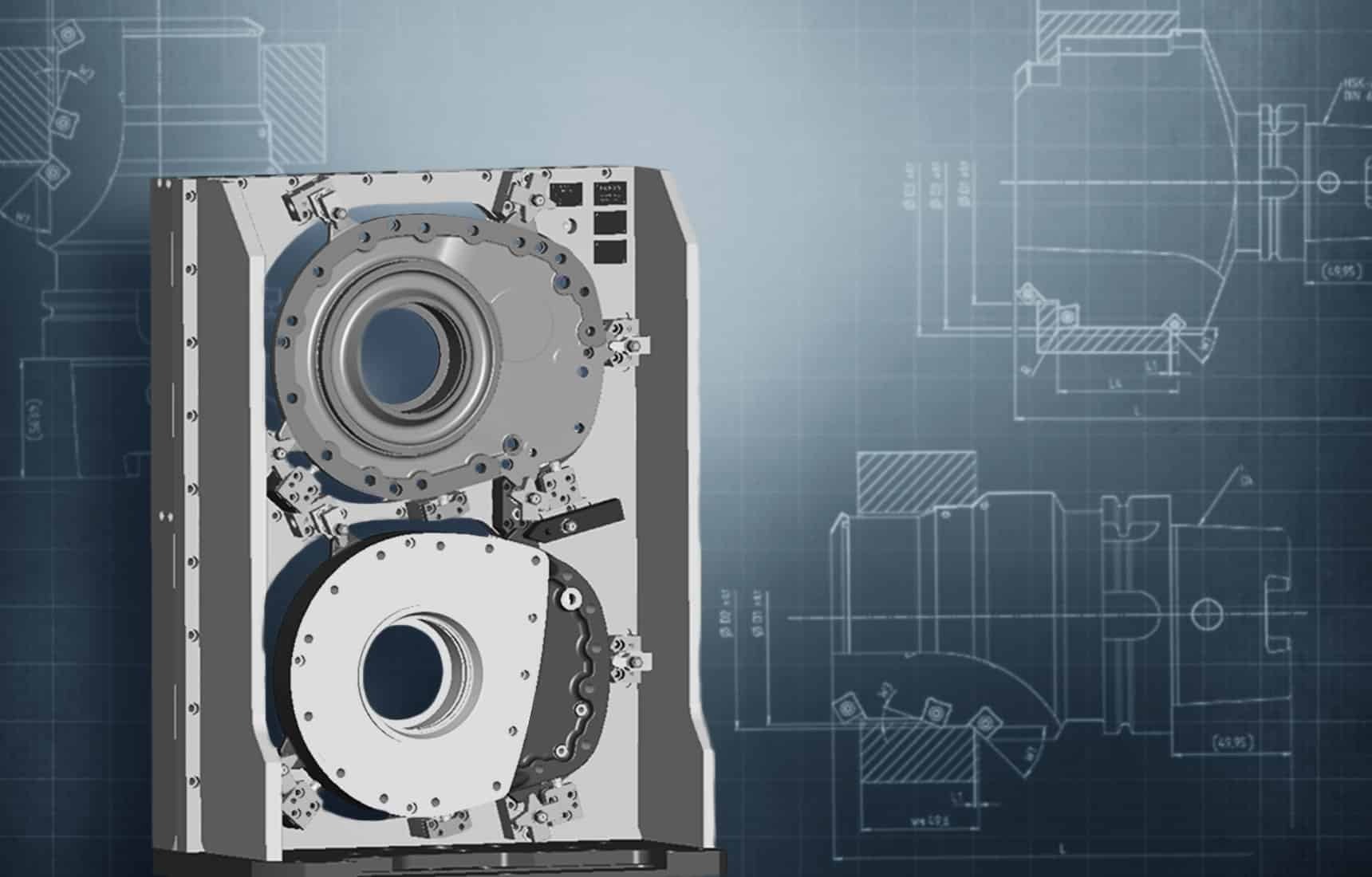
Der Bearbeitungsprozess muss schneller ablaufen. So lautet der Auftrag, mit dem sich der Hersteller eines Guss-Getriebedeckels an Gühring wendet. Ein klarer Fall für den das Retooling-Team, welches für die Auslegung neuer Prozesse zuständig ist, aber auch bestehende Prozesse von Grund auf analysiert und optimiert. In diesem Fall war das Ergebnis eine Zeitersparnis von mehreren Minuten pro Bauteil – und damit ein gewaltiger Kostenvorteil für den Kunden.
Nicht immer ist ein Prozess, der sich einmal bewährt hat, auch der effizienteste. Das weiß auch ein Hersteller von Antriebskomponenten für landwirtschaftliche Fahrzeuge, der sich mit einer konkreten Anfrage an Gühring wendete: Bei dem Herstellprozess eines Getriebedeckels sollte Bearbeitungszeit eingespart werden. Bisher dauerte es 33 Minuten, das Guss-Werkstück zu bearbeiten. Gühring sollte diesen Prozess nun so optimieren, dass am Ende eine Zeiteinsparung von 10 Prozent pro Bauteil möglich ist.
