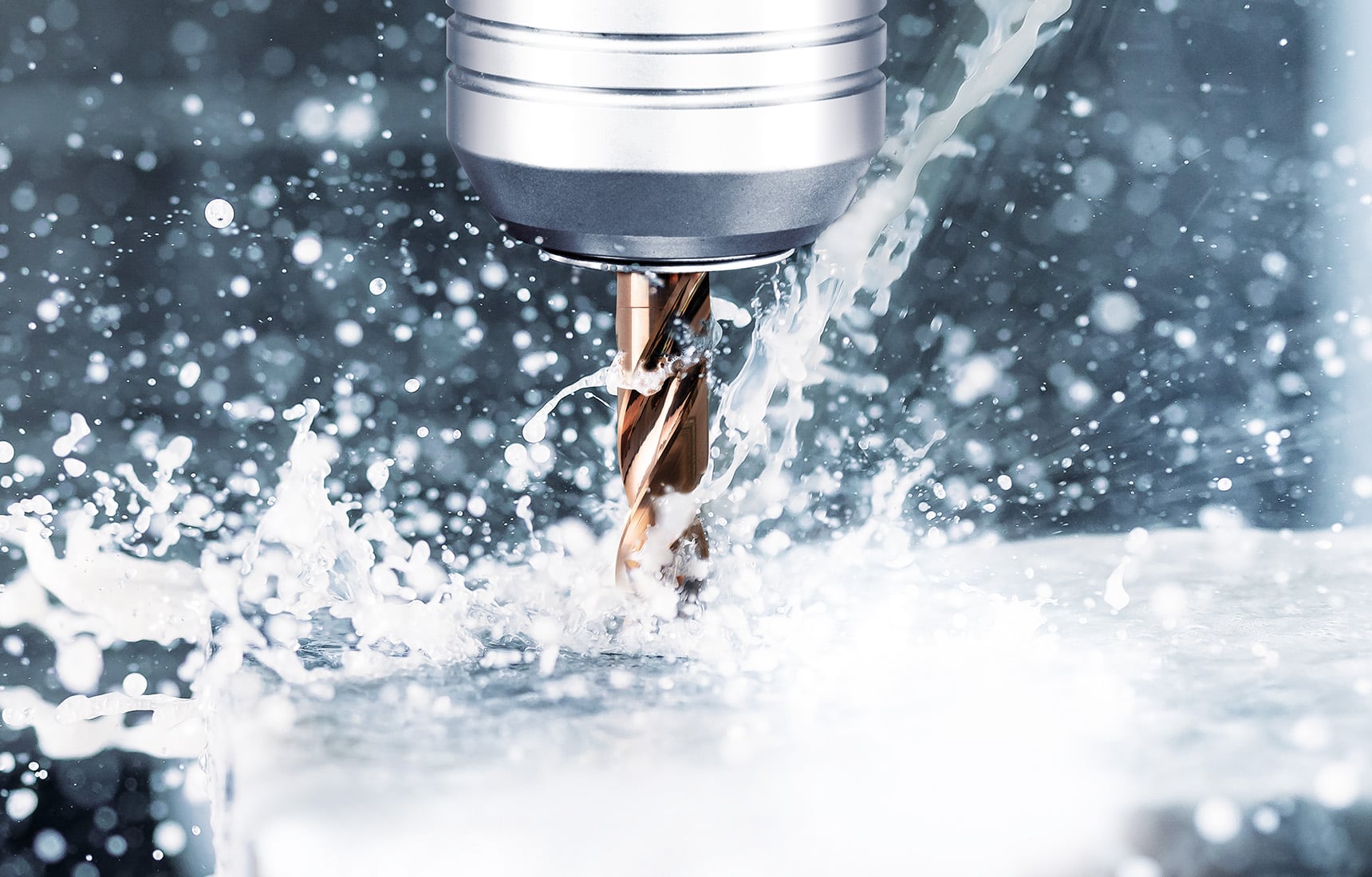
With the new high-performance tools for stainless steel machining, Gühring offers the optimal solution. Special coatings and adapted geometries guarantee the highest cutting values and extended service life. This means that the most demanding machining tasks can be mastered in a wide range of industries.
If you need to ensure corrosion- and acid resistance, then the answer is always stainless steel. Regardless of whether you’re in the food, automotive, medical or energy technology sector – every industry relies on the high durability of the ISO M material group. However, their toughness and low thermal conductivity make them tricky materials to machine.
