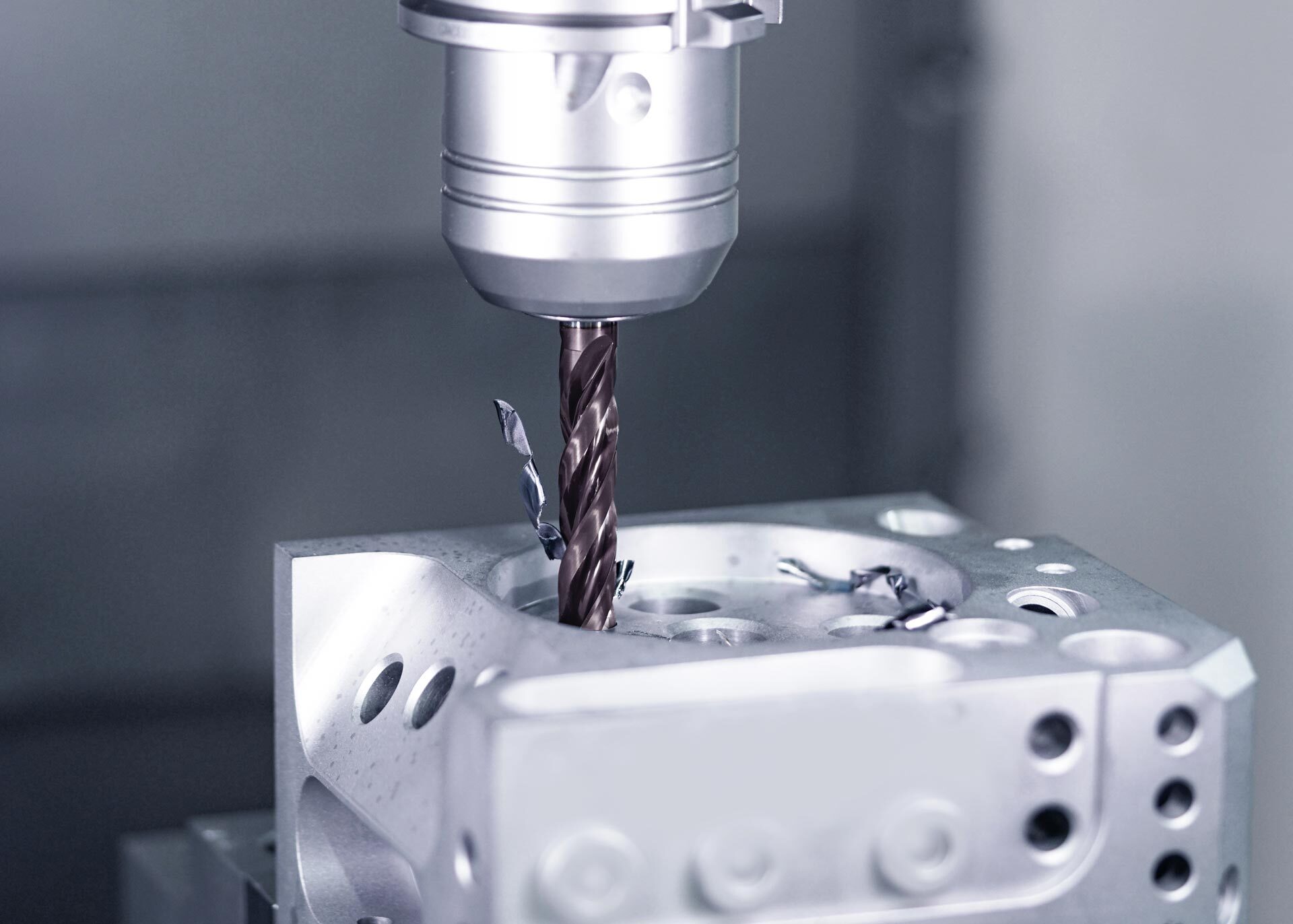
Higher feed rate thanks to a third cutting edge? This is what is promised by a new high-performance drilling tool for steel and cast materials from Gühring. The problem of chip removal is resolved by an optimised flute profile and coolant ducts with a particularly large cross-section.
