft schaffen: Der Maschinenbauer Fill aus dem österreichischen Gurten und Werkzeughersteller Gühring, Experte im Bereich OEM-Projektierung und Sonderwerkzeuge. Mit spezialisierten Sondermaschinen und integrierten Werkzeuglösungen werden Fahrwerksteile aus AlSi9 prozesssicher und wirtschaftlich gefertigt.
„Wir haben das richtige Maschinenportfolio für die Bearbeitung großer Strukturbauteile und Gühring, mit seinem Tochterunternehmen Hollfelder-Gühring, das passende Werkzeug“, so simpel klingt es, wenn Produktmanager Markus Gadringer über die Zusammenarbeit beider Unternehmen spricht. Fill, das ist ein Maschinenbauer aus Gurten in Österreich, gegründet 1966 als „Schlossereibetrieb mit Tankstelle“ wie Gadringer erzählt. Ganz in der Nähe ist Ski-Fischer ansässig, bis heute führend im Skisport. Von Fischer hat Fill den Auftrag für den Bau der ersten Skiproduktionsmaschine erhalten. „Wir sind im Sondermaschinenbau groß geworden. Und haben hier gelernt, Lösungen zu suchen, die es noch nicht gibt“, sagt Stefan Frauscher, bei Fill für die Werkzeugauslegung verantwortlich. Diese Lösungskompetenz hat Fill über die Jahre perfektioniert.
Am Markt ist das Familienunternehmen als extrem innovativ und zukunftsorientiert bekannt. Das Portfolio gliedert sich in fünf Geschäftsbereiche: Automotive, Aerospace, Sport, Holz & Bau und Digitalisierung. Der Geschäftsbereich Automotive und die Sparte Metallzerspanungstechnik wuchsen aus der jahrelangen Erfahrung im Gießerei-Sektor.
Know-how, das laut Fill bis heute bei gewissen Bauteilen den entscheidenden Wissensvorsprung bringt. Wo zu Beginn noch einfache Vorbearbeitungen abgedeckt wurden, steht Fill heute als Spezialist für den Sondermaschinen- und Anlagenbau. Im Fill Kompetenz Center Metallzerspanungstechnik entstand ergänzend die Standardmaschinen-Baureihe syncromill, welche sich mittlerweile bei vielen Anwendungen zu einer Branchen-Benchmark entwickelt hat. An Fills Seite ist der Partner Gühring, der sich als OEM für kundenspezifische Sonderlösungen etabliert hat.
syncromill d22-100 für die Bearbeitung großer Bauteile
Der Auftrag für die Bearbeitung von Achsträgern kam über einen asiatischen Automobilisten zu Fill. Die Anforderungen waren enorm: Im Gegensatz zu eher kompakten Bauteilen, wie beispielsweise Motorblöcken, sind Achsträger sehr verwinkelt, wodurch die Zugänglichkeit und Aufspannung schwieriger ist. Gefordert sind Werkzeuge mit positiver Schneidengeometrie, um die Schnittkräfte und somit auftretenden Schwingungen zu reduzieren. In diesem Fall sind das die Satzfräser mit Tangentialplatten von Hollfelder-Gühring, idealerweise eingesetzt auf einer Maschine mit extrem steifem Aufbau für enorme Zerspanleistung.
