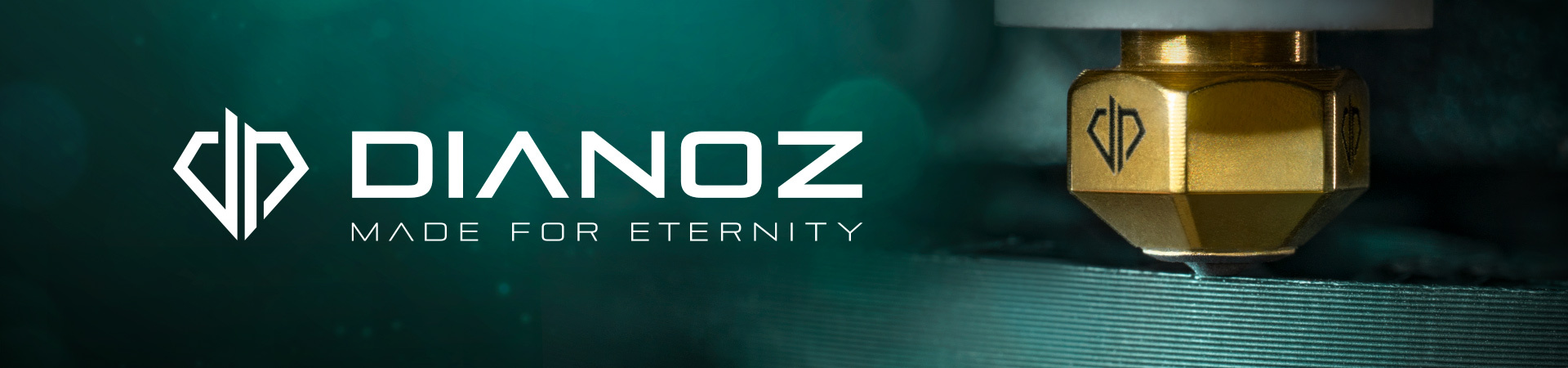
DIANOZ 3D printer nozzle
Diamond nozzle marks a new milestone in additive manufacturing
The most common 3D printing technology is fused deposition modelling, known as FDM for short. In this process, a nozzle applies molten material to a pressure plate layer by layer. The printer nozzle acts as a tool for the printer and is one of the most wear-prone parts of the 3D printer. This is now changing with the diamond-tipped DIANOZ printer nozzle from Gühring. As an interface between the printer and the component, the nozzle makes a significant contribution to the print quality. Wear and poor thermal conductivity affect the printing process and the result. That’s why Gühring has spent over two years researching and developing an innovative new nozzle: The DIANOZ diamond-tipped printer nozzle.
Poor surfaces, incorrect printing temperature, re-levelling – are these problems that you are familiar with?
Even the best 3D printer can’t help if you are using the wrong nozzle
- worn nozzle tips lead to poor print results and unclean surfaces with droplet-like excess material
- time-consuming adjustment of the nozzle clearance to the print bed to compensate for wear
- termination of the printing process as it is not possible to continue printing without a loss of quality due to changed parameters after a nozzle has been replaced
