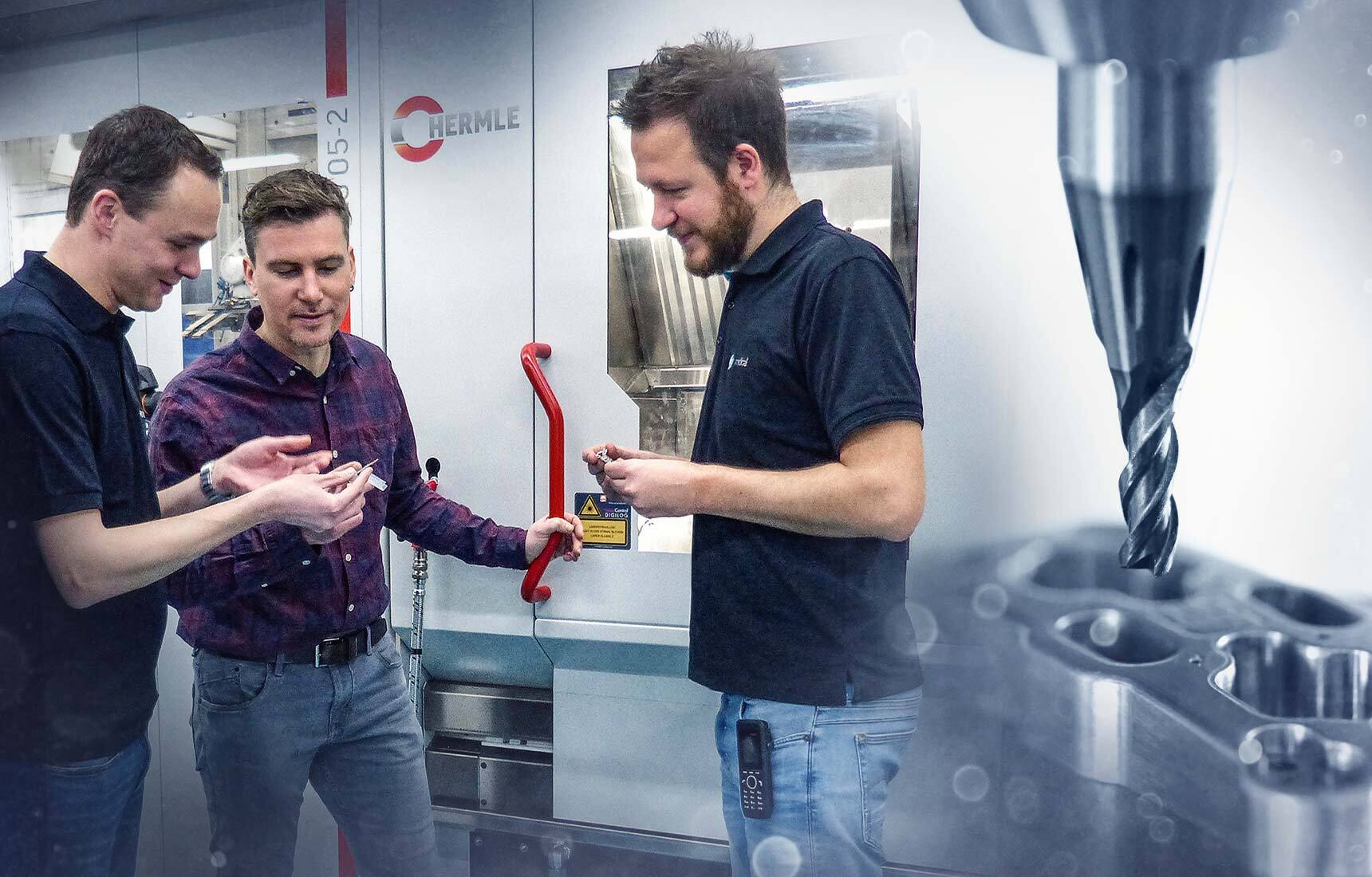
Gühring-Produktmanager Christian Sieker (links) präsentiert Florian Lukats (Mitte) und Mike Stutenz von hg Medical den RF 100 Mikrodiver.
Expertise and flexibility – both are essential when there are problems to solve. And both are characteristics that make Gühring a strong partner for the medical technology sector. And this was also clear in the case of hg medical: Where conventional tools quickly reach their limits when it comes to wear, a Gühring micro-precision milling cutter with adapted carbide roughs and slots for 1100 minutes in titanium.
