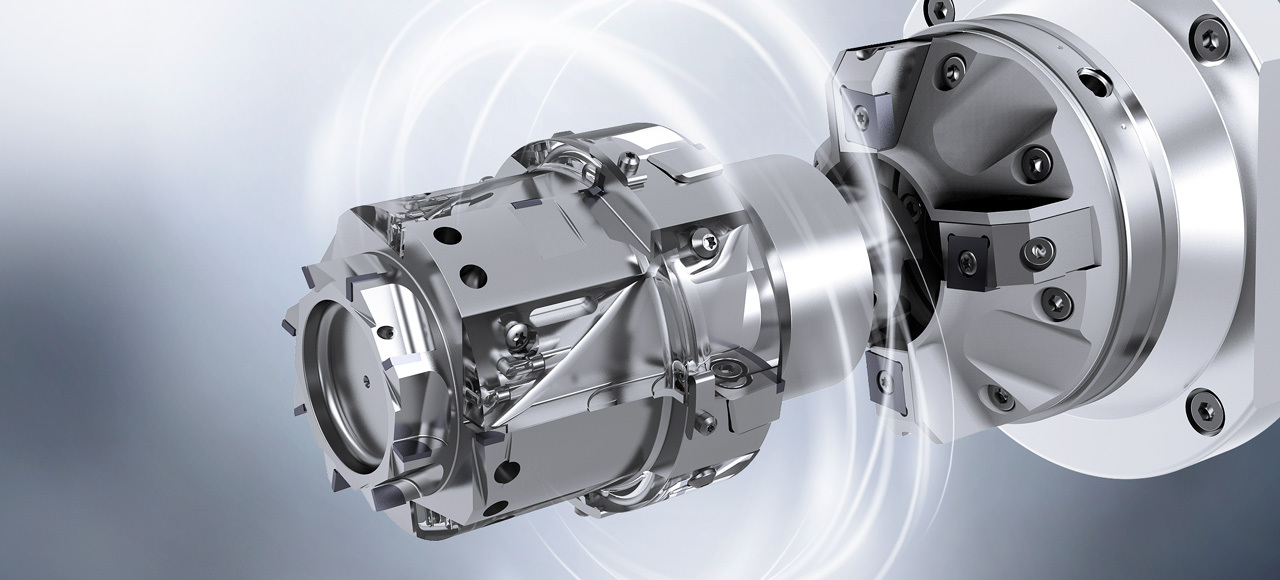
Ein Meter lange Aluminium-Späne, die sich um das Werkzeug wickeln, Spanräume verstopfen und Oberflächen zerkratzen – mit diesem Problem hat ein Automobilzulieferer zu kämpfen. Doch wie können lange Späne zerkleinert werden, wenn alle bekannten Mittel versagen? Die Antwort liefert ein neuer „Spänehäcksler“ von Gühring.
Das Bauteil ist eigentlich nichts Besonderes: ein Motorengehäuse, wie es in jedem Auto zur Unterstützung der Servolenkung sowie Spurhalte- und Einparkassistenten benötigt wird. Doch bei der Herstellung geht ein Automobilzulieferer aus Baden-Württemberg einen besonderen Weg. Denn bisher werden solche Bauteile in einem aufwendigen und teuren Alu-Druckgussverfahren, genannt HPDC (High Pressure Die Casting), hergestellt.