Retooling-Service optimiert Prozesse
Für eine solche Optimierung ganzer Bearbeitungsprozesse gibt es bei Gühring einen eigenen technischen Dienstleistungsbereich: Gühring Retooling. Hauptsächlich ist das Retooling-Team für die Konzeption und Umsetzung neuer Prozesse zuständig. Aber auch um die Optimierung eines Prozesses auf einer bestehenden Maschine kümmern sich die Retooling-Experten.
Was ist Retooling?
Retooling ist ein technischer Dienstleistungsbereich bei Gühring. Das Retooling-Team ist hauptsächlich für die Konzeption und Umsetzung neuer Prozesse zuständig.
In jedem Fall übernimmt Gühring dabei das komplette Projektmanagement – von der Planung des Prozesses, über die Anpassung an die vorhandene oder Auslegung einer neuen Vorrichtung bis hin zur Inbetriebnahme. Unser Team aus Ingenieuren, Technikern und Konstrukteuren greift dabei auf seine langjährige Erfahrung im Bereich der Projektplanung zurück. Am Ende steht immer eine maßgeschneiderte Lösung, die auch in der Praxis prozesssicher funktioniert.
Bei einer Großserie, die über Monate läuft, bedeutet jede eingesparte Minute einen riesigen Kostenvorteil.
Den Anfang eines Retooling-Projekts bildet immer die Analyse des zu fertigenden Werkstücks: Wie ist die Aufspannsituation des Getriebedeckels? Welche Werkzeuge und Spannvorrichtungen kommen bei den einzelnen Arbeitsschritten zum Einsatz? Mit welchen Prozessparametern wird gearbeitet? „Wir haben den Prozess unter unseren Gesichtspunkten überarbeitet“, sagt Hartmut Raach, Leitung Retooling bei Gühring. „Dabei hatten wir einige Ideen, die sich in unserer Zeitberechnung niedergeschlagen haben.“
Doppelspannung und reduzierte Werkzeugvielfalt
Bei der Herstellung des Getriebedeckels sind vor allem Fräs- und Bohrwerkzeuge im Einsatz. Hier profitiert Gühring von seiner Kompetenz und Erfahrung als Hersteller von Sonderwerkzeugen. Indem einige Werkzeuglösungen speziell auf diese Bearbeitung zugeschnitten wurden, konnten Arbeitsschritte zusammengefasst und dadurch die Werkzeugvielfalt reduziert werden. Vor allem bei der Vorbearbeitung spart der Kunde auf diese Weise einige Werkzeugwechsel. Zudem ersetzten die Retooling-Experten ausgewählte Werkzeuge durch Hochleistungswerkzeuge von Gühring. Diese haben zum Beispiel mehr Schneiden und ermöglichen dadurch den Einsatz höherer Schnittparameter.
Eine weitere Optimierungsmaßname setzt bereits bei der Vorrichtung an: Bisher wurde jedes Bauteil einzeln zur Bearbeitung auf die Maschine gespannt. Die Gühring-Experten setzten nun auf eine Doppelvorrichtung, mit der zwei Bauteile bearbeitet werden können. So lassen sich vor allem die Neben- und Wechselzeiten bei der Bearbeitung deutlich senken.
Nachdem Werkzeuge und die Vorrichtung bei Gühring konzipiert wurden, musste die neue Lösung eine Kollisionsprüfung durchlaufen, bei der sie auf ihre Prozesssicherheit hin geprüft wurde. Das Einfahren des Prozesses samt neuer NC-Programmierung erfolgte durch unsere erfahrenen Anwendungstechniker vor Ort beim Kunden.
