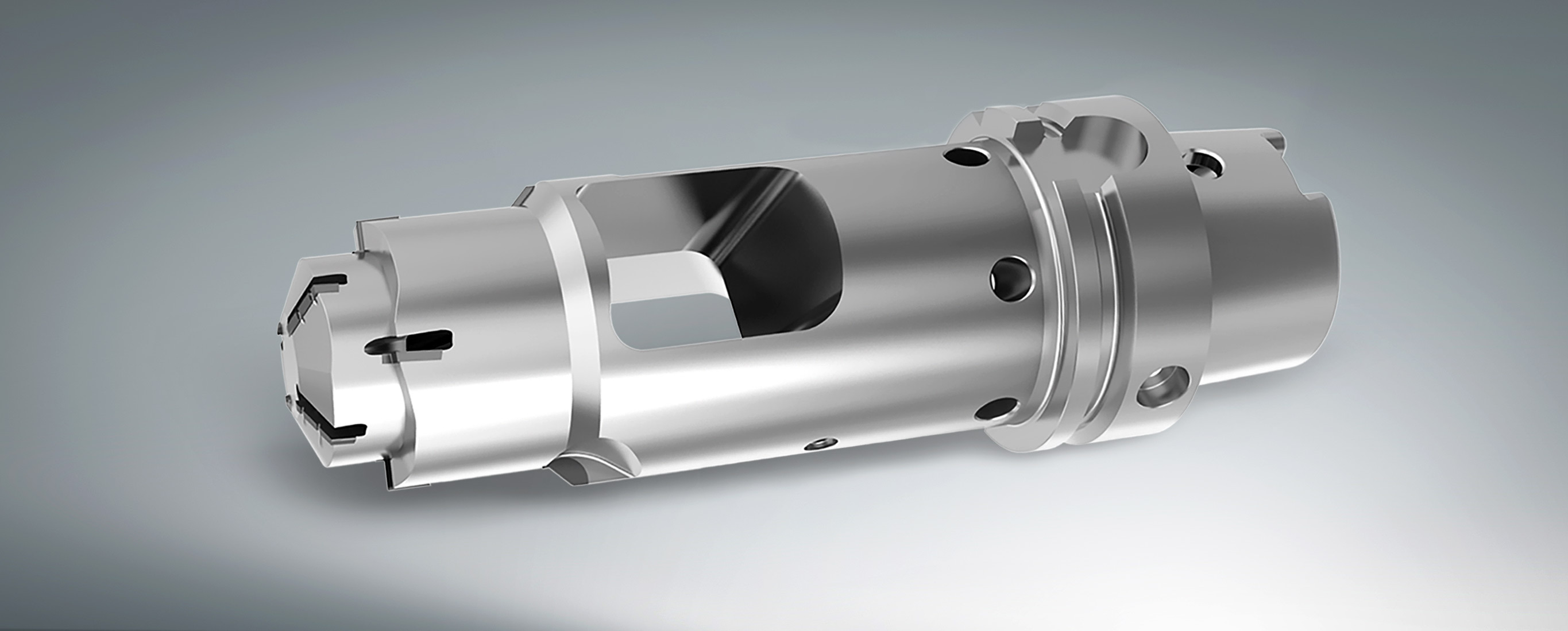
The complicated evacuation of chips from an aluminium component causes problems for the automotive supplier Handtmann. Gühring delivers a solution with a PCD drilling tool made in a 3D printer.
Chips are falling whenever drilling, turning and milling take place. Chips can be problematic! They can fall into openings where they are difficult to remove, stick to contact surfaces, leave marks on surfaces, clog up boreholes and can even lead to tool breakage.
Handtmann from Biberach was facing exactly these difficulties. A well-known vehicle manufacturer had requested a high output of several thousand components per week: Intake manifolds for combustion engines. The intake manifold is the piece that connects the engine block and the air filter. Fresh air from the air filter enters the combustion chamber via the intake valves. An exhaust gas recirculation valve controls how much exhaust gas is returned to the combustion process. This reduces the vehicle’s emissions.
