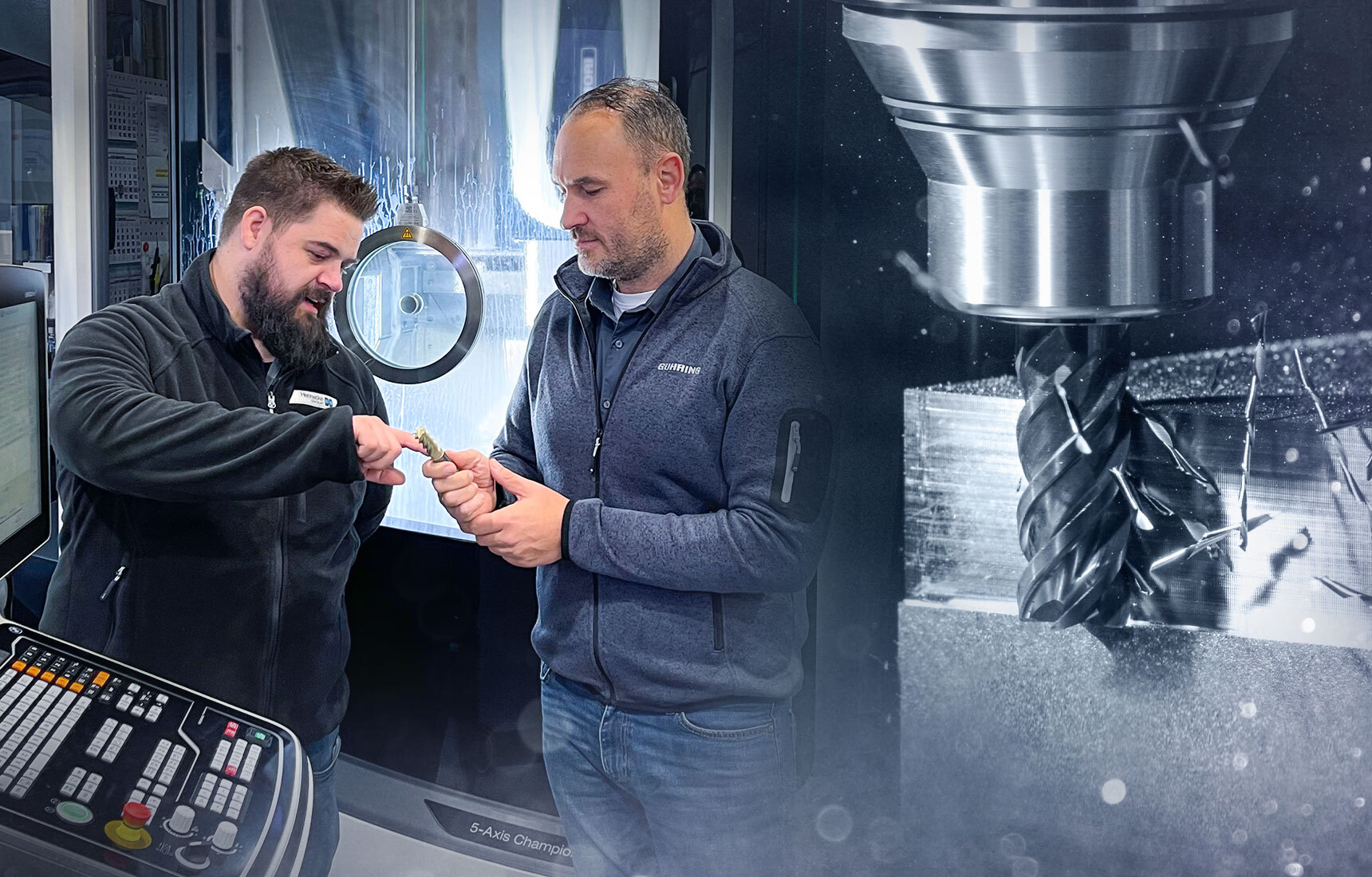
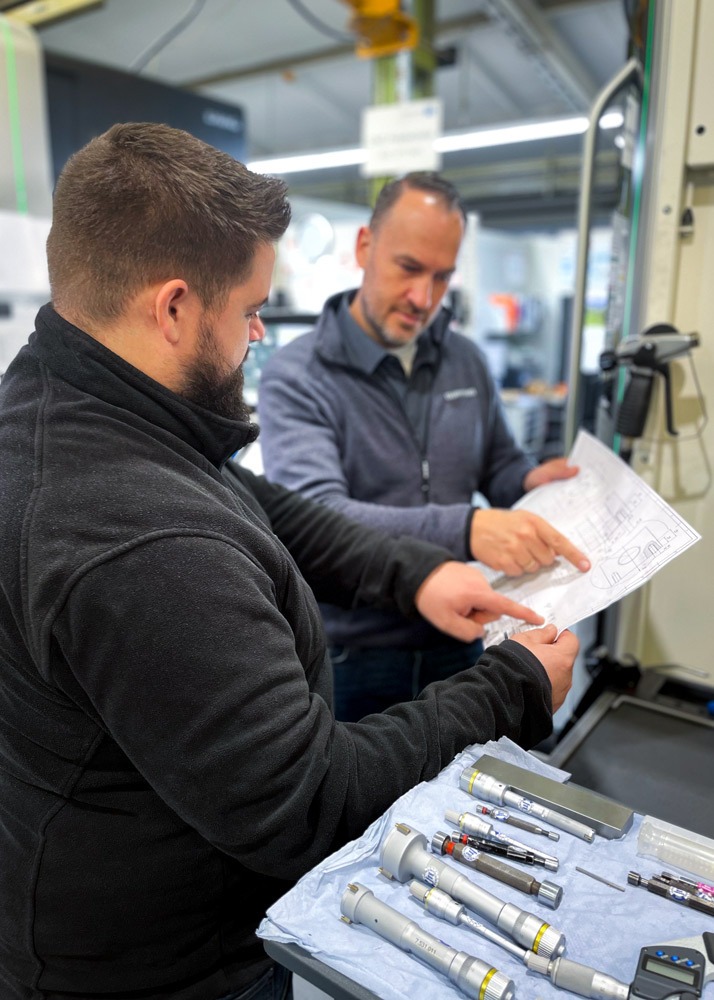
Double the tool life
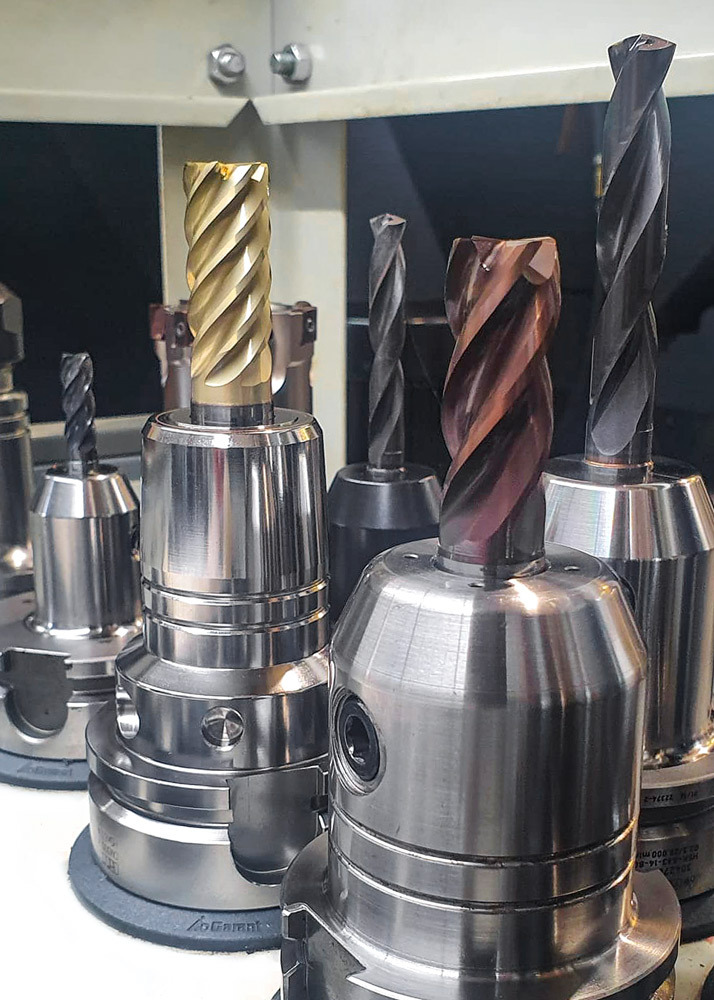
The RF 100 Speed P is characterised by high metal removal rates and stable process reliability. Even in materials that are difficult to machine. The uneven blade pitch of the RF 100 Speed P also improves running smoothness in HPC milling and leads to excellent surface quality. The stable cutting edge corners with corner chamfer and correction of the front offer optimum protection against wear. This results in a longer tool life, which benefits Hennecke.
