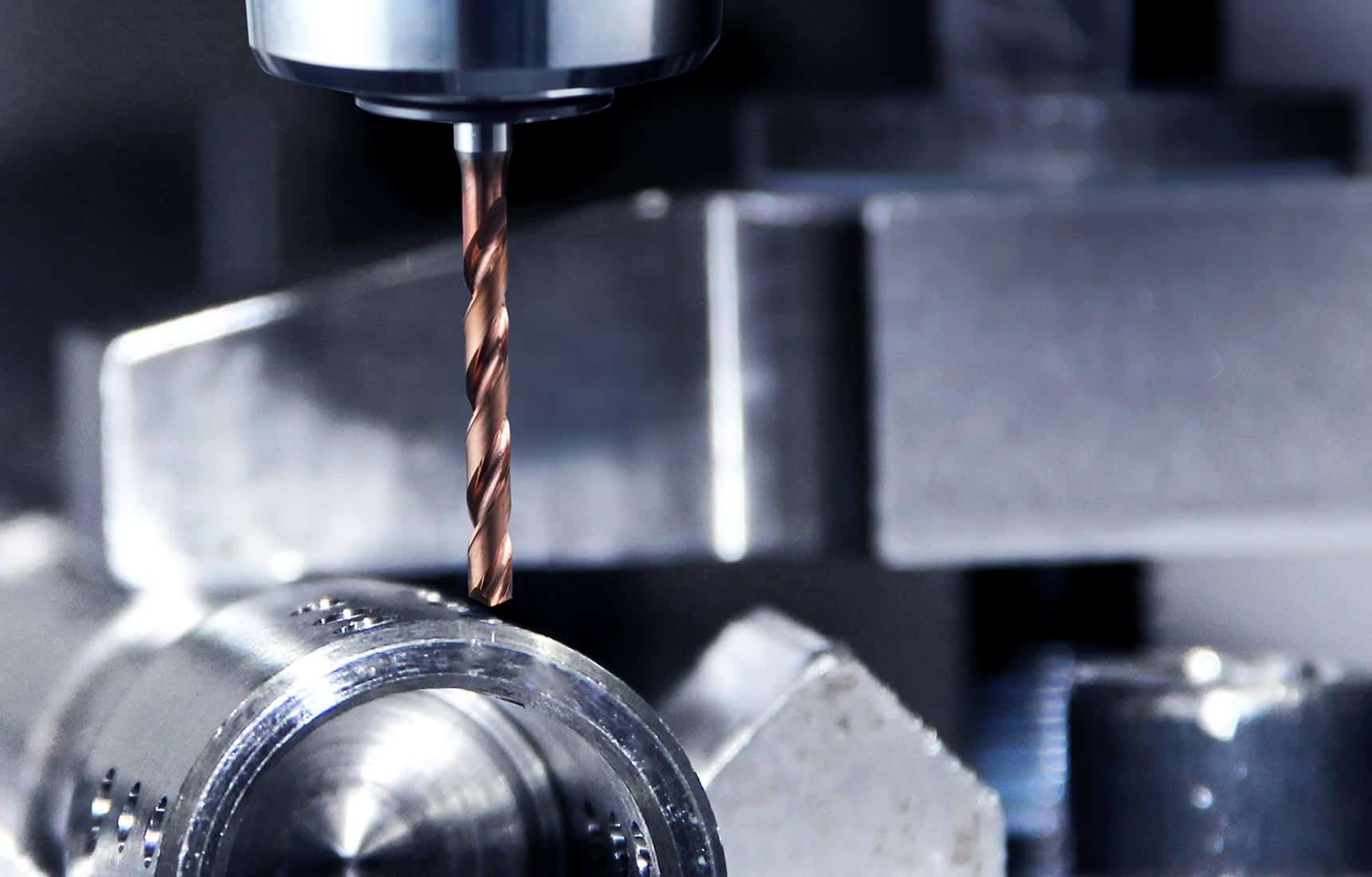
Table of contents
1. Challenges when drilling in difficult-to-machine materials
2. Our 3 tool highlights for drilling aluminium, titanium and stainless steel materials
2a. Drill 1: ExclusiveLine micro-precision drill VA for micro-drilling in difficult-to-machine materials
2b. Drill 2: Solid carbide drill RT 100 InoxPro for high feed drilling in stainless steels
2c. Drill 3: Deep hole drill RT 100 T AL for deep hole drilling without material adhesion
3. FAQs: The most important questions about drilling stainless steel, titanium and aluminium
Here we present three new drill specialists specially designed for machining materials such as INOX, aluminium, titanium and stainless steel. With their extra smooth surfaces, they ensure reliable chip formation and removal during machining. Polished flutes and a superior surface quality in the web thinning prevent material from sticking to the cutting edges and creating built-up edges during drilling. Effective internal cooling also ensures that the temperature in the cutting zone is lowered and chips are flushed out of the hole. These tools are ideal for precise machining of a wide range of materials.
