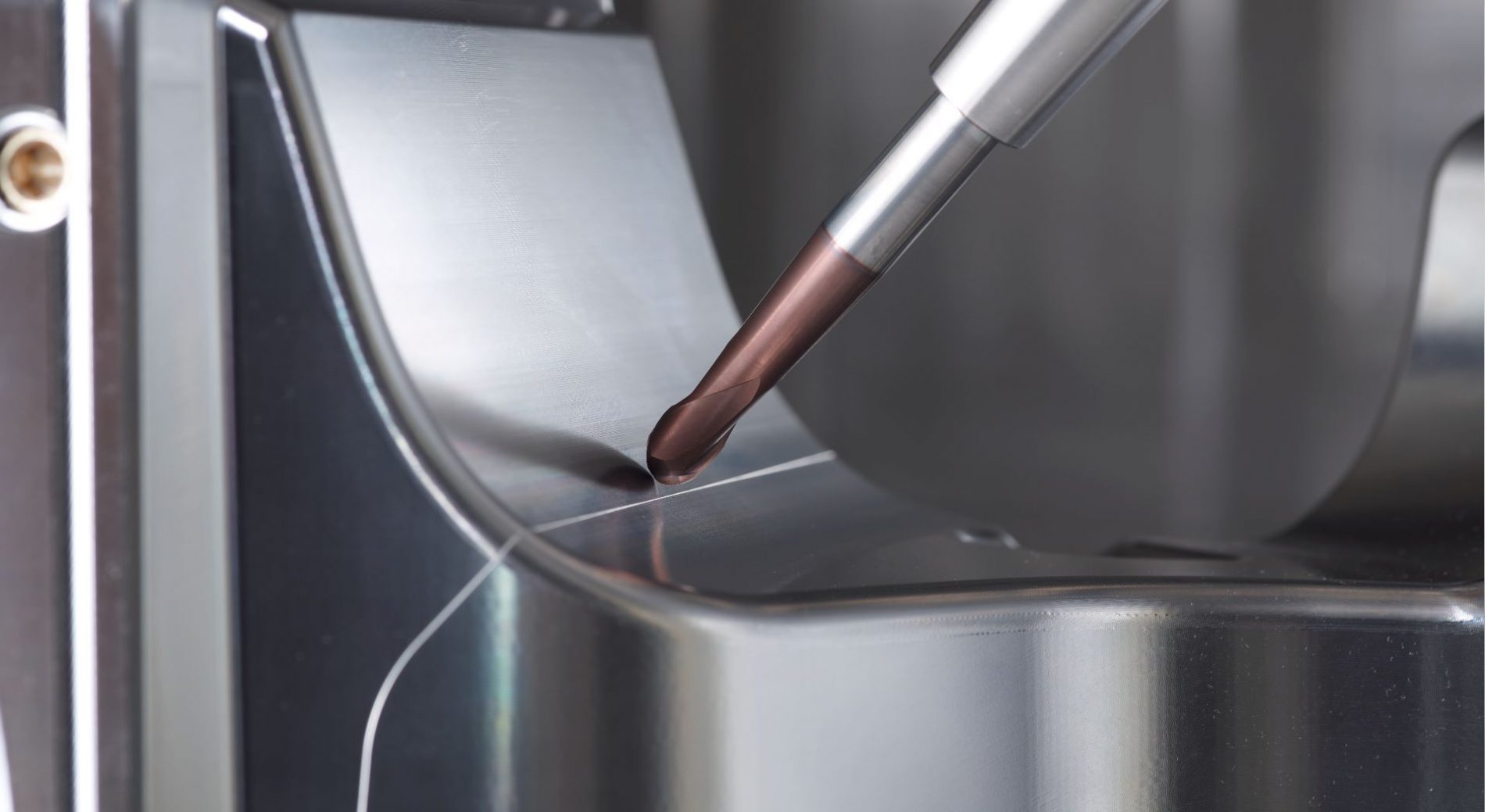
Mould making plays a key role in many industries. Mould makers place high demands on cutting tools – after all, they are a key component in ensuring product quality. This is why Gühring is presenting a new milling cutter range for high-precision finishing requirements at AMB 2022. The combination of new geometry, adapted coating system and ultra-hard substrate makes the high-precision milling cutters so successful when used in hardened tool steel.
Maximum angular and fit accuracy
Whether plastic, metal, glass or chocolate – moulding is what turns raw materials into products. Because these moulds produce the surfaces of the finished components, maximum precision is required here: Only a perfectly manufactured mould can produce a final product with tolerances and surfaces that meet the required quality without reworking. For perfect part quality, mould makers rely on tools that guarantee process reliability, precision and repeatability.
