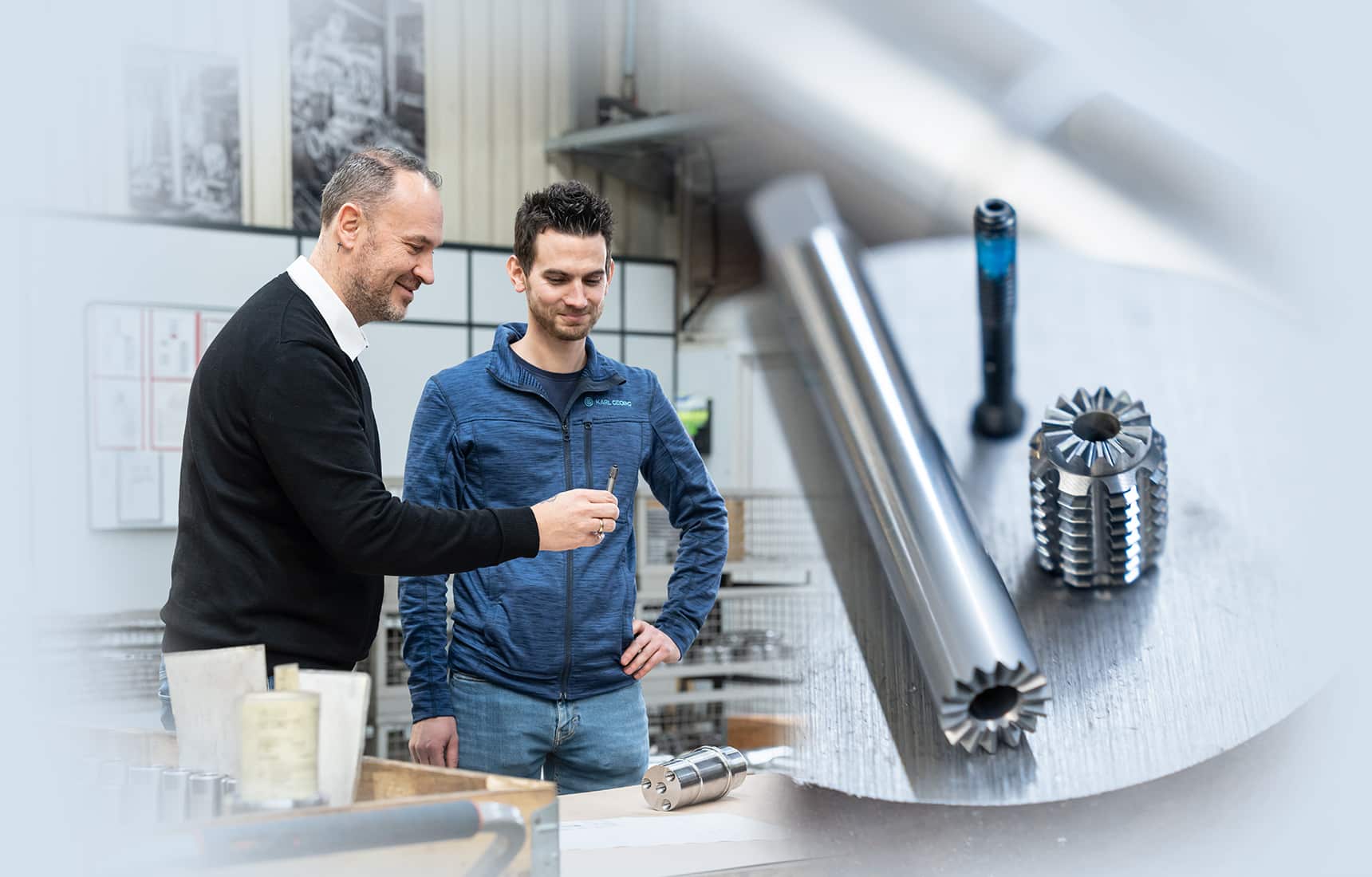
Begeistert vom neuen modularen Gewindeformer sind Marcel Horn (GÜHRING, links) und Philipp Hüsch (Karl-Georg).
