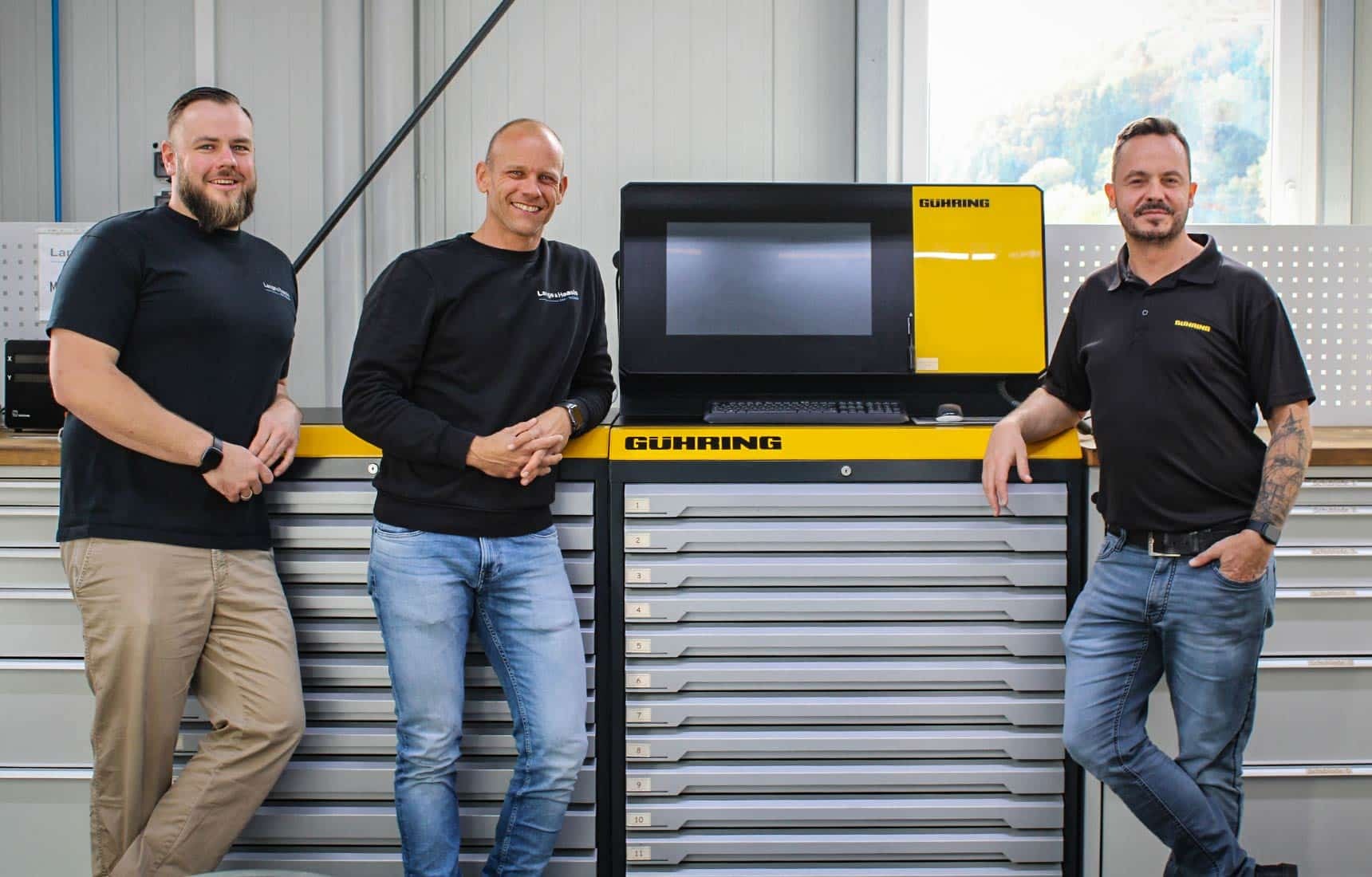
Table of contents
1. For reliable processes: Never miss a calibration again
2. Quality management in companies– self-explanatory and easy to handle
3. Measuring instruments are only the beginning when it comes to quality monitoring
4. FAQs regarding measuring equipment management with GTMS
Wherever components are manufactured with high precision, regularly calibrated measuring instruments are essential. But how do you stay on top of things? Lange & Haasis has switched from handouts to digital measuring equipment management with Gühring Tool Management Software (GTMS) – and is saving a lot of time in this way.