The Swabian tool manufacturer Gühring meets precisely these requirements with a new range of high-precision milling cutters: The μ-precise solid carbide milling cutter cutters have a stable core geometry and an optimised flute profile. Both reduce displacement during milling and ensure stability which is reflected in a very high contour accuracy. This makes the tools suitable for finishing high-precision fits and guides with exact angular accuracy.
Harder substrate, extremely smooth layer
Because tool and mould making involves machining high-strength and hardened steels, Gühring has adapted its carbide substrate to these materials with the new high-precision milling cutters: The cutting material is now around 200 HV harder and finer-grained. This ultra-hard solid carbide substrate guarantees very good edge stability and thus process-reliable service life in hard machining. The precision blanks also have optimised shaft tolerances in the h5 range and are μ-precise in diameter, concentricity and roundness. The radius tolerances are even in the range of +- 5 μm.
The coating system has also been specially adapted for mould making: A Perrox coating produced using the HiPiMS process makes the tool surfaces extremely smooth and therefore very resistant to wear. Thanks to this combination of carbide, coating and geometry, the new high-precision milling cutters promise a significant increase in performance – both in soft and harder materials up to 65 HRC and even in high-alloyed or powder metallurgically manufactured tool steels.
Every milling application covered
With its new G-Mold μ tool range, Gühring can now cover all milling processes in mould making. The solid carbide full-radius milling cutter “G-Mold μ65 B”and the high-precision torus cutter “G-Mold μ65 T” are perfect for copy milling and finishing of moulds and mould inserts made of hardened steel up to 65 HRC. The cylindrical high-precision finishing cutters “G-Mold μ65 F” for hardened workpieces and “G-Mold μ48 F” for soft workpieces enable the optimal angular accuracy and exact fits when finishing guides and pockets in moulding plates.
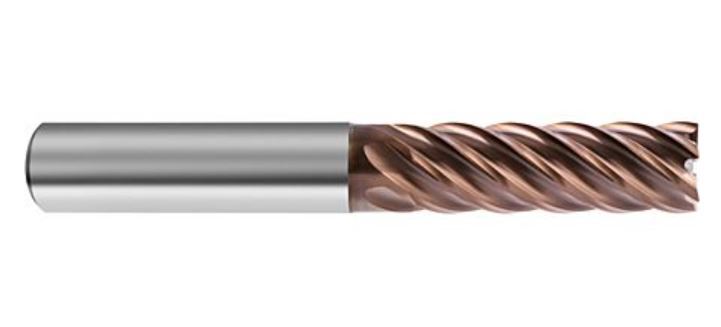
The new μ-precise micro milling cutter “MikroMill µ55 U ”meets high demands in the micro range: Very high-quality surfaces can be achieved with the tightest tolerances and precise concentricity. An FEM-optimised radius angle transition also ensures maximum radial rigidity and low displacement during micro-milling. The innovative GühroJet internal cooling increases the service life of the tool and ensures process reliability.
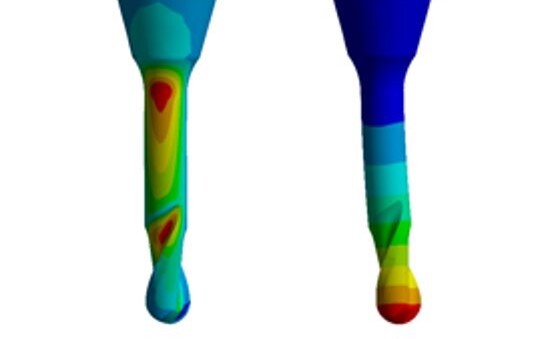
The FEM-optimised radius-angle transition ensures minimal deflection.