This is where you need specialists who have been precisely developed for machining stainless steels: Our new high-performance tools for stainless steel machining. Thanks to their special coatings, the tools can withstand high thermal loads for significantly longer, while their carbide substrate offers the perfect ratio of hardness-to-toughness. At the same time, the adapted geometry is able to deliver the highest cutting values, which ensure maximum economic efficiency, especially in medium and large-scale batch production.
3 High-performance tools for economical machining of stainless steel
Top-Performance Micro-Precision Drill: RT 100 InoxPro Micro
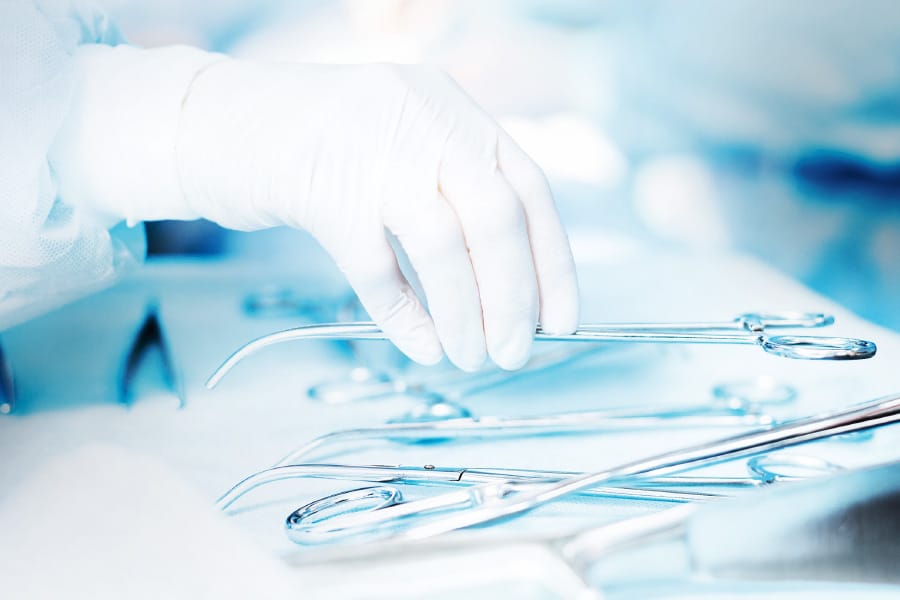
Holes in the handle of a medical instrument
Industry: Medical technology
Material: 1.4021 / X20Cr13
Target: To reduce the machining time with absolute process reliability
Polished surfaces are a must-have for all medical devices. This is the only way to prevent bacteria and viruses from settling on the surface. So, this instrument for minimally invasive surgery is also made of martensitic, stainless chrome steel. The material is not only very easy to polish, but also resistant to chemicals and acids.
However, one problem is that high temperatures develop at the tool’s cutting edge when drilling into this material, which can promote abrasive wear. This is particularly problematic in fully automated production, where high process reliability and therefore consistently high tool lives are required.
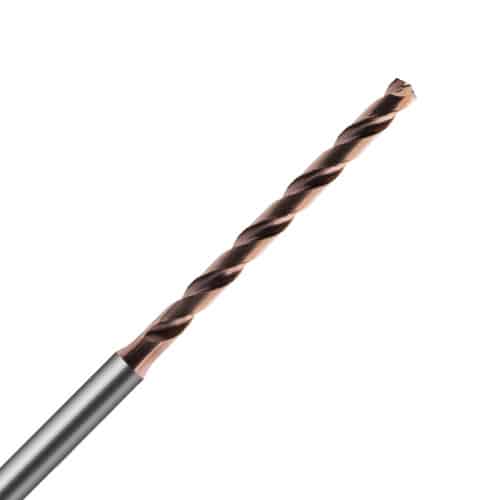
The RT 100 InoxPro Micro is our high-end micro drill for machining stainless steels, special alloys and titanium. The optimised geometry with a concave main cutting edge helps to deliver an aggressive cutting behaviour. In this way, the micro-precision drill produces short chips even in long-chipping materials, making it easier for the chips to be removed. At the same time, the Perrox coating protects the tool from abrasive alloy components and prevents built-up edges. As a result, the micro drill achieves the highest feed rates with very long and reliable tool lives.
