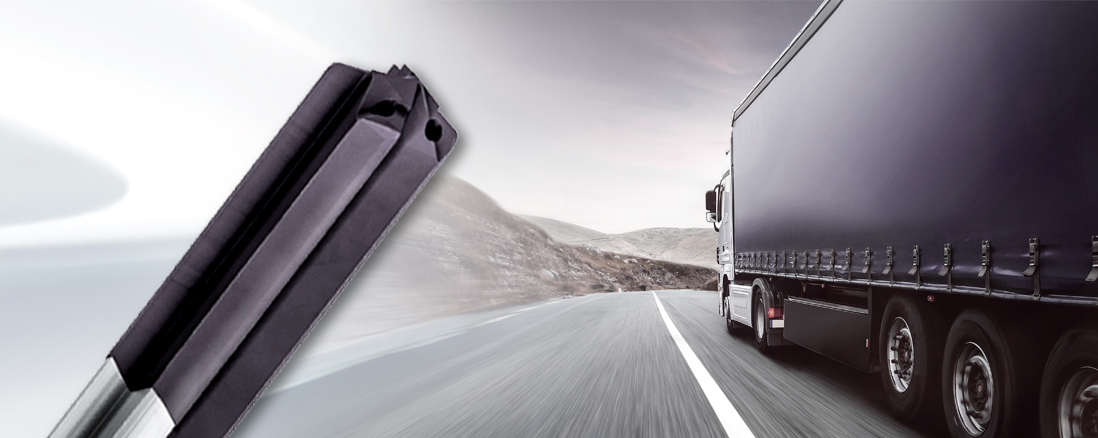
Gühring has developed a new tool technology that can produce drilling depths of up to 40xD. This technology can work up to twice as fast compared with conventional methods – even when drilling deep holes, reducing the cycle time considerably, sometimes by several minutes, significantly increases capacity.
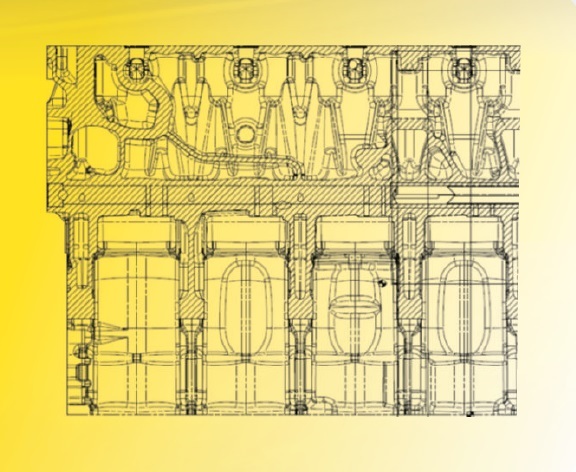
The giants of the vehicle sector: Ships, trucks, buses, construction and agricultural machinery. Moving masses on this scale requires immense power under the bonnet – which can only be provided by large engines.
But manufacturing them poses challenges for companies, as deep holes have to be drilled into the drive components made of different types of cast iron. Creating these holes in the conventional way is time consuming and expensive.
A new tool solution is required, with an adapted geometry and inherent stability that absorbs the forces during machining and keeps them as low as possible.
The crux of the matter: The machine related limits of axial force and torque are limited on many machines. The drilling quality and tool life must also remain the same as with conventional methods. Working in partnership with a customer, Gühring developed a new power technology: The four-fluted deep hole drill VB 80 and the four-fluted drill VB 100 are used to drill holes, pilot holes and stepped holes.
2+4 cutting edges for process reliability
These tools are specially designed for castings. Their performance is based on the carbide made by Gühring from ultra-fine grains and the proven Signum coating. “This has proven to be the strongest layer for castings,” explains Philipp Kunze, developer in the field of deep hole drilling at Gühring. To cope with the high chip volume, Gühring uses its patented 2+4 cutting edge division. The main load of the massively increased feed per revolution is initially absorbed by the two inner cutting edges. These are supported by a thick core and a specially defined cutting wedge static. The special grinding for producing the transverse cutting edge ensures low forces. The four “peripheral cutting edges” are then used to absorb the high torque. Typical casting wear is divided over four instead of two cutting edges. The corner radii complete the system by creating the finest surface finishes. The result: shorter chips, higher cutting parameters and a significant increase in process reliability.