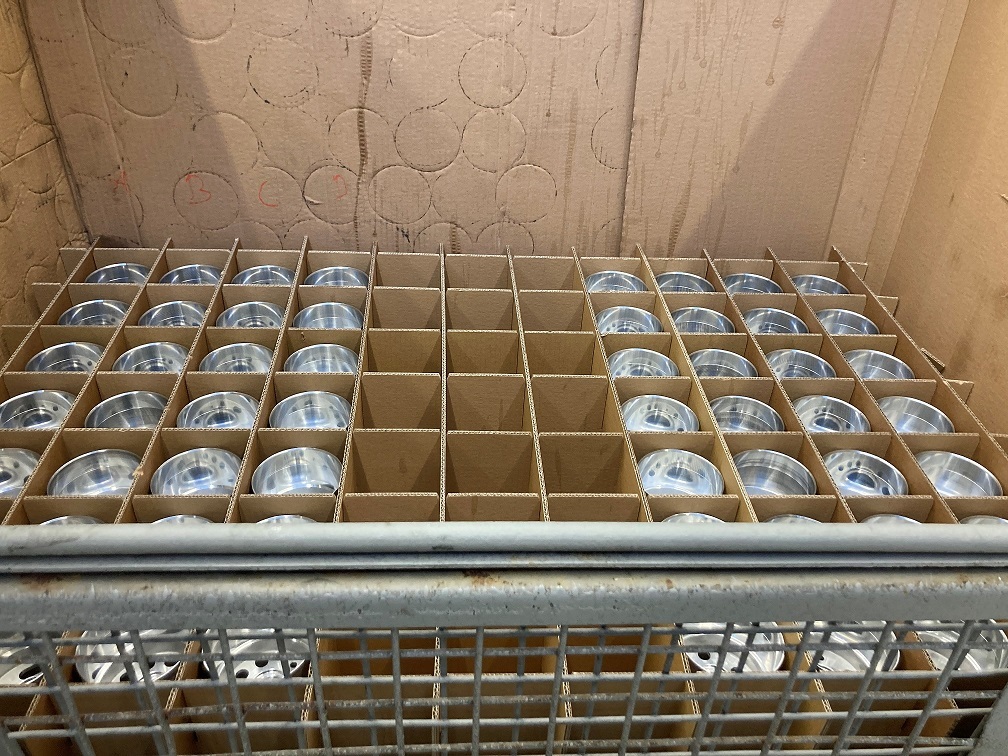
Viel schneller und kosteneffizienter ist jedoch das Kaltfließpressen. Dabei wird eine Aluminiumronde in eine Matrize gelegt und ein Stempel erzeugt von oben Druck, sodass das Aluminium an einer Seite tiefgezogen wird. Dieses Verfahren hat den Vorteil, dass viel seltener Poren und Undichtigkeiten entstehen, was die Ausschussrate gering hält. Beim Kaltfließpressen lassen sich außerdem viel dünnere Wandstärken realisieren – und das bedeutet Einsparungen bei Gewicht und Ressourcen.
Doch wenn es an die Nachbearbeitung des gegossenen Rohlings durch Zerspanungswerkzeuge geht, birgt diese innovative Technik ihre Tücken: Während die Bauteile üblicherweise aus gut zerspanbaren Aluminiumlegierungen mit 7 bis 12 % Siliziumgehalt hergestellt werden, ist die Zusammensetzung des Werkstoffs beim Kaltfließpressen deutlich anspruchsvoller für den Zerspaner. So wird der Rohling in diesem Fall aus Aluminium mit sehr niedrigem Siliziumanteil (< 1 %) hergestellt, das zum Tiefziehen besonders gut geeignet ist. Das Problem: Die Späne waren extrem lang und biegsam, sodass sie nicht von selbst brachen. „Sie erreichten Längen von bis zu einem Meter“, erinnert sich Matthias Helbig, technischer Berater für PKD-Werkzeuge bei Gühring.
