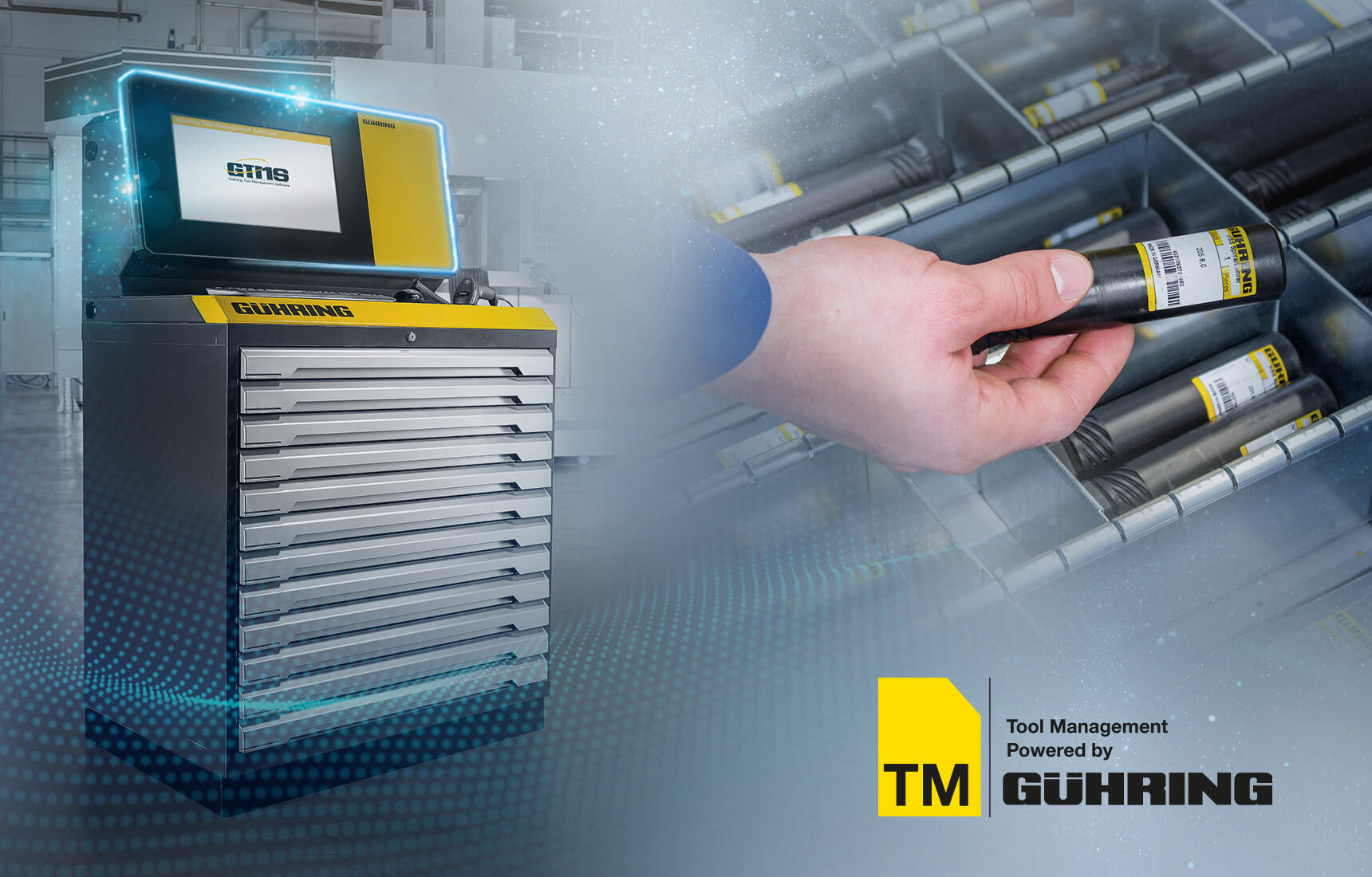
Your tool management solution, but lack the time to make changes alongside your day-to-day business? The tool managers from Gühring specialise in topics such as logistics, procurement and scheduling. This allows you to concentrate completely on the tasks that generate value for you – for added efficiency in your business.
A wide variety of tools are stored loose on shelves that are so high that employees have to climb ladders to look for the right tool: This was the situation at Hewi G. Winker in the summer of 2019. The tool situation at the automotive supplier based in Spaichingen in Baden-Wuerttemberg was too confusing as the range of variants from ten different tool suppliers was far too wide and the sensible, ergonomic removal of tools was almost impossible.