You put in a lot, you get a lot out. But does this saying also apply when it comes to the number of cutting edges on solid carbide drills? Actually, it seems logical: By adding a third cutting edge, the tool will drill at higher feed rates and reduce machining time. But it’s not that easy, because the problem with three-fluted cutters often arises when it comes to chip removal.
Compared to two-fluted tools, the individual chip space is significantly smaller in three-fluted tools. As the number of cutting edges increases, higher feed rates become possible, but this also results in a higher chip volume, which can be more difficult to remove through the smaller chip spaces. The result? Chips get stuck in the chip space, you have to deal with chip jams and, in the worst case, drill breakage.
But Gühring is launching a new three-fluted cutter with high feed rates that cuts machining time while also solving the chip problem: the FT 200 U. This is made possible by an optimised flute profile, which rolls the chips up tightly and breaks them reliably. At the same time, an internal cooling duct with the maximum cooling duct cross-section ensures effective chip removal and optimum thermal management. The solid carbide drill showcases its strengths when machining steel and cast materials in particular. For example, feed rates of 5 to 6 percent of the tool diameter can be achieved in steel.
Spiropoint grind for perfect self-centering
In terms of dimensional accuracy, three-fluted tools have the edge over two-fluted tools, which is primarily due to their better centring properties. The FT 200 U goes one step further here and ensures perfect material penetration with its Spiropoint tip in combination with specially designed web thinning. Thanks to the specially developed Spiropoint grind, the point angle is similar to a funnel that rises in a spiral shape. This point grind ensures that the tool centres itself very well, spot drills precisely and thus creates very dimensionally stable holes with a high standard of quality.
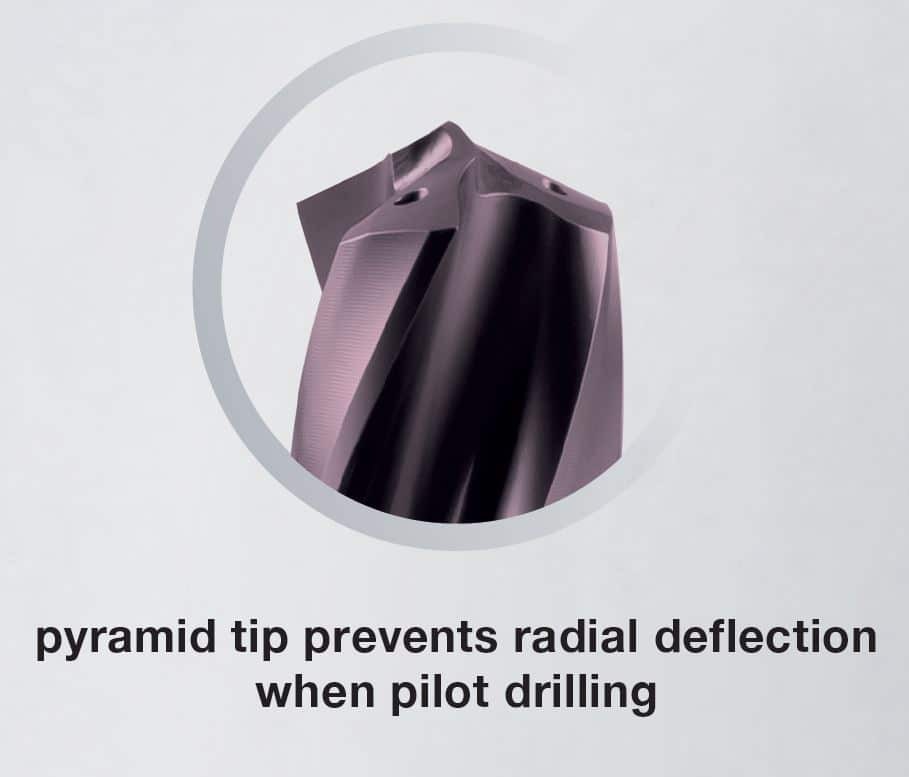
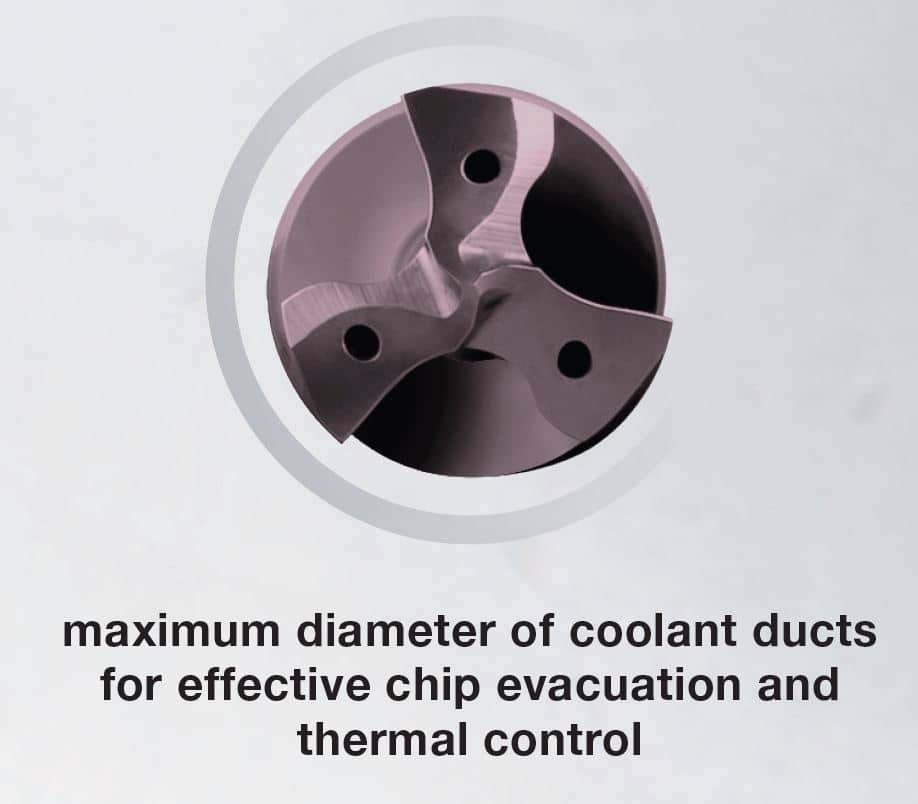
In addition, the Spiropoint grind enables very good running smoothness and cutting edge stability, which prevents chipping on the main cutting edges. The very high-grade carbide and protective nanoFire coating also delay tool wear.