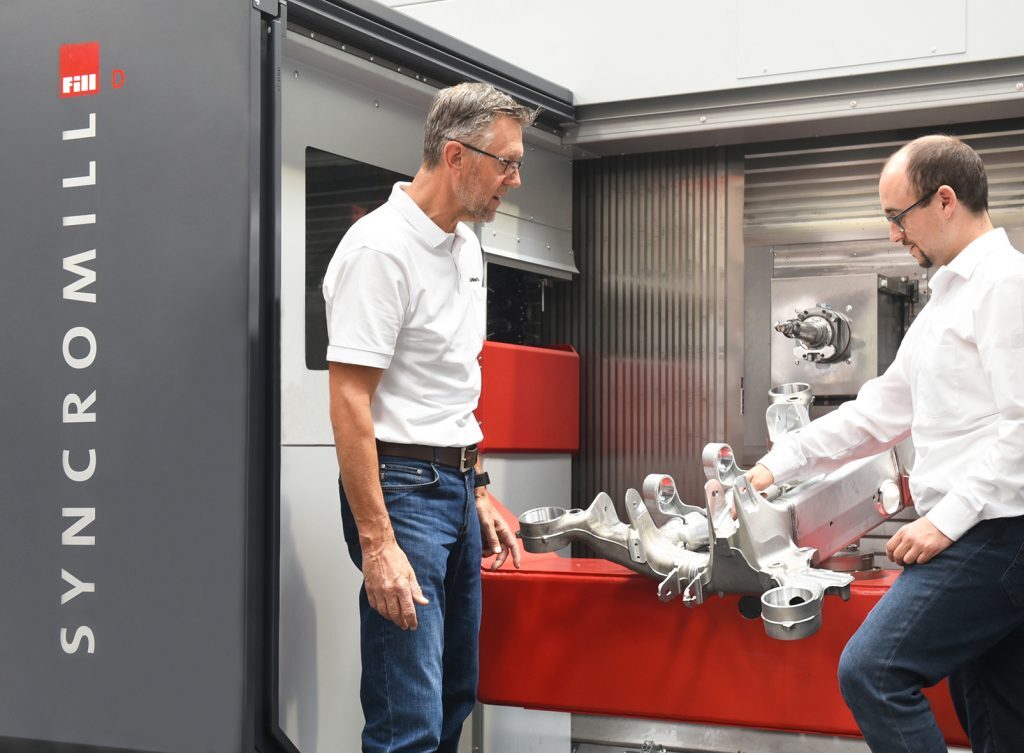
Zwei Unternehmen mit einer Vision: Gühring- Anwendungstechniker Klaus Schwörer (li.) und Werkzeugspezialist Stefan Frauscher (re.) von Fill.
Am Bauteil dürfen keine Vibrationen entstehen, damit die Flächen sauber sind und die Bearbeitungstoleranzen eingehalten werden können. Die syncromill d erfüllt diese Anforderungen: Das Werkstück wird mit Hilfe eines Rundtisches im Bearbeitungsraum positioniert, die Werkzeugspindel in X-, Y- und Z-Richtung. Durch die variable Positionierung des Rundtisches (A/B-Achse) kann eine Vielzahl unterschiedlicher Bearbeitungen abgedeckt werden. Das seitlich angeordnete Werkzeugmagazin ermöglicht neben kurzen Span-zu-Span-Zeiten auch beste Zugänglichkeit. Ob Achsträger, Fahrzeugstrukturbauteile, Fahrwerksteile oder Batteriewannen: Das Fill-Bearbeitungszentrum syncromill d22-100 wird eingesetzt, wenn präzise und platzsparende Bearbeitungen von großvolumigen Bauteilen in Verbindung mit intelligenten Spann- und Werkzeugkonzepten unter Berücksichtigung von cost-per-part durchgeführt werden müssen.
Das Werkzeugkonzept von Gühring
syncromill d22-100: das steht für zwei separate Bearbeitungsräume mit je einem Rundtisch und einer Bearbeitungsspindel mit HSK-100 Werkzeugschnittstelle. Eine präzise und stabile Aufspannung des Bauteils sowie eine hohe Maschinendynamik waren im Falle der Achsträgerbearbeitung wichtig, um große Satzfräser mit einem Werkzeug-Durchmesser von bis zu 255 mm und einem Gewicht von 20 Kilogramm aufzunehmen. Diese Satzfräser von Hollfelder-Gühring kommen neben 32 weiteren Werkzeugen bei der Bearbeitung zum Einsatz.
Der Achsträger besteht aus vier miteinander verschweißten Gussknoten, wobei Fill hier bereits die Schweiß-Vorbearbeitung übernimmt. Zur Minimierung der Taktzeit wird in einer Aufspannung und vornehmlich mit Kombinationswerkzeugen bearbeitet, die mehrere Bearbeitungsschritte abdecken. 95 % der hier von Gühring ausgelegten Werkzeuge sind Sonderwerkzeuge. Mit den Satzfräsern von Hollfelder-Gühring ist die Zerspanung großer Radien möglich. So auch beim Achsträger mit 25 mm Schnittbreite am Grund. Durch die Kombination mehrerer Bearbeitungsschritte in einem wird die Bearbeitungszeit verkürzt, PKD-bestückte Schneidplatten sorgen für lange Standzeiten. Der Satzfräser kombiniert das beidseitige Fräsen von zwei Laschen in einem Schnitt. Durch die richtige Schneidenanordnung stabilisiert sich das Bauteil, die Laschen beginnen nicht zu flattern oder zu schwingen. Das alles bei großer Genauigkeit unter Berücksichtigung der geforderten Toleranzen. Durch die Schneidengeometrie wird eine gratarme Bearbeitung begünstigt.