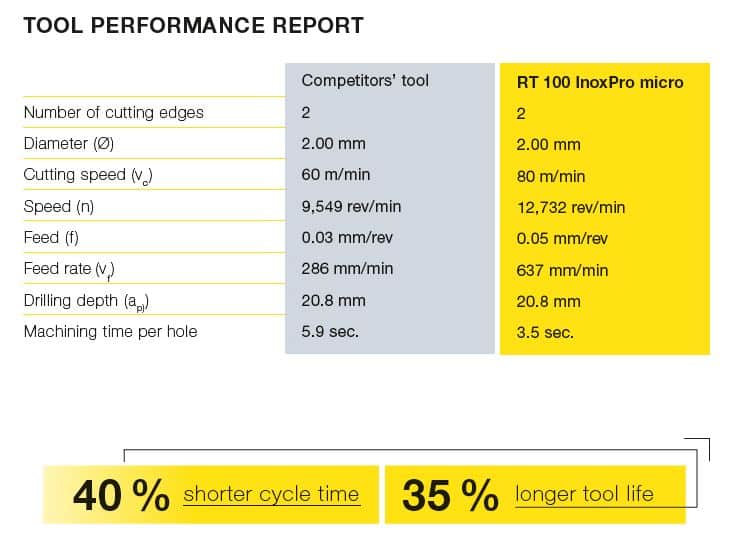
Maximal produktivity with our drilling specialist: Solid carbide drill InoxPro
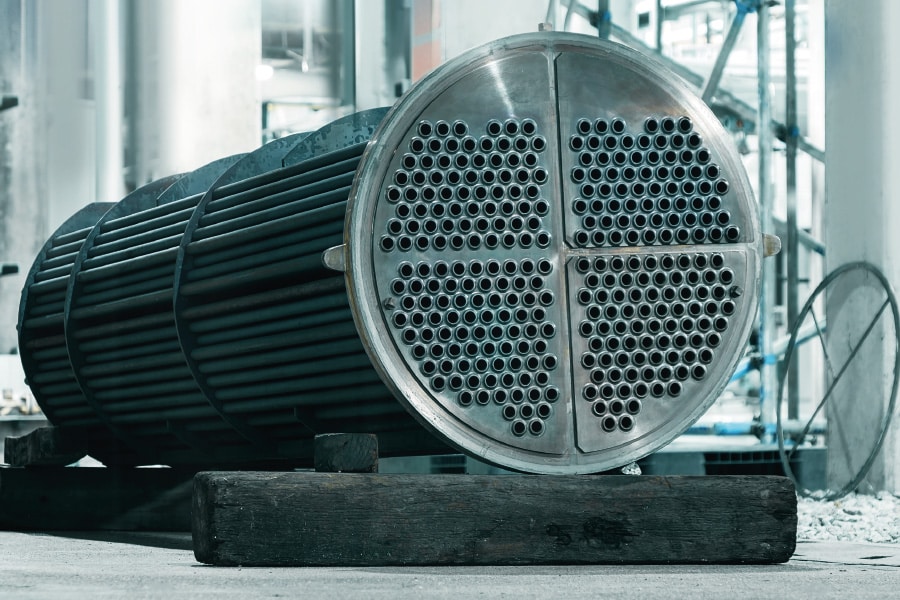
Holes in a perforated plate for a heat exchanger
Industry: Power generation
Material: SA 240 316L
Target: Reduction of cycle time but with a constant tool life
In various energy technology systems, heat exchangers transport the heating medium through the pipes, which are consolidated by a perforated plate. Given these circumstances, this component has to be corrosion-resistant and able to withstand temperatures up to 550 °C as well as low temperatures – criteria that are all by met by stainless steel.
But when it comes to machining, the material is challenging: When drilling, huge amounts of heat are generated, affecting the tool. In addition, long chips form in the tough material and wrap around the drill. If they stick to the tool’s cutting edges, this can result in cutting edge chipping or even tool breakage.