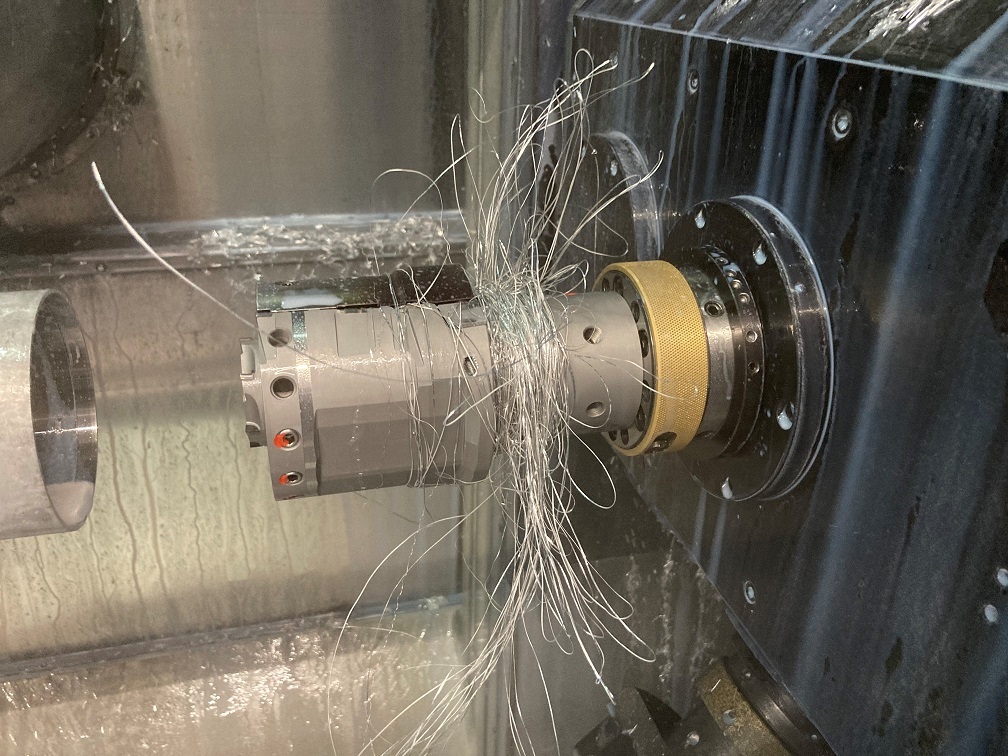
Keine Methode hält dem Spanfluss stand
Für den Kunden war klar: Hier kommen nur Werkzeuge infrage, die die Späne auf irgendeine Art brechen. Denn geschieht das nicht, können die langen Späne nicht aus der Bohrung abtransportiert werden und würden sich in den Spanräumen sammeln und das Werkzeug verstopfen oder um den Werkzeughals wickeln. Dies würde unweigerlich zu Qualitäts- und Standzeiteinbußen führen; zumal die Anforderungen an die Oberfläche mit <Rz 4 sehr hoch sind. „So kann kein Serienprozess funktionieren“, erklärt Matthias Helbig.
Mehrere namhafte Werkzeughersteller machten sich auf die Suche nach einer Lösung, um die Späne zu brechen. Doch keine der herkömmlichen Methoden wie Spanleitstufen, Spanteilern oder Prallelemente konnte dem Spanfluss auf Dauer standhalten. Die einzig erprobte Alternative wäre gewesen, durch einen Stottervorschub den Reibprozess immer wieder kurz zu unterbreche, um dem Span Zeit zum Brechen zu geben. Doch diese Methode würde viel zu viel Zeit in Anspruch nehmen und die Qualität der Bohrung würde durch das ständige Anbohren ebenfalls leiden.
Die Gühring-Experten standen also vor der Frage, welche Möglichkeiten es noch gibt, um den Span zu beeinflussen. Dabei kamen sie auf einen völlig neuen Ansatz: Die Späne sollen direkt nach der Entstehung durch einen komplett geschlossenen Spanraum bis zu einer „Häckselschneide“ geführt werden, wo sie in kleine „Abschnitte“ zerteilt werden. Der eigentliche Spänehäcksler schließt sich im hinteren Teil an den Stahl-Grundkörper des Werkzeugs an und ist fest mit dem Spindelkopf der Maschine verbunden. Somit dreht sich das Werkzeug, während die Häckselschneiden stillstehend. Das abgebildete System wurde für einen Maschinentyp mit manueller Werkzeugspannung (HSK-C) entwickelt, doch auch Ausführungen für eine Maschine mit automatischem Werkzeugwechsel (HSK-A) sind möglich.