Eine Innovation – der neue modulare Gewindeformer von Gühring – hat es ermöglicht, tief liegende Herausforderungen in der Herstellung von Sacklochgewinden bei Karl Georg zu lösen und die Prozesssicherheit auf ein neues Niveau zu heben.
Inhalt
Präzision und Prozesssicherheit im Fokus
Spanabfuhr aus tiefen Sacklöchern
Die Lösung: Der modulare Gewindeformer
Sicher und schnell: Gewindeformen stattbohren
Ein starkes Team für große Aufgaben
Fazit: Ihre Vorteile mit dem modularen Gewindeformer
FAQ: Die wichtigsten Fragen zum Formen von Sacklochgewinden
Präzision und Prozesssicherheit im Fokus
Im Hafen, wo tonnenschwere Container von gigantischen Kranen bewegt werden, hängt alles an der Präzision: Zahnräder greifen ineinander, Wellen treiben an, und jedes einzelne Bauteil muss höchste Belastungen aushalten. Doch so imposant diese Maschinen wirken, so entscheidend ist auch die Präzision im Kleinen.
„Unsere Maschinen bearbeiten Werkstücke in Größenordnungen von 20 Millimetern bis 1400 Millimetern – da steckt viel Know-how dahinter“, erzählt Philipp Hüsch, der bei Karl Georg die Verantwortung für Werkzeugeinkauf und Prozesse trägt. „Gerade bei den Gewinden standen wir jedoch in der Vergangenheit vor erheblichen Herausforderungen.“
Karl Georg: Spezialist für Kran-Komponenten
Karl Georg, ein traditionsreiches Familienunternehmen mit Sitz im Herzen Deutschlands, ist ein weltweit gefragter Spezialist für Kran-Komponenten. Mit 146 Mitarbeitenden fertigt das Unternehmen unter anderem Laufräder, die in Hafenkranen oder logistischen Schwerlastsystemen zum Einsatz kommen. Dieses Jahr feiert das Unternehmen sein hundertjähriges Bestehen – und blickt dabei auf ein beeindruckendes Wachstum und technologische Fortschritte zurück.
Spanabfuhr aus tiefen Sacklöchern
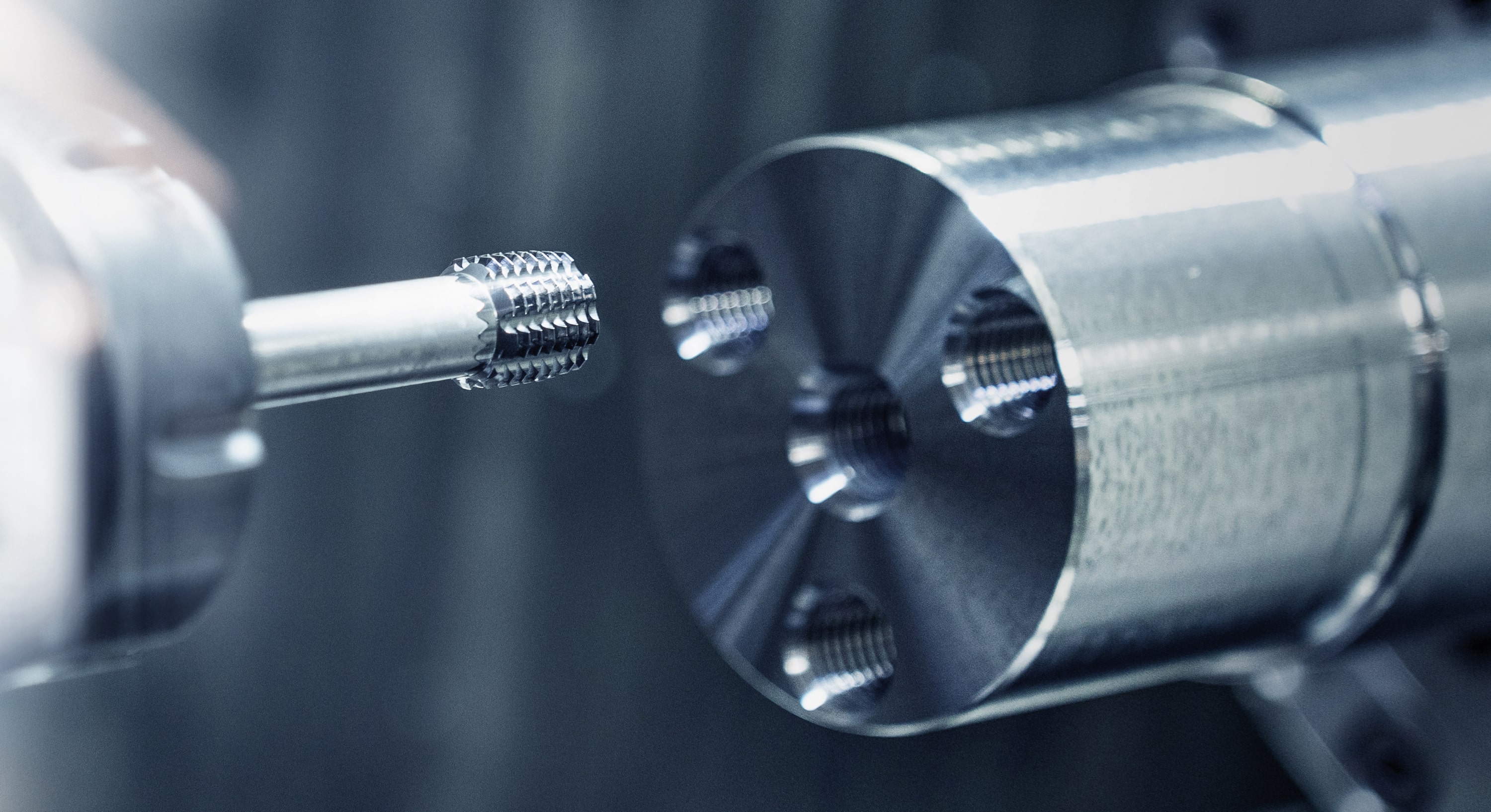
