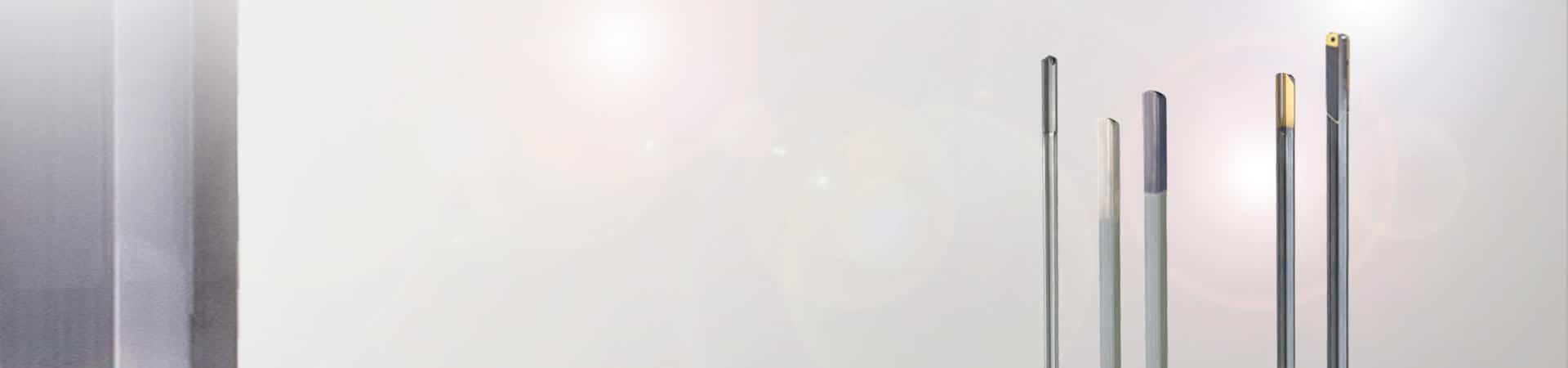
Gun Drills
For every task a suitable gun drill
For a diameter-length-ratio from 15xD one generally refers to gun drilling. Gun drills are for example applied for the machining of camshafts, crankshafts, drive shafts, injectors, drill pipes for oil production, in the medical and the food industry. Dependent on the requirements of the hole, the machine conditions, the batch size and the drilling depth Gühring determines the most economically efficient tool option.
Single-fluted gun drill
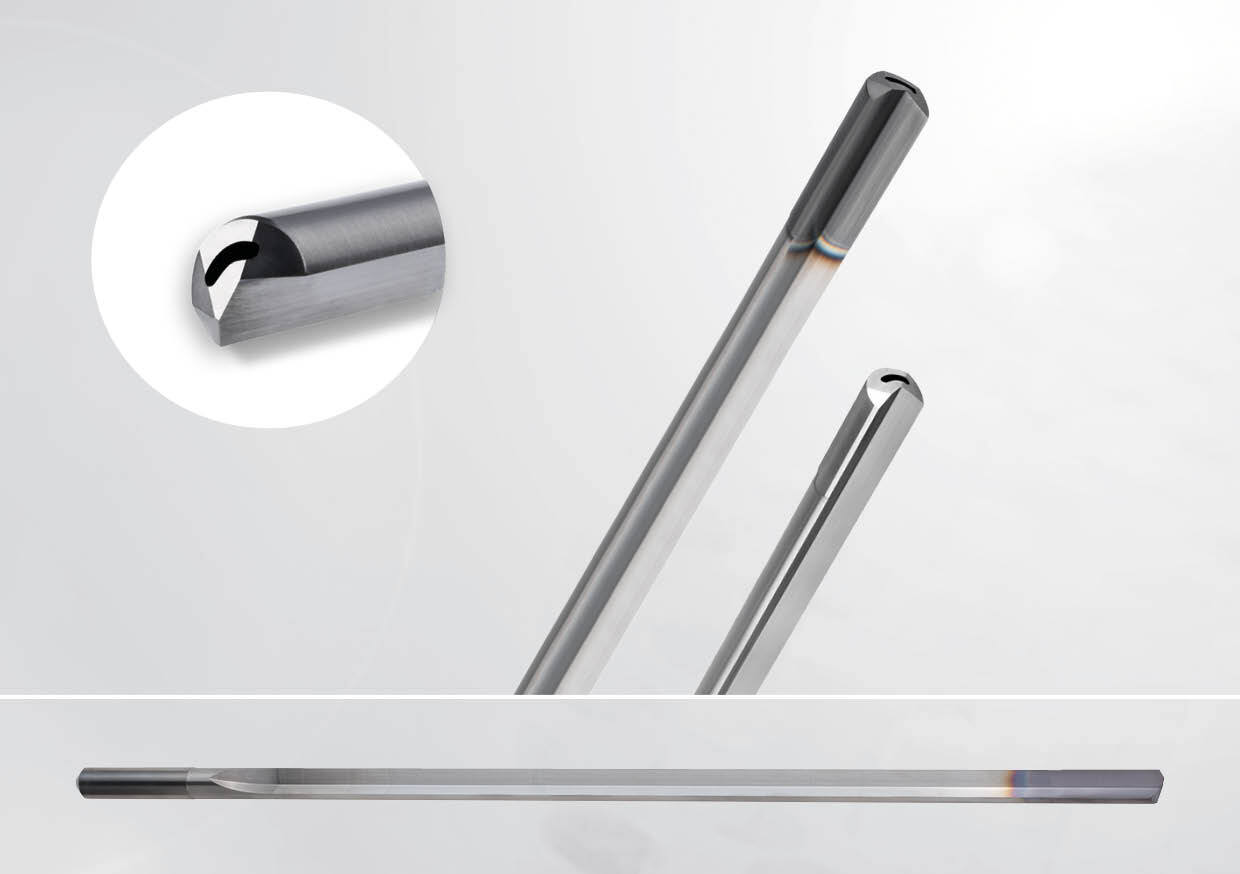
SINGLE-FLUTED GUN DRILL EB 100 MONO: SMALLEST
\ solid carbide single-fluted gun drills
\ single-fluted gun drill especially for close drilling tolerances
\ can be manufactured from 1,000 mm up to 16,000 mm nom.-Ø
\ flute length up to 580 mm
\ up to 80xD with only one tool
