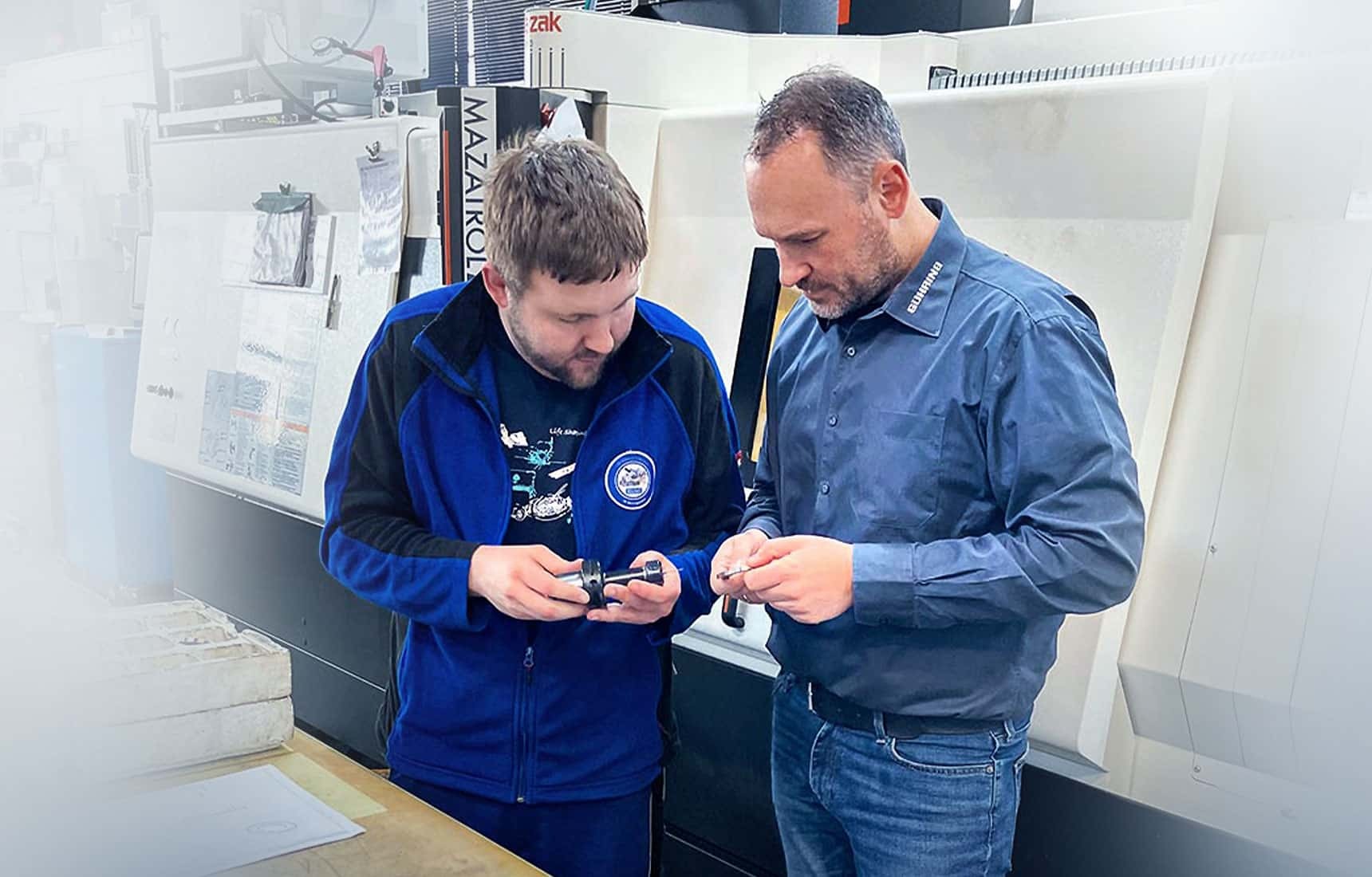
A good team for micro-drilling: Niki Hörner, CNC specialist at IBAG, and Gühring sales representative Marcel Horn.
Table of contents
1. Micro-drilling in stainless steel: A case for the ExclusiveLine micro-precision drill for stainless steel
2. Tool highlight for micro-drilling: ExclusiveLine micro-precision drill for stainless steel
3. For shorter machining times: 66 % faster drilling
4. Suitable tools with optimum cutting data: the Gühring online shop
5. FAQs: The most important questions about micro-drilling in stainless steel
The Zurich-based IBAG Group is a renowned manufacturer of high-frequency motor spindles in the world of tool and mould making as well as engraving, dressing and grinding. The highest quality standards and precision requirements play a central role here, especially in demanding micro-machining operations. IBAG finds the solution to these challenges in the ExclusiveLine micro-precision drill for stainless steel from Gühring, an expert in micro-precision drilling. This innovative tooling solution not only enables efficient job completion, but also results in an impressive reduction in machining times of up to 66 %.