Besonders anspruchsvoll ist die Herstellung von Sacklochgewinden in Antriebs- und Leerlaufwellen, die später in die Kranlaufwerke eingeschrumpft werden. Hier müssen mit Gewindeschneidern Gewindetiefen bis zu 70 Millimeter eingebracht werden – ungewöhnlich tief für ein M16-Gewinde. Diese Tiefe führte regelmäßig zu Problemen bei der Spanabfuhr.
„Früher hatten wir oft Einbußen bei der Standzeit, weil Späne im Sackloch verklemmten. Oft ist sogar das Werkzeug abgebrochen und konnte nicht mehr aus der Bohrung entfernt werden“, erinnert sich Hüsch. „Das ganze Bauteil wurde zu Ausschuss.“ Besonders ärgerlich sind solche Vorfälle, wenn sie in einem automatisierten Bearbeitungsprozess vorkommen: Der gesamte Ablauf kommt ins Stocken, Maschinen müssen angehalten werden und wertvolle Zeit geht verloren. „Ich muss mich sich auf den Prozess verlassen können“, stellt Hüsch klar.
Die Lösung: Der modulare Gewindeformer
Bisher war Karl Georg bei solch tiefen Gewinden auf Sonderwerkzeuge angewiesen, doch hier hatte Gühring-Außendienstberater Marcel Horn eine andere Idee: der neue modulare Gewindeformer. „Die Länge hier ist perfekt und wir müssen nicht mit irgendwelchen Verlängerungen und Sonderkonzepten arbeiten“, erkärt Marcel Horn. Ein weiterer Vorteil des Gühring-Systems ist die Verbindung von HSS-Werkzeugschaft und Hartmetall-Gewindekopf. Die AlCrN-Beschichtung des Gewindekopfs sorgt für eine hohe Verschleißfestigkeit, während die wiederholte Nutzung des Schafts die Kosten pro Bauteil drastisch reduziert. Neben den praktischen Vorteilen bietet die Prozessumstellung auch eine verbesserte Qualität: Durch das Gewindeformen entstehen besonders feste Gewindegänge, die den hohen Belastungen im Betrieb von Krananlagen mühelos standhalten. Für ein Unternehmen wie Karl Georg, das auf Zuverlässigkeit und Präzision angewiesen ist, ist das ein entscheidender Wettbewerbsvorteil.
