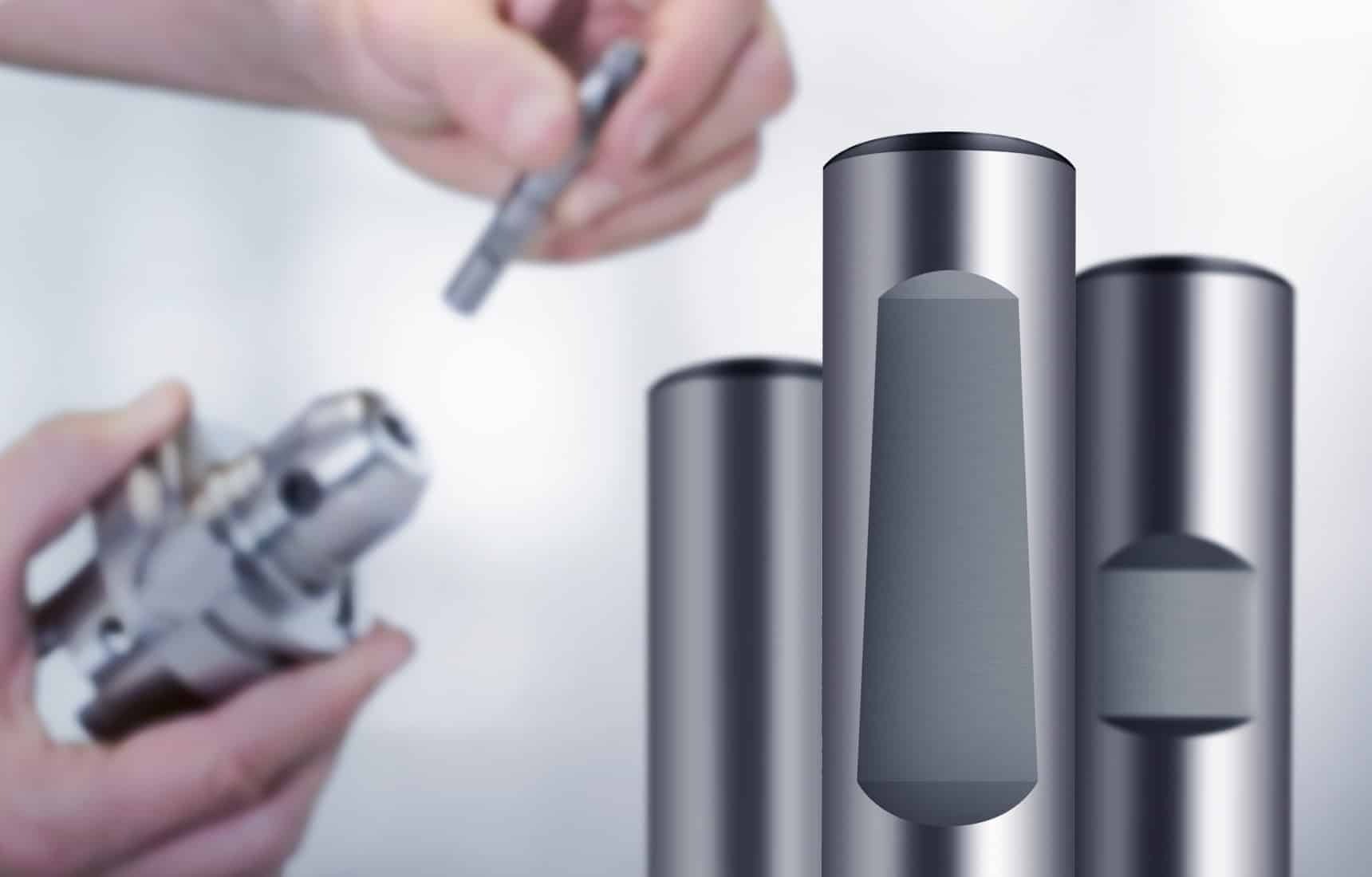
Inhalt
1. HA clamping surface: Smooth shank for drills from 7xD
2. HB clamping surface: Ideal for milling cutters in combination with Weldon tool holder
3. HE clamping surface: Best choice for drills in combination with whistle notch tool holder
4. For perfect concentricity, clamping surfaces and tool holders match up
5. FAQs about tool holder and clamping chuck
The interaction between the tool shank and clamping chuck is crucial for perfect concentricity when machining workpieces. An optimum result can only be achieved if the tool shank and clamping chuck are perfectly matched to each other according to the rule of thumb: “Same to same”. In this article, we present the various clamping surfaces HA, HB and HE and explain how the selection of the wrong clamping surface can have an impact on the tool life of drills and milling cutters as well as on component quality.
The milling cutter is perfectly clamped – and yet sudden tool life problems occur during milling. How is this possible? One reason that is often overlooked is the compatibility of the clamping surface and the tool holder. There are three types of clamping surfaces on the tool shank: HA, HB and HE. In this article, we take a closer look at the three clamping surfaces.
