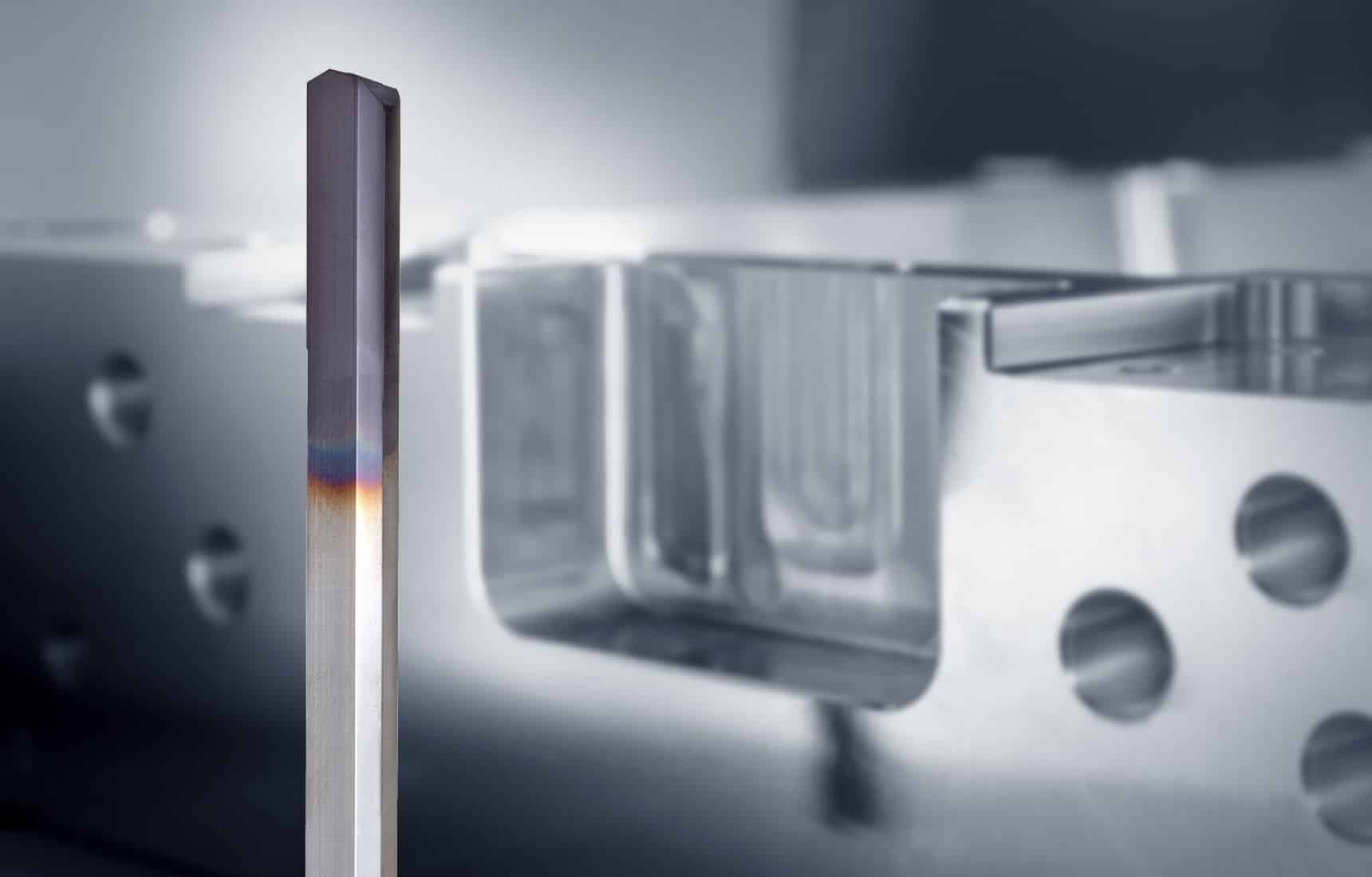
Tiefbohrbearbeitungen fallen häufig im Formenbau sowie in zahlreichen anderen Branchen an. Doch immer wieder ist es dabei von konstruktiver Seite vorgegeben, dass sich zwei Bohrungen kreuzen. Solche sich kreuzenden Tiefbohrungen lassen sich also nicht vermeiden, doch ihre Bearbeitung ist knifflig: Denn in dem Moment, in dem der Tieflochbohrer aus der einen Bohrung austritt und in die nächste eintritt, durchquert er einen Lückenbereich, in dem der Kühlprozess unterbrochen wird und eine teils sehr ungünstige Anbohr- bzw Führungssituation entsteht. Das Kühlmittel ist nicht mehr imstande die entstehenden Späne ordentlich auszuspülen, die das Werkzeug beschädigen können. Auch die Führung des Werkzeugs ist unterbrochen, worunter die Stabilität des Werkzeugs nicht mehr gegeben ist. Nur mit der richtigen Strategie und dem geeigneten Werkzeug kann ein solcher Lückenbereich prozesssicher überbrückt werden.