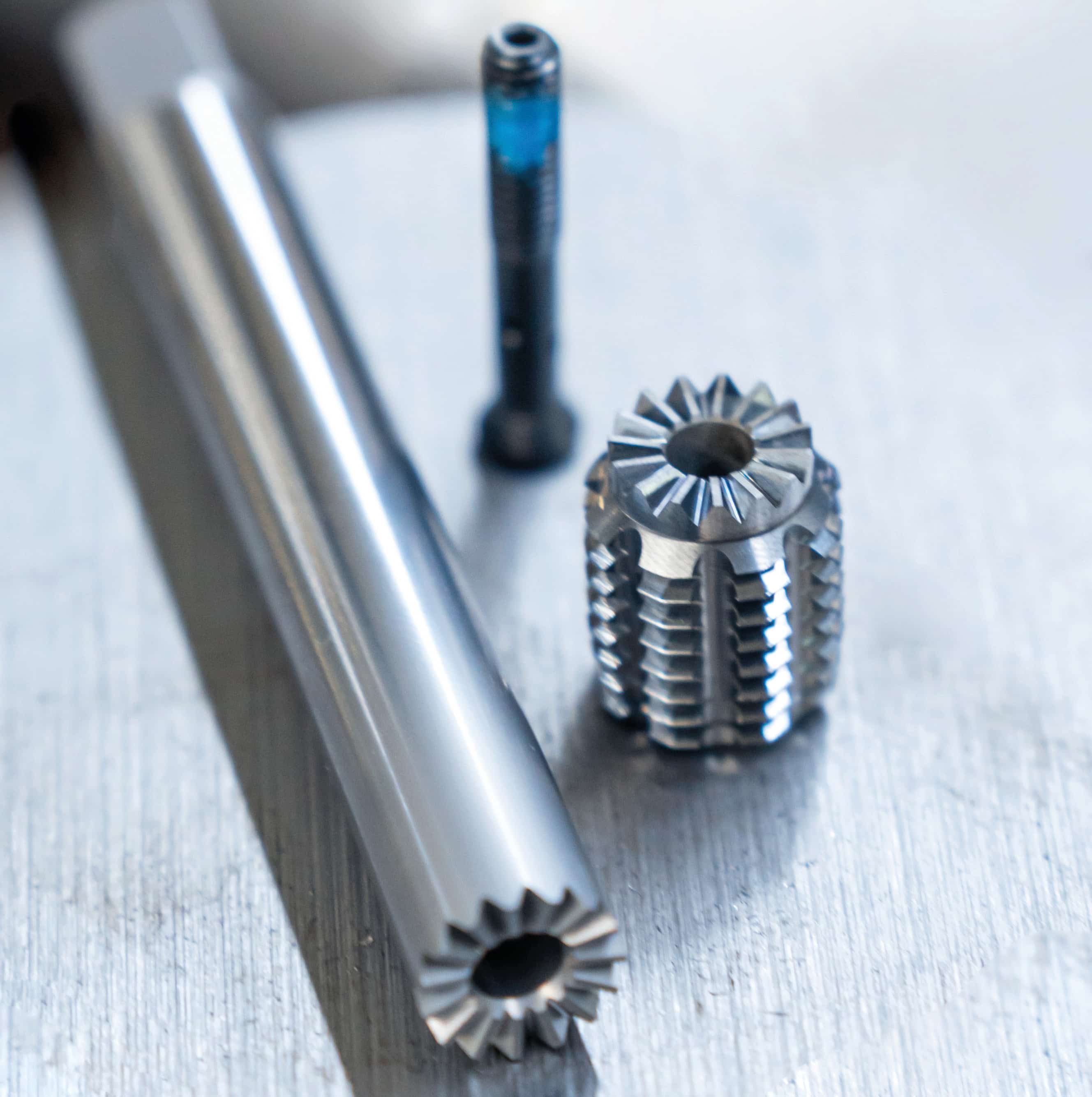
Sicher und schnell: Gewindeformen statt -bohren
„Das macht den gesamten Prozess nicht nur sicherer, sondern auch schneller.“
„Das war ein echter Gamechanger“, berichtet Philipp Hüsch. Im Gegensatz zu Gewindebohrern und Fräsern, bei denen die Späne aus dem Sackloch entfernt werden müssen, entstehen beim Gewindeformen keine Späne. „Das macht den gesamten Prozess nicht nur sicherer, sondern auch schneller“, so Hüsch. Besonders beeindruckend ist die Modularität des Werkzeugs. „Der Schaft bleibt erhalten, und nur der Werkzeugkopf wird bei Verschleiß gewechselt. Das spart Kosten und vereinfacht den Wechsel erheblich“, erklärt Hüsch.
Für Karl Georg bedeutet das: keine Sonderlösungen mehr, keine aufwändigen Anpassungen, sondern ein effizienter und störungsfreier Ablauf. „Wir haben mit dem Werkzeug nicht nur die Standzeiten von 20 auf 60 Minuten verdreifacht, sondern auch die Bearbeitungszeiten deutlich reduziert, da das Nachbohren zur Spanentfernung komplett entfällt.“
3 x mehr Standzeit und ein Arbeitsgang weniger
Werkzeug | Modularer Gewindeformer, Ø = M16x2 Art.-Nr. 4871 Kopf Art.-Nr. 4873 Schaft |
Material | 42CrMo4 (1.7225) |
