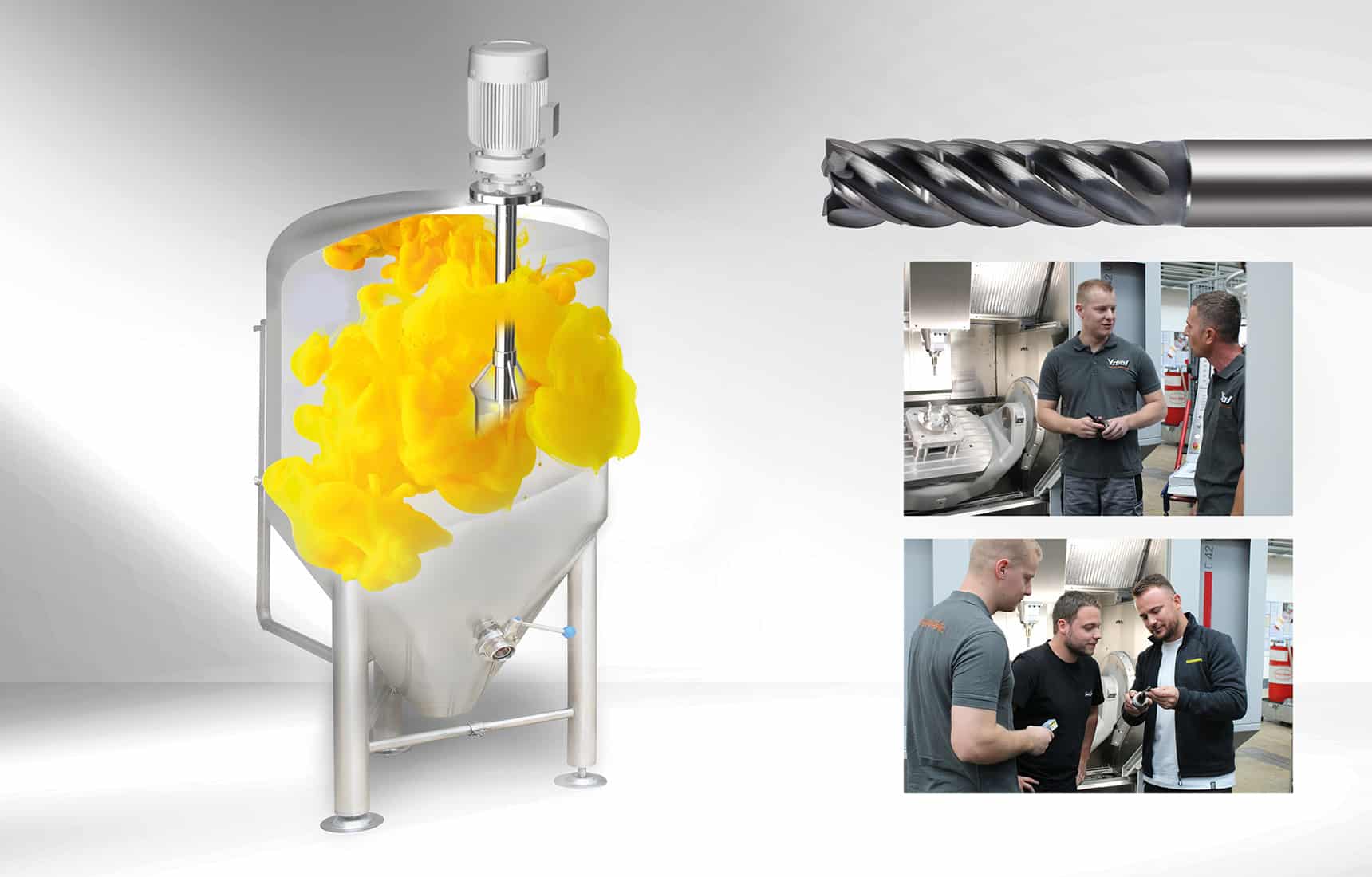
When milling wing supports made of highly abrasive austenitic chromenickel steel, milling cutters at ystral gmbh fail after just one component. A solid carbide milling cutter from Gühring ensures the necessary process reliability thanks to its two-fold tool life.
