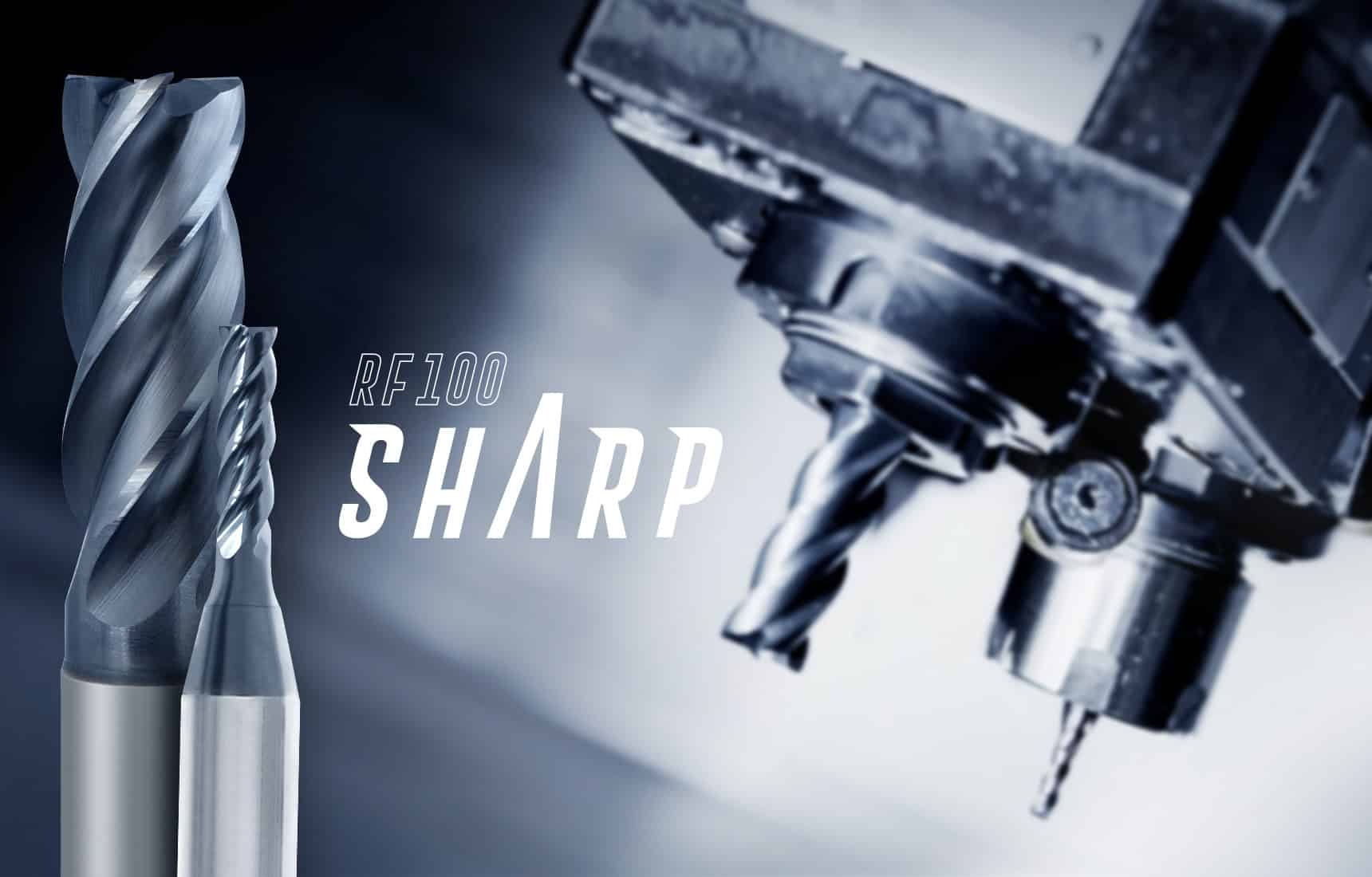
In autumn 2021, Gühring presented an innovation in milling. A solid carbide high-performance milling cutter that promises full flexibility and is currently the sharpest milling cutter on the market with its higher rake angle: The RF 100 Sharp. Since then, the tool has been the cause of success stories around the world: Although the materials, applications and machining conditions were always different, the end result was always a satisfied customer who was able to generate a real advantage for their operations. We have summarised five such success stories here.