Vorschub | f = 1.200 mm/U |
Schnittgeschwindigkeit | Vc = 30 m/min |
Drehzahl | n = 600 U/min |
Auch das eigens von Gühring entwickelte Ausgleichsfutter trägt zur Prozessstabilität bei. Es gleicht axiale und radiale Belastungen aus und verlängert so die Lebensdauer des Werkzeugs. „Das war für uns ein echter Mehrwert, da die Werkzeuge dadurch noch länger halten und die Qualität der Gewinde auf einem konstant hohen Niveau bleibt“, betont Hüsch.
Ein starkes Team für große Aufgaben
Die Zusammenarbeit zwischen Karl Georg und Gühring besteht seit fünf Jahren und hat sich seither stetig vertieft. „Früher herrschte in unserem Werkzeugmanagement ein ziemliches Durcheinander“, erinnert sich Philipp Hüsch. „Doch nachdem wir alle Gewindewerkzeuge rigoros auf Gühring umgestellt haben, haben wir nur positive Erfahrungen gemacht.“
Mit dem modularen Gewindeformer hat Gühring eine Lösung entwickelt, die den besonderen Anforderungen von Karl Georg gerecht wird und dabei höchste Prozesssicherheit garantiert. Für Hüsch und sein Team bedeutet das: Weniger Stillstand, weniger Ausschuss und mehr Effizienz – eine Erfolgsgeschichte, die zeigt, wie aus kleinen Umstellungen große Veränderungen erwachsen.
