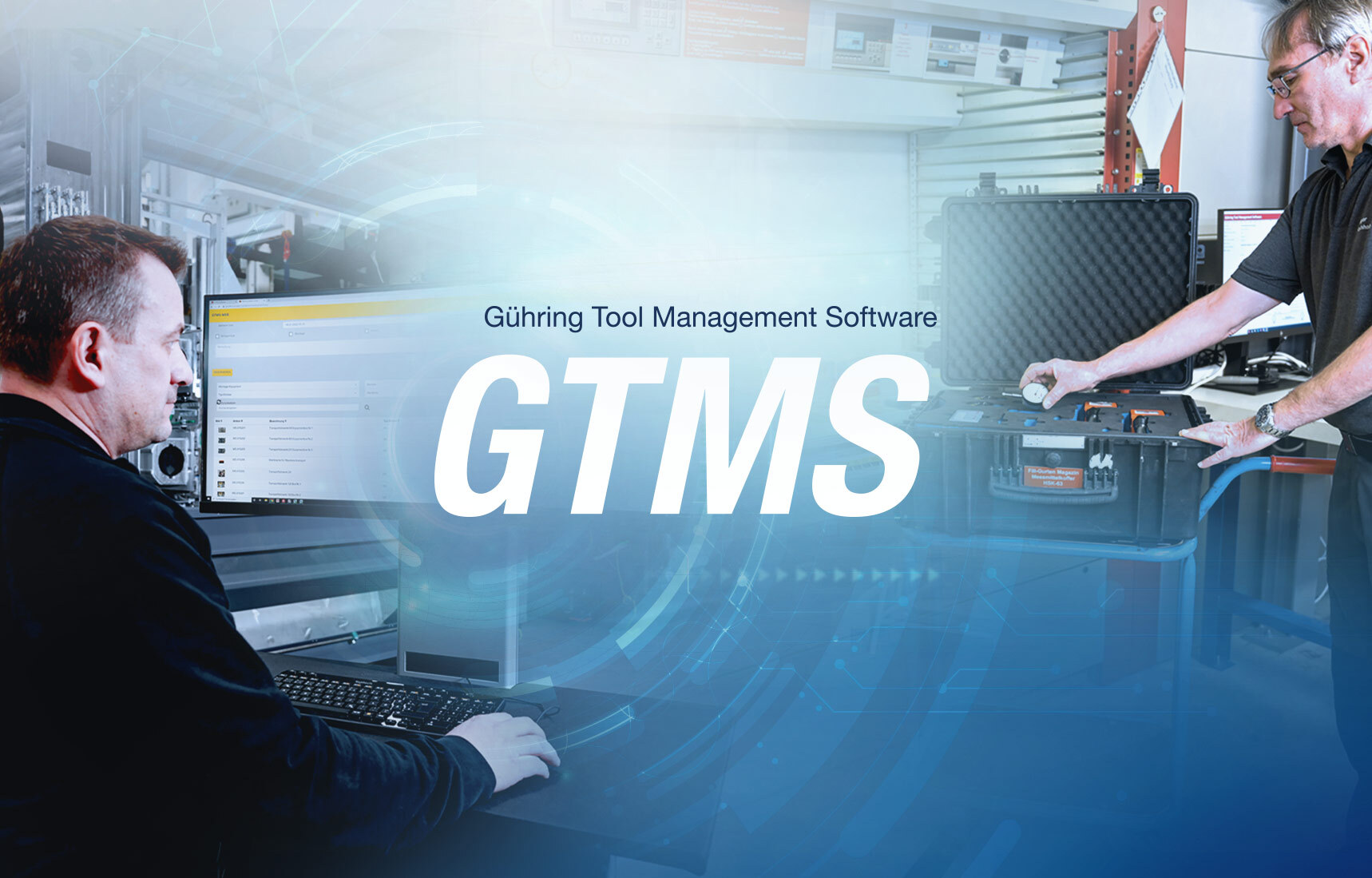
“Have I thought of everything?” Almost everyone asks themselves this question as soon as they get in the car. It is especially important for service technicians who travel to customers on a daily basis and need to take tools or spare parts with them. However, they are often located centrally at the headquarters – and are not accessible on an ad hoc basis. Fill service technicians conveniently select their operating resources online and can simply have their toolbox sent out or prepared at their destination. This is made possible by software from Gühring.