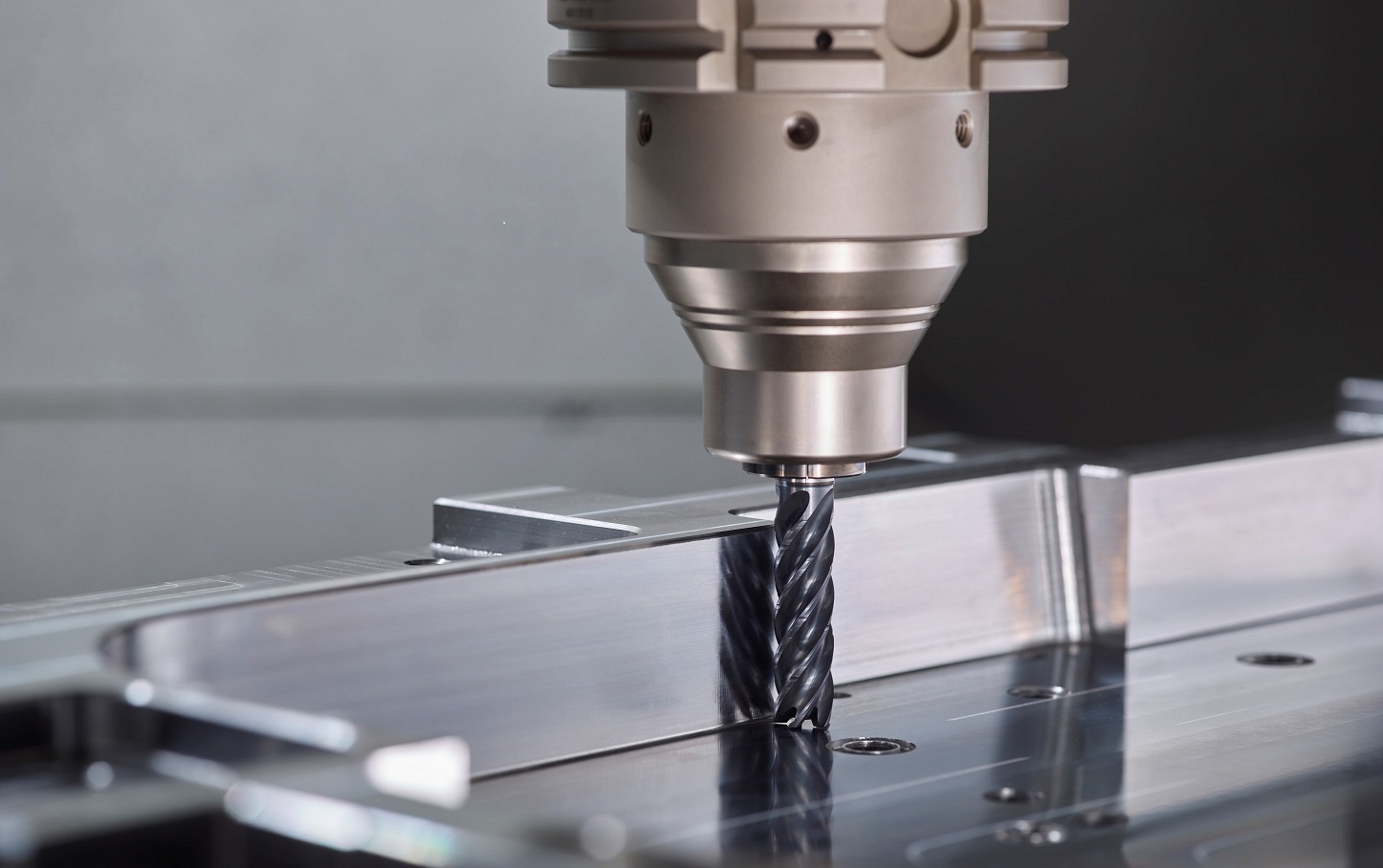
Maximum process reliability thanks to innovative GühroJet internal cooling.
The new range offers a high degree of flexibility with over 350 different dimensions, a wide range of full or corner radii as well as corner chamfers and different versions for hard and soft materials. Because quality counts above all in addition to quantity, the tool manufacturer has invested specifically in specialised production and measuring technologies at its site in Germany – for tools that customers in tool and mould making can rely on.
Have we piqued your interest?
Or arrange your consultation appointment now:
Technical advice and support are also available quickly and directly via our service hotline 00800 2607 2607. We can also be reached on WhatsApp: +49 172 658 53 53. Save the number!
You might also be interested in:
Modular drills: Their advantages and how you can benefit from them
Modular drilling systems such as the BT 800 from Gühring offer full performance at lower costs. Thanks to interchangeable drill heads, you save time, storage space and money – ideal for flexible applications with the highest demands on cost-effectiveness.
Threads for giants: Crane manufacturer relies on modular fluteless tap for blind holes
An innovation – the new modular fluteless tap from Gühring – has made it possible to solve deep-seated challenges in the production of blind hole threads at Karl Georg and to raise process reliability to a new level.
30% more tool life: With this parting off plate you achieve maximum performance in high-grade steel
30% more tool life when parting off: The new 2 mm parting off plate from Gühring’s System 222 impresses with excellent chip control, high process reliability and a perfect surface finish on ISO-M materials such as high-grade steel.