In addition to wear resistance, the thermal conductivity of the nozzle has a decisive influence on the printing process. Materials such as ruby (corundum) on the nozzle tip are thermally insulating and therefore affect print quality and process reliability:
- unclean, rough surfaces due to uneven filament flow
- the set value deviates from the actual temperature on the tip and makes accurate, process-reliable printing difficult
- the insulating effect is compensated by increasing the printing temperature by up to 15° C and constantly increases energy consumption
DIANOZ – the 3D print nozzle with a black diamond
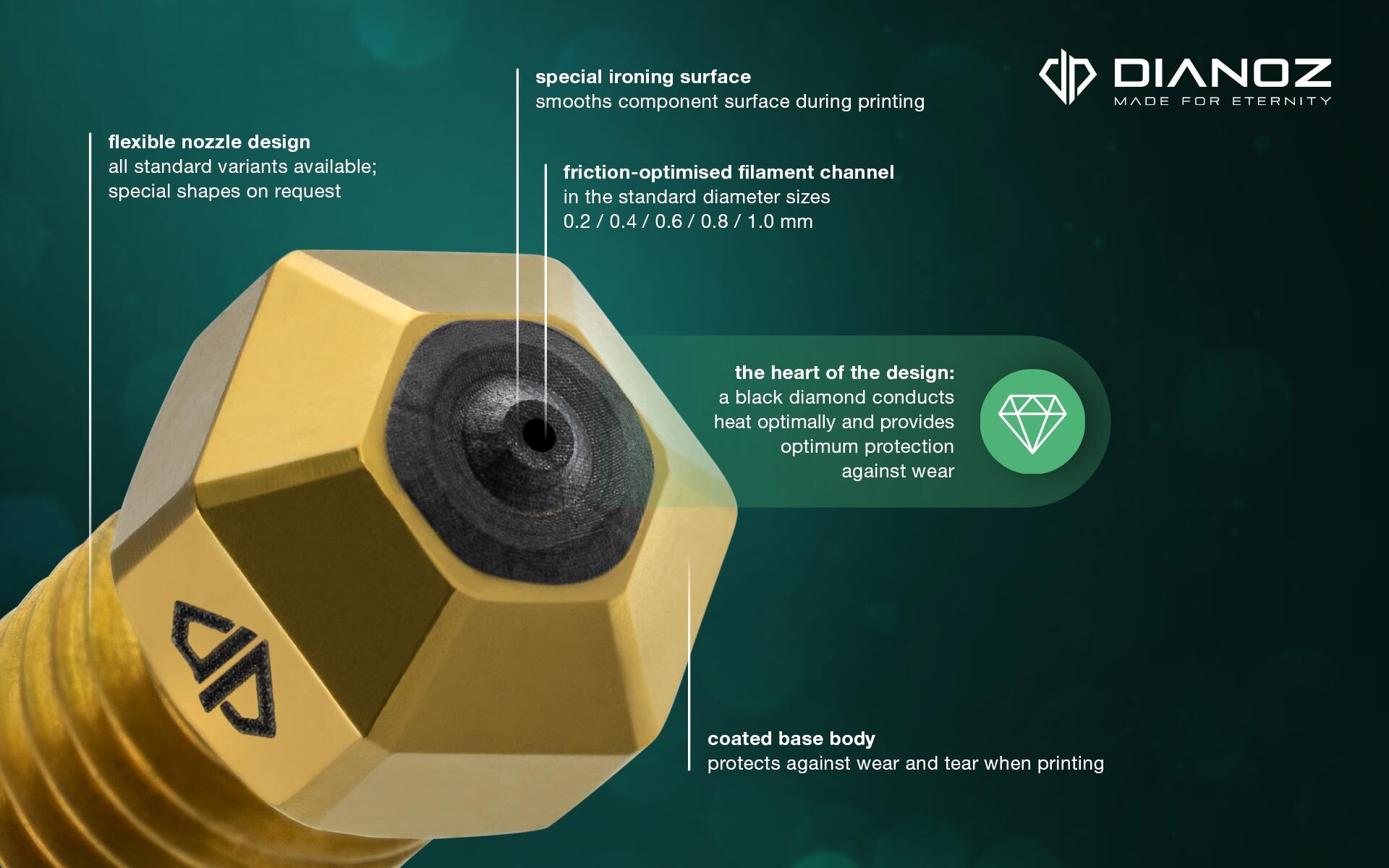
How you benefit from the DIANOZ nozzle
As the hardest natural material in the world, diamond offers the best wear protection – including as an insert in the nozzle tip. At the same time, it conducts heat extremely well, ensuring even material extrusion and smooth surfaces. No other material can combine these two properties so well, which is why the DIANOZ nozzle is reinforced with a synthetic diamond. These man-made diamonds, also known as polycrystalline diamonds or PCD for short, have identical chemical and physical properties and are in no way inferior to natural gemstones in terms of hardness and thermal conductivity.