Challenges when drilling in difficult-to-cut materials
Regardless of whether they are deep holes, micro holes or regular blind holes – reliable chip removal is often a critical issue when drilling. But some materials make machining especially difficult. For example, aluminium or stainless steels create built-up edges or, in some cases, particularly long chips during machining. If these built-up edges are not prevented and the chips are not removed effectively, there is a risk of the cutting edges breaking away or the chips clogging the hole.
Added to this is the high heat build-up in stainless steels and titanium alloys. If this heat is not dissipated properly, it can lead to problems such as tool wear. These factors make machining stainless steel materials, titanium and special alloys and non-ferrous materials a complex task that requires special tools to be selected. We are introducing three new specialists with a few common features: The RT 100 T AL deep hole drill, the ExclusiveLine VA micro-precision drill and the RT 100 InoxPro solid carbide drill.
Our 3 tool highlights for drilling aluminium, titanium and stainless steel materials
Drill 1: ExclusiveLine micro-precision drill VA for micro-drilling in difficult-to-cut materials
Special alloys, titanium and stainless and high-alloy steels can be easily machined with the stainless steel version of the ExclusiveLine micro-precision drill. This is made possible thanks to its newly developed flute profile with a concave main cutting edge, which promotes more aggressive cutting behaviour. In this way, it also produces easily removable short chips in long-chipping materials such as aluminium, brass or copper. As a result, drilling depths from 3xD to 15xD can be achieved with the micro-precision drill. In addition, the Perrox coating provides excellent protection against abrasive alloying constituents and prevents built-up edges, resulting in long tool lives and high feed rates.
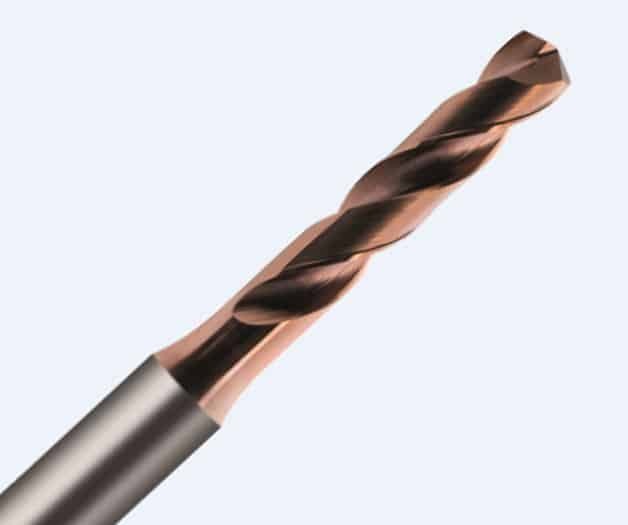
Your advantages when machining stainless steels:
- up to twice the feed rate
- long tool life thanks to Perrox coating
- newly developed flute profile with a concave main cutting edge for aggressive cutting behaviour
In long-chipping materials, the micro-precision drill creates short chips that can be easily removed. This is made possible thanks to its newly developed flute profile with a concave main cutting edge, which promotes more aggressive cutting behaviour. In addition, the Perrox coating provides excellent protection against abrasive alloying constituents. The carbide for the micro-precision drill is also perfect for machining stainless and high-alloyed steels. Thanks to all these features, long-chipping non-ferrous materials, such as aluminium, brass or copper, also aren’t a problem for the micro-precision drill.