At its site in Lindlar, IBAG Germany has not only specialised in the high-precision parts for its spindles: At its technology and demonstration centre, it is also able to immediately implement, analyse and optimise customer requirements. “We have the highest quality requirements for our components, including when it comes to positional tolerances,” explains Niki Hörner, CNC specialist at IBAG. “Some components require small holes, which are used for air transmission, for example. These holes must be manufactured with precise positioning – there is hardly any room for tolerances.” For this, the spindle manufacturer requires tools that are up to its own high standards. And with the help of Gühring, IBAG quickly found what it needed.
Micro-drilling in stainless steel: A case for the ExclusiveLine micro-precision drill for stainless steel
“In order to manufacture its high-performance spindles, the company IBAG needs reliable micro-tools that work very precisely even in the smallest range – and even in demanding materials,” says sales representative Marcel Horn. “I quickly realised: This is a case for the ExclusiveLine micro-precision drill for stainless steel.”
With its solid carbide micro-precision drill, Gühring offers a specialist for high machining performance in special alloys as well as in stainless and high-alloyed steels. Thanks to its innovative geometry, users do not have to worry about chip removal: The newly developed flute profile with a concave main cutting edge facilitates an impressive cutting response. From a diameter of 1.0 mm, the micro-precision drill is also available with cooling channels – another advantage that promotes chip removal. In addition, the Perrox coating ensures extremely high levels of protection against wear and adhesion. In combination with geometry and coating, the carbide guarantees high process reliability and unbeatable tool lives – even in material groups that place high demands on the tool.

Tool highlight for micro-drilling: ExclusiveLine micro-precision drill for stainless steel
The spindle manufacturer from the Rhineland region is also confronted with these high requirements when manufacturing air rings made of high-alloyed steel. An air ring has the important task of generating overpressure of 1 bar for sealing air in the front section of the spindle. This overpressure prevents external influences – such as grinding sludge, chips or other impurities – from entering the spindle and damaging it. For this protection mechanism to work, several holes with a diameter of 1.5 mm are needed. And they have to be in exactly the right position.
But this seems easier said than done at first: With the conventional HSS drill that IBAG used to use, the hole exits were anything but positionally accurate despite pre-centring. “The holes were partly tapered, and we also had to accept some tool breakage at the hole exit due to the incline,” explains Niki Hörner. For sales representative Marcel Horn, it was clear: The ExclusiveLine micro-precision drill for stainless steel would be better at this.
The tool is used in the 10xD design with a diameter of 1.5 mm (item no. 6490). And it achieved immediate success: “With the carbide micro-precision drill, we were able to make precise and straight holes in the air rings,” praises Hörner. In addition to the properties specially designed for machining high-alloyed steels, the internal cooling of the selected tool design also promotes optimum chip removal. But the ExclusiveLine micro-precision drill not only impresses in terms of its process reliability and precision: IBAG now also saves valuable time previously needed for pre-centring.
For shorter machining times: 70 % faster drilling
However, IBAG achieves unbeatable time savings in another component made of high-alloyed case hardened steel. A total of 5 holes with a drilling depth of just under 15 mm need to be drilled for each component. IBAG used to use an HSS drill for this, too, which required around 90 seconds for completion with an infeed of 1.5 mm per stroke per component. Impressed by the performance and precision of the ExclusiveLine micro-precision drill for stainless steel, IBAG also decided to test the high-tech tool for this application. And it achieved impressive time savings right from the outset: “With the solid carbide micro-precision drill, we were able to reduce the machining time per component by 60 seconds,” says Hörner happily. This is due to the high cutting data that can be achieved with the solid carbide micro-precision drill: With a feed rate of 0.5 mm/rev during piloting and a subsequent feed rate of 0.7 mm/rev, IBAG machines all 150 components – saving a total of 66% pure machining time. In addition to reduced tool wear, the company also saves on the additional centring tools, as the micro-precision drill facilitates direct machining on the shell without centring. IBAG can also significantly improve position accuracy and process reliability through the tool change cycle. “Thanks to IBAG’s high requirements, we were able to fully exploit the potential of the micro-precision drill. The cooperation is also beneficial for Gühring, because both sides can learn from each other,” summarises Marcel Horn.