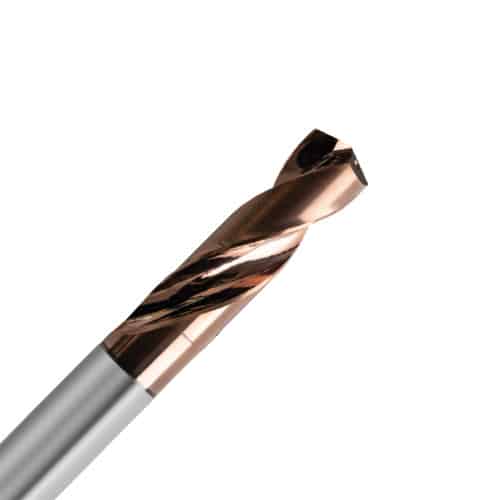
Our solid carbide drilling specialist, the RT 100 InoxPro, solves the problem of machining in stainless steel: The new drill geometry with an optimised sickle-shaped cutting edge and the increased taper of the tool minimise the tendency towards jamming in stainless steel and ensure optimum chip control. As well as the polished flutes, Gühring’s own HiPIMS Perrox coating offers very high wear protection. An adapted carbide substrate also ensures that the blade does not break, even under high loads. The result: Maximum process reliability – even with large diameters and deep holes up to 7xD.
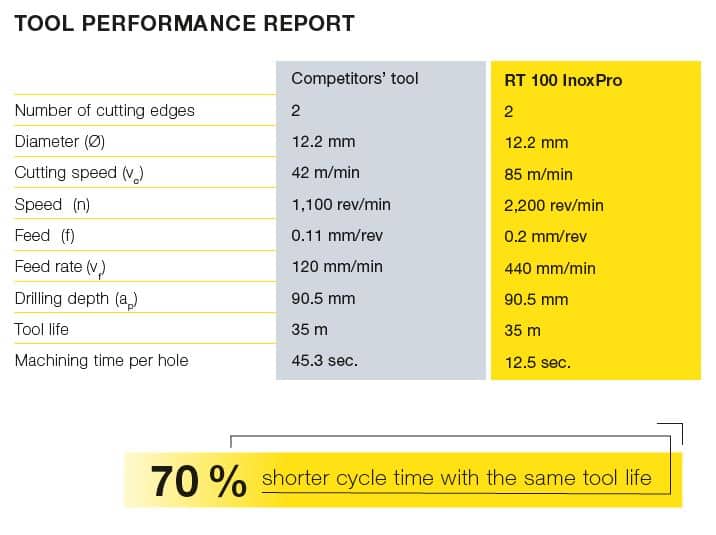
High performance for your threads: Tap Pionex
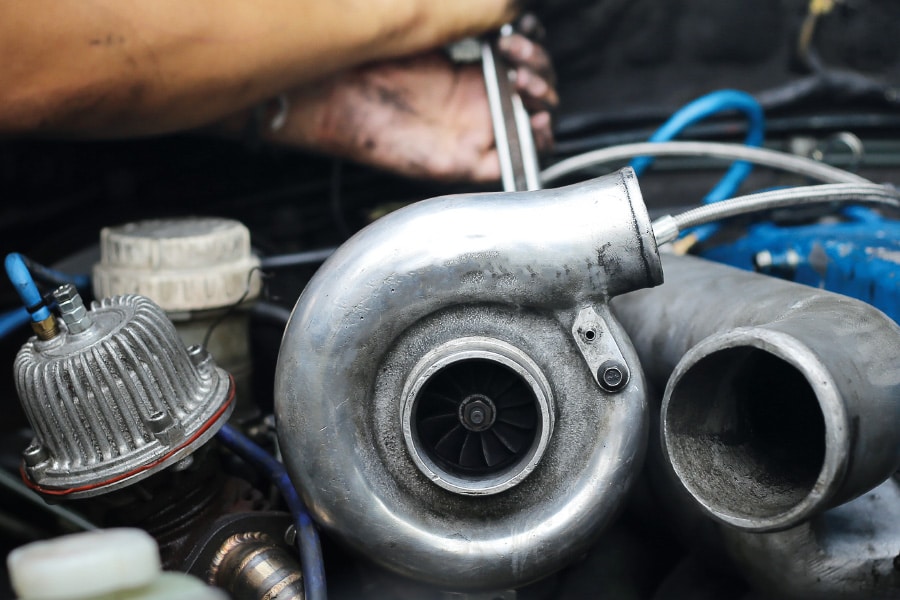
Through-thread in the housing for a turbocharger
Industry: Automotive industry
Material: 1.4826 / X15CrNiSi20-12
Target: Reduce tool costs through longer tool lives
An important component in a turbocharger, this housing is responsible for transporting hot exhaust gases. High-temperature components like this are often made from this special stainless steel, which is resistant to temperatures up to 1000°C and offers extra tensile strength. However, during machining, the material tends to form hard carbides on tool surfaces. Especially on the tap’s cutting edges, these lead to increased wear and micro-chipping, which negatively affects the cutting performance and tool life.