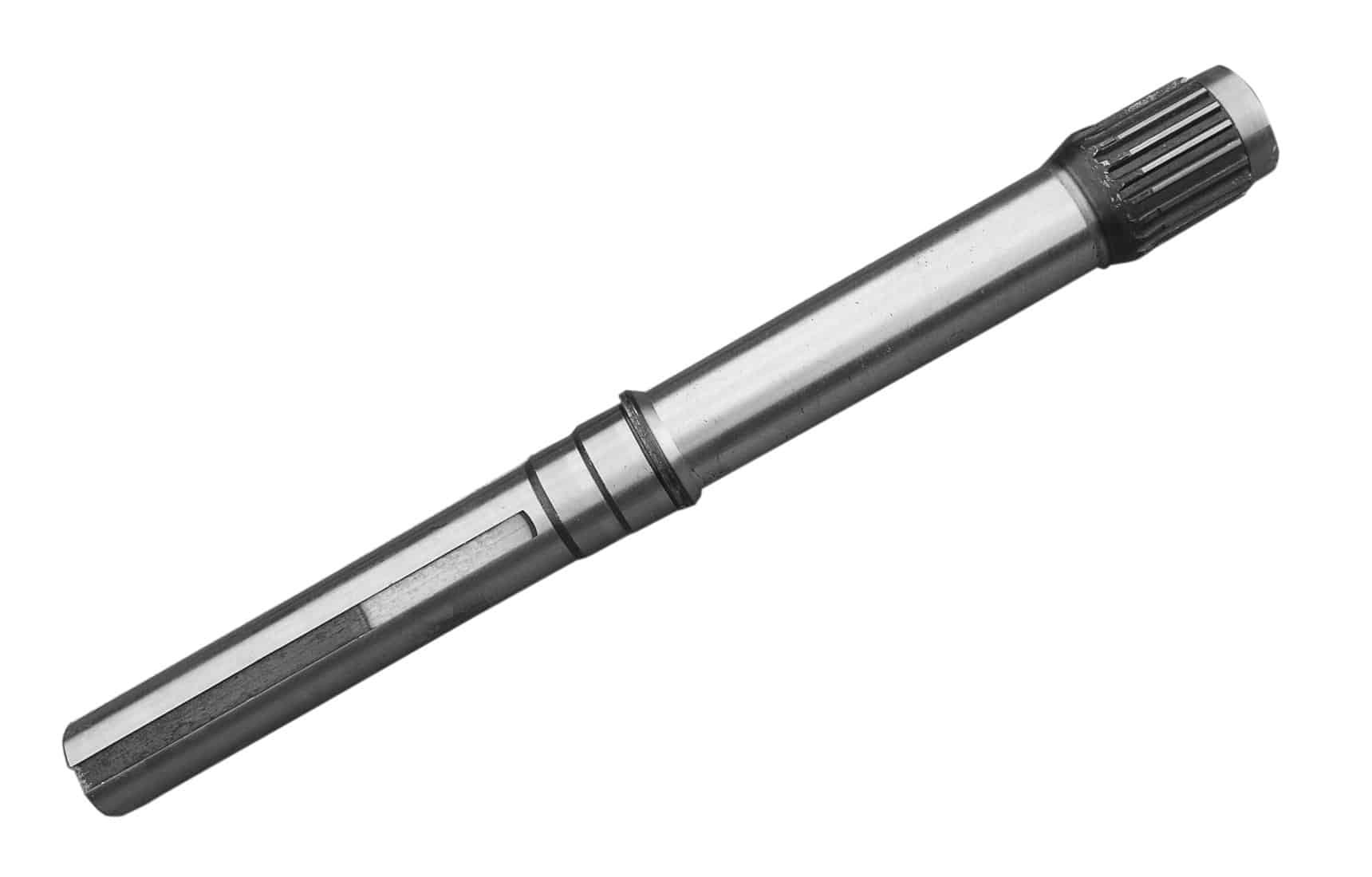
-50 % machining time