\ suitable for MQL applications
\ suitable deep drilling for most materials
\ wide variety even of inch dimensions
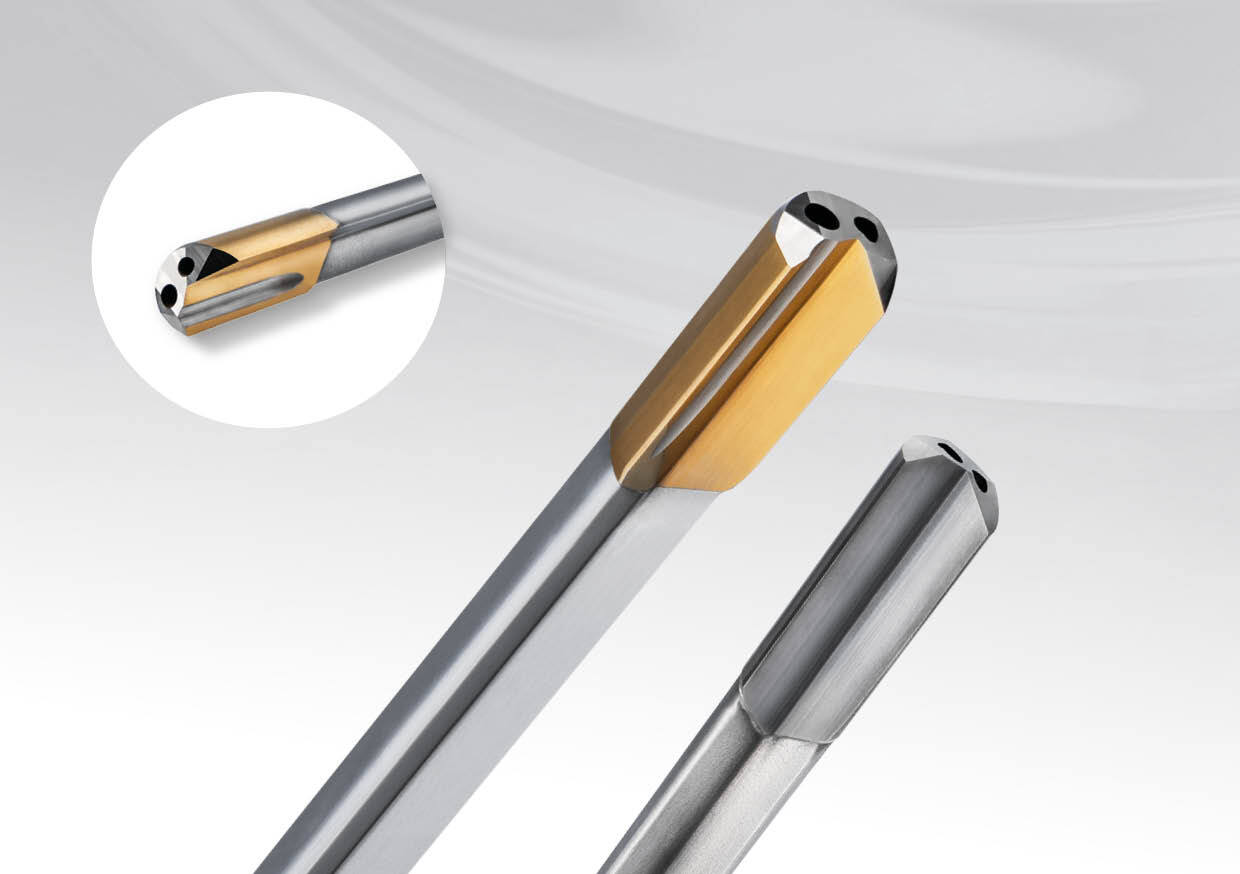
SINGLE-FLUTED GUN DRILL EB 80: CONVENTIONAL
\ single-fluted gun drills with brazed carbide head
\ Total length to 3.600 mm
\ nominal diameter from 2,000 mm to 40,000 mm
\ wide range of options, i.e. ball nosed or step drill
\ suitable for most materials
\ wide range for machining centres and deep drilling machines
\ wide variety of deep drilling even of inch dimensions
\ fast service programme EB 80
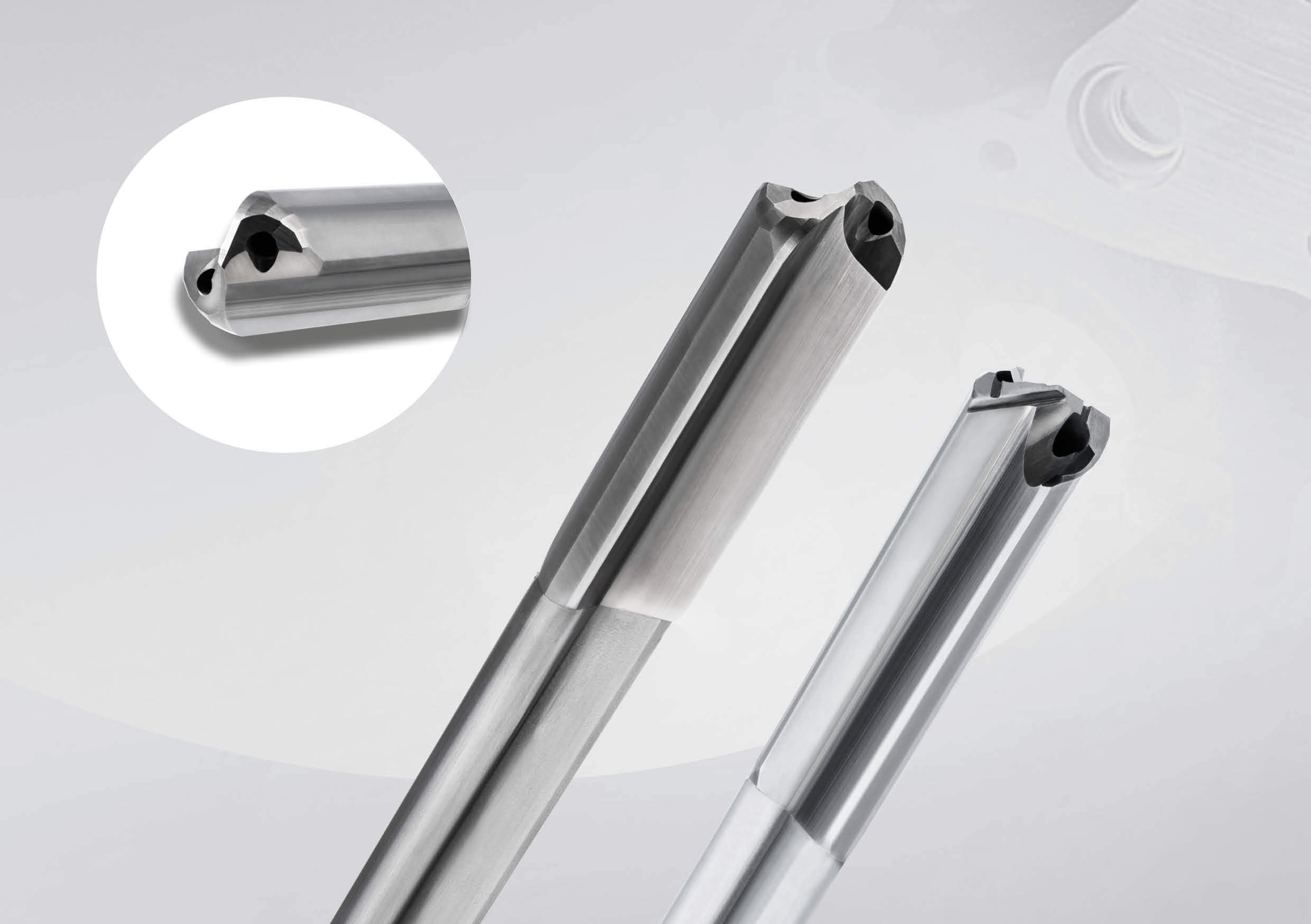
ZB 80 TWO-FLUTED GUN DRILLS: THE SPECIALIST FOR CAST IRON
\ solid carbide two-fluted gun drills
\ total length to 1.000 mm
\ nominal diameter from 6,000 mm to 30,000 mm
\ perfect for machining of cast iron