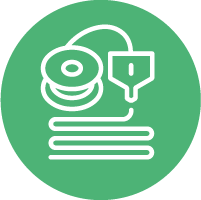
Ultra-wear resistant for abrasive filaments
- easy printing of challenging materials such as glass or carbon fibre reinforced plastics as well as ceramic or metal filled materials and high temperature filaments
- large components and high quantities possible without changing nozzles in 24/7 printing operation
- one nozzle for all materials – “always on nozzle”
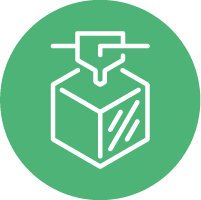
High-quality print results
- high thermal conductivity ensures uniform filament flow and smooth surfaces
- friction-optimised filament channel supports uniform material extrusion
- ironing surface on the nozzle tip smooths the print surface
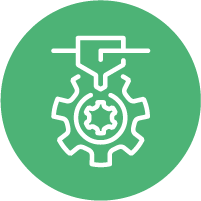
Increased process reliability while printing
- no printing interruptions due to nozzle changes
- uniform layer thickness without wear-related readjustment
- reliable temperature setting
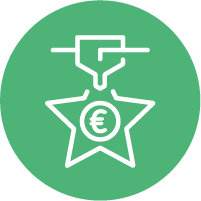
Cost-effective printing
- fewer nozzle purchases
- reduced personnel costs for maintenance and nozzle replacement
- lower temperature printing to reduce energy costs
FRAUNHOFER APPROVED
OUTSTANDING PRINT PERFORMANCE
„Our tests have shown that the diamond insert means that DIANOZ nozzles exhibit almost the same stable extrusion behaviour as a brass nozzles and has the added advantage of abrasion resistance. Compared to other wear-resistant nozzles, such as ruby ones, more uniform extrusion performance was exhibited over larger temperature extrusion speed ranges.“
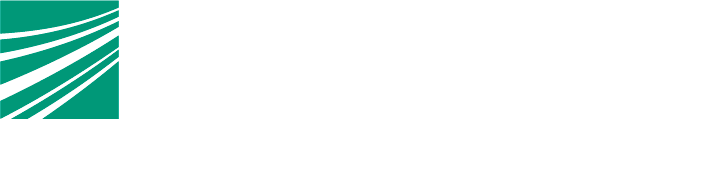
3D printer nozzles: What’s different?
Nozzles, as they are often called, are usually made of brass or hardened steel. Ruby nozzles have a ruby tip (corundum). The main difference is their resistance to wear and thermal conductivity. The ideal 3D printing nozzle for you depends on the filament used and the load.
