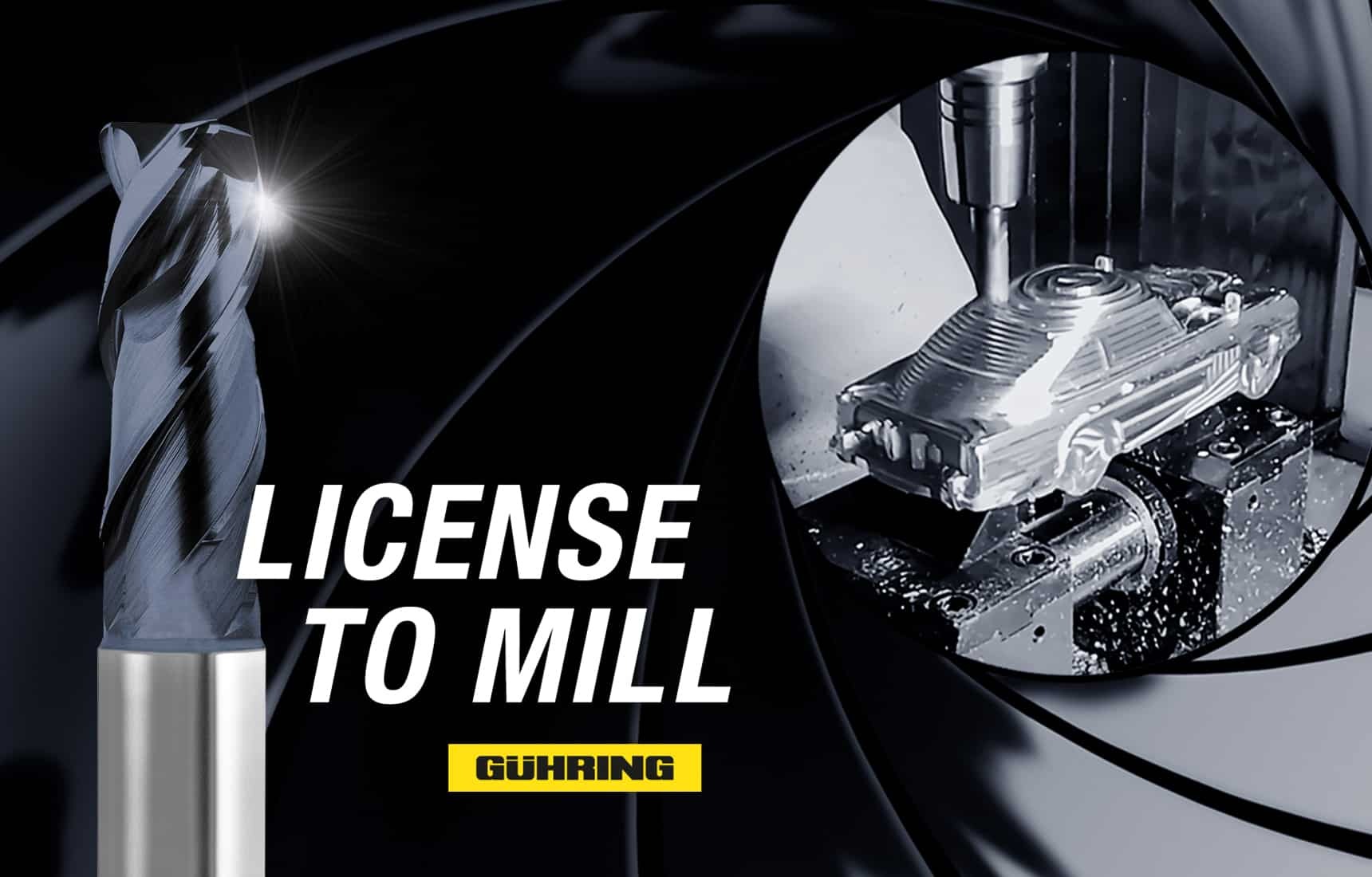
When you bring together the three best products, you get the perfect process. Gühring and Blaser have combined a high-quality MQL oil with a solid carbide corner radii milling cutter for aluminium machining and an MQL tool holder. The result showcases the advantages that collaborative engineering can yield.
Perhaps the most legendary car in the world: the Aston Martin Silver Birch DB5. In 1964, Sean Connery raced away from his enemies in the silver sports car in “Goldfinger”. Pierce Brosnan and Daniel Craig were also seen behind the wheel of the racer during five other spectacular film appearances. But it is not just its elegant curves that make the Bond car an icon, but also the special gadgets that Quartermaster Q builds in for 007: Buttons for nails, smoke and machine guns in the centre console, an ejector seat, tyre shredder and pile driving device. The value of the original car, which has since disappeared and hasn’t been seen for 25 years, is now estimated at 25 million US dollars.
The company Blaser is also a very big fan of the Aston Martin DB5. This gave rise to the idea of reproducing the iconic sports car in detail – in paperweight size and made of solid aluminium. Based in Rüegsau (Switzerland), the company benefits from its expertise as a global technical leader in the field of cooling lubricants: Blaser has been producing lubricant solutions with measurable added value that are kind to people and the environment since 1936. With a wide range of cooling lubricants, Blaser helps its customers to fully exploit the potential of their machines and tools. And this was the case with the Aston Martin, too, because perfect cooling would be the only way to produce surfaces that matched the mirror-like polish of the original.