HA clamping surface: Smooth shank for drills from 7xD
If the tool needs to have very good concentricity for machining, a tool shank with a HA clamping surface is recommended. Gühring therefore, offers only this smooth surface on the shank for all drills with a diameter-length ratio from 7xD.
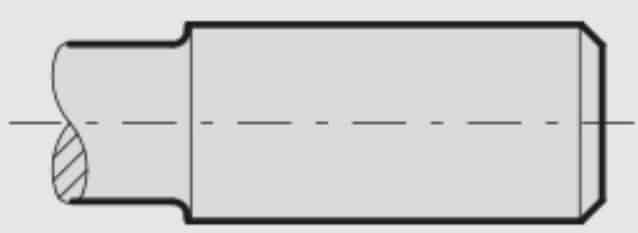
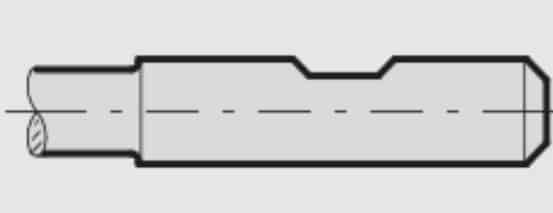
HB clamping surface: Ideal for milling cutters in combination with Weldon holders
The HB clamping surface is characterised by a small flat surface which is ground parallel to the axis. However, the small flat surface is more intended for milling cutters. The clamping chuck is also referred to as the Weldon holder, one of the most common forms of clamping chuck. The clamping screw of the holder is specially adapted to the HB surface of the tool – it ensures a form-fitting connection. However, you should make sure that you only use genuine Weldon clamping screws. If these are replaced by a standard screw, the form-fitting connection is lost. For shank diameters between 25 and 32mm, there are two flats on the shank and the holder is clamped by two clamping screws.
HE clamping surface: The ideal choice for drills in combination with whistle notch holders
For drilling, a HE clamping surface is the better choice. It is slightly inclined – as is the screw with which the tool is clamped in the so-called whistle notch holder. This will push the drill into the chuck and prevent it from pulling out of the chuck. The 2° angle acts like a wedge placed under a car tyre to prevent the vehicle from rolling away. As an additional feature, this system offers length adjustment from the drilling tool to the length of the clamping surface.
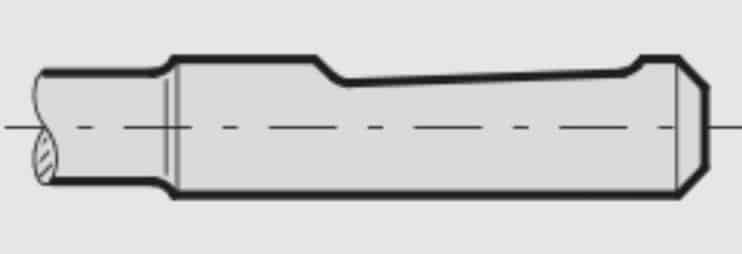
For perfect concentricity, clamping surfaces and tool holders match up
In addition to the different suitability of the shank shapes for the respective machining task, one thing above all must be taken into account: The tool and the holder must always match up – otherwise you run the risk that the machining will not run smoothly in the truest sense of the word. For example, if you combine a drill with a HE shank with a Weldon holder, you are clamping an inclined tool clamping surface with a straight screw – the drill is only clamped with one corner. As a result, the drill may move axially. In the worst case, the drill can break due to the wedge effect when clamping in the holder.
The same applies in reverse: If you clamp a milling cutter with a HB clamping surface in a whistle notch holder, the angled clamping screw presses on a straight surface. There is no frictional connection and you run the risk of the milling cutter being pulled out of the chuck. Similarly, the milling cutter’s shank can also break due to the point-like pressure.