Vorgehen bei Lückenbereichen
Das richtige Vorgehen bei Querbohrungen zeigen wir anhand eines Praxisbeispiels: In eine Formplatte aus Stahl (1.2321) muss eine Vielzahl an Tieflochbohrungen eingebracht werden. Diese dienen später als Temperierbohrungen, durch die ein Kühlmittel fließt, um die Temperatur der Form zu kontrollieren. Hergestellt werden diese Bohrungen auf einem horizontalen Bearbeitungszentrum von DMG, die Programmierung erfolgte über Tebis. Doch Querbohrungen und die dadurch entstehenden Lückenbereiche machen die Bearbeitung besonders anspruchsvoll. Hier unterscheiden wir zwei Bohrsituationen, bei denen sich jeweils ein bestimmtes Vorgehen bewährt hat.
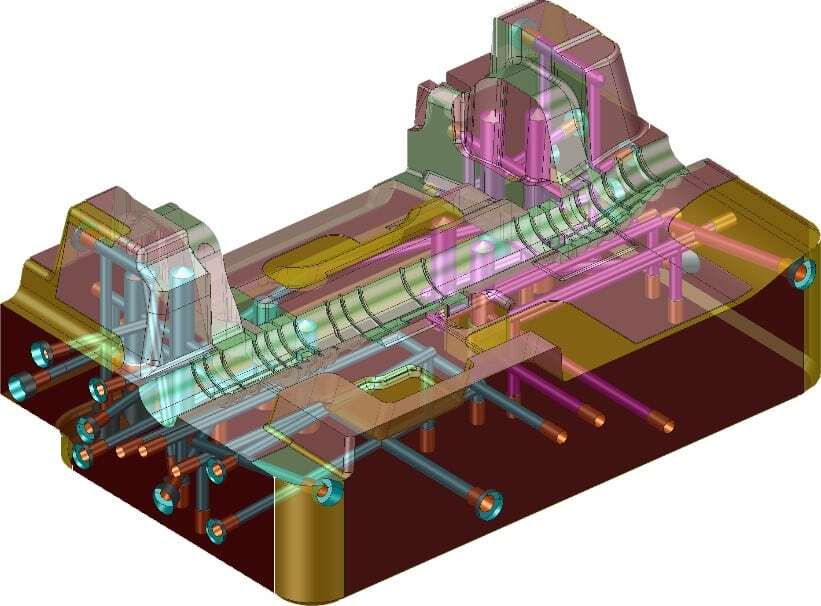
Bauteil bereitgestellt von der Tebis AG
1. Zwei Bohrungen treffen sich im 90°-Winkel
Nicht jede Querbohrung ist problematisch: Treffen zwei Bohrungen in einem 90°-Winkel aufeinander, läuft die Bearbeitung meistens reibungslos ab. In solchen Fällen hat sich ein bestimmtes Vorgehen bewährt, das wir am nachfolgenden Beispiel skizzieren.