\ specifically developed carbide grades and cutting edge geometries for innovative deep drilling
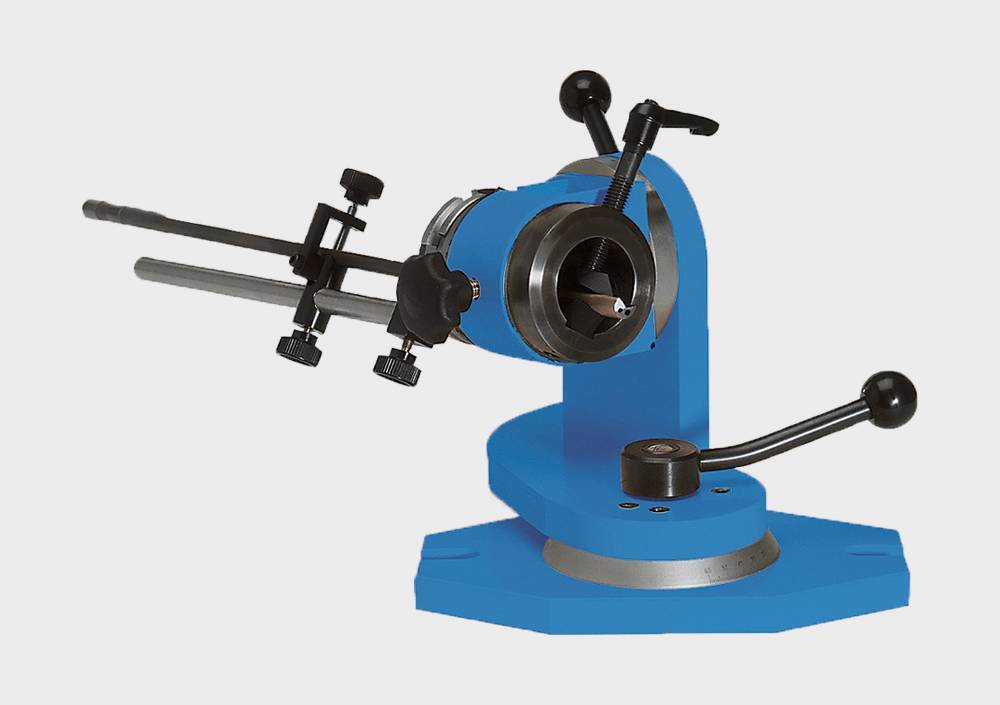
TBV 116: FOR Ø 3 UP TO 32 MM
\ regrinding of single-fluted gun drills, Ø 3 mm up to 32 mm
\ standard and special grinding operations
\ no minimum flute length
\ support device available for long tools
\ universal application on any type of grinding machines
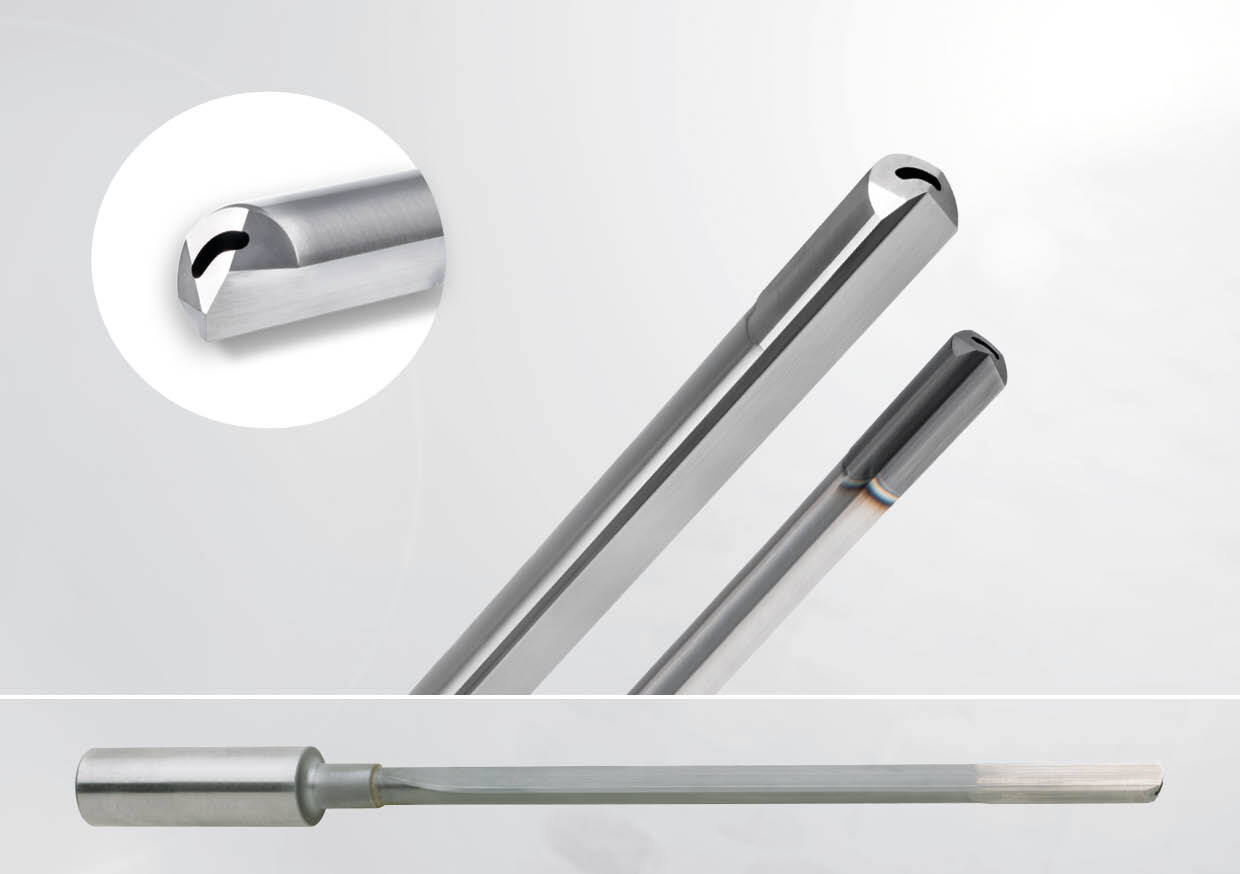
SINGLE-FLUTED GUN DRILL EB 100: SMALLEST
\ single-fluted gun drills in soldered solid carbide for fast deep hole drilling
\ single-fluted gun drills especially for close dilling tolerances
\ can be manufactured from 0,9000 mm up to 16,000 mm nom.-Ø
\ flute length to 580 mm
\ up to 80xD with only one tool
\ suitable for most materials
\ wide variety of deep drilling even of inch dimensions
\ fast service programme EB 100