Riesiger Kostenvorteil auf lange Sicht
Durch die verschiedenen Optimierungsmaßnahmen gelang es Gühring vor allem die Nebenzeiten pro Bauteil beinahe zu halbieren. So sinkt die gesamte Bearbeitungszeit pro Werkstück von 33 auf 28 Minuten, was einer Zeitersparnis von 14 % entspricht. „Fünf Minuten Einsparung klingen zwar erst einmal wenig“, stellt Hartmut Raach fest. „Doch bei einer Großserie, die über Monate läuft, bedeutet jede eingesparte Minute einen riesigen Kostenvorteil.“
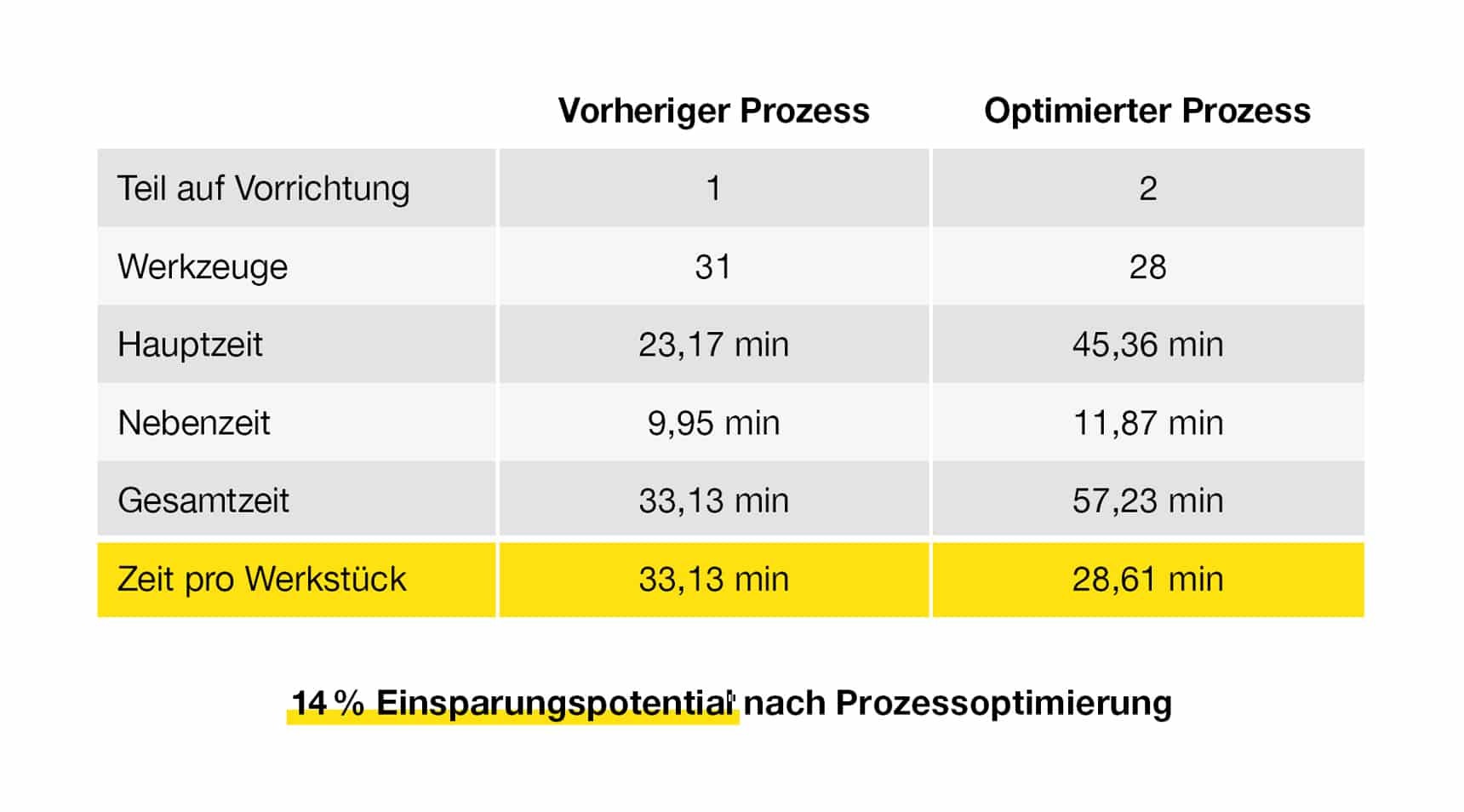
Das könnte Sie auch interessieren:
Werkzeugverwaltung im Wandel: Digital den Überblick behalten
Getsch+Hiller optimiert mit der Gühring Tool Management Software (GTMS) seine Werkzeugverwaltung. Dank digitaler Ausgabeschränke und modularer Software spart das Unternehmen Zeit, reduziert Kosten und bleibt flexibel – perfekt angepasst an das schnelle Wachstum der Medizintechnik.
Ihr Werkzeug im Detail: Das GTMS Werkzeugdatenmodul
Steigern Sie Ihre Effizienz mit dem GTMS Werkzeugdatenmodul. Vermeiden Sie Fehlerquellen, optimieren Sie Rüstzeiten und erhalten Sie volle Transparenz über Werkzeugbedarf und Bauteilkosten. Erleben Sie präzises Werkzeugdatenmanagement für maximale Kontrolle.
Keine Zeit für Papierkram? Das GTMS Auftragsmodul
Optimieren Sie Ihre Auftragsplanung und steigern Sie die Effizienz mit der Gühring Tool Management Software (GTMS). Das Auftragsmodul bietet Transparenz, ermöglicht Echtzeitüberwachung und fördert standardisierte Abläufe für höchste Produktqualität.