Tieflochbohren einer Querbohrung als Sackloch in Stahl
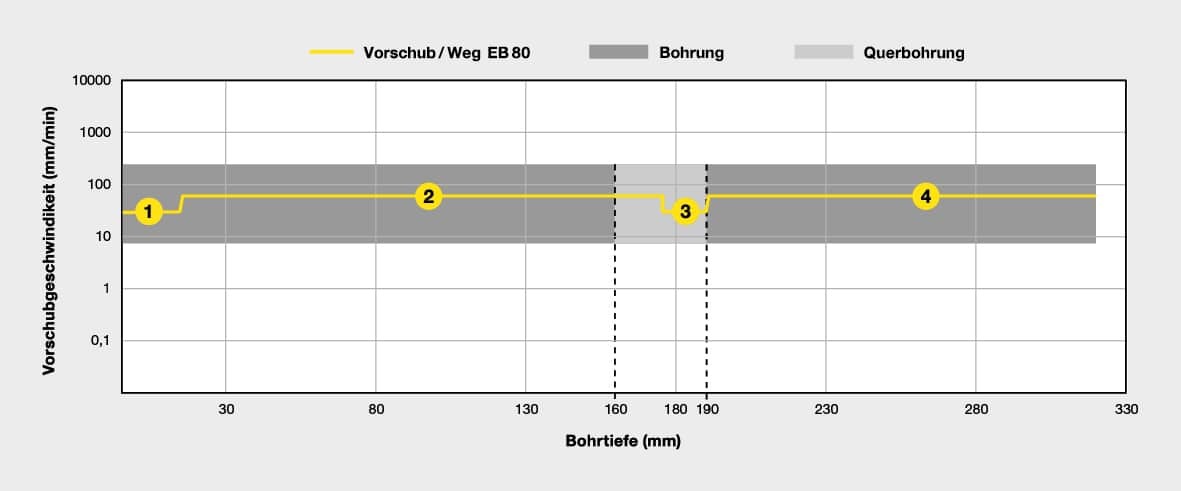
- Wir fahren im linkslauf mit einem reduzierten Vorschubgeschwindigkeit von 30 mm/min und einer Drehzal von 500 U/min in die Pilotbohrung ein. Geführt wird das Werkzeug beim Einfädeln durch die Pilotbohrung mit 12 mm Tiefe.
- Sobald sich der Bohrer in der Bohrung befindet, wird die Vorschubgeschwindigkeit erhöht auf 60 mm/min und mit diesem erhöhten Bohrvorschub bis zur Querbohrung gebohrt.
- Wir treten mit dem gleichen hohen Vorschub in die Querbohrung ein und erst bei Wiedereintritt in die zweite Bohrung reduzieren wir den die Vorschubgeschwindigkeit um die Hälfte von 60 auf 30 mm/min.
- Nach dem Einfädeln in die zweite Bohrung erhöhen wir den Vorschub erneut auf 60 mm/min und bohren die Bohrung mit diesem hohen Vorschub zu Ende.
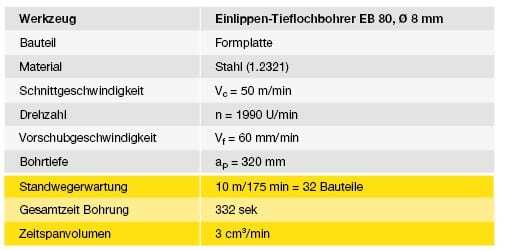
2. Zwei Bohrungen bilden einen kritischen Lückenbereich
Schwieriger wird es, wenn die Kreuzung zwischen den Bohrungen von diesem 90°-Winkel abweicht (s. untere Querbohrung in der Grafik). Auch wenn eine kleine auf eine größere Bohrung trifft (s. obere Querbohrung in der Grafik) entstehen Probleme.
Für genau solche Anwendungen hat Gühring einen Sonderbohrkopf für den EB 80 entwickelt: Dieser VHM-Bohrkopf verfügt über den üblichen Schneidteil mit verjüngter Kontur, der jedoch durch einen geraden Führungsteil um etwa das Doppelte verlängert wird. Dieser Führungsteil stabilisiert das Werkzeug beim Eintritt in die Querbohrung und bewirkt, dass die Bohrspitze beim Wiedereintritt in das Material sicher anbohrt und nicht zu stark zu einer Seite weggedrückt wird. Ein weiterer Vorteil des Führungsteils ist der bessere Bohrungsverlauf. Der üblichen Verlaufswerte von 0,1 mm/100 mm können durch den Führungsteil bis zu halbiert werden.