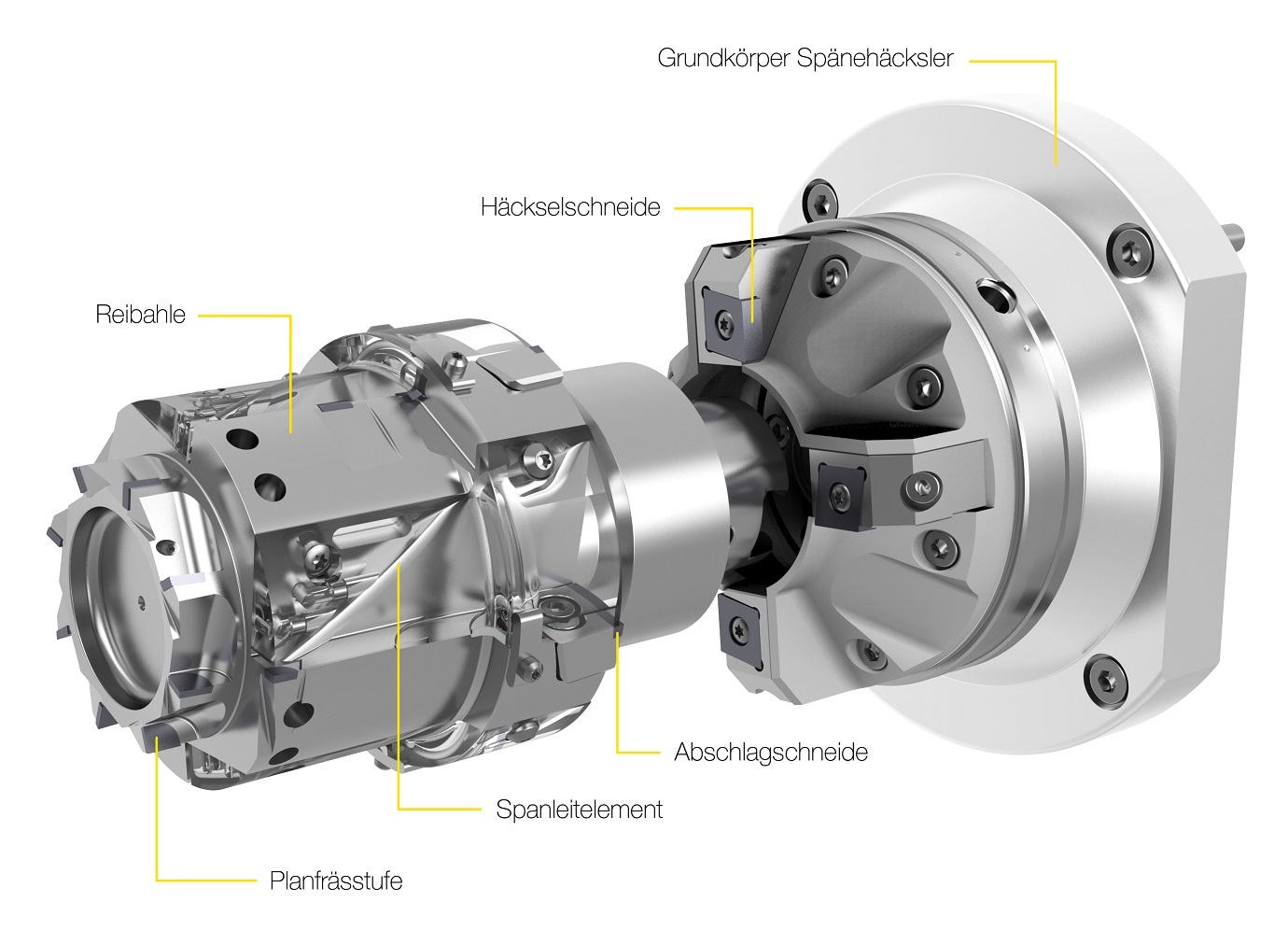
Die insgesamt vier Häcksel- und vier Abschlagschneiden sind als geschraubte VHM-Platte ausgeführt, die bei Verschleiß einfach ausgewechselt werden können. Die Reibstufen bestehen aus gelöteten PKD-Segmenten, so dass eine möglichst hohe Standzeit mit sehr gleichmäßig scharfer Schneidkante gewährleistet werden kann. Aufgrund der sehr dünnen Wandstärke am Bauteil, hat die Reibahle eine starke Ungleichteilung erhalten. Somit beeinflussen sich die Reibstufen nicht gegenseitig und die Rundheit von <15µm konnte eingehalten werden. Die geschraubten und passgenau gefertigten Spanleitelemente führen dazu, dass die Späne ausschließlich nach hinten abgeleitet werden und nicht die erzeugte Oberfläche der Bohrungswandung beschädigen. Zusätzlich wird der Spänefluss durch entsprechend ausgerichtete Kühlkanäle und einen leicht positiven Achswinkel unterstützt.