Tool | ExclusiveLine micro-precision drill VA, Ø = 2.05 mm |
Material | X6CrNiMoTi17-12-2 (1.4571) |
Cutting speed | Vc = 80 m/min |
Feed rate | fz = 0.0615 mm |
Cutting depth | ap = 30 mm |
Drill 2: Solid carbide drill RT 100 InoxPro for high feed drilling in stainless steels
The new RT 100 InoxPro solid carbide drill has been specially designed for the production of precise holes in stainless steels and titanium materials and promises the highest cutting values and a long tool life. Thanks to its wide range of diameters from 3 to 20 mm, this drill can be used flexibly. Three versions of the tool are available: 3xD, 5xD and 7xD.
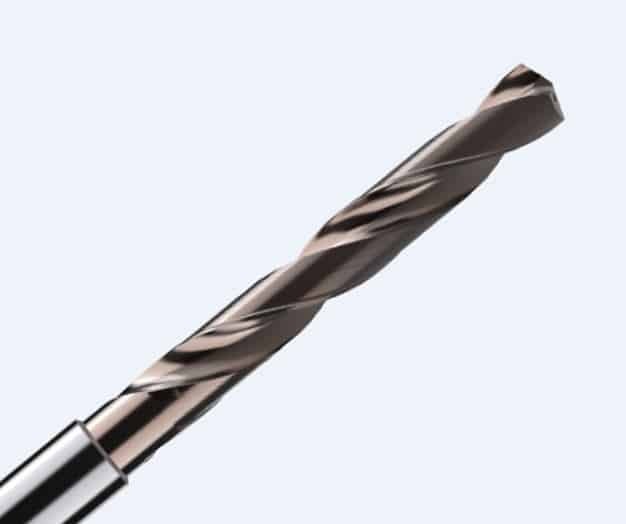
Your advantages when machining stainless steel
- up to 50 % higher feed rate in stainless steels
- maximum tool life thanks to wear-resistant Perrox coating
- optimum chip control and removal
- maximum process reliability even with deep holes up to 7xD and large diameters
As well as the polished flutes, Gühring’s own Perrox coating, which covers the tool, offers very high wear protection. Gühring has also adapted its carbide substrate specifically for machining stainless steel materials: An improved combination of hardness and toughness in the cutting material means that the cutting edge does not break, even under high loads. A new drill geometry has been developed with the same aim in mind: The optimised sickle-shaped cutting edge and the stronger taper of the tool minimise the tendency to jam in stainless steel.
Tool | RT 100 InoxPro Ø 3, 7xD |
Material | X46Cr13 (1.4034) |
Cutting speed | Vc = 100 m/min |
Feed rate | f = 0.09 mm/U |
Cutting depth | ap = 17.5 mm |
Drill 3: Deep hole drill RT 100 T AL for deep hole drilling without material adhesion
The RT 100 T AL is Gühring’s new specialist for deep hole drilling in aluminium. This tool is used for machining a wide range of components, such as cylinder heads, hydraulic blocks and various moulded parts. The deep hole drill’s strengths really come to the fore in aluminium with a silicon content of less than nine percent. But the tool can also be used above this. Four guide chamfers ensure the necessary stability during deep hole drilling. Diameters range from 3 to 14 mm and when it comes to drilling depth, the customer can choose between 15xD, 20xD and 25xD versions.
