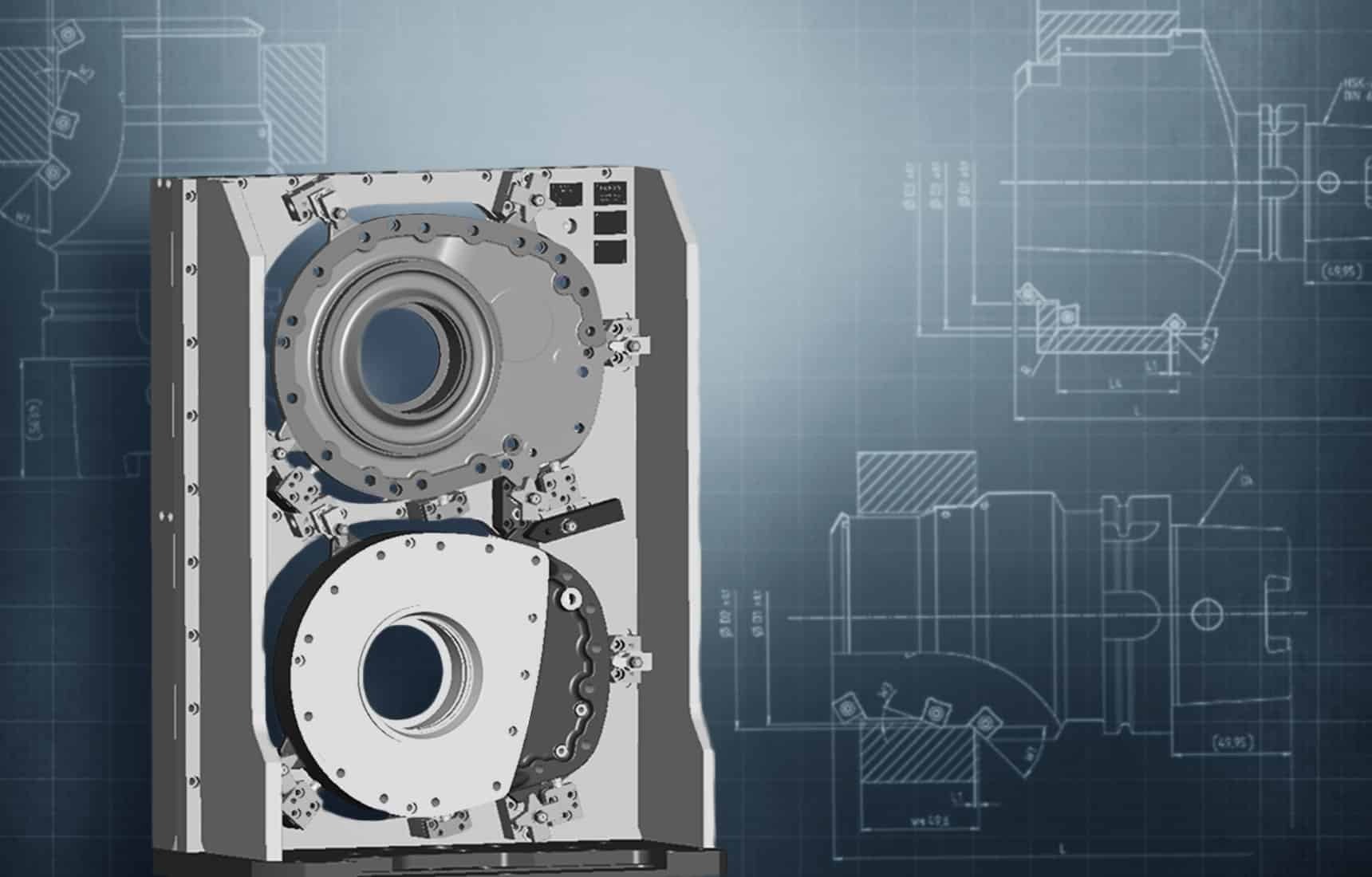
The machining process needs to be quicker. This was the task set when a manufacturer of a cast gear cover contacted Gühring. A clear case for the retooling team, which analysed and optimised the process from scratch. The result was a time saving of several minutes per component – and thus a huge cost advantage for the customer.
A process that has been proven to yield results is not always the most efficient. A manufacturer of drive components for agricultural vehicles had also experienced this, so they contacted Gühring with a specific enquiry: Savings were needed in the machining time for the manufacturing process of a gear cover. Previously, it took 33 minutes to machine the cast workpiece. Gühring’s task was to optimise this process so that a time saving of 10 percent per component could ultimately be achieved.
Retooling service optimises processes
Gühring has its own technical service division for optimising entire machining processes: Gühring Retooling. With this service, we take care of the entire project management process – from planning the process, to making changes in line with the existing solution or designing a new one, right through to commissioning. During this process, our team of engineers, technicians and designers draws on their many years of experience in the field of project planning. The result is always a bespoke solution that also works reliably in practice.
A retooling project always starts with an analysis of the workpiece to be manufactured: What is the clamping situation for the gear cover? Which tools and clamping fixtures are used in the individual working steps? Which process parameters are used? “We revised the process according to our criteria,” says Hartmut Raach, Head of Retooling at Gühring. “We had a few ideas that were reflected in our time calculation.”
Double clamping and reduced tool variety
Milling and drilling tools are the main tools used to manufacture the gear cover. Gühring benefited here from its expertise and experience as a manufacturer of special tools. By tailoring some tool solutions specifically to this machining process, it was possible to combine working steps and thus reduce the number of tools. Especially in the pre-machining phase, the customer could save a few tool changes in this way. In addition, the retooling experts replaced selected tools with high-performance tools from Gühring. These have more cutting edges, for example, and thus enable higher cutting parameters to be used.
Another optimisation measure starts with the fixture itself: Previously, each component was clamped individually onto the machine for machining. The Gühring experts used a double fixture that enables two components to be machined. In this way, the non-productive and changeover times during machining could be significantly reduced.
After tools and the fixture were designed at Gühring, the new solution had to undergo a collision check, in which it was tested for its process reliability. The process and new NC programming were proved out by our experienced application technicians at the customer’s site.
Huge cost advantage in the long term
Thanks to the various optimisation measures, Gühring was able to almost halve the non-productive times per component. This reduces the total machining time per workpiece from 33 to 28 minutes, which corresponds to a time saving of 14 %. “At first, five minutes of savings do not sound like much,” says Hartmut Raach. “But with large-scale batch production running over months, every minute saved means a huge cost advantage.”
You might also be interested in:
Conserving resources for the future: 5 reasons for carbide recycling
Save resources and benefit from carbide recycling with Gühring! Exchange worn tools for money and reduce your carbon footprint. Simple, sustainable and efficient.
Tool management in flux: Keeping track with digital tech
Getsch+Hiller optimiert mit der Gühring Tool Management Software (GTMS) seine Werkzeugverwaltung. Dank digitaler Ausgabeschränke und modularer Software spart das Unternehmen Zeit, reduziert Kosten und bleibt flexibel – perfekt angepasst an das schnelle Wachstum der Medizintechnik.
Detailed data on your tools: The GTMS tool data module
Increase your efficiency with the GTMS tool data module. Avoid sources of error, optimise set-up times and gain full transparency over tool requirements and component costs. Experience precise tool data management for maximum control.