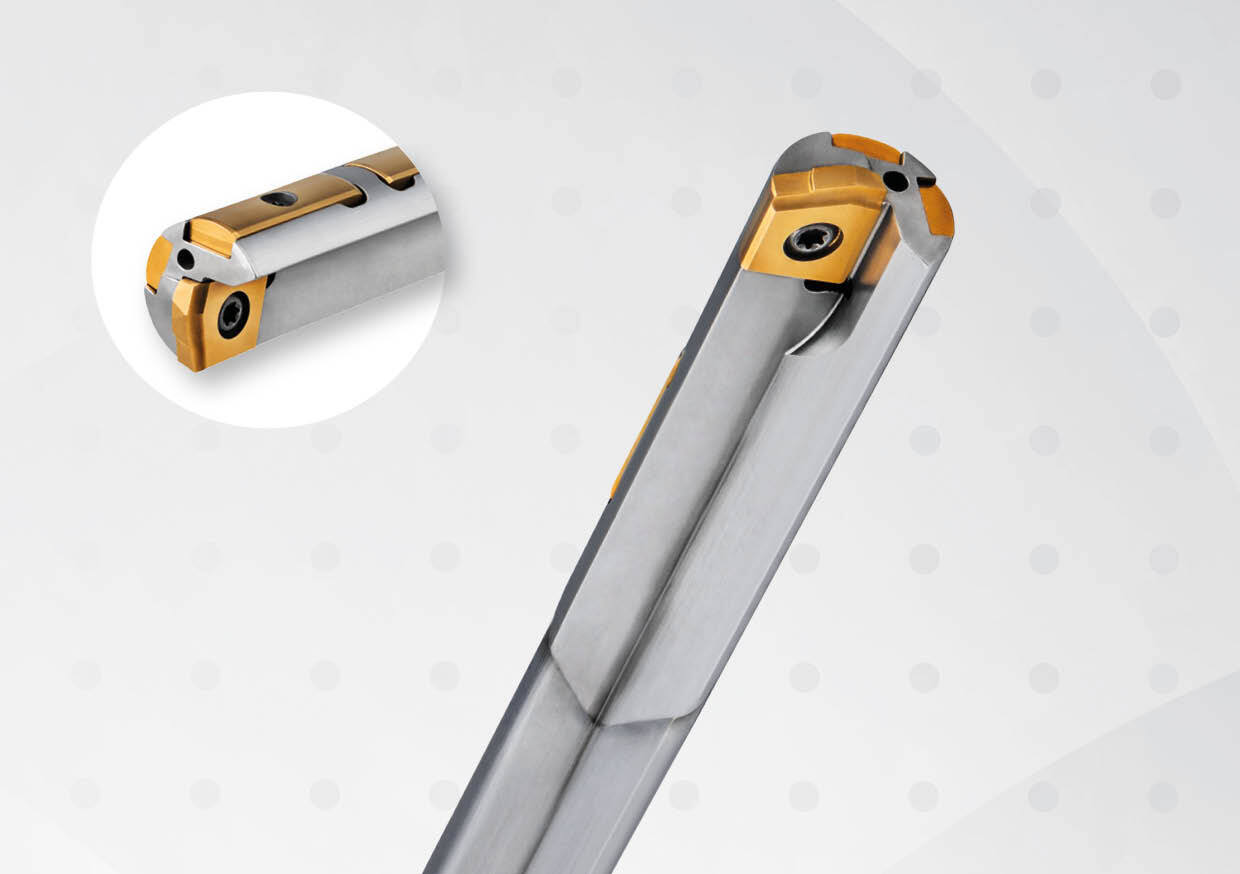
SINGLE-FLUTED GUN DRILL EB 800: FLEXIBLE
\ single-fluted gun drill with indexable inserts and supporting strips
\ total length to 3.600 mm
\ nominal diameter from 12,000 to 52,000 mm
\ convertible by 0,5 mm per basic body range
\ any combination of carbide grades and coatings possible
\ suitable for most materials
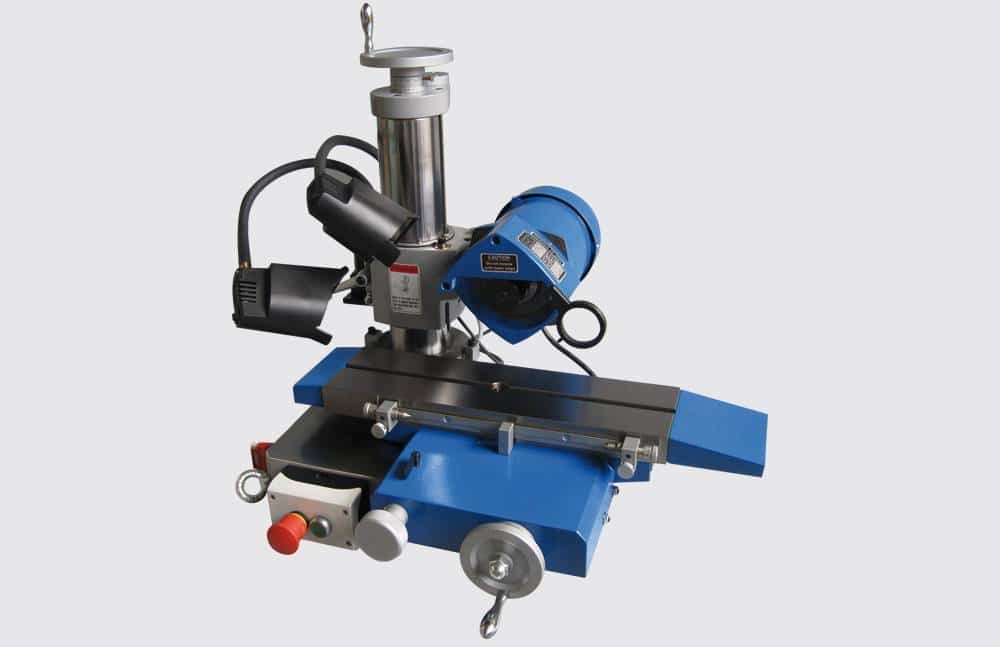
TBM 116: UNIVERSAL MANUAL GRINDING MACHINE
\ extremely compact
\ ideal for regrinding for small and medium quantities of tools with
different diameters and lengths
\ easy mounting of lateral chip breakers on single-fluted gun drill
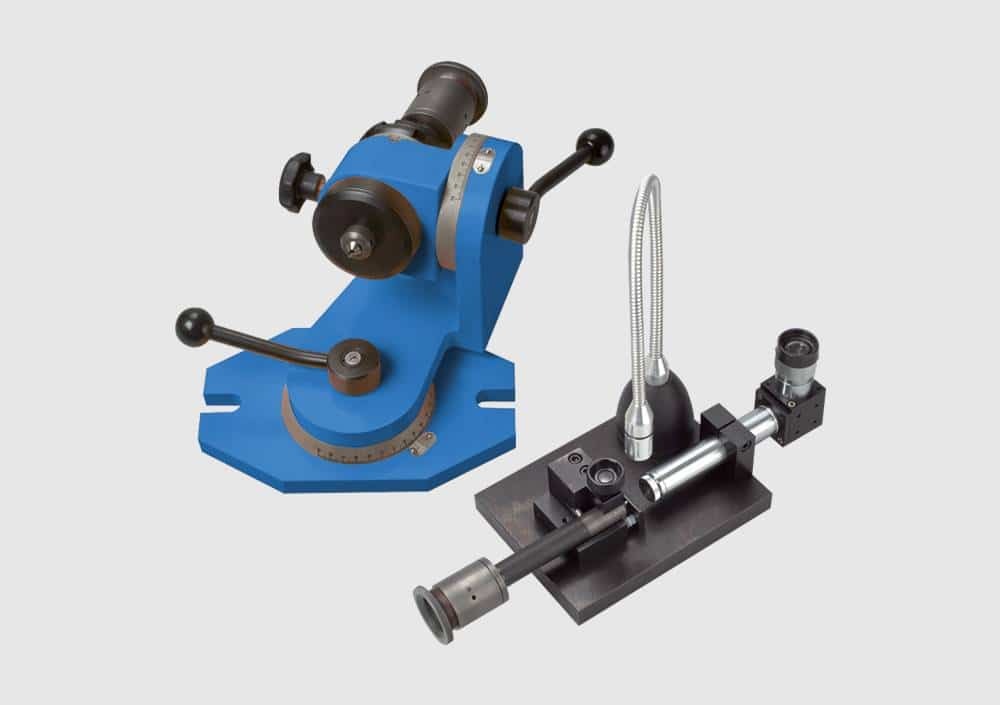
TBV 216: FOR Ø 0,5 UP TO 6 MM
\ grinding device, especially for small-diameter sizes
\ max. length 350 mm
\ easy handling, requiring just four working steps