Your advantages with the FT 200 U
- Powerful and smooth under all operating conditions
- High feed drilling for reduced cycle times and cost-efficient machining
- Reduced hardening of the edge layer
Thanks to all these properties found in the FT 200 U, high-feed drilling can be achieved with the solid carbide drill, also resulting in reduced cycle times and cost-effective machining. The tool is available in the length 5xD and from autumn 2023 also in 3xD and in a diameter range of 4 to 20 mm.
Save money by reducing your tool requirements
However, the FT 200 U does not just have the edge over two-fluted concepts: The new Gühring drill also managed to impress in a direct comparison with a competitor’s three-fluted cutter. When creating a through-hole in a cast iron lid (GGG-60), the FT 200 U had double the tool life. The Gühring tool enabled 220 components to be machined with one drill, while the competitor’s drill only produced 110 components before the tool change. For the customer, this means a significant saving, because the lower tool requirement alone leads to a total cost saving of 5 percent. And it will also be cheaper for the customer over the long term: While the FT 200 U can be reground up to three times, the competitor’s drill can only be reground once.
This might also be interesting for you:
Modular drills: Their advantages and how you can benefit from them
Modular drilling systems such as the BT 800 from Gühring offer full performance at lower costs. Thanks to interchangeable drill heads, you save time, storage space and money – ideal for flexible applications with the highest demands on cost-effectiveness.
With three cutting edges, you can create a 180° hole base faster than ever before
While competitors rely on two cutting edges in their 180° flat drills, Gühring is launching a three-fluted tool. And to great success: The FB 200 U excels with up to 50% higher cutting values, process reliability and better hole quality.
From difficult-to-machine to aluminium: 3 new material specialists
Discover three new specialists from Gühring for reliable drilling in stainless steel materials, titanium and aluminium. They guarantee optimum results thanks to their extra smooth surfaces, polished flutes and effective internal cooling.