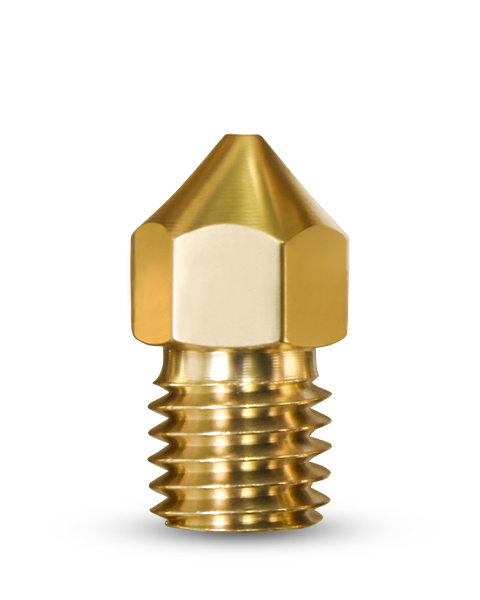
Brass nozzles
Brass nozzles are particularly suitable for printing soft plastics such as PLA Popular:
- high thermal conductivity
- highly susceptible to wear – not suitable for abrasive materials
- low heat resistance (up to 300°C)
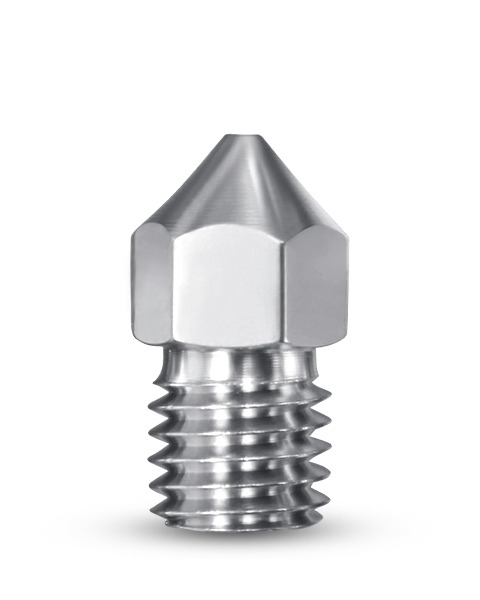
Steel nozzles
Steel or hardened steel nozzles exhibit longer resistance to wear Brass nozzles are unable to match them when it comes to thermal conductivity:
- moderate thermal conductivity
- moderate wear resistance
- higher heat resistance (up to 500°C)
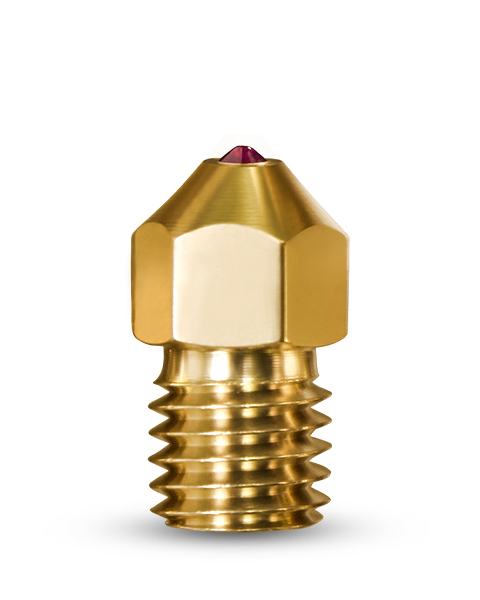
Ruby nozzles
Ruby-tipped nozzles protect the tip from wear. However, the synthetic gemstones have heat-insulating properties:
- high wear resistance
- low thermal conductivity
- high heat resistance (up to 550° C)
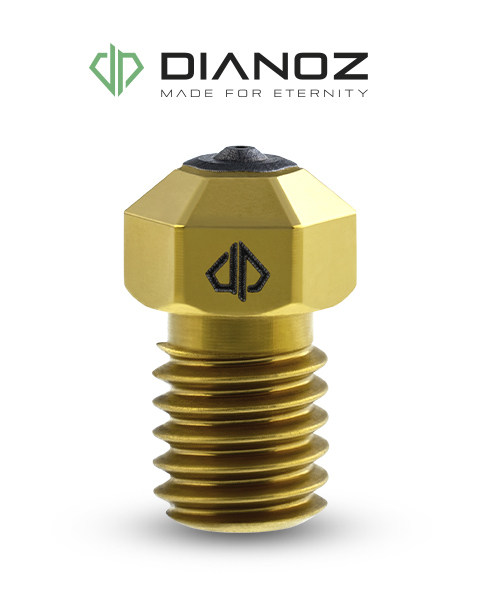
DIANOZ diamond nozzles
Diamond is not only the hardest substances in the world, it also has excellent heat-conducting properties. This combination is the hallmark feature of the world’s only patent-pending DIANOZ diamond nozzle:
- highest wear resistance
- very high thermal conductivity
- high heat resistance (up to 550° C)
The diamond – unbeatable in terms of hardness & thermal conductivity
3x harder than ruby (corundum)
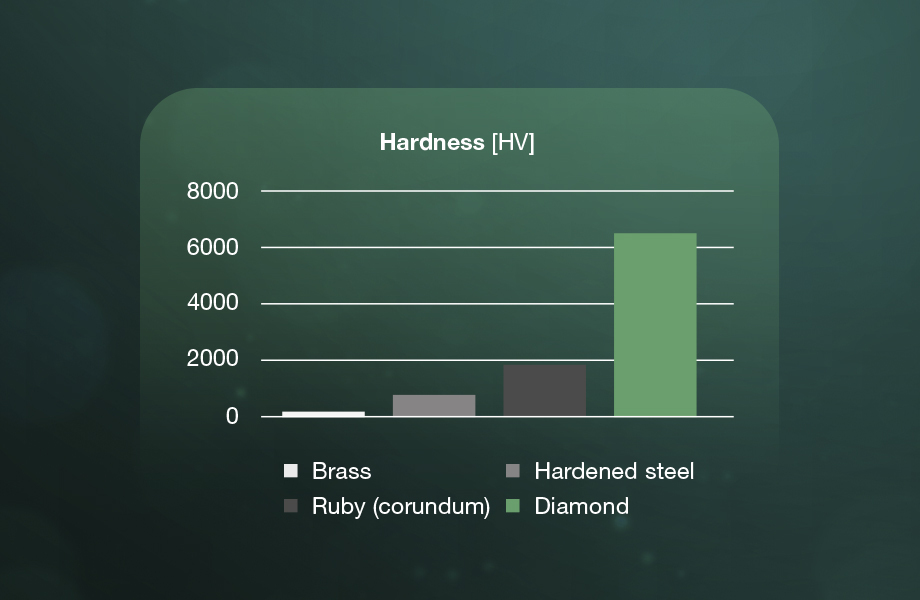
4x better thermal conductivity than brass
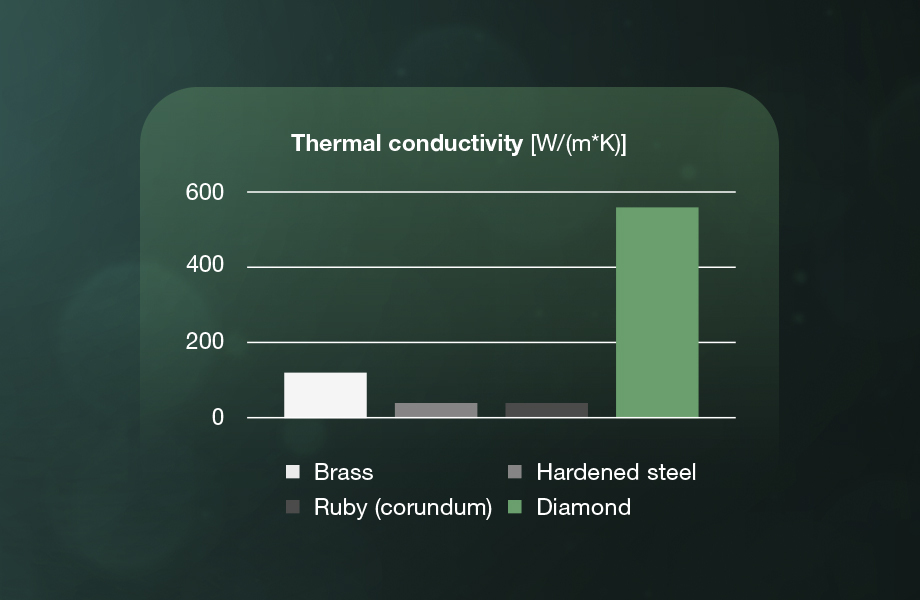
A nozzle for abrasive filaments and high-temperature printing
With DIANOZ, you can print everything from PLA, carbon fibres and PEEK to metallic and ceramic filled materials
There is already a wide range of materials that can be printed. The most suitable filament depends primarily on the function and application of the component. Plastics are the most common printed material – and the number-one choice is PLA, short for polylactic acid. This is a biodegradable plastic made from renewable raw materials such as corn starch or sugar cane. PLA is cost-effective, easy to process and harmless to health.