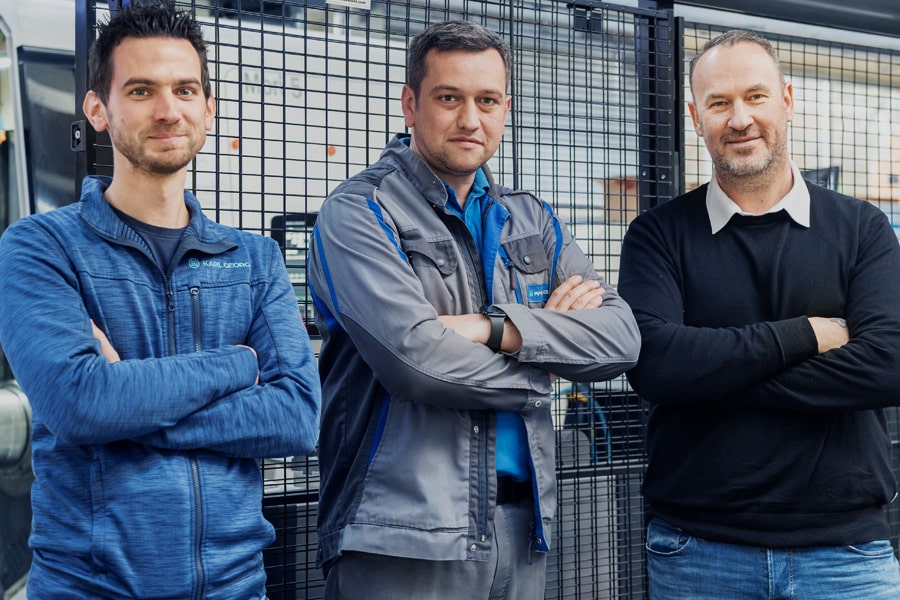
Mit Teamwork zur Problemlösung (v.l.n.r.): Philipp Hüsch, Rudolf Wall (beide Karl Georg) und Marcel Horn (Gühring).
Fazit: Ihre Vorteile mit dem modularen Gewindeformer
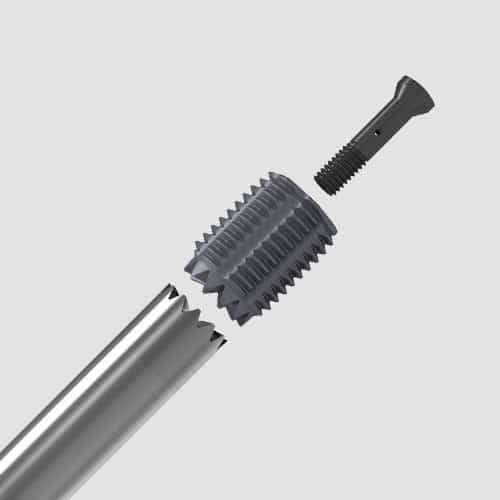
Modularer Gewindeformer
Modulares System für maximale Flexibilität und Wirtschaftlichkeit
Das modulare System, bestehend aus einem Stahlschaft mit wechselbarem Hartmetall-Gewindekopf, ermöglicht maximale Flexibilität und kürzere Reaktionszeiten. Das Werkzeug kann auch bei nicht idealen Rahmenbedingungen eingesetzt werden, bspw. auf älteren Maschinen. Dabei sorgt der Hartmetall-Gewindekopf für eine Taktzeitreduzierung bei deutlich höheren Standzeiten.
Ihre Vorteile mit dem modularen Gewindeformer:
- hohe Wirtschaftlichkeit durch Mehrfachverwendung des Werkzeugschafts nach Verschleiß des Gewindekopfs (bis zu 8x)
- Kostenreduktion durch modulares Wechselsystem
- auch für nicht optimale Rahmenbedingungen geeignet
- Reduktion des Drehmoments durch spezielle Polygonform und Beschichtung
FAQ: Die wichtigsten Fragen zum Formen von Sacklochgewinden
Welche Vorteile bietet ein modularer Gewindeformer gegenüber klassischen Gewindeformern?
Ein modularer Gewindeformer bietet gegenüber klassischen Gewindeformern mehr Flexibilität und Effizienz. Durch das modulare System lassen sich Gewindeformer schnell an unterschiedliche Werkstoffe und Gewindetypen anpassen. Das reduziert Rüstzeiten und senkt die Kosten in der Fertigung. Besonders bei wechselnden Anforderungen an Gewinde und Werkstoffe ist der modulare Gewindeformer die ideale Lösung.