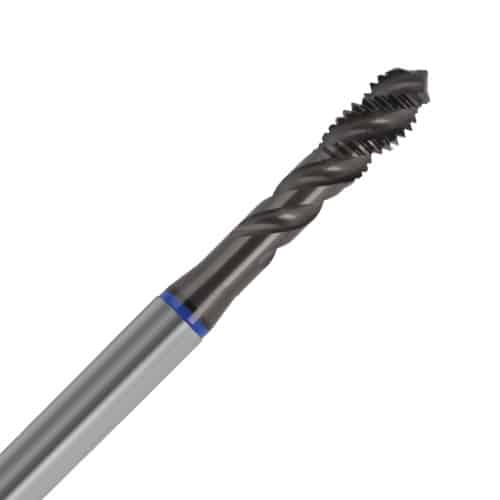
The Pionex is our high-performance tap for blind hole machining in stainless steels. The tool is characterised by an increased helical pitch and its optimised flute geometry. Both ensure better chip removal and increase the tool life. At the same time, an advanced TiAIN coating system reduces friction during thread tapping. In addition to stainless steels, Pionex is also ideal for use in stainless steels as well as low and high alloy steels.
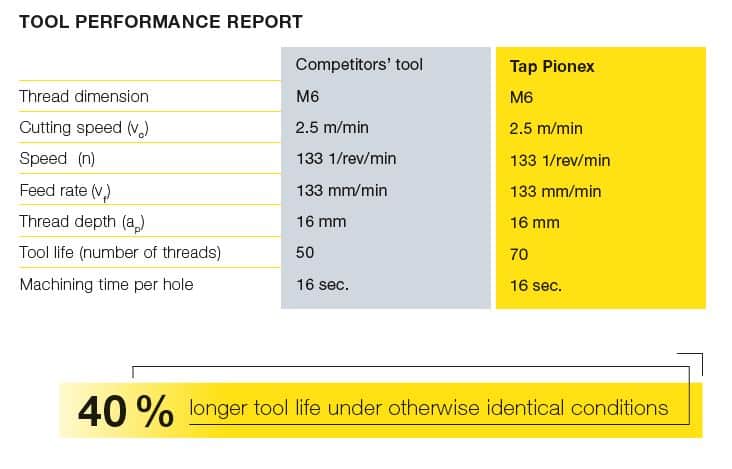
Perfect dimensional accuracy: Fluteless tap InoxPro
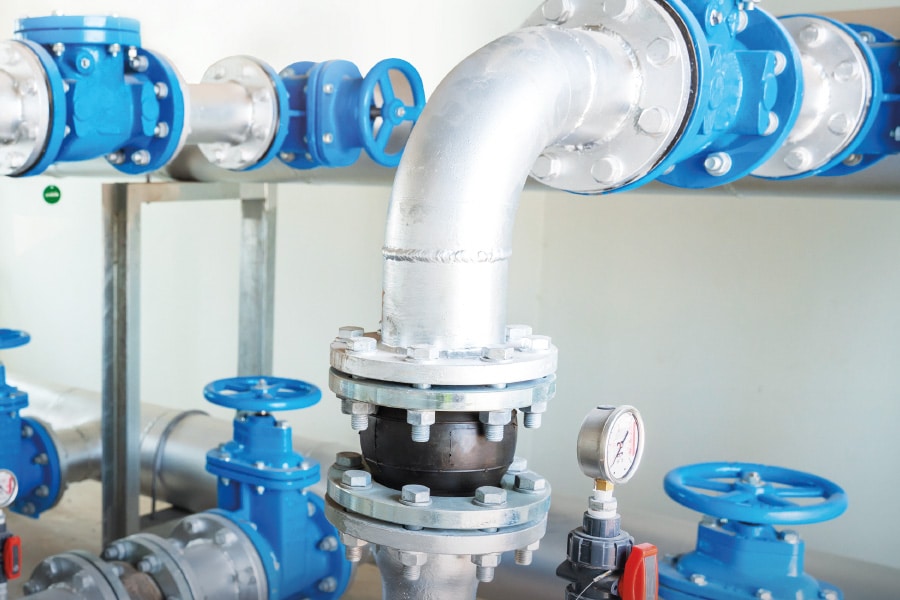
Blind hole thread in a valve body for cooling lubricants
Industry: Fluid technology
Material: 1.4301 / X5CrNi18-10
Target: maximum tool life in large-scale batch production
The valve body is used to control liquids, which is why the manufacturer relies on the excellent corrosion resistance of the chrome-nickel steel. However, the stainless austenitic high-grade steel has a high toughness and hardness, which makes deformation more difficult. Tool wear during thread production in this material is as high as you would anticipate: The hard particles damage the fluteless tap’s tool surfaces and the quality of the thread also suffers under the material’s high strength. Even tool breakage is not uncommon, as only a few fluteless taps can withstand the extremely high elongation.