Chipped coatings and high cutting edge wear – when milling wing supports, milling cutters at ystral gmbh quickly reached their limits. “After one component, it was over”, recalls Deputy Production Manager Marco Wissmann. “That’s simply not a reliable process.” This high level of wear is due to the material to be machined: 98 percent of the components manufactured on the state-of-the-art milling machines of this attractive employer in the Markgräflerland region are made of stainless, austenitic chrome-nickel steel.
This highly tough stainless steel is resistant to chemicals and therefore perfectly suited to the wing supports installed in large mixing tanks for the pharmaceutical and chemical industries. But at the same time, the material is highly abrasive and difficult-to-machine. Gühring sales representative Oliver Mattes also noticed the many worn milling cutters during one of his regular customer visits to ystral. “When I asked, I learned that many suppliers found this material a hard nut to crack”, he recalls. He knows the challenges of stainless steel processing: Heat causes the material to warp. To ensure that a component with perfect threads and fits is created in the end, the milling cutter must exert only a little pressure on the material. In addition, manufacturing at ystral also runs automatically at night and at weekends – so process reliability is paramount.
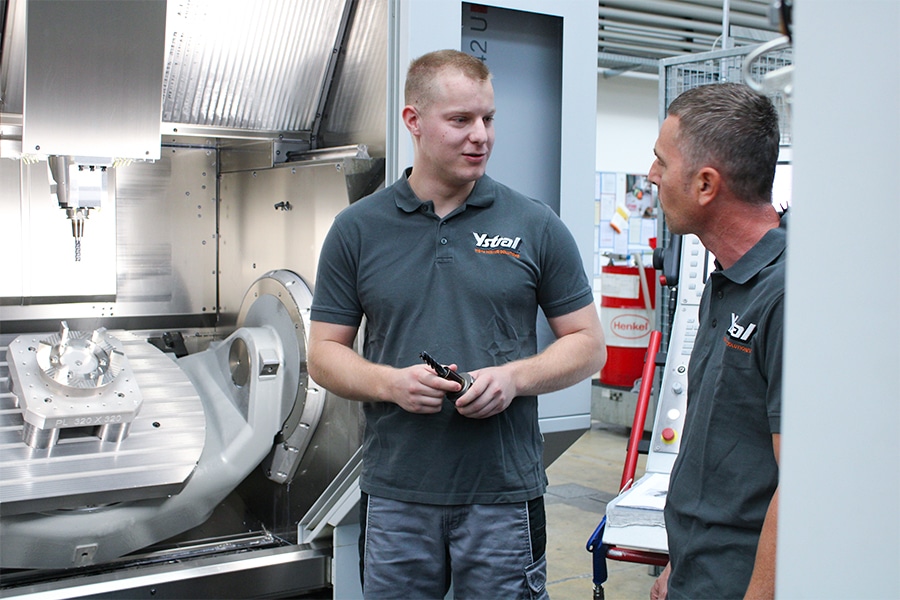
After tests by Tim Zorawski (left) and Andreas Krumnack (right), the result is impressive.
Gühring milling cutter puts an end to chip nests
Confidently, Oliver Mattes offered ystral to start a trial with a Gühring milling cutter – and had just the right one in mind: the RF 100 5 Speed. “The speed is optimal for this application because it is particularly strong in V4A”, says Oliver Mattes. The solid carbide milling cutter from Gühring ensures extreme metal removal rates even in difficult-to-machine materials with the highest process reliability. With five teeth and a large helix angle of 38°, it is perfect for roughing. The RF 100 5 Speed is also equipped with a 9° back rake angle and offset chip breakers – a major advantage, as Wissmann explains: “When we used tools without chip breakers, chip nests were constantly formed in the machine as chip removal was not possible.” The machine had to be stopped constantly for chip removal. “We save this time now because the much shorter chips are simply flushed out”, says Wissmann happily.