Four times the cutting speed
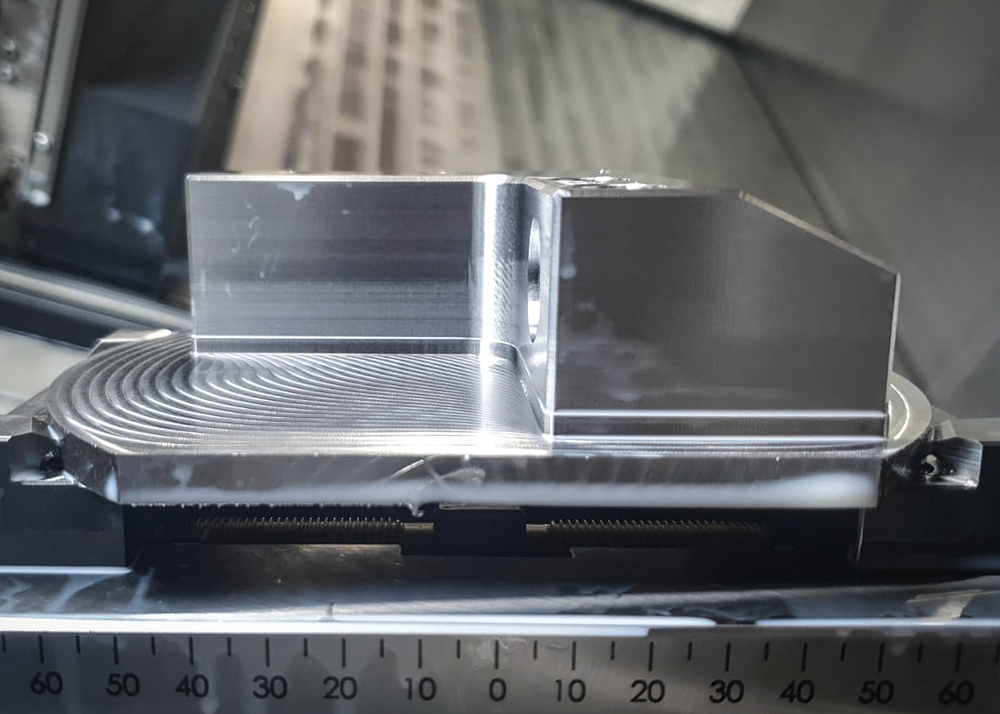
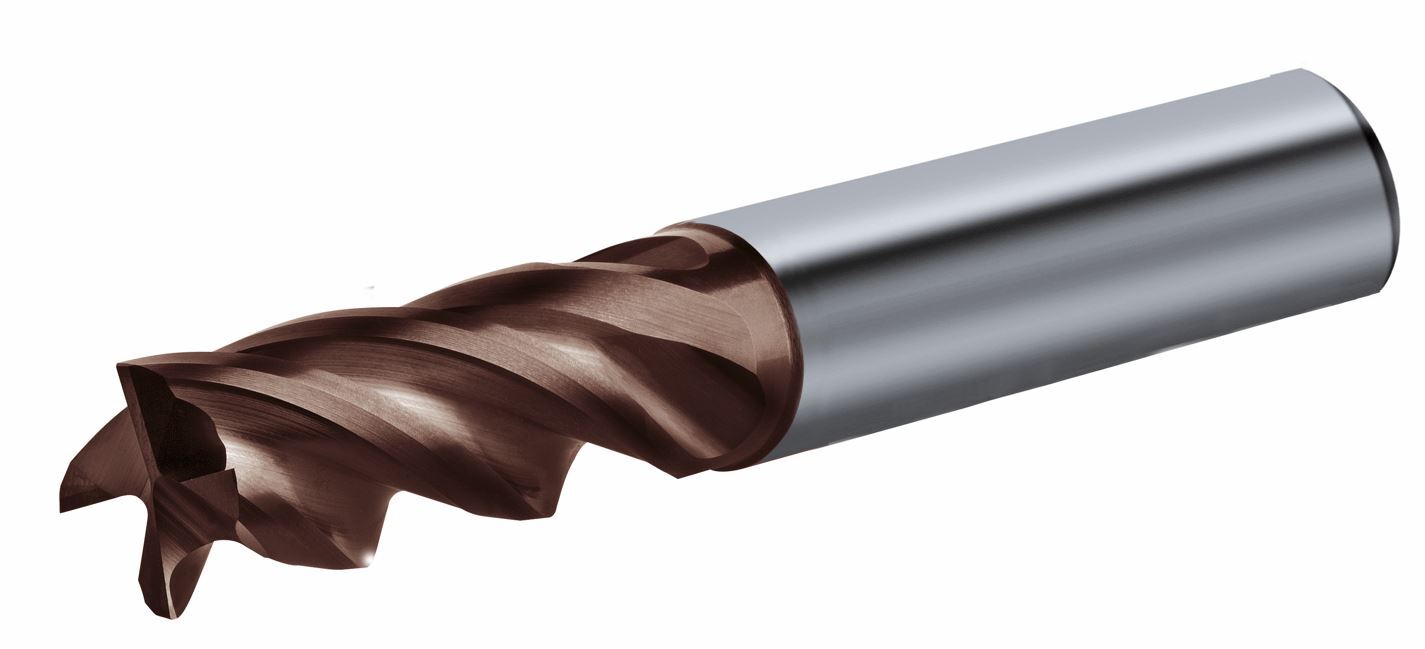
Half the machining time
Hennecke recently started using the high-performance RF 100 VA end mill: Another example of a tool that enables the customer to benefit from higher metal removal rates and tool lives. When manufacturing a mixing head blank, the RF 100 VA doubled the previous cutting speed from 90 m/min to 180 m/min, saving an impressive 9 minutes per component. This tool is particularly suitable for soft, ductile and stainless steels. The milling cutter impresses with its smooth running, optimum chip removal and stable cutting edge corners. “We were able to achieve good results using the RF 100 VA in high-alloy stainless steel,” says Hörger.
Uncovering potential with Gühring
Hennecke shows that the search for a better alternative does not always have to be preceded by complications. Gühring always sees itself as a technology partner for its customers. With the common goal of enhancing processes on an ongoing basis. While other manufacturers stick to established processes, Hennecke is exploiting hidden potential through foresight. And, as a result, it is able to reduce costs and machining times across several tool categories and significantly extend tool lives. In addition to milling cutters, the company now also uses numerous grooving systems as well as micro and deep hole drills, combined with the same advantages: Time and cost savings.
Gühring shows that changing tools in this way can be easy. In many places, Hennecke was able to replace the tools directly and has already noticed significant improvements. With the cutting data that Gühring provides free of charge via the Navigator, the customer also saves precious time during setup. And all this without any compromises, because the need for top quality never loses its priority.
Have we piqued your interest?
We can also be reached on WhatsApp: +49 172 658 53 53. Save the number!
You might also be interested in:
Modular drills: Their advantages and how you can benefit from them
Modular drilling systems such as the BT 800 from Gühring offer full performance at lower costs. Thanks to interchangeable drill heads, you save time, storage space and money – ideal for flexible applications with the highest demands on cost-effectiveness.
Threads for giants: Crane manufacturer relies on modular fluteless tap for blind holes
An innovation – the new modular fluteless tap from Gühring – has made it possible to solve deep-seated challenges in the production of blind hole threads at Karl Georg and to raise process reliability to a new level.
30% more tool life: With this parting off plate you achieve maximum performance in high-grade steel
30% more tool life when parting off: The new 2 mm parting off plate from Gühring’s System 222 impresses with excellent chip control, high process reliability and a perfect surface finish on ISO-M materials such as high-grade steel.