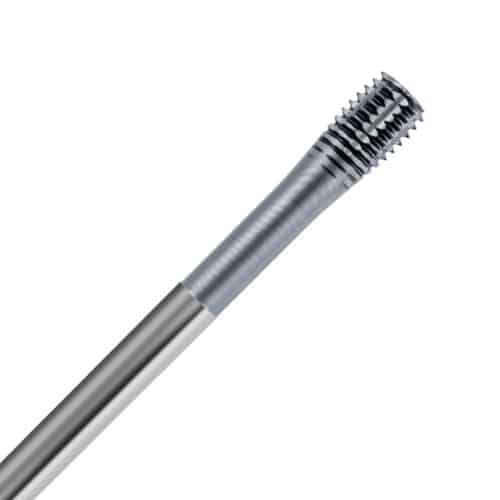
The new fluteless tap InoxPro succeeds where many conventional fluteless taps fail: its perfectly synced macro and micro geometry with an optimised lubricating flute geometry and polygon shape ensure reliable fluteless tapping in stainless steels. To minimise tool wear, we also rely on a particularly smooth and temperature-resistant
HiPIMS AICrN coating. You can also rest assured that you’ll enjoy the highest tool life and perfect dimensional accuracy for your threads in combination with water-mixed emulsions.
This product is only available from 10.09.2024!
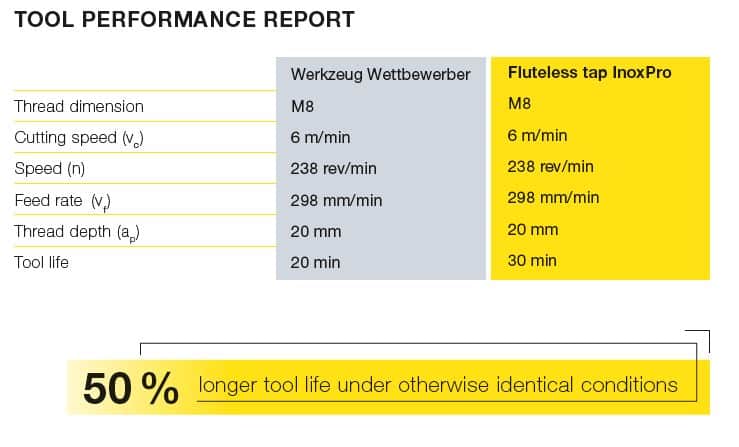
You might also be interested in:
150 % longer tool life: the interchangeable head drilling system for maximum cost-effectiveness
Modular drilling systems enable quick head changes within the machine – but if process reliability is lacking, the time savings can quickly become negligible. The BT 800 demonstrates that simple handling and performance don’t have to be mutually exclusive.
Maximum economic efficiency: Modular drill reduces set-up times and scrap for the customer
Tool life up, machining times down: With the BT 800 interchangeable head drilling system, the company Kurt Metallverarbeitung has found a modular solution that not only impresses with simpler handling, but also with outstanding performance.
Modular drills: Their advantages and how you can benefit from them
Modular drilling systems such as the BT 800 from Gühring offer full performance at lower costs. Thanks to interchangeable drill heads, you save time, storage space and money – ideal for flexible applications with the highest demands on cost-effectiveness.