In the medical technology sector, it is considered the “super material”: grade 5 titanium (Ti6Al4V). Implants made from this material are extremely resistant without feeling heavy inside the body. The material is biocompatible, does not cause reactions or allergies, does not corrode and is not magnetic. For all these reasons, hg medical also relies on grade 5 titanium. The medical technology manufacturer from Raisting (in Upper Bavaria, Germany) manufactures 95 percent of its components from the super material, including various bone plates, bone screws and implants for orthopaedic and general surgery.
And yet, however practical grade 5 titanium is in practice, it is also extremely challenging to machine. Due to the high toughness of the material, chips do not break, but instead tend to stick to the tool. In addition, titanium has extremely poor thermal conductivity: The temperatures up to 1200°C that occur within the cutting zone are also conducive to tool wear.
Expertise within the medical sector
These were the problems facing hg medical in the manufacturing a grade 5 titanium bone plate: Chippings began appearing on the cutting edges of the milling cutters after just a short amount of time. So, head of the milling workshop Florian Lukats contacted his tool supplier, who has been advising hg medical on machining problems for 20 years: “Gühring is a good business partner and has a broad portfolio of products in the tooling sector,” Lukats confirms. “Even when we need solutions quickly, we can always rely on Gühring to deliver.”
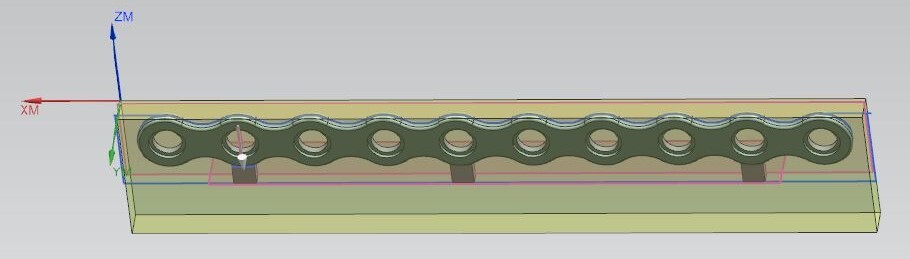
Die Gühring-Experten fertigten das Modell einer Knochenplatte an, um die Werkzeuge daran zu testen.
Gühring has greatly expanded its expertise in the field of medical technology in recent years, especially with regard to the design of tools and processes for specific components. In test centres, tools are individually tailored to the customer and tested on in-house machines. “This allows us to prepare the process to achieve the best results for the customer and provide them with both tools and a finished machine program so that they can get started right away,” explains Daniel Laqua. As a Gühring application technician, he is in charge of designing products in the micro-precision tools group – including for hg medical. When he heard which material needed to be processed in this case, a specific Gühring tool immediately came to mind: “The RF 100 Micro Diver is our top tool for special alloys in the micro range,” says Laqua. “Grade 5 titanium is a challenge, but the Micro Diver has the right geometry and high hardness when it comes to substrate and coating.” He had already achieved very good results with the micro high-performance milling cutter, especially in the field of medical technology.
Longer tool lives thanks to effective cooling
With the RF 100 Micro Diver, Gühring offers a high-performance tool for machining challenging materials in the micro range. One of the most impressive features of the micro-precision milling cutter is its innovative internal cooling: The shank contains IC channels arranged in a pitch circle around the cutting wedge. During milling, they supply the flow of coolant into the cutting zone. Cooling as effective as this is indispensable, especially for grade 5 titanium, as it is needed to reduce the high temperatures during milling and thus extend the tool life.
Another key criterion for tools used to machine titanium is reliable chip removal. As Christian Sieker, Gühring product manager for micro tools, points out, the RF 100 Micro Diver also scores points here: “The optimised tool surfaces ensure that chips do not stick in the flute, but are removed safely.” To achieve this, the tools are also provided with an extra-smooth layer. “In addition to protecting against abrasive wear, this also has the advantage that the friction between the chips and the tool is significantly lower, which also reduces the thermal load on the cutting edges,” says Sieker.
Gühring optimises carbide on a bespoke basis
Although the RF 100 Micro Diver performed significantly better than tools used in the past, it was unable to fully demonstrate its strengths at hg medical at first. The reason? The component in question is a small, very thin plate that cannot be optimally clamped. As the milling cutter travels along it, the plate begins to vibrate, causing small impacts that the very hard carbide cannot absorb. The milling cutter breaks.