Professional 3D printing often uses more sophisticated materials. The DIANOZ nozzle can be used to easily print these materials (examples, list not exhaustive):
- ABS
- ASA
- CPE
- filaments filled with glass fibre
- HDPE
- HIPS
- ceramic-filled filaments
- filaments filled with carbon fibre
- LDPE
- metal-filled filaments
- PA
- PBT
- PC
- PC-ABS
- PCL
- PCTG
- PEEK
- PEI
- PET-G
- PLA
- PMMA
- POM
- PP
- PPSU
- PS
- PVA
- PVDF
- TPE
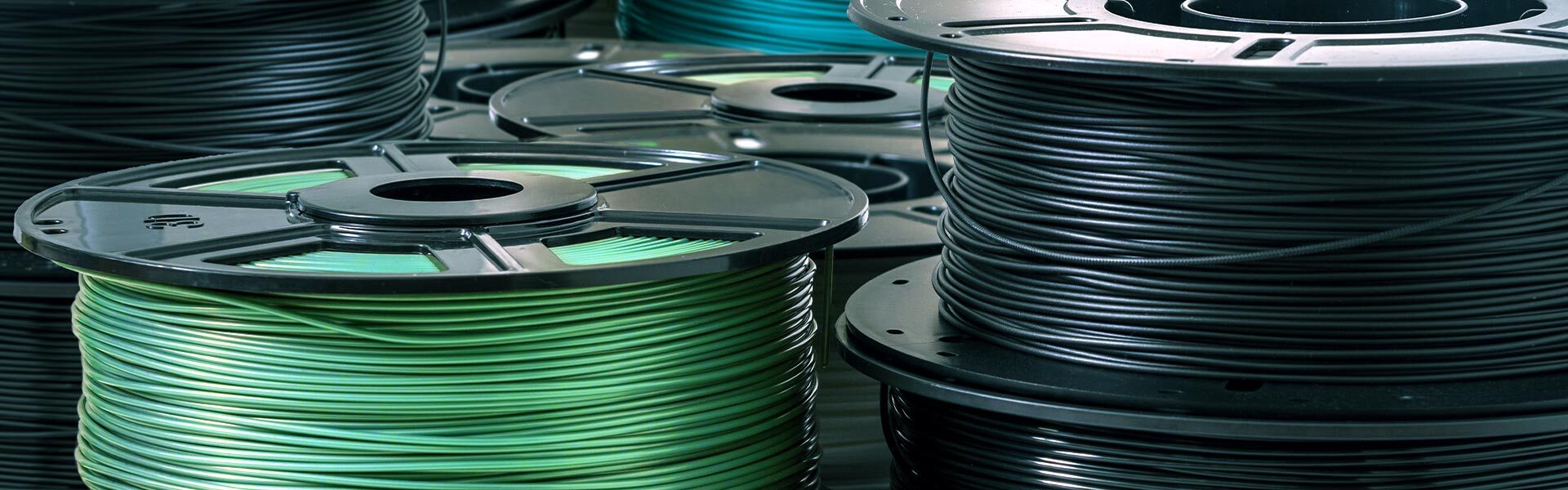
3D printing: nozzle diameter and layer thickness
Printer nozzles are available in different diameters. The nozzle diameter affects both surface quality and print speed. Small diameters dispense less material, allowing finer structures to be printed. They are therefore particularly suitable for delicate, intricate printed objects. If the print speed is paramount and the component quality is secondary, larger nozzle diameters are better suited.
The nozzle diameter also limits the minimum and maximum layer thickness. With a conventional 0.4 mm nozzle, the recommended minimum layer thickness is 0.1 mm and the maximum thickness is 0.3 mm. The following rule of thumb helps to determine the correct layer thickness:
Minimum layer thickness = 0.25 * nozzle diameter
Maximum layer thickness = 0.75 * nozzle diameter
What nozzle size is suitable for what?