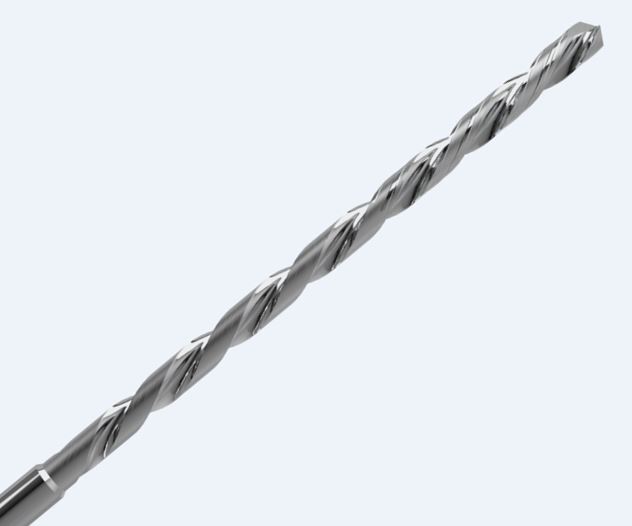
Your advantages in aluminium machining
- virtually no material adhesions
- 30 % longer tool life and higher cutting data in aluminium and aluminium alloys
- high hole accuracy and very low deviation from concentricity
This drilling tool also has polished surfaces with the lowest Rz values for the flute and web thinning. This reduces the adhesive effect of the aluminium. The deep hole drill is delivered with bright surface finishes as standard but can be coated optionally.
Tool | RT 100 T AL Ø 5,00 mm, 25xD |
Material | AlSi9 (3.2573) |
Cutting speed | Vc = 120 m/min |
Feed rate | f = 0.25 mm/rev |
Cutting depth | ap = 125 mm |
Have we piqued your interest?
Technical advice and support are also available quickly and directly via our service hotline 00800 2607 2607 We can also be reached on WhatsApp: +49 172 658 53 53. Save the number!
FAQs: The most important questions about drilling stainless steel, titanium and aluminium
What are the main differences in machining stainless steel compared to conventional steel?
Stainless steel often contains alloying constituents, such as chromium and nickel, which provide corrosion resistance but also affect machinability. Using specific cutting materials and adjusted cutting speeds is essential here.
Which types of tools are best suited for aluminium machining?
For aluminium, carbide tools are ideal as they provide the sharpness and wear resistance needed to ensure precise cuts.
How does the cutting speed influence the quality of aluminium machining?
With aluminium, high cutting speeds are important to achieve a good surface finish. However, it is important to find a balance to prevent the material from melting.
What makes titanium a difficult material for machining?
Titanium is known for its strength and temperature resistance, which makes it difficult to machine without special tools and techniques as it has a tendency for tool wear and heat build-up.
What strategies improve tool life with titanium machining?
The use of cooling strategies, optimised cutting parameters and the use of tools with special coatings are crucial for extending tool life.
What are common mistakes in stainless steel, aluminium and titanium machining and how can they be avoided?
Common mistakes include not adjusting the cutting parameters and selecting the wrong tool. These can be avoided with careful planning of the machining processes and training of personnel.
To what extent do the material properties of stainless steel, aluminium and titanium influence the economic efficiency of the machining processes?
Material costs, tool wear and machining times vary greatly based on material properties. Efficient machining therefore requires a detailed cost-benefit analysis.
You might also be interested in:
150 % longer tool life: the interchangeable head drilling system for maximum cost-effectiveness
Modular drilling systems enable quick head changes within the machine – but if process reliability is lacking, the time savings can quickly become negligible. The BT 800 demonstrates that simple handling and performance don’t have to be mutually exclusive.
Maximum economic efficiency: Modular drill reduces set-up times and scrap for the customer
Tool life up, machining times down: With the BT 800 interchangeable head drilling system, the company Kurt Metallverarbeitung has found a modular solution that not only impresses with simpler handling, but also with outstanding performance.
Modular drills: Their advantages and how you can benefit from them
Modular drilling systems such as the BT 800 from Gühring offer full performance at lower costs. Thanks to interchangeable drill heads, you save time, storage space and money – ideal for flexible applications with the highest demands on cost-effectiveness.