But in this case, Gühring has a clear advantage over many other tool manufacturers, as Laqua explains: “We produce the carbide for our tools ourselves and can therefore adapt the individual components perfectly to suit the customer’s requirements.” As such, the experts at Gühring designed a carbide substrate that gives the tool a high level of toughness and heat resistance even when exposed to high dynamic cutting forces. A Gühring coating tailored perfectly to these circumstances ensures good sliding properties and additional wear protection.
Hardly any wear after double the tool life
A Micro Diver was tested in-house for approximately 1100 minutes until it showed initial signs of wear on the cutting edges and had to be replaced. The feed rate was also more than twice as high with the new tool, which has a significant impact on the product runtime. For hg medical, this means lower set-up costs with consistent quality and, as a result, considerable cost savings. At the same time, the surface quality was maintained and even improved in some areas.
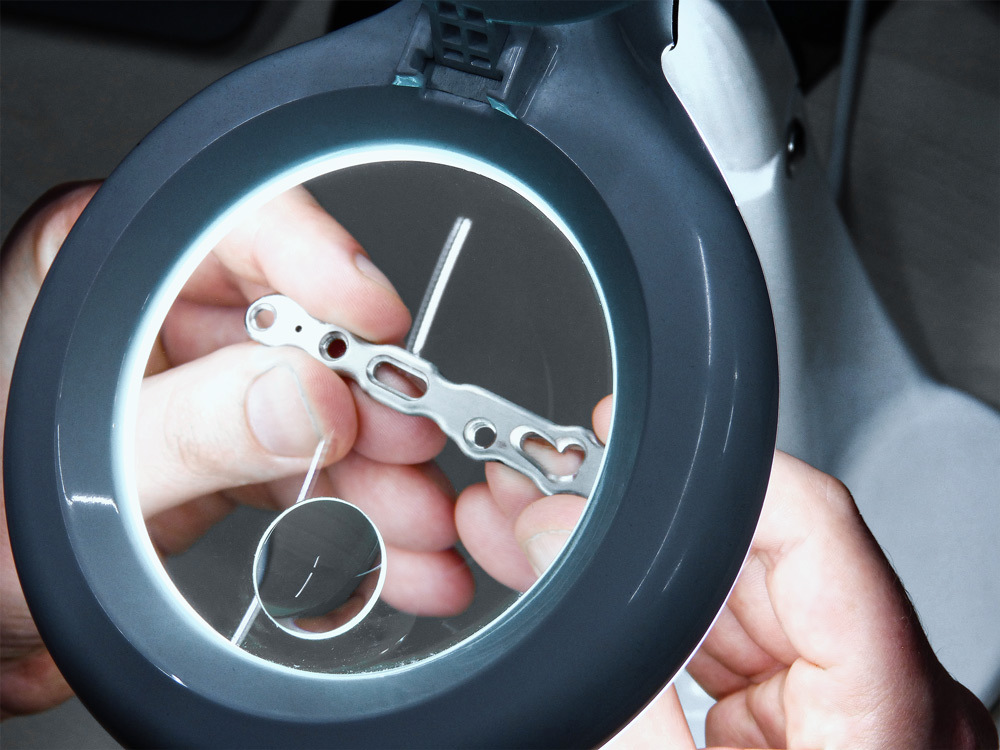
Florian Lukats from hg medical is impressed: “Titanium is known to be a material that is hard to machine, but thanks to the excellent cooperation with Gühring, we were able to stabilise the milling process.” For him, this is further proof of the good working relationship with Gühring: “As our tool supplier, Gühring has been involved in the growth of hg medical from the outset, as we have an advantage over competitors thanks to such stable milling processes.”
Have we piqued your interest?
Then arrange your personal consultation appointment now:
Technical advice and support are also available quickly and directly via our service hotline 00800 2607 2607
We can also be reached on WhatsApp: +49 172 658 53 53. Save the number!
You might also be interested in:
Maximum economic efficiency: Modular drill reduces set-up times and scrap for the customer
Tool life up, machining times down: With the BT 800 interchangeable head drilling system, the company Kurt Metallverarbeitung has found a modular solution that not only impresses with simpler handling, but also with outstanding performance.
Modular drills: Their advantages and how you can benefit from them
Modular drilling systems such as the BT 800 from Gühring offer full performance at lower costs. Thanks to interchangeable drill heads, you save time, storage space and money – ideal for flexible applications with the highest demands on cost-effectiveness.
Threads for giants: Crane manufacturer relies on modular fluteless tap for blind holes
An innovation – the new modular fluteless tap from Gühring – has made it possible to solve deep-seated challenges in the production of blind hole threads at Karl Georg and to raise process reliability to a new level.