\ grinding with a 3-axis swivel
\ various grinding angles are possible
Deep hole drilling with solid carbide spiral fluted gun drill
EXCLUSIVE LINE: RT 100 T
With spiral deep hole drills type RT 100 T available as part of an extended ex-stock programme for the drilling depths 15xD, 20xD, 25xD, 30xD and 40xD, the user benefits from maximum feed rates and cutting speeds and therefore benefits from a significant reduction in manufacturing times. Gühring achieves these advantages thanks to the following features:
- Optimised flute cross-section gun drilling
Die spiralisierten Tieflochbohrer verfügen über eine auf die besonderen Anforderungen speziell angepasste Nutgeometrie für einen optimalen Spantransport aus tiefen Bohrungen. - Maximum coolant duct cross-section
To optimally supply the cutting edge with lubricant, the tools possess coolant ducts with maximum cross-section. This ensures an effective lubricant supply to the cutting edge and excellent chip evacuation. - Problem-free chips
The aforementioned factors in combination with the perfectly adapted cutting parameters to suit the application result in chips that are evacuated problem-free even from deep holes. Therefore, chip congestion and the herewith combined jamming of the tool is effectively prevented.
- Wear resistant cutting edges
Thanks to the head coating with Gühring’s A-coating (TiAlN) the heavily stressed cutting edge area is effectively protected against wear. - HA shank for accurate clamping
For clamping with hydraulic chucks from Gühring’s GM 300 programme the RT 100 T ex-stock range is equipped with a HA shank, shank tolerance h6. The combination of RT 100 T and hydraulic chuck