The nozzle opening is also called the outlet diameter or capillary, the following diameters are common:
- Ø 0.2 mm for intricate, particularly fine-resolution prints
- Ø 0.4 mm for all conventional prints, good compromise between detail accuracy and print speed
- Ø 0.6 mm for higher print rates and to reduce the risk of nozzle clogging with short-fibre filaments
- Ø 0.8 mm for maximum material throughput, especially for coarser and correspondingly faster prints
Why can’t you select the layer height thickness equal to the nozzle diameter?
In order to ensure reliable layer adhesion, the extruded filament – viewed in cross-section – must be discharged as an oval strand. If the nozzle diameter is the same as the layer thickness, this is not guaranteed and the individual layers do not optimally adhere to one another.
What else needs to be taken into account with regard to the nozzle diameter?
The larger the nozzle diameter, the higher the flow rates. As such, more filament must be melted in a shorter time and this is only possible with a more powerful heating block or hot end.
Which nozzle diameter is suitable for what?
The outlet diameter depends on the surface requirements and the desired printing time. Nozzles with a diameter of 0.4 mm are often used for daily printing with different filaments. When working with filaments containing short fibres, we recommend switching to nozzles with Ø ≥ 0.6 mm.
Why does the nozzle of a 3D printer get clogged?
The short fibre content in some filaments is randomly distributed in the filament strand. This can lead to local fibre accumulations in the nozzle’s conical outlet area causing it to clog up. The wrong printing parameters, material carburisation or residue from filaments that have already been printed have a higher melting point and can also cause possible nozzle clogging.
Which materials can be printed using the FDM process?
All amorphous and partially crystalline thermoplastics can be processed. It is also possible to use compounds of wood fibres, glass fibres, ceramic composites or metallic components.
What are abrasive materials or filaments?
Abrasive materials have a comparatively high grinding effect and put a great deal of strain on the printer nozzle. They usually consist of a base filament enriched with additional particles or fibres. Glass-, ceramic- and metal-filled plastics as well as carbon-fibre-reinforced thermoplastics are a few examples of abrasive filaments. High-temperature filaments can also be assigned to this category.
Fused deposition modelling
What FDM, FFF, FLM and MEX are all about
The most common 3D printing process is known as fused deposition modelling. Similar to a hot glue gun, material is heated and dispensed again in molten form. In fused deposition modelling, the print material is normally wire-shaped and wound onto a coil. This filament is melted in the printer’s hot-end system and applied to a flat surface, the print bed. This creates a three-dimensional print object – layer by layer. If a component has overhangs, additional support structures are printed which stabilise the component during the printing process before being removed again.