Welche Herausforderungen entstehen bei der Herstellung von Sacklochgewinden?
Bei der Herstellung von Sacklochgewinden entstehen besondere Herausforderungen durch die begrenzte Gewindetiefe und die Gefahr von Spanbildung. Im Vergleich zum Gewindeschneiden ermöglicht der Gewindeformer eine spanlose Bearbeitung, was das Risiko von Ausbrüchen am Sackloch reduziert. Besonders bei anspruchsvollen Werkstoffen ist eine präzise Werkzeugwahl entscheidend. Der Einsatz eines geeigneten Gewindeformers sorgt für höhere Prozesssicherheit und längere Standzeiten.
Wie verhindert das Gewindeformen Werkzeugbruch in tiefen Sacklöchern?
Das Gewindeformen reduziert das Risiko von Werkzeugbruch in tiefen Sacklöchern, da es ohne Spanbildung auskommt. Im Gegensatz zum Gewindeschneiden entstehen keine störenden Späne, die das Werkzeug blockieren oder beschädigen könnten. Der Gewindeformer sorgt für eine gleichmäßige Krafteinleitung, selbst in schwierigen Werkstoffen. So wird die Standzeit erhöht und die Prozesssicherheit bei Sacklochgewinden deutlich verbessert.
Wann lohnt sich der Einsatz eines modularen Systems bei der Gewindebearbeitung?
Der Einsatz eines modularen Systems bei der Gewindebearbeitung lohnt sich besonders bei häufigem Werkzeugwechsel und wechselnden Gewindeanforderungen. Ein modularer Gewindeformer lässt sich flexibel an verschiedene Werkstoffe und Sackloch-Geometrien anpassen. Das spart Rüstzeit und senkt die Produktionskosten. Für Betriebe mit variantenreicher Fertigung ist ein modular aufgebautes System die effiziente Lösung für präzise Gewinde.
Für welche Werkstoffe eignet sich ein Gewindeformer besonders gut?
Ein Gewindeformer eignet sich besonders gut für duktil verformbare Werkstoffe wie Aluminium, Kupfer, Messing und viele nichtrostende Stähle. Diese Werkstoffe lassen sich ohne Spanbildung zuverlässig verformen und ergeben stabile, tragfähige Gewinde.
Wie wirkt sich das Gewindeformen auf die Prozesssicherheit und Bauteilqualität aus?
Das Gewindeformen steigert die Prozesssicherheit, da es ohne Spanbildung arbeitet und damit das Risiko von Werkzeugbruch, besonders bei Sacklöchern, deutlich senkt. Durch die Kaltverformung entstehen präzise, belastbare Gewinde mit hoher Maßhaltigkeit. Der Gewindeformer sorgt zudem für glatte Gewindeoberflächen und reduziert Nachbearbeitungen. Die Bauteilqualität verbessert sich dadurch nachhaltig.
Das könnte Sie auch interessieren:
Experten in rostfreien Stählen: 3 Werkzeuge für die Inox-Bearbeitung
Mit den neuen High-Performance-Werkzeugen für die Inox-Bearbeitung bietet Gühring die optimale Lösung für anspruchsvollste Zerspanungsaufgaben. Spezielle Beschichtungen und Geometrien garantieren höchste Schnittwerte und verlängerte Standzeiten.
Gewindefräsen: Diese Software liefert das perfekte CNC-Programm
Um das Gewindefräsen mit Ihrem Gewindefräser noch anwenderfreundlicher zu gestalten, hat Gühring die intuitive Software CNC Gühro ThreadMill entwickelt. Und dank eines Upgrades bietet Ihnen die neue Version V3 noch mehr Möglichkeiten.
Maximal flexibel und wirtschaftlich: Modulare Gewindewerkzeuge
Gühring kombiniert die Vorteile von Hartmetall und Schnellarbeitsstahl in einem Werkzeug und schraubt einen Hartmetallkopf auf einen HSS-Schaft. Das Ergebnis sind neue Gewindeformer als modulares System – für mehr Flexibilität beim Gewindeformen.