Prozesssicher in der Großserie
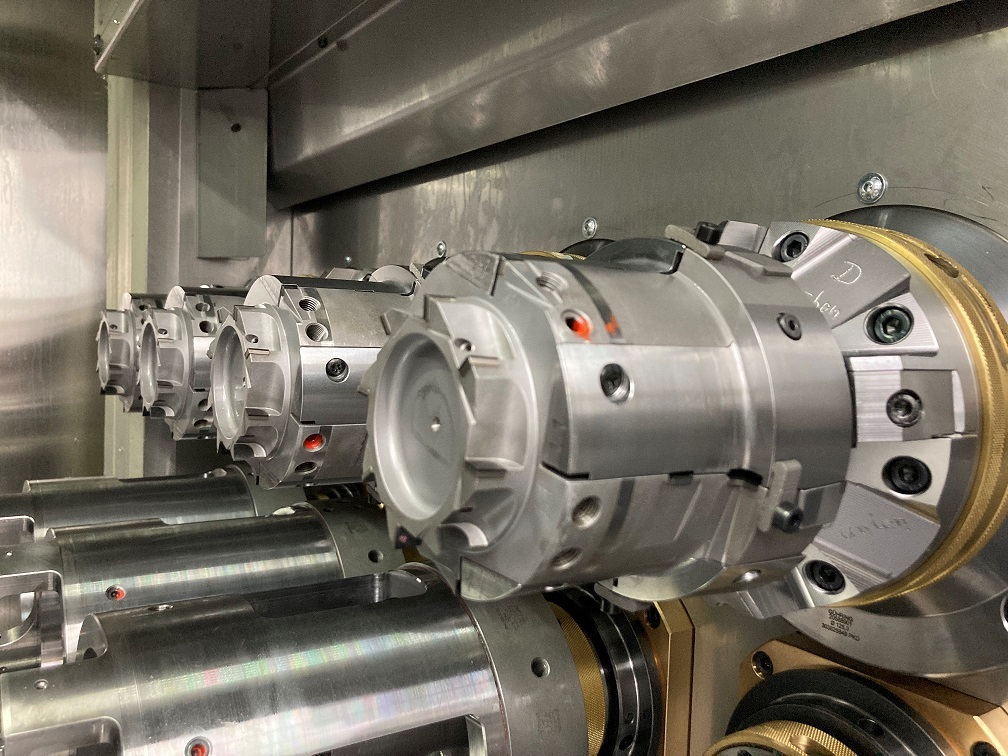
Die größte Stärke des Werkzeugs liegt in seiner hohen Prozesssicherheit. Durch den Spänehäcksler sind die Späne am Ende zwischen 90 und 180 mm lang und lassen sich sicher abtransportieren. Aber auch die Messergebnisse können sich sehen lassen: Durchmesser, Rundheiten sowie Oberflächen befinden sich innerhalb der geforderten Toleranz und das, obwohl wegen der sehr dünnen Wanddicke auch die Bauteilspannung im Zusammenhang mit Form- und Lagetoleranzen eine Herausforderung darstellte. „Diese hohen Qualitätsanforderungen können wir nur dadurch erfüllen, dass wir die Späne kontaktlos aus dem Bauteil abführen“, stellt Matthias Helbig fest. Die Spanlänge kann über folgende Faktoren verändert werden: die Anzahl der Häckselschneiden und Schnittgeschwindigkeit (Vc = m/min).