Since 1966, Fill in Gurten, Austria, has evolved into one of the world’s leading machine and plant manufacturers. The family run company is known on the market to be extremely innovative and forward thinking. Experienced Fill technicians and service technicians are therefore employed around the world to guarantee consistently high productivity of Fill machines over their entire life cycle. On-site visits to the customer are part of the day-to-day business of service technicians, who also support the maintenance, optimisation and spare parts management of the production plant after acceptance.
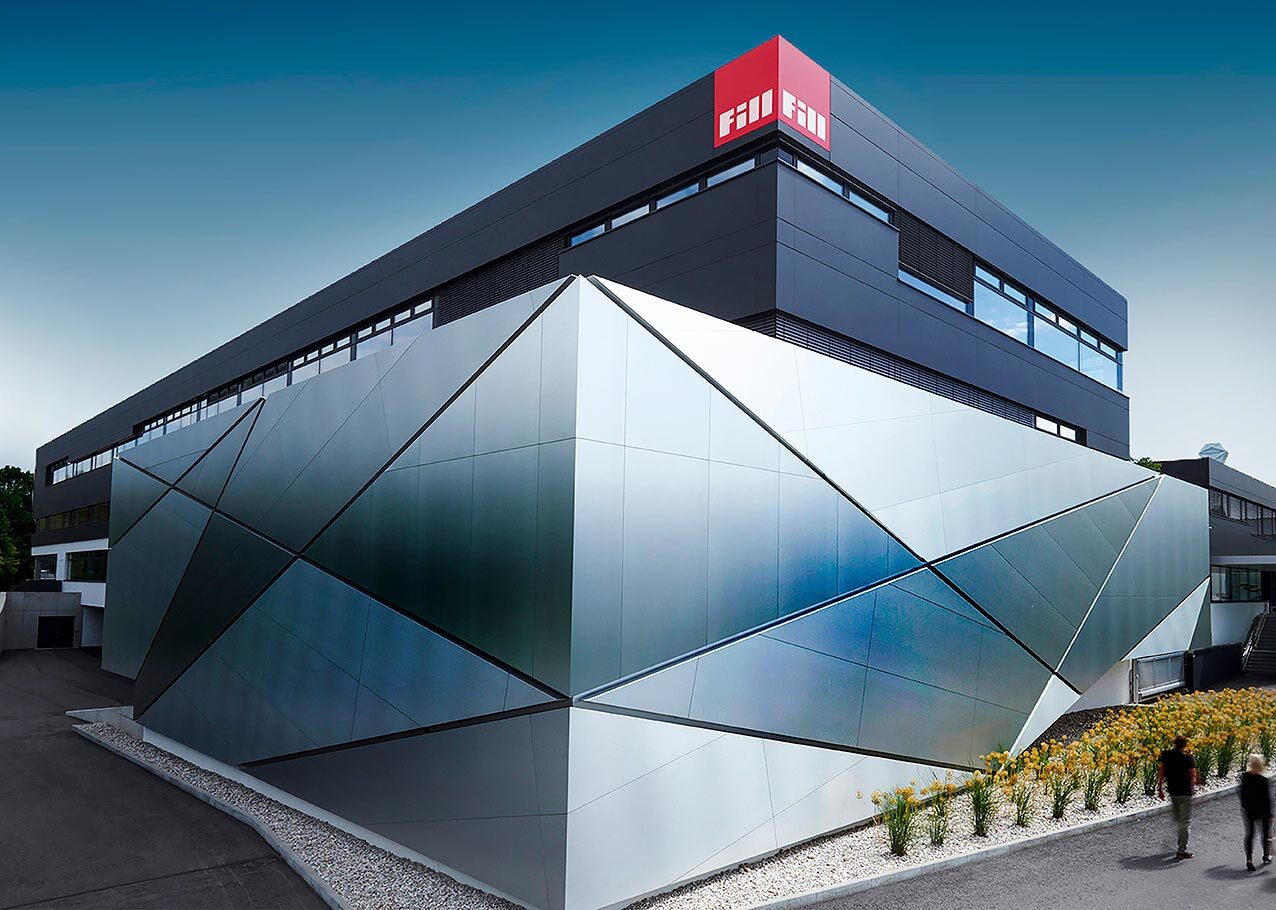
The right operating resources are essential at such customer appointments: Tools, spare parts, but also personal protective equipment such as helmets and gloves. Until recently, Fill had a central storage location for all these articles: A lift system at the Gurten site that was supervised by one store keeper. This was the only place where operating resources could be borrowed from and returned. These withdrawals and returns were not recorded. The service technician simply placed a personalised tool token on the location of the removed operating equipment.