Overcoming all the hurdles
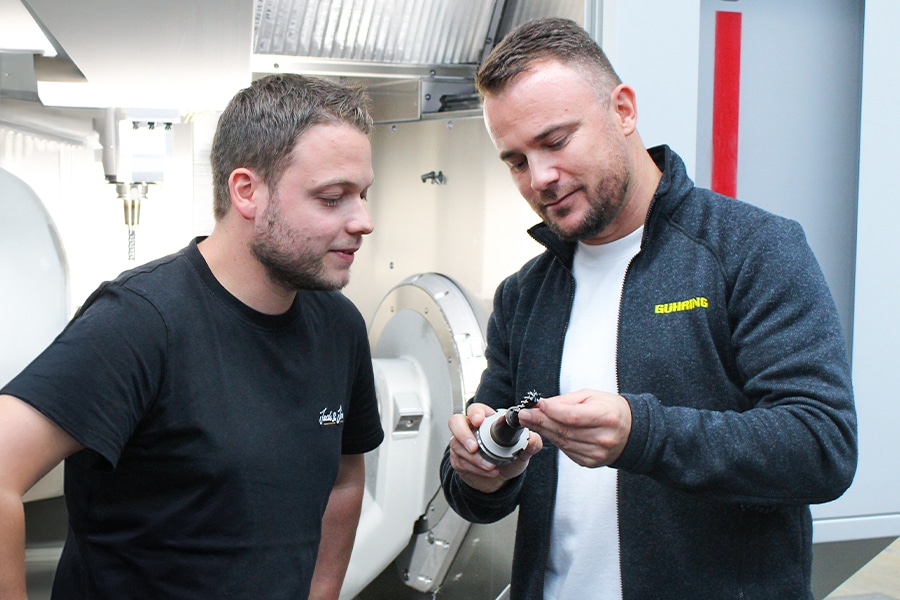
Working together to find a solution: Marco Wissmann (ystral) and Oliver Mattes (Gühring).
The wing supports with 200 to 230 mm diameter are manufactured as turned parts. The wings, which later serve to disperse the liquids in the tank, are then milled out on the milling machine. This milling operation is carried out in the trochoidal process. The milling cutter moves in an elliptical circular motion and plunges into the material with its entire cutting edge length. This highly dynamic milling technology means that process reliability, tool life and time savings are particularly high – and the RF 100 5 Speed is perfect for this, as it enables up to 10 percent lateral infeed. The contour is then finished with the same tool. The surface quality plays an important role here, as the finished wing supports must have an Ra value of 0.8 mm.
In terms of cutting values, Gühring is guided by the previously used tool of a competitor. Marco Wissmann explains: “The average values set the times that we have to keep achieving, because we didn’t want to work slower.” The production manager explains that the count began immediately: “Old milling cutter out, new one in; once it is up and running, we buy it.” After extensive tests by Tim Zorawski and Andreas Krumnack, the result was convincing.
The high-quality SuperA coating of the RF 100 5 Speed breaks off significantly later, so that instead of the previous one component, the Gühring milling cutter can be used to produce two components. “I was also impressed by the fast delivery time”, explains Wissmann. “Whenever we need something, an application technician is always there quickly. This service is simply very good.” Oliver Mattes is also satisfied with the result: “There are always a few hurdles with such a material, but they were all solved in a very reasonable time.”
Tool | RF 100 5 Speed (Art.-Nr. 6858) |
Material | Austenitic chrome-nickel steel (1.4404 / X2CrNiMo17-12-2) |
Diameter | Ø = 16 mm |
Cutting speed | Vc = 180 m/min |
Feed | f = 3.340 mm/rev |
Feed rate | fz = 0,21 mm/z |
Lateral delivery | ae = 21 % |
Technical advice and support are also available quickly and directly via our service hotline 00800 2607 2607. We can also be reached on WhatsApp: +49 172 658 53 53. Save the number!
You might also be interested in:
Experts in stainless steels: 3 tools for stainless steel machining
With the new high-performance tools for stainless steel machining, Gühring offers the optimal solution. Special coatings and adapted geometries guarantee the highest cutting values and extended service life. This means that the most demanding machining tasks can be mastered in a wide range of industries.
Six times higher metal removal rate: New micro-precision milling cutter for ISO-N materials
The RF 100 AL Micro offers an outstanding combination of precision, efficiency and process reliability, making it the first choice when machining aluminium, copper and brass. With its innovative properties this tool raises the bar for micro-machining.
Finger on the pulse: Pocket milling in grade 5 titanium
A customer uses grade 5 titanium to make the case for pacemaker batteries, but machining the material is challenging. Gühring has the solution: The G-Mold 65 HF solid carbide end mill enabled it to extend the tool life 73 times over.