However, this also called for tools that safely conveyed this high-quality coolant to the cutting edge through internal coolant ducts. So, Blaser turned to Gühring, with whom the company has a long-standing, close working relationship. Previous projects had already shown that: “The coolant ducts in our tools have the perfect cross-sections to allow the oil to be transported well,” says Michael Gnatkowski, Sales Manager for the Automotive Sector at Gühring.
Gühring specialist for aluminium: The RF 100 A
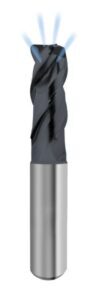
So, it didn’t take long to find the perfect tool for manufacturing the Aston Martin: The solid carbide corner radii milling cutter RF 100 A (item no.: 6982 16,020) with axial and radial internal cooling from Gühring’s specialist range for aluminium machining. Its internal coolant ducts and coolant exits ensure a precise supply of lubricant to the cutting edge.
A particularly important factor for the machining of the Aston Martin: The nanopolished cutting edges of the RF 100 A enable low-vibration milling thanks to their micro support chamfers, thereby creating the ideal surfaces. This combination of polished cutting surfaces, a carbo-coating and targeted MQL internal cooling is the ideal prerequisite for machining even sticky aluminium alloys.
MQL cooling: economical and sustainable
In order to get the perfect performance from this tool, the experts at Blaser defined the ideal interaction between air pressure and oil quantity for the cooling lubricant. This mix is transported through the tool’s IC channels directly to the cutting edge and workpiece surface, where machining takes place. Only as much oil as necessary is used here. This is where the benefits of MQL technology come to the fore: The application is very clean and cleaning is kept to a minimum. By saving oil, disposal processes are also eliminated, which makes sense in terms of sustainability.
In MQL technology in particular, tool holders also play a decisive role as an interface between tool and machine. So, for the Aston Martin, Blaser used an MQL clamping chuck for single-channel systems from Gühring’s GM 300 range.
The best products combined
The successes achieved with the Aston Martin on a small scale reveal Gühring’s vision: The tool supplier wants to offer its customers everything for an ideal process, especially in project-related equipment: cutting tools, but also tool holders and cooling lubricants. Michael Gnatkowski firmly believes that: “If we bring the perfect products together – a reliable tool with a high-quality cutting oil – then we can optimise processes.”
Aleksej Wahnsiedler, Head of Industrial Partnerships at Blaser, also sees the project as proof of the perfect symbiosis of tool and cooling lubricant: “We are combining the advantages of both systems, thereby enabling us to generate a much bigger benefit.” This advantage is reflected particularly in better surfaces and longer tool lives. In this technological incentive, Wahnsiedler sees the common ground between the two companies: “That together we generate the added value that the customer is looking for.”
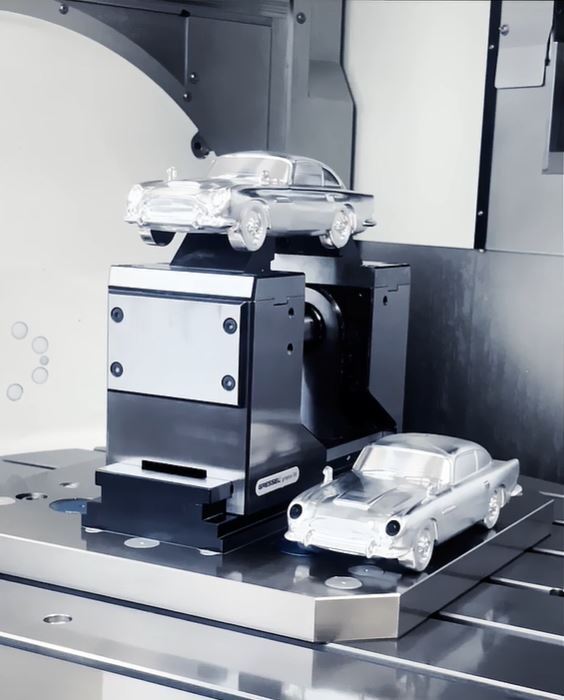
Have we piqued your interest?
Then arrange your personal consultation appointment now:
Technical advice and support are also available quickly and directly via our service hotline 00800 2607 2607
We can also be reached on WhatsApp: +49 172 658 53 53. Save the number!
You might also be interested in:
Maximum economic efficiency: Modular drill reduces set-up times and scrap for the customer
Tool life up, machining times down: With the BT 800 interchangeable head drilling system, the company Kurt Metallverarbeitung has found a modular solution that not only impresses with simpler handling, but also with outstanding performance.
Modular drills: Their advantages and how you can benefit from them
Modular drilling systems such as the BT 800 from Gühring offer full performance at lower costs. Thanks to interchangeable drill heads, you save time, storage space and money – ideal for flexible applications with the highest demands on cost-effectiveness.
Threads for giants: Crane manufacturer relies on modular fluteless tap for blind holes
An innovation – the new modular fluteless tap from Gühring – has made it possible to solve deep-seated challenges in the production of blind hole threads at Karl Georg and to raise process reliability to a new level.