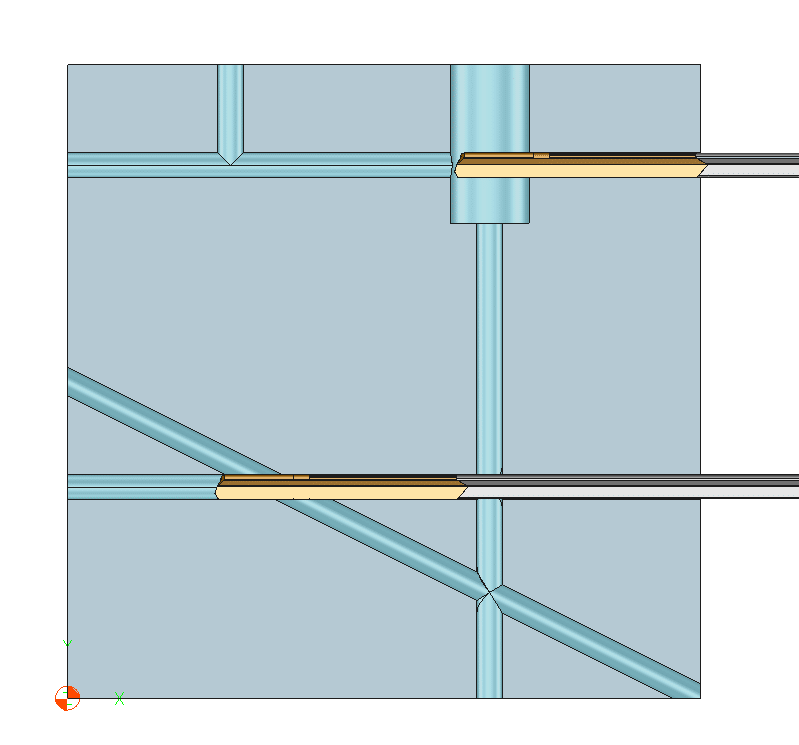

5 Regeln für perfekte Querbohrungen
- kleine Durchmesser vor großen Durchmessern
- tiefe Bohrungen vor kurzen Bohrungen
- Lückenbereiche vermeiden (Druckverlust des Kühlmittels)
- Lückenbereiche, wenn möglich, mit kurzen Bohrern bearbeiten (Torsion)
- Querbohrungen verschließen um Druckverlust und Spanumleitung zu vermeiden
Technische Beratung und Support erhalten Sie auch schnell und direkt über unsere Service-Hotline 00800 2607 2607
Auch auf WhatsApp sind wir für Sie erreichbar: +49 172 658 53 53. Gleich einspeichern!
Das könnte Sie auch interessieren:
Dieser Tieflochbohrer revolutioniert die Gusszerspanung
Wo tiefe Bohrungen in Teile des Antriebsstranges eingebracht werden sollen, sind diese Werkzeuge die Spezialisten. Doch nicht nur ein großer Durchmesserbereich lässt sich mit den Vierschneidern herstellen, sondern auch Bohrtiefen von bis zu 40xD.
Am Puls der Zeit: Taschenfräsen in Titan Grad 5
Ein Kunde setzt Titan Grad 5 für Herzschrittmacher-Batteriegehäuse ein, doch die Bearbeitung des Werkstoffs ist eine Herausforderung. Gühring hat die Lösung: Der Vollhartmetall-Schaftfräser G-Mold 65 HF ermöglichte eine 73-mal höhere Standzeit.
Schnell und dynamisch: Trochoidalfräsen im Formenbau
Vor allem im Formenbau, wo die Zerspanung teils sehr harter Materialien in kürzester Zeit erfolgen muss, hat sich eine Frässtrategie bewährt: Das GTC-Fräsen. Diese Form des Trochoidalfräsens führt zu besonders hohen Standzeiten bei der Bearbeitung.