Reducing expensive waits and journeys
Peter Brandstötter, production team leader at Fill, remembers a system with weaknesses: “The strong growth of our company in recent years has made it harder and harder to keep track of the tools and operating resources available.” This meant that Fill technicians had no prior insight into whether the required operating resources were actually available or were even sent away after a long waiting period after discovering the required article was not available at all.
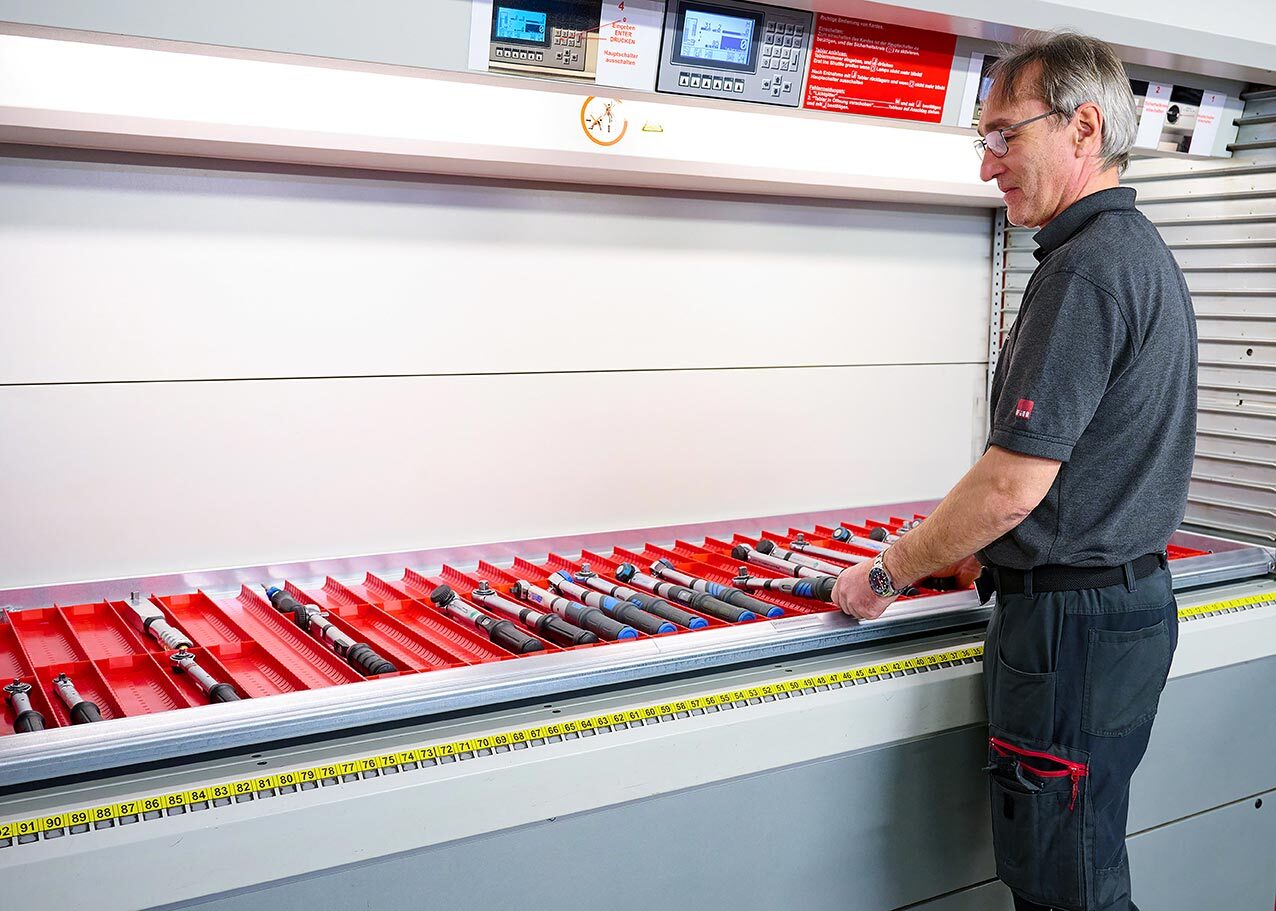
Such unproductive waits and journeys are hugely expensive, so the company decided to redesign the process for dispensing tools and operating resources. A digital solution had to be created that would enable every employee to reserve tools and operating resources via a tablet, smartphone or PC. Fill brought in a long-standing partner for the implementation, because “Gühring had the best concept ready for our requirements,” Brandstötter says.
Product management with GTMS
This concept is based on the Gühring Tool Management Software (GTMS). Originally developed for controlling Gühring tool cabinets, almost all products can now be managed using this software. This is not an off-the-shelf solution, it is flexibly adapted to the needs of customers. Uwe