The extrusion process has many different names in the 3D printing world. Here are the most common abbreviations and their meanings:
- FDM = Fused Deposition Modelling
- FFF = Fused Filament Fabrication
- FLM = Fused Layer Modelling
- MEX = Material Extrusion
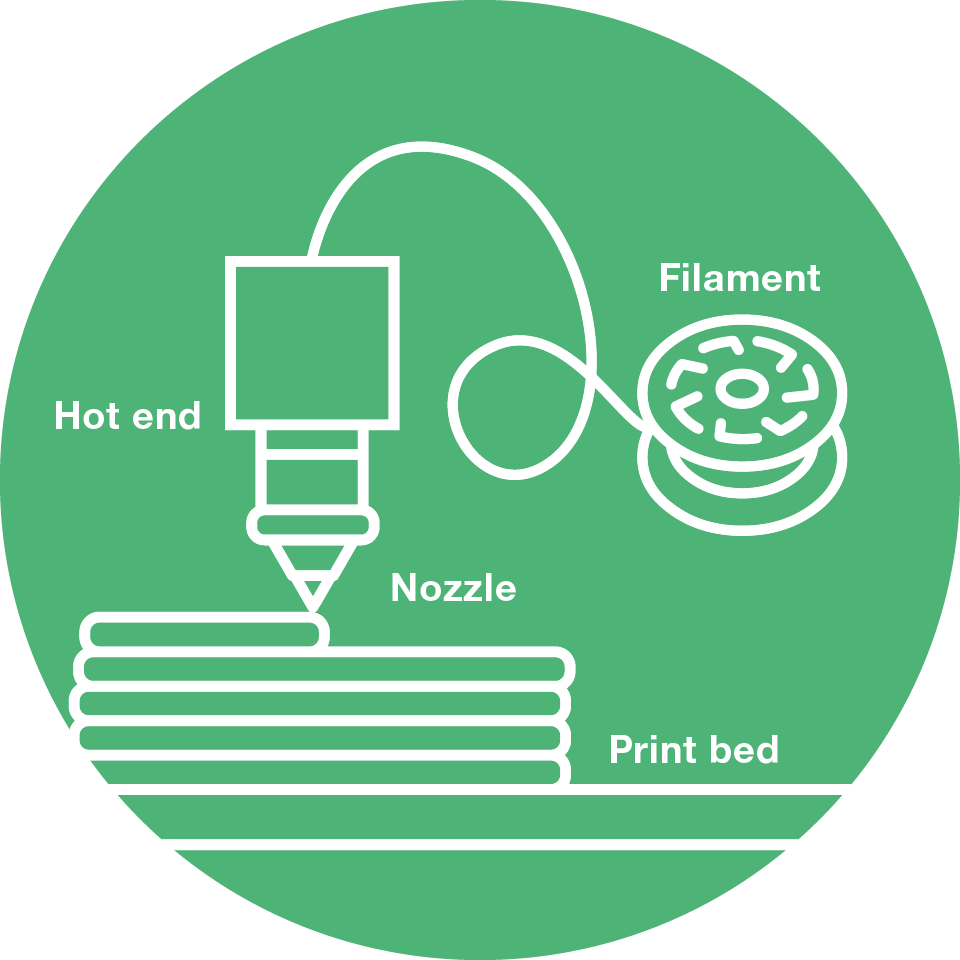
Order your DIANOZ nozzle now
Have any questions about DIANOZ? Or are you keen to order one right away? Please do not hesitate to contact us:
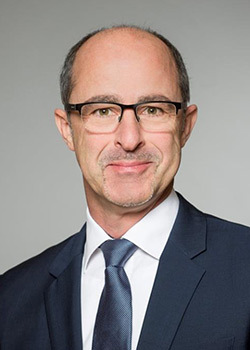
Udo Lerach
Head of Sales for Trade & Special Parts, Private Label
Gühring goes additive
From diamond tool to diamond nozzle
Gühring’s industry-changing pioneering work has been undisputed since the invention of modern tool coating: In 1981, Gühring developed the first TiN-coated twist drill – a milestone in machining technology. The finished tools drastically reduce manufacturing costs and become the benchmark for the entire industry.
The design and production of customer-specific diamond-tipped tools has also been one of the Swabian company’s core skills for over 40 years. PCD tools – short for polycrystalline diamonds – are indispensable in many industries such as the automotive sector: high-precision machining, reproducible processes and durable tools are essential here. With DIANOZ, the diamond is now also entering the world of additive manufacturing, marking a new milestone in FFF technology.
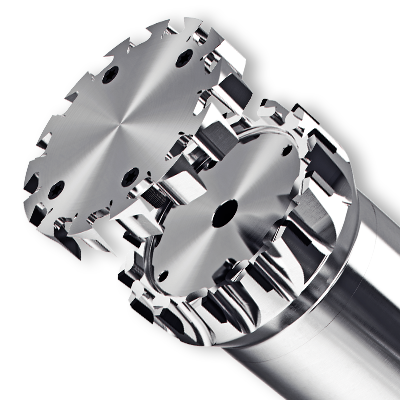