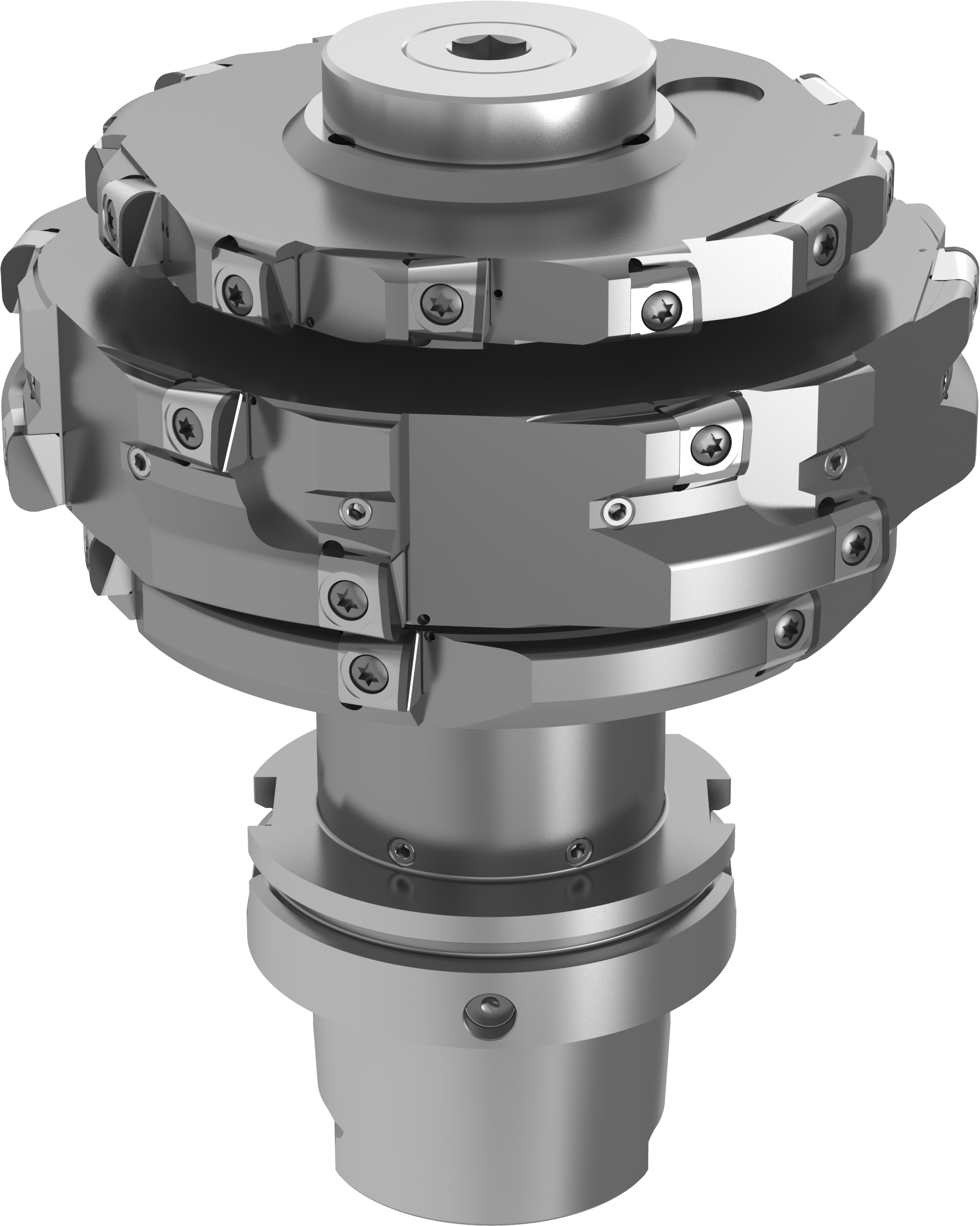
Tangential angeordnete Schneidplatten vs. konventionelle Schneidenanordnung
Die Anordnung der Tangentialplatten im Werkzeug unterscheidet sich grundlegend von der Anordnung der Schneiden konventioneller Wendeschneidplatten. Durch die tangentiale Anordnung der Wendeschneidplatten am Umfang des Grundkörpers bleibt ein großer und stabiler Werkzeugkern, der die Stabilität und die Präzision des Werkzeugs erhöht. Schwingungen werden dadurch reduziert, was zu einer hohen Prozesssicherheit und präzisen Arbeitsergebnissen führt.