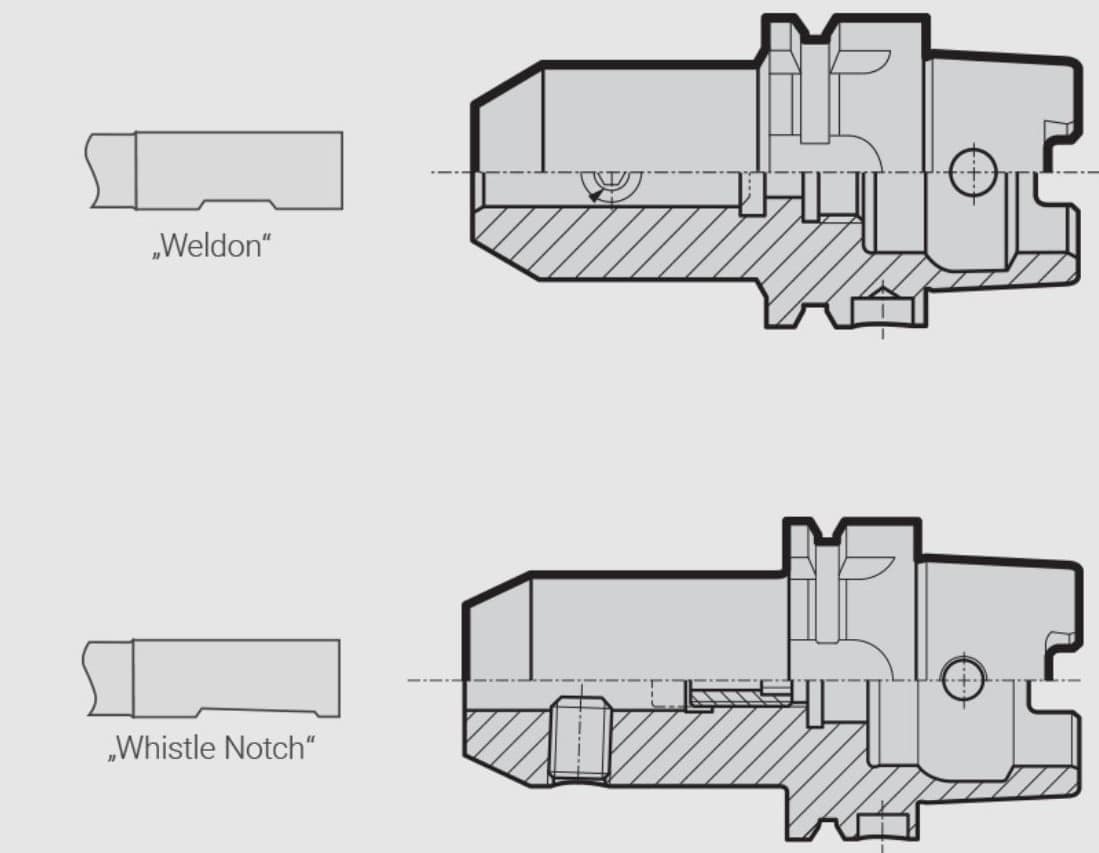
Therefore, it is important to always remember: HB shank to Weldon tool holder and HE shank to whistle notch holder – for optimum concentricity.
And by the way – Whether Weldon or whistle notch – you always have some play when drilling, as the tool must be minimally smaller than the holder. As a result, the tool is pushed slightly “off centre” during clamping with the lateral clamping screw. The result? A concentricity error of up to 10 µm.
FAQs on tool shanks and clamping chucks
Why is it so important that the clamping surface of the tool matches the clamping chuck?
When machining workpieces, choosing the correct clamping surface on the tool shank is critical to achieving perfect concentricity. If the clamping surfaces of the tool do not match the clamping chuck, this can lead to problems with the tool life of drills and milling cutters.
What are the different clamping surfaces on tool shanks?
There are three different types of clamping surfaces: HA, HB and HE.
For which tools is a HA clamping surface suitable?
The HA clamping surface is recommended for drills from a diameter of 7xD.
What is the HB clamping surface and what is it used for?
The HB clamping surface is a small flat surface that is ground parallel to the axis and is primarily intended for milling cutters.
What is the HE clamping surface and what is it used for?
The HE clamping surface is slightly inclined and is particularly well suited for drilling.
What happens when I clamp a HE shank in a Weldon holder?
If you clamp an inclined surface with a straight screw, the tool is only clamped with one corner. The pressure that presses the tool towards the machine spindle is too low. This can cause the tool to move axially or even break.
What can you do if concentricity problems occur in spite of suitable clamping surfaces?
If concentricity problems arise when using the appropriate clamping surfaces, other factors such as the machine spindle or workpieces may be important. We recommend checking these factors as well.
What is the Weldon holder and what is it used for?
The Weldon holder is a common clamping chuck used primarily for milling cutters. Here, the HB clamping surface of the tool is held by a small flat surface.
What is the whistle notch holder and what is it used for?
The whistle notch holder is a clamping fixture primarily used for drilling. Here, the HE clamping surface of the tool is held by a slightly inclined surface.
Have we piqued your interest?
Technical advice and support are also available quickly and directly via our service hotline 00800 2607 2607
We can also be reached on WhatsApp: +49 172 658 53 53. Save the number!
You might also be interested in:
Modular drills: Their advantages and how you can benefit from them
Modular drilling systems such as the BT 800 from Gühring offer full performance at lower costs. Thanks to interchangeable drill heads, you save time, storage space and money – ideal for flexible applications with the highest demands on cost-effectiveness.
Threads for giants: Crane manufacturer relies on modular fluteless tap for blind holes
An innovation – the new modular fluteless tap from Gühring – has made it possible to solve deep-seated challenges in the production of blind hole threads at Karl Georg and to raise process reliability to a new level.
30% more tool life: With this parting off plate you achieve maximum performance in high-grade steel
30% more tool life when parting off: The new 2 mm parting off plate from Gühring’s System 222 impresses with excellent chip control, high process reliability and a perfect surface finish on ISO-M materials such as high-grade steel.