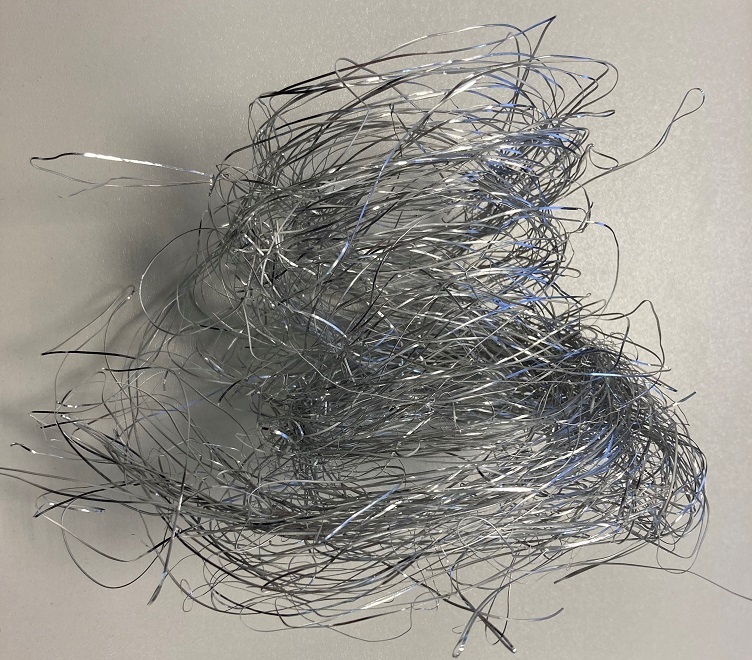
Mit einer Reibahle ohne Spänehäcksler sind die Späne bis zu einem Meter lang.
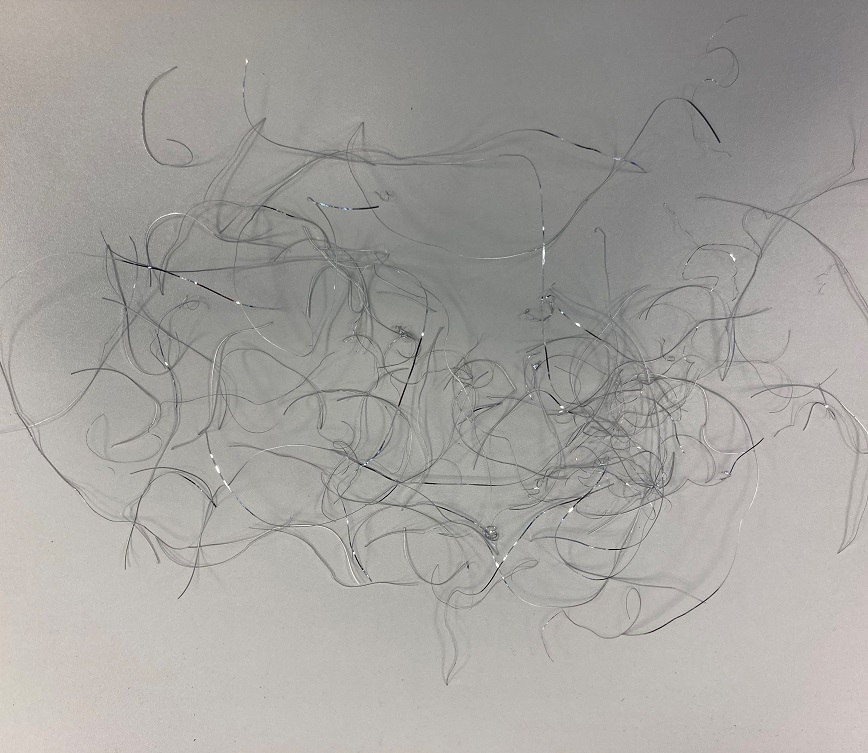
Der neue Spänehäcksler bringt die Späne auf eine Länge von 90 bis 180 mm.
So können mit dem neuen Spänehäcksler Schnittwerte erzielt werden, die den bisherigen Prozess in den Schatten stellen. Weil das Bauteil rotationssymmetrisch ist, wurde es zuvor auf einer Drehmaschine hergestellt. Dies dauerte 27,9 Sekunden pro Bauteil. Mit dem neuen Reibwerkzeug wurde diese Hauptzeit auf 4,8 Sekunden gesenkt – der Kunde muss also nur noch 17 Prozent der Bearbeitungszeit aufwenden. „Die Schnittwerte sind vor allem dann hoch, wenn man bedenkt, dass das Bauteil nur eine Wandstärke von 0,7 mm hat“, lautet das Fazit von Matthias Helbig. Deshalb hat Gühring das System „Spänehäcksler“ bereits zum Patent angemeldet.