Measuring screws, limit gauges, thread gauges – the machinists at Lange & Haasis always have their measuring equipment to hand to check the quality and dimensional accuracy of construction parts. Although the products produced by the company for CNC metalworking in Albstadt differ greatly, they all have one thing in common: Highest precision down to the µ range. “No order is processed without measuring instruments”, notes founder and co-owner Jens Lange. And that’s why there are so many of them in Lange & Haasis’ production.
The problem: Measuring instruments have an expiry date and must be recalibrated before expiry. Uncalibrated measuring instruments must not be used for measurement. But how do you keep track of all the measuring equipment in everyday production? Jens Lange had to find out in his company that management using handouts is not the perfect solution: “That was a huge source of error when it came to calibration cycles”, he recalls. In addition, employees were never able to trace who had taken which measuring instruments and spent a lot of time searching for them. Plus, the company is certified according to the ISO 9001 international standard, which stands for process-oriented quality management.
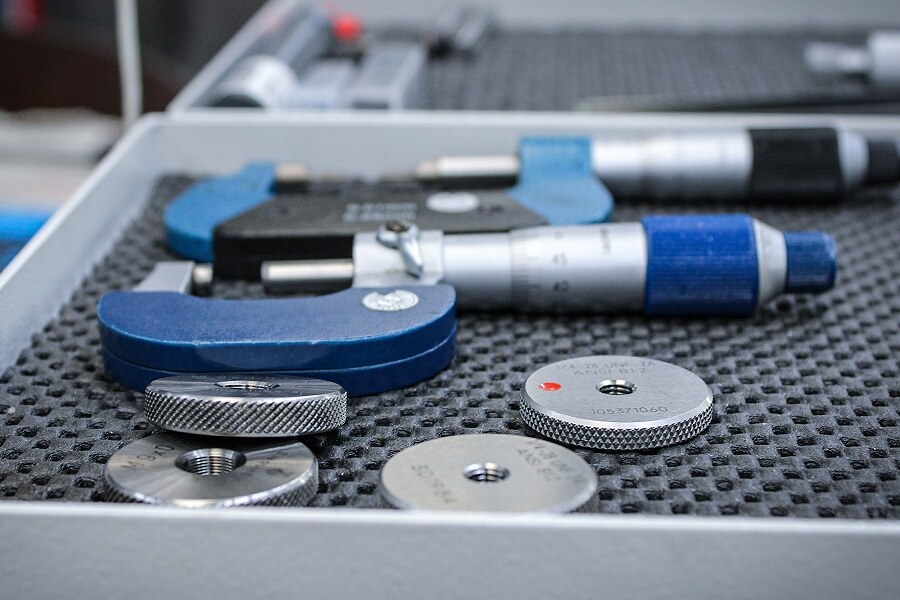
“In order to maintain this certification and expand the associated processes, we need measuring equipment management”, says Patrick Maier, who is responsible for measuring equipment management at Lange & Haasis. “We wanted a quick and simple solution that would give us more structure and control in our measurement equipment management.” The simple solution is just a few kilometers away: Lange & Haasis has been working very closely with Gühring for 20 years. So it was clear for Patrick Maier: “The regional aspect and the ability to quickly ask questions and solve problems were very important to us, which is why we did not need to look at other software solutions.”
For reliable processes: Never miss a calibration again
The Gühring Tool Management Software (GTMS) can cover all production and logistics-relevant areas in companies. GTMS offers a way to manage measuring instruments and the corresponding calibrations. Test dates are permanently monitored digitally and internal calibrations are created, carried out and documented in accordance with an audit based on a stored test plan. In addition to ISO 9001, which is so important for Lange & Haasis, IATF 16949 and QSF-A 1998 are also covered by the GTMS. Anyone who combines the software with a Gühring tool cabinet can also specify that only calibrated measuring instruments are removed from drawers and all others are blocked. All of this ensures that sufficient measuring instruments are always available in production and that documentation gaps during customer audits are avoided. “GTMS is perfect for all customers who do not want to lose track of their testing and operating resources”, summarises Christoph Schönhaar, who looks after the company as a Gühring software expert.