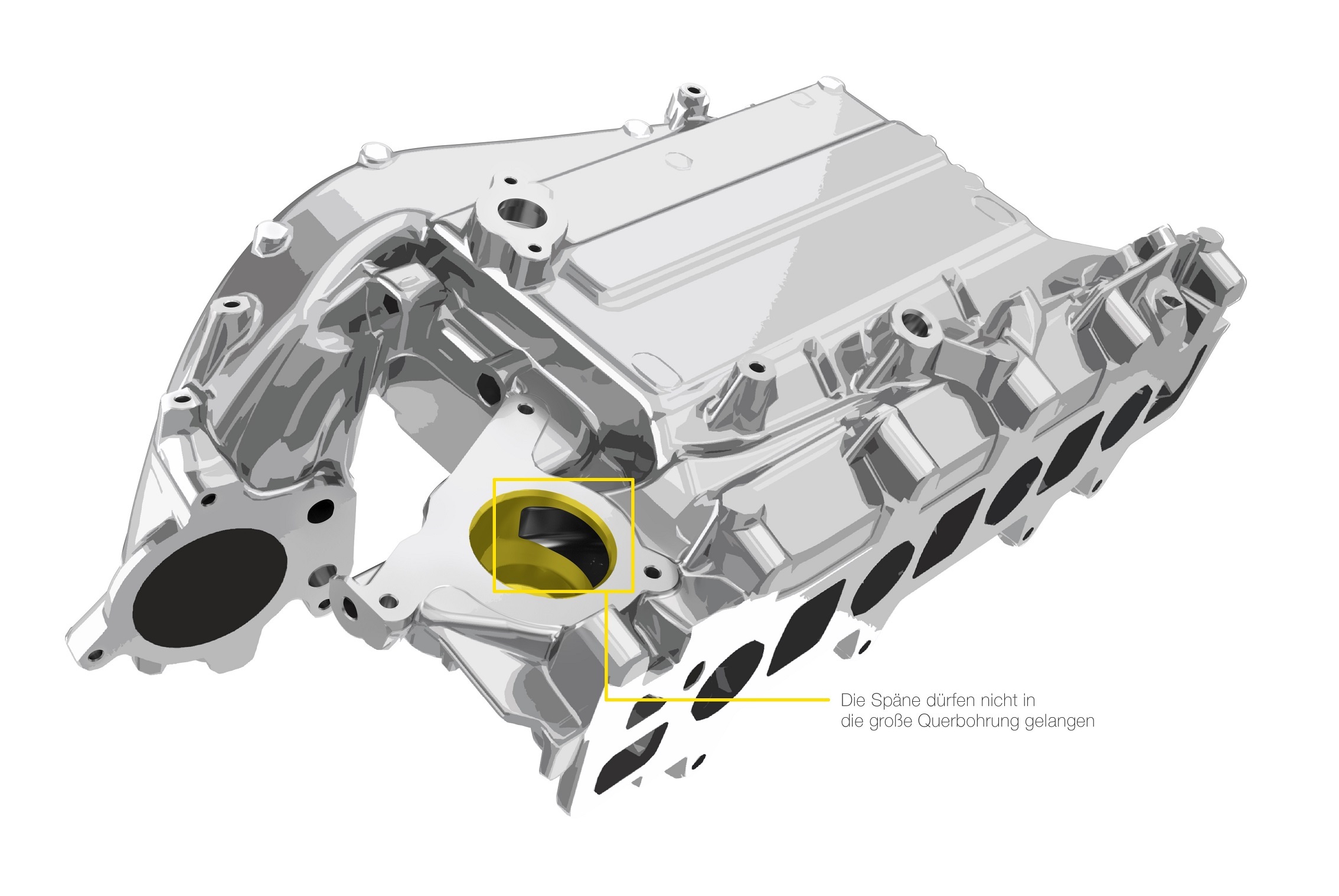
Complex workpieces like these are pure routine for the Handtmann Group, which specialises in drive and chassis components made from cast aluminium and magnesium. The only problem in the whole process was a single bore in the intake manifold which made machining almost impossible. The bore in question was a connection hole with a heavily interrupted cut. There was a risk that chips could enter the adjoining channels to the component from the side and front.