Reich, sales manager for digitalisation at Gühring, adds: “The GTMS has already given us many opportunities to digitise this process, we only had to tailor it to Fill.” For this purpose, Gühring initially installed a tool dispensing system at Fill, in which all tools and fast-moving consumables for service technicians are now managed digitally.
Operating resources and spare parts are still stored in the lift system, but each article has been added to the database. The result: The lift system with all travel commands now is now managed and controlled automatically via the GTMS. All booking processes are linked to Fill’s ERP system. Data is still maintained in the customer’s ERP system.
The “digital service technician”
This year, the process has been extremely straightforward for the service technicians: They log in to the Fill intranet with their personal login details. No matter where in the world they are. They then fill a digital shopping cart with all the required operating resources. As soon as they save this shopping cart, a corresponding reservation is generated in GTMS.
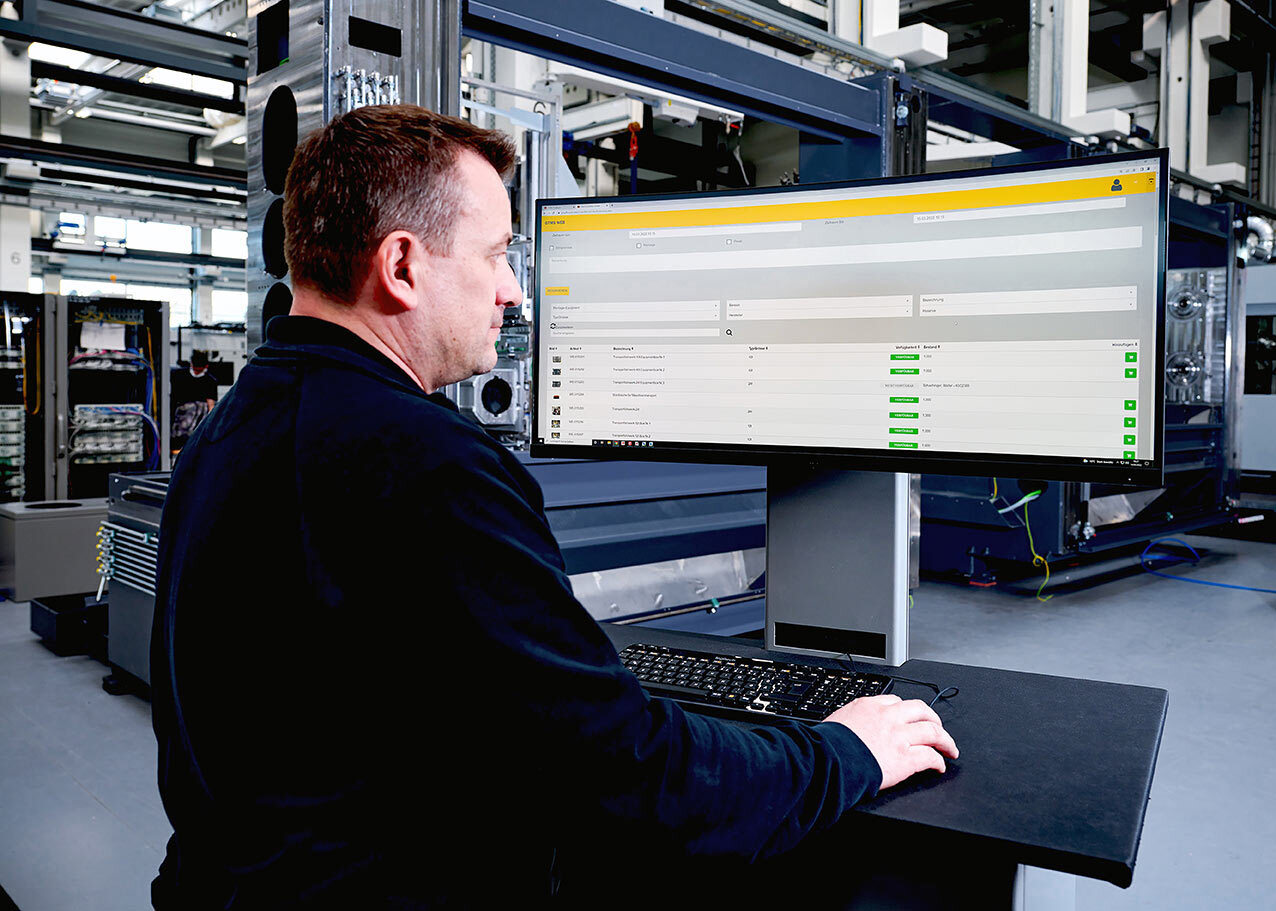