Suitable tools with optimum cutting data: the Gühring online shop
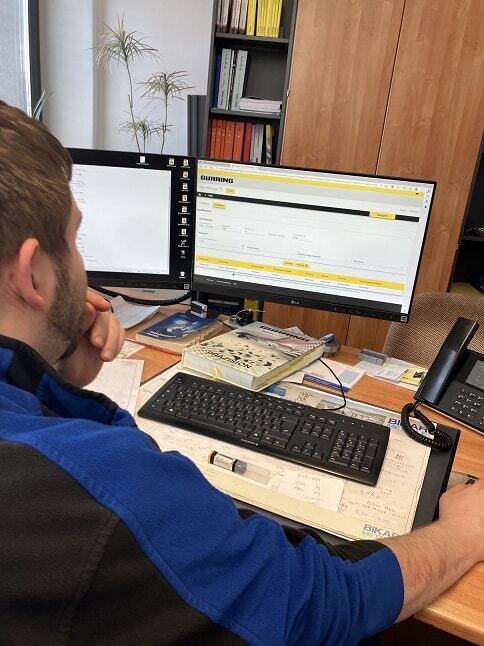
Perfect machining results require optimum cutting data. Here, too, Niki Hörner sees a major advantage of working with Gühring: “Via the online shop, we can easily and conveniently access cutting data. This makes it easier for us to get to grips with different machining processes and new tools.” And that’s not the only benefit: In the online shop, prices and stocks can be checked with just a few clicks and reordered around the clock. This also facilitates cooperation between purchasing and production: Before ordering, the production manager can check the tools that the purchasing team has placed in the shopping basket. Thanks to the online shop and cutting data, IBAG can therefore not only rely on optimum processing results in record time – the time savings start right from the order process.
Have we piqued your interest?
Technical advice and support are also available quickly and directly via our service hotline 00800 2607 2607
We can also be reached on WhatsApp: +49 172 658 53 53. Or you can buy the ExclusiveLine micro-precision drill for stainless steel from our online shop.
FAQs: The most important questions about micro-drilling in stainless steel
What is micro-drilling and how is it different from standard drilling methods?
Micro-drilling refers to a precision manufacturing process in which holes with diameters in the micrometer range are produced. It differs from standard drilling methods in terms of the achievable size and precision of the holes; the equipment and technology needed are also much more intricate and more accurate.
Why is selecting the right tool for micro-machining so crucial?
Choosing the right tool is critical, as the quality and accuracy of micro-machined parts depend directly on the precision of the tool. The tools must also be specifically designed for micro-level machining to minimise wear and maximise tool life.
How can surface finish and precision be optimised when micro-drilling stainless steel materials?
Surface quality can be optimised and precision increased by using specialised cutting fluids, adjusting the spindle speed and feed rate, and using micro-drilling tools with special coatings.
What are the biggest challenges when micro-drilling stainless steel materials?
The challenges include avoiding thermal influences, preventing burr development and removing chips from deep holes. It also requires precision control of machining parameters to achieve the desired level of accuracy.
What role do coatings play in micro-drilling tools for machining stainless steel?
Coatings such as titanium nitride (TiN) can improve the hardness and wear resistance of tools, resulting in a longer tool life and better surface quality. They can also reduce friction, allowing for less heat generation and better machining results.
How can the cost-effectiveness of micro-machining in stainless steel be improved?
The economic efficiency of micro-machining in stainless steel can be improved by optimising machining parameters, reusing tools, automating processes and minimising reject rates. Process monitoring and control also help to reduce errors and thus increase efficiency. In addition, close collaboration with tool manufacturers and technology providers can produce innovative solutions that reduce costs and optimise production.
You might also be interested in:
Modular drills: Their advantages and how you can benefit from them
Modular drilling systems such as the BT 800 from Gühring offer full performance at lower costs. Thanks to interchangeable drill heads, you save time, storage space and money – ideal for flexible applications with the highest demands on cost-effectiveness.
Threads for giants: Crane manufacturer relies on modular fluteless tap for blind holes
An innovation – the new modular fluteless tap from Gühring – has made it possible to solve deep-seated challenges in the production of blind hole threads at Karl Georg and to raise process reliability to a new level.
30% more tool life: With this parting off plate you achieve maximum performance in high-grade steel
30% more tool life when parting off: The new 2 mm parting off plate from Gühring’s System 222 impresses with excellent chip control, high process reliability and a perfect surface finish on ISO-M materials such as high-grade steel.