Quality management in companies – self-explanatory and easy to handle
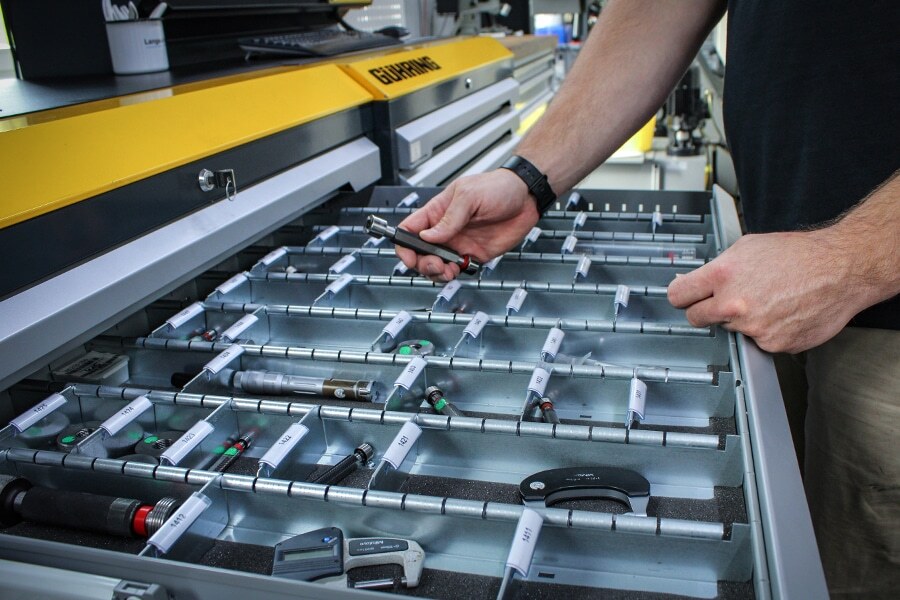
This is exactly what Lange & Haasis wanted: “First of all, we wanted to digitalise measuring equipment management so that we could minimise search efforts and establish traceability of the measuring equipment removal”, explains Patrick Maier. It was particularly important to them that the new system be simple to use and self-explanatory and could be used quickly and error-free by all employees. After Christoph Schönhaar showed him the possibilities of GTMS, he quickly realised: “With Gühring, we have found the perfect partner!”
Schönhaar says that the planning and implementation of the project then went quite quickly and smoothly: “There was always honest and direct feedback, which helped us find the right solutions.” This is what Patrick Maier thinks: “No matter what problem we had, a targeted solution was always found immediately!”
Measuring instruments are only the beginning when it comes to quality monitoring
Where is the measuring instrument or who has it? How often was it used? When is the next calibration interval? Thanks to GTMS, Lange & Haasis employees can now answer all these questions at a glance. Because its measuring equipment is now managed centrally, Lange & Haasis employees can put together everything they need for an order much more quickly. “The time savings associated with measuring equipment management are enormous,” notes Patrick Maier. But that’s not all: “The long-term goal is for us to implement our complete production, tool and warehouse management with the GTMS from Gühring and use the software to the fullest extent possible”, says Jens Lange.
Further GTMS modules are to be built up gradually in order to further digitalise manufacturing. “Thanks to GTMS, many functions can be covered with a single software solution”, explains Schönhaar. “The next steps could now be towards warehouse management and machine connection.” The new measuring equipment management is therefore only a first important step on the road to digital manufacturing. This is also Jens Lange’s conclusion: “With GTMS, we as a medium-sized company have taken a big step towards digitalisation.”