And the situation at Hewi is the same for a huge number of other companies, as some of our case studies show: Foremen spend up to 60% and machine operators spend up to 20% of their time searching for tools, resulting in overall machine availability falling by around 9%. A total of 16% of all workflow interruptions are due to a lack of tools. Most companies are aware of these shortcomings, but there is no time for improvement alongside day-to-day business.
This is where Gühring comes in, says Marcello Mintrone, sales manager in the tool management team: “When talking to customers, I often feel that tool management is seen as a necessary evil. Time and expertise flow mainly into production and technology. It is precisely this necessary evil that is our core business. As a tool manager, we have specialised purely in topics such as logistics, procurement and materials planning.” This means that the customer is spared the non-value-adding tasks, which increases efficiency in the company.
Tailor-made tool management
Tool management from Gühring is a very flexible service that is individually adapted for each customer. For this purpose, the Gühring tool managers first analyse the company’s entire tool management system, including the tool cycle, work preparation, tool storage and production areas. Based on these analyses, organisational weaknesses and optimisation solutions are identified and corresponding concepts are determined.
This also includes suggestions for outsourcing processes and functions as well as for the use of tool management software and hardware. The customer can then compile an individual service package from five modules with different services. “This is our menu from which you can put together your meal,” explains Marcello Mintrone. “We are completely flexible and do not force the customer into a rigid system.”
The “Power menu”
When the customer has chosen the “ingredients” required in their production facilities and combined them into a customised tool management package, there are two different processes: The customer can either specify which tool from which supplier is used in their company.
Gühring acts as the central coordinator for procurement and refurbishment. “We offer the customer a uniquely high level of transparency with regard to the procurement of Gühring and third-party tools and in all removal and billing processes,” explains Marcello Mintrone.
Another option is to hand over responsibility for all tooling to Gühring. In this case, our project team on-site takes over the scheduling and ordering of all tools, the monitoring of delivery dates, incoming goods inspections and the management of the tool warehouse, but also the assembly and pre-calibration of new tools. The service also includes the continuous technological optimisation of tools and processes and comprehensive reporting.
Tool application
- Assembly and pre-setting
- Disassembly
- Assessment
- Despatch for refurbishment
- Scrapping
Process optimisation
- ABC analysis of tooling costs
- Analysis of unstable processes
- Action plan
- Target pursuit
Process planning
- Cut index
- Tool design
- Technology parameters
- Manufacturing data
- Planning of the original equipment
Tool maintenance
- Tool collection
- De-coating, re-grinding
- Modification
- Tool delivery
Logistics
- Determination of requirements
- Disposition and procurement
- Consignment stock
- Incoming goods inspection
- Collection of worn tools
- Set-up of the automated tool dispensing systems
Exploiting full potential
The end result is a tool management solution that optimally meets the wishes and requirements of the customer and brings in corresponding optimisations. Experienced tool managers on-site ensure that these improvement concepts are also implemented promptly and that the optimisation goals are achieved. Because only measures that have actually been implemented are effective.
In this way, you can achieve your optimisation goals much faster. Hewi also decided to hand over logistics completely to the Gühring tool managers, who also looked for optimisation potential in tool management. This enabled tool variety to be reduced by 33%. Optimising the tools themselves will lead to a 20% reduction in tool costs and thanks to better tools, the company will save almost 32 days of machine runtime per year.
Have we piqued your interest?
Then arrange your personal consultation appointment now:
You might also be interested in:
Conserving resources for the future: 5 reasons for carbide recycling
Save resources and benefit from carbide recycling with Gühring! Exchange worn tools for money and reduce your carbon footprint. Simple, sustainable and efficient.
Tool management in flux: Keeping track with digital tech
Getsch+Hiller optimiert mit der Gühring Tool Management Software (GTMS) seine Werkzeugverwaltung. Dank digitaler Ausgabeschränke und modularer Software spart das Unternehmen Zeit, reduziert Kosten und bleibt flexibel – perfekt angepasst an das schnelle Wachstum der Medizintechnik.
Detailed data on your tools: The GTMS tool data module
Increase your efficiency with the GTMS tool data module. Avoid sources of error, optimise set-up times and gain full transparency over tool requirements and component costs. Experience precise tool data management for maximum control.