guarantees maximum concentricity, extreme clamping force, minimal imbalance and optimal economic efficiency. - Intermediate dimensions & special lengths
In addition to the ex-stock programme ensures Gühring continues to provide RT 100 T as a special tool to customer requirements. We provide intermediate dimensions for the ex-stock range with a maximum drilling depth up to 40 x D / a maximum total length up to 400 mm. - MQL suitable
Thanks to the modification of the shank to the for MQL machining optimised shank end the ex-stock tools are also optimally suited for MQL machining.
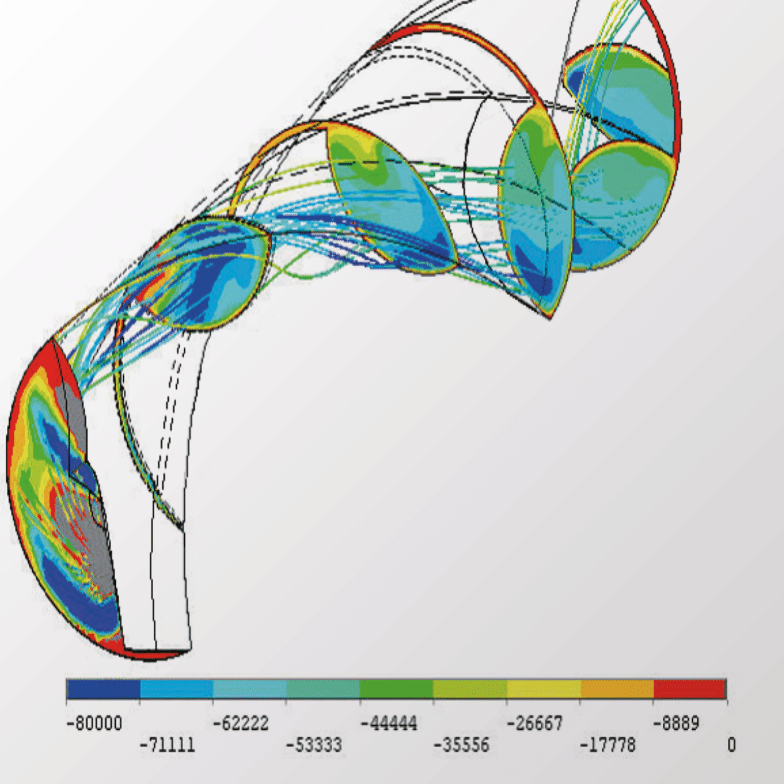
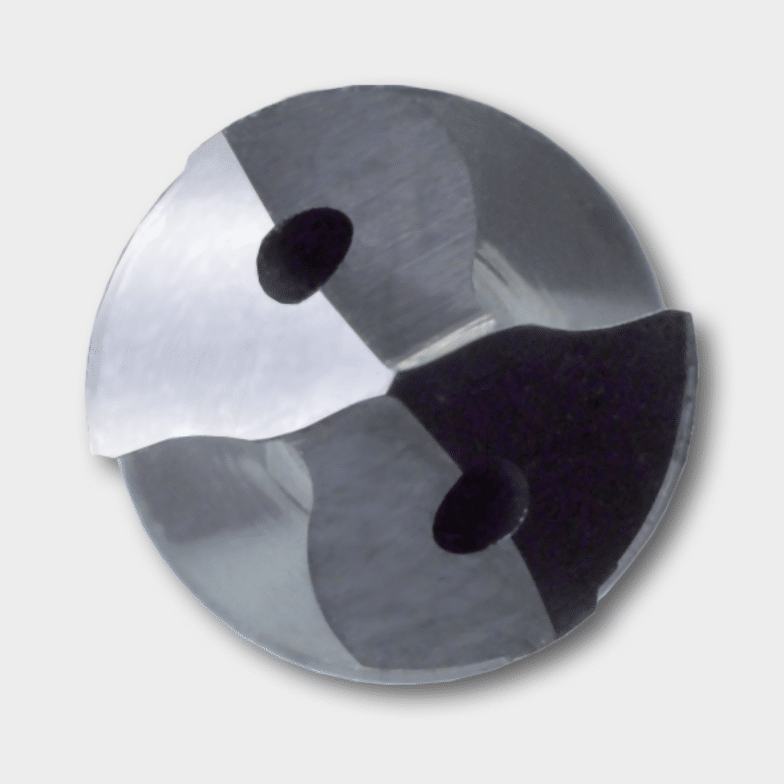
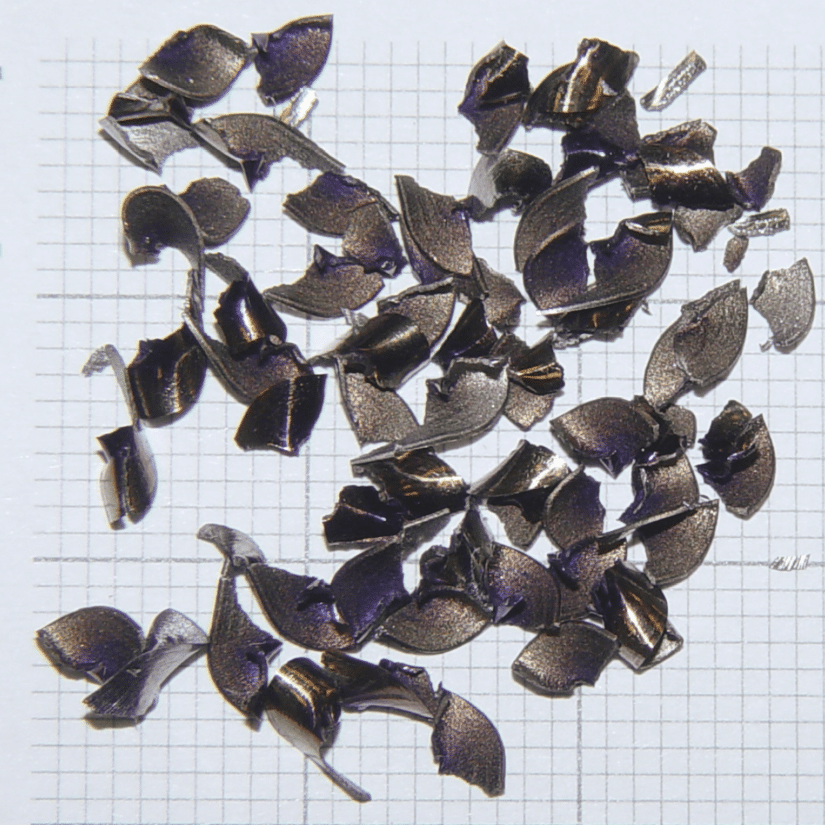
HSS-E-PM deep hole drill: GT 2000
Drilling depths up to 20xD without pecking cycles
- Special deep drilling programme
- Ø 3.00 -12.00 mm
- up to 20xD drilling depth
- new parabolic flute geometry for optimal chip evacuation
- especially suitable for the machining of steel
- The TiAlN-based head coating ensures a high wear resistance of the stressed cutting edge of the tool during heavy machining.

Point grind
Optimal wear resistance and excellent cutting conditions with deep holes thanks to the newly developed point geometry with optimised S web thinning.
Flute form
A specially developed parabolic flute form with optimised surface finish quality ensures optimal chip formation and chip evacuation.
High surface finish quality
Thanks to the bright flute with high surface finish quality the chips are optimally evacuated.
CLAMPING SYSTEM
Precision is setting-up matter
DRILLING TOOLS
Sophisticated drill technology
AVIATION
Highest requirement for tool & process