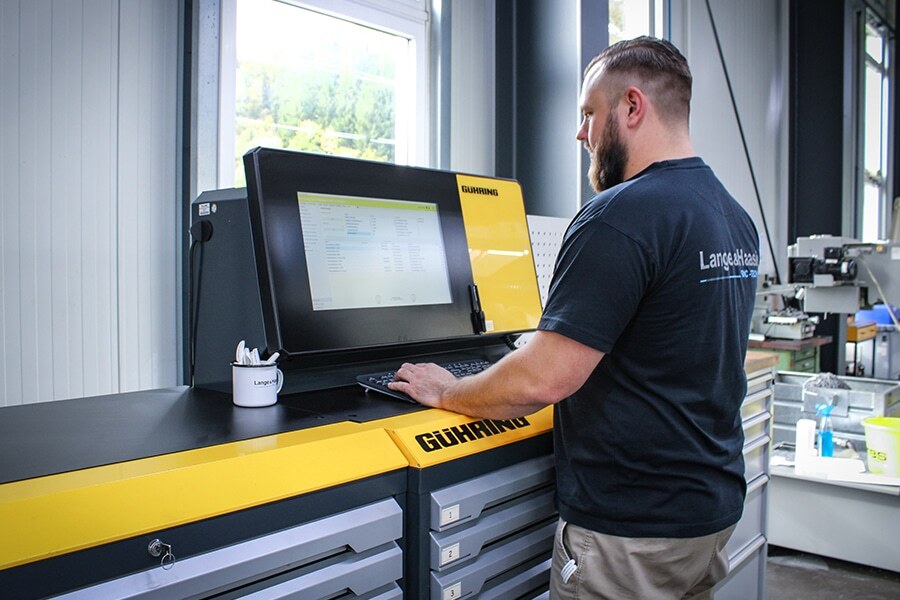
FAQs regarding measuring equipment management with GTMS
What is measuring equipment management in the context of a company?
Measuring equipment management is a systematic approach to managing and monitoring all measuring instruments and test equipment in a company. It includes the recording, calibration, maintenance and monitoring of measuring instruments to ensure precise measurements and thus product quality.
Why is regular calibration of measuring equipment so important?
Regular calibrations are critical to maintaining the accuracy and reliability of measuring equipment. They are used to identify and correct deviations that may occur due to normal wear and tear.
Why is automated measuring equipment management so important for quality management?
Automated measuring equipment management ensures that all tools and components in the production process are properly maintained and calibrated. This minimises errors and downtime, increases production efficiency and guarantees compliance with quality standards.
What is GTMS and how does it support quality management processes in companies?
GTMS stands for Gühring Tool Management Software. It is a piece of tool management software that supports quality assurance by accurately tracking and monitoring tools and measuring devices. GTMS helps to organise and document testing processes, which is essential for compliance with quality standards.
How can GTMS improve quality control efficiency?
GTMS improves efficiency by automating administrative tasks such as inventory monitoring and maintenance planning. This leads to a faster response to tooling needs and issues, which in turn increases process quality.
What can be used to optimise the quality control processes with GTMS?
Processes can be optimised through automated data collection, real-time reporting, and alarm functions that raise awareness of deviations. This enables rapid intervention and continuous improvement.
Technical advice and support are also available quickly and directly via our service hotline 00800 2607 2607
We can also be reached on WhatsApp: +49 172 658 53 53. Save the number!
You might also be interested in:
Tool management in flux: Keeping track with digital tech
Getsch+Hiller optimiert mit der Gühring Tool Management Software (GTMS) seine Werkzeugverwaltung. Dank digitaler Ausgabeschränke und modularer Software spart das Unternehmen Zeit, reduziert Kosten und bleibt flexibel – perfekt angepasst an das schnelle Wachstum der Medizintechnik.
Detailed data on your tools: The GTMS tool data module
Increase your efficiency with the GTMS tool data module. Avoid sources of error, optimise set-up times and gain full transparency over tool requirements and component costs. Experience precise tool data management for maximum control.
A glimpse into your machine: The GTMS Machine module
Efficient machine management – that’s what the Gühring Tool Management Software (GTMS) stands for. Because with the machine module you ensure transparency, prevent downtimes, optimize the machine park and increase the OEE.