Der Hartmetallquerschnitt in Schnittrichtung ist deutlich größer, dadurch wird der Plattensitz gegebenenfalls bei Verschleiß oder Ausbrüchen geschützt. Der maximale Hartmetallquerschnitt ermöglicht so höhere Vorschübe als mit konventionellen Wendeschneidplatten. Die tangentiale Anordnung erlaubt zudem eine höhere Schneidenzahl pro Werkzeug, was das Zeitspanvolumen des Werkzeugs weiter begünstigt. Durch die engere Schneidenteilung können die Schnittkräfte gezielt auf die verschiedenen Schneiden verteilt werden. Der Verschleiß wird minimiert.
Perfektes Zusammenspiel für die Zukunft
Fill erfüllt den Anspruch, bei allen Aufträgen in Turnkey-Lösungen zu denken. Das umfasst verschiedenste Prozessschritte vom Rohgussteil bis zum bearbeiteten, gereinigten, geprüften und montierten Fertigteil. Um die Form- und Lagetoleranzen einzuhalten, ist das perfekte Zusammenspiel von Maschine, Aufspannung und Werkzeug essentiell. „Wichtig ist, dass beide Seiten sich verstehen und wissen, was gebraucht wird“, sagt Stefan Frauscher. Durch die jahrelange Kooperation der Unternehmen Fill und Gühring existiert bereits eine enorme Wissensbasis, die mit jedem Projekt weiter wächst. So sei es bei neuen Projekten einfacher, oben aufzusetzen. Die Bearbeitung des Achsträgers funktionierte dank Maschinen- und Werkzeugkonzept auf Anhieb. Dabei konnten letztlich höhere Schnittwerte gefahren werden als berechnet.
Derzeit arbeitet Fill an einer neuen Generation der syncromill d mit modularem Aufbau. Gühring wird den Maschinenbau-Spezialisten aus Gurten sicher erhalten bleiben: „Die OEM-Betreuung funktioniert sehr gut. Flache Hierarchien bei Gühring sorgen für schnelle Entscheidungswege, wenn es mal brennt,“ freut sich Produktmanager Markus Gadringer auf zukünftige spannende Projekte gemeinsam mit Partner Gühring.
Technische Beratung und Support erhalten Sie auch schnell und direkt über unsere Service-Hotline 00800 2607 2607. Auch auf WhatsApp sind wir für Sie erreichbar: +49 172 658 53 53. Gleich einspeichern!
Das könnte Sie auch interessieren:
Dieser Tieflochbohrer revolutioniert die Gusszerspanung
Wo tiefe Bohrungen in Teile des Antriebsstranges eingebracht werden sollen, sind diese Werkzeuge die Spezialisten. Doch nicht nur ein großer Durchmesserbereich lässt sich mit den Vierschneidern herstellen, sondern auch Bohrtiefen von bis zu 40xD.
„License to mill“: Bond-Car aus dem Vollen gefräst
Wenn die besten Produkte zusammenkommen, entsteht ein perfekter Prozess. So haben Gühring und Blaser ein MQL-Öl mit einem VHM-Eckradienfräser und einer Werkzeugaufnahme kombiniert. Das Ergebnis zeigt, welche Vorteile gemeinsames Engineering bringt.
Späne kontrollieren: 3D-Werkzeug löst scheinbar Unmögliches
Der komplizierte Abtransport von Spänen aus einem Aluminium-Bauteil stellt den Automobilzulieferer Handtmann vor Probleme. Gühring liefert die Lösung mit einem PKD-Aufbohrwerkzeug aus dem 3D-Drucker.