Tools that are subject to an inspection interval are blocked by the system on the inspection date and the responsible internal inspection body is automatically informed. GTMS then converts the booking of the service technician into a picking order. The store keeper receives a packing slip, from which he simply enters the individual articles into the lift system – and all the required operating resources are then dispensed to it.
“From now on, service technicians can concentrate entirely on service,” explains Uwe Reich. “And the store keeper always knows who needs what and when it will come back.”As Brandstötter reports, GTMS makes daily work much easier for Fill employees: “Our fitters and service technicians love this innovative software solution and could no longer imagine organising tools without it.” There are also many advantages from a business perspective.
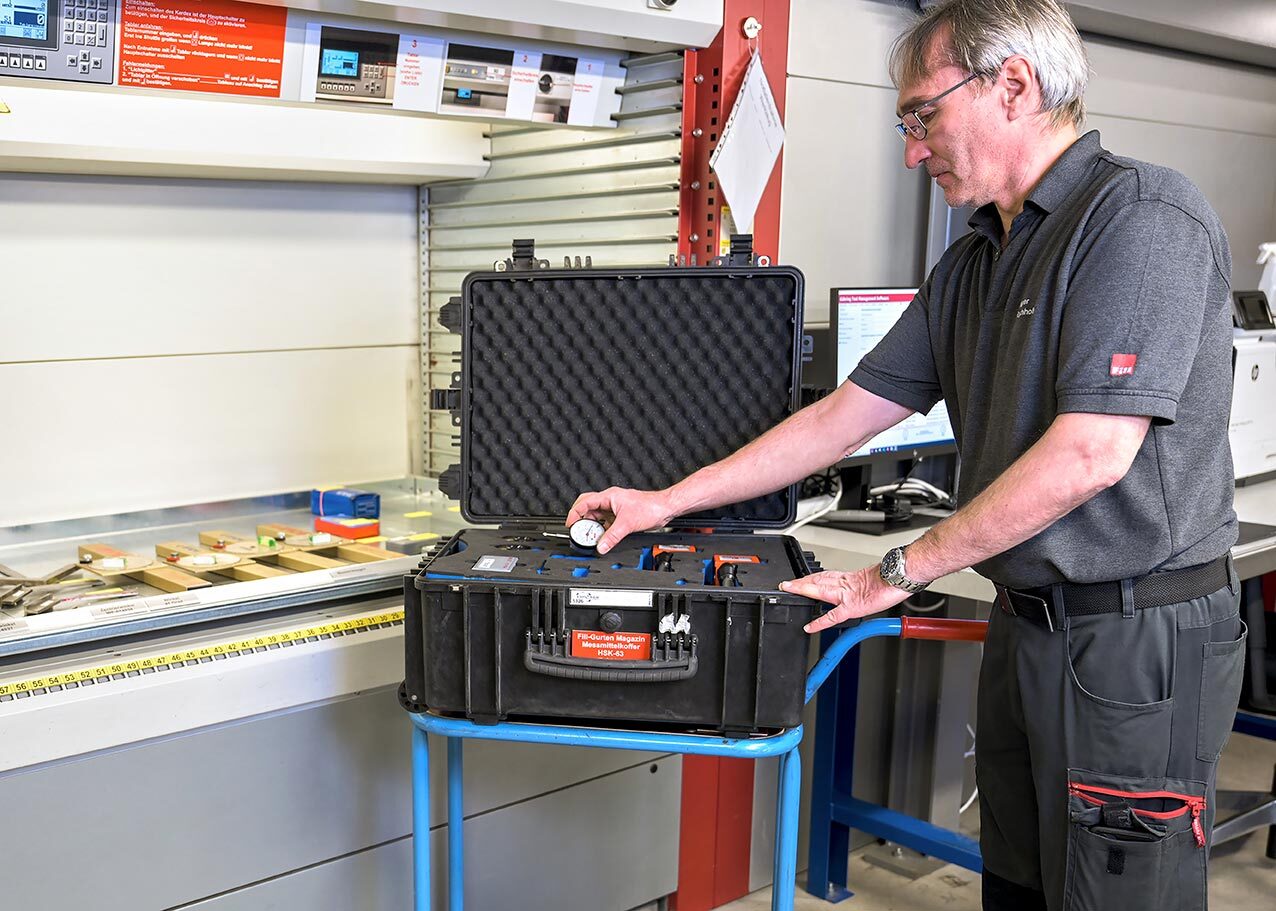
Processes are optimised and efficiency is increased. Thanks to greater transparency regarding articles in circulation, it is possible to track where the operating resources are currently located at any time.“Thanks to the digital solution, waiting and travel times were greatly reduced,” Brandstötter notes. He is also enthusiastic about the cooperation between the two companies: “The implementation process with the Gühring software developers was very professional and straightforward.”
For Uwe Reich, the order is an example of how software solutions simplify everyday life: “This is a perfect example of classic digitalisation: Manual paperwork becomes a perfectly thought-out, digital process. And the customer is grateful.”
Have we piqued your interest?
Then arrange your personal consultation appointment now:
Technical advice and support are also available quickly and directly via our service hotline 00800 2607 2607
We can also be reached on WhatsApp: +49 172 658 53 53. Save the number!
You might also be interested in:
Conserving resources for the future: 5 reasons for carbide recycling
Save resources and benefit from carbide recycling with Gühring! Exchange worn tools for money and reduce your carbon footprint. Simple, sustainable and efficient.
Tool management in flux: Keeping track with digital tech
Getsch+Hiller optimiert mit der Gühring Tool Management Software (GTMS) seine Werkzeugverwaltung. Dank digitaler Ausgabeschränke und modularer Software spart das Unternehmen Zeit, reduziert Kosten und bleibt flexibel – perfekt angepasst an das schnelle Wachstum der Medizintechnik.
Detailed data on your tools: The GTMS tool data module
Increase your efficiency with the GTMS tool data module. Avoid sources of error, optimise set-up times and gain full transparency over tool requirements and component costs. Experience precise tool data management for maximum control.