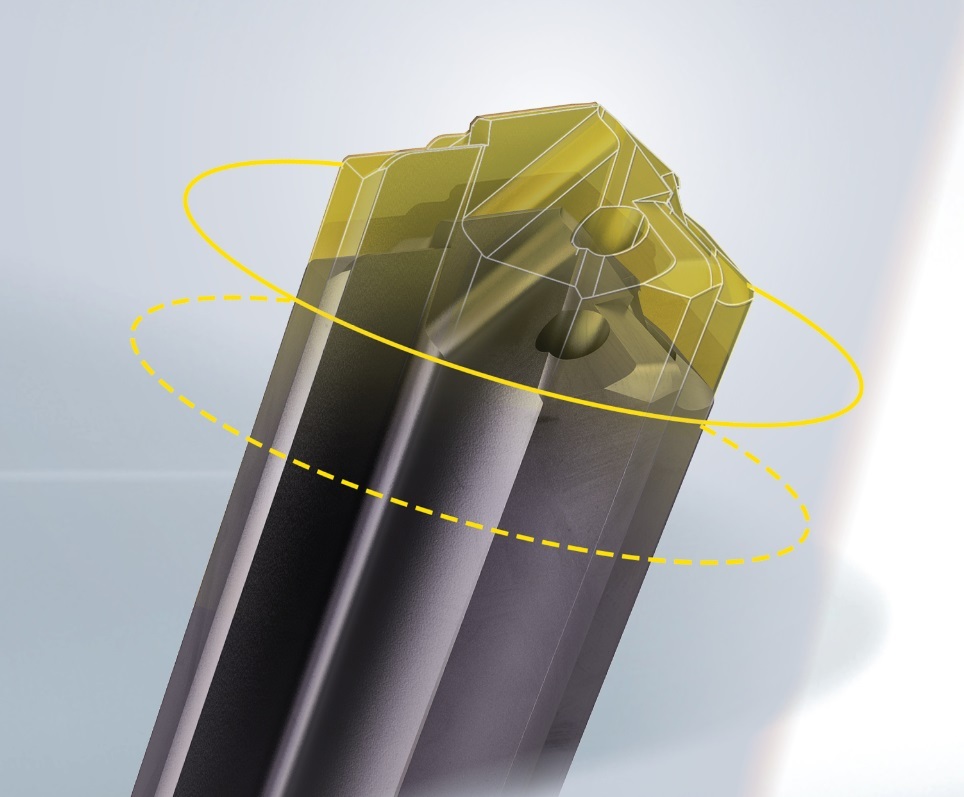
The four cutting edge corners of the four-fluted cutter reduce the abrasive wear.
The VB 80 deep hole drill has a solid base body made of solid material with straight flutes onto which a solid carbide head is brazed in a form-fitting way. Despite the faster processing, the tool life remains the same or can even be significantly improved.
For example, in the material GG25, both types of drill can achieve tool life of up to 250 m under optimum conditions. Once the tools have reached tool life, they can be reground 5 to 10 times due to low wear.
With regard to possible roundness, values of less than 10 μm have already been achieved with the four-flute drills. With diameter tolerances zones of up to IT7, the tool also outperforms established quality values, and surface values in the roughness class N8, sometimes even N7, can be achieved in different cast types.
Thanks to the optimised cutting edge formation and the inherent stability of the drills, very low runouts are generated. In combination with a VB 100 as a pilot drill, the VB 80 deep hole drill achieves comparable or even better results in terms of the runouts despite the high feed rates compared to established processes.
Safe cooling and flexible voltage
As with any high-performance drilling tool, the coolant supply is crucial for functional and process reliability. With the four-flute drills, the coolant or minimum quantity lubrication is transported via a central channel and a Y-distribution integrated into the solid carbide.
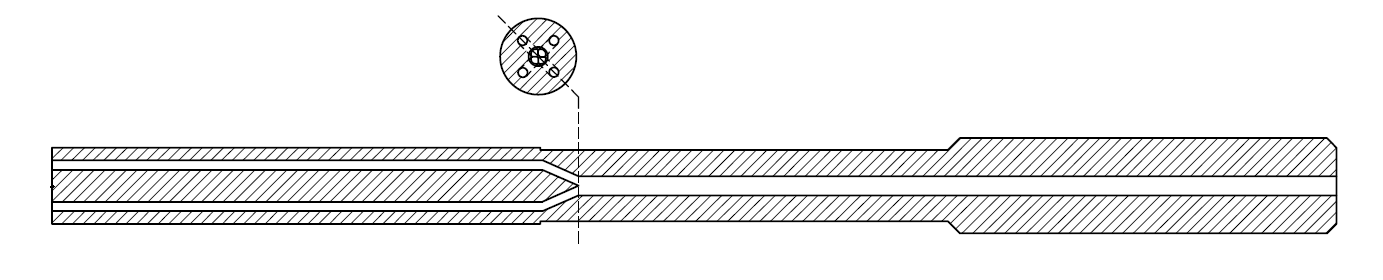
From there, it is distributed highly efficiently to the front four channels and the cutting edges. This is necessary to flush the coolant chips produced during drilling out of the hole with maximum flow rates. The result: The tool geometry is also protected during high performance.
The already tested diameter range for the VB 100 to 5xD drill is between 8.0 and 40 mm. With the VB 80 deep hole drill, diameters of 8 to 30 mm and tool lengths of up to 1000 mm can currently be produced.
Have we piqued your interest?
Then arrange your personal consultation appointment now:
Technical advice and support are also available quickly and directly via our service hotline 00800 2607 2607
We can also be reached on WhatsApp: +49 172 658 53 53. Save the number!
You might also be interested in:
Modular drills: Their advantages and how you can benefit from them
Modular drilling systems such as the BT 800 from Gühring offer full performance at lower costs. Thanks to interchangeable drill heads, you save time, storage space and money – ideal for flexible applications with the highest demands on cost-effectiveness.
Threads for giants: Crane manufacturer relies on modular fluteless tap for blind holes
An innovation – the new modular fluteless tap from Gühring – has made it possible to solve deep-seated challenges in the production of blind hole threads at Karl Georg and to raise process reliability to a new level.
30% more tool life: With this parting off plate you achieve maximum performance in high-grade steel
30% more tool life when parting off: The new 2 mm parting off plate from Gühring’s System 222 impresses with excellent chip control, high process reliability and a perfect surface finish on ISO-M materials such as high-grade steel.