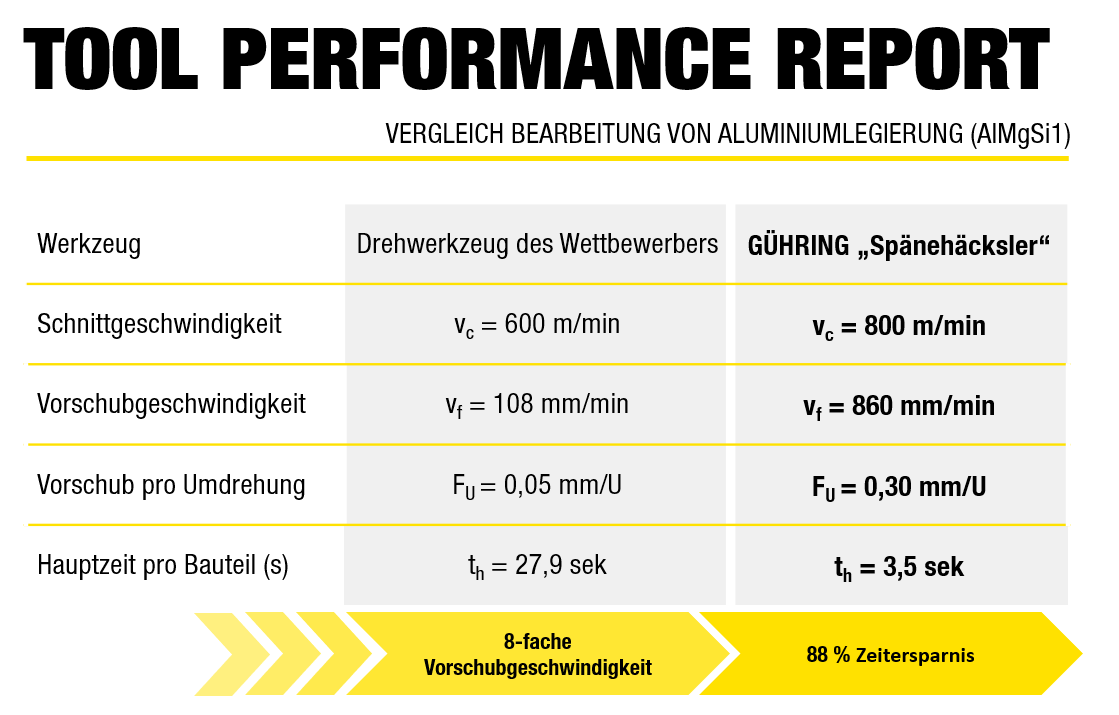
Haben wir Ihr Interesse geweckt?
Dann vereinbaren Sie jetzt Ihren Beratungstermin:
Technische Beratung und Support erhalten Sie auch schnell und direkt über unsere Service-Hotline 00800 2607 2607. Auch auf WhatsApp sind wir für Sie erreichbar: +49 172 658 53 53. Gleich einspeichern!
Das könnte Sie auch interessieren:
Diamant-Düse: 50 kg Carbon – drucken ohne Ende
CR-3D ist führender Anbieter im Bereich additive Fertigung und entwickelt und produziert alle erforderlichen Komponenten für den 3D-Druck im industriellen Umfeld. Gühring liefert das Herzstück für diese Art von Maschinen: die Druckerdüse aus Diamant.
Mit Diamant gegen Verschleiß: Magnesiumbearbeitung in der E-Mobilität
Bei der Fertigung von Magnesiumteilen für E-Motoren stößt ein Kunde auf Verschleißprobleme: Mit speziellen Diamantwerkzeugen erhöht Gühring die Standzeit von Wochen auf ein Jahr. So spart das Unternehmen Kosten und Zeit.
Allround-Talent in Alu: Der neue PKD-Diver
Maximale Zerspanraten und endlose Standzeiten in Aluminium: Das verspricht der neue PKD-Diver. Dank seiner innovativen Geometrie garantiert das Werkzeug Top-Qualität bei gleichzeitig geringer Leistungsaufnahme und hoher Stabilität.