If the chips stayed in the component (even after rinsing), this would have fatal consequences: The chips could impede the combustion process or even cause mechanical damage. “When machining with conventionally open tools, a complicated and cost intensive cleaning was required,” recalls Robert Fiesel, Plant Manager at Handtmann. “After the chips were rinsed and blown out, each component had to be checked for chip residues.”
To prevent this, a drilling tool had to be used to remove chips from the component in a defined manner – Two tool manufacturers had already failed in this task after only achieving a distance of approx. 50mm.
“Tube design” for safe chip removal
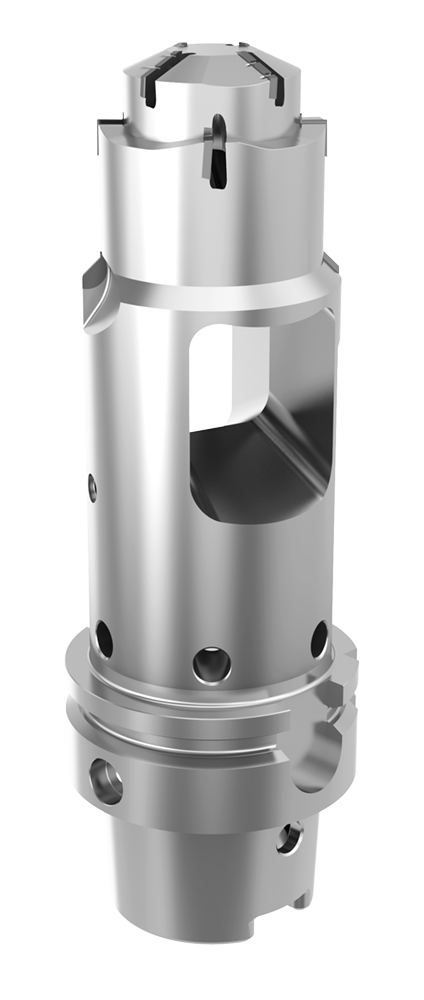
Tool manufacturer Gühring has a tool concept for exactly such applications: Machining of components with interrupted cutting where a large amount of chips is generated and have to be discharged in a controlled manner. In this so-called “tube design”, chip removal takes place inside the tool, which looks like a long
tube. A defined gap between the cutting edge and the tool body prevents the chip from escaping forwards or falling out of the side of the tool during removal from the cutting edge. The tube, in turn, ensures the removal of chips from inside the tool. The process reliability and the component quality are significantly increased with this tool geometry.
Tool bodies like this can only be manufactured in a conventional manner to a limited extent. That’s why Gühring relies on additive manufacturing using 3D printing for its tube design. “3D printing gives the designer significantly more freedom in the choice of geometry,” explains Michael Bopp, designer in development at Gühring. This makes it possible to produce a three-dimensional cooling duct guide as well as defined chip evacuation areas.
In addition, the material is only applied to the tool body where it is needed, higher strengths and rigidity are still achieved. The tube’s internal diameter can be maximised, especially with smaller diameters. The only disadvantage? These 3D-printed tools are expensive. This is why Gühring only uses additive manufacturing technology if it creates technical added value. Just like at Handtmann.
Perfect cooling thanks to the three-part system
Handtmann is a long-standing customer of Gühring and the two companies have already completed several large projects together. “We opted for a special tool from Gühring because the company already has experience with similar machining scenarios and the sales force was able to advise and support us on site,” explains Robert Fiesel.
Based on the component, it was clear that a reliable chip evacuation process would only be possible here with the “tube design”. Another requirement was to dispense with bolted chip guide elements and thus minimise „material build up“ and wear. “It quickly became clear to us that we would reach our limits with conventional methods,” recalls Michael Bopp. “That’s why we decided on a tool from the 3D printer.”
Gühring tested two prototypes of the core drill on the series production machine at Handtmann – both revealed potential for optimisation. The chips were not removed quickly enough, the internal chip chamber had clogged. Based on these tests, Gühring produced a third version. “We used our findings from the first two prototypes and ultimately came up with a really good tool,” reports Zarko Stevanovic, who was also involved in the development.
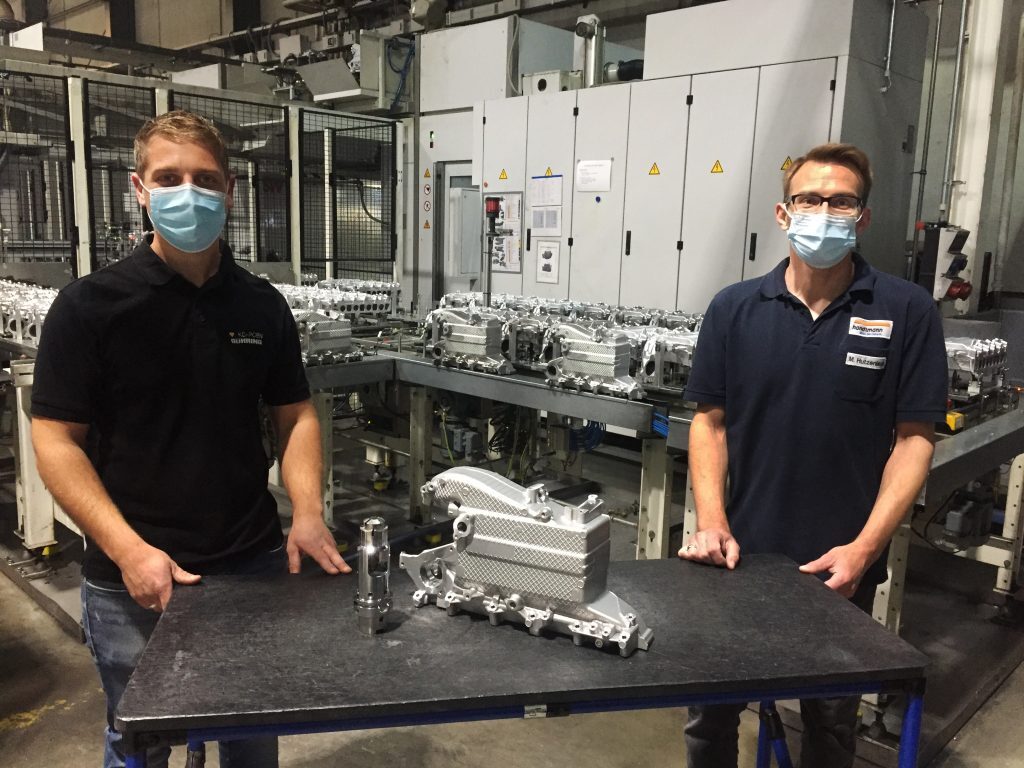
Christian Dreher, Application Engineer at Gühring (left) and Marco Hutzenlaub,
Tool Planner at Handtmann, are happy.
The tubular tool head made from steel is additively manufactured and connected to the base body. It has segment seats with PCD cutting edges. With a high output of 13,600 components per week, this cutting material achieves a long service life. In order to supply the individual cutting edges with coolant, the tool head has internal and three-dimensional coolant guides. In addition, three backward-facing cooling channels support chip removal. The chips emerge through two lateral openings at a sufficient distance from the component.
Robert Fiesel is happy: “The current version of the tool worked right away and has since solved the task as desired. No more chips get into the connection bores.” This means that Handtmann can dispense with meticulous chip control at the end of the process
Technical advice and support are also available quickly and directly via our service hotline 00800 2607 2607.
We can also be reached on WhatsApp: +49 172 658 53 53. Save the number!
You might also be interested in:
Modular drills: Their advantages and how you can benefit from them
Modular drilling systems such as the BT 800 from Gühring offer full performance at lower costs. Thanks to interchangeable drill heads, you save time, storage space and money – ideal for flexible applications with the highest demands on cost-effectiveness.
Threads for giants: Crane manufacturer relies on modular fluteless tap for blind holes
An innovation – the new modular fluteless tap from Gühring – has made it possible to solve deep-seated challenges in the production of blind hole threads at Karl Georg and to raise process reliability to a new level.
30% more tool life: With this parting off plate you achieve maximum performance in high-grade steel
30% more tool life when parting off: The new 2 mm parting off plate from Gühring’s System 222 impresses with excellent chip control, high process reliability and a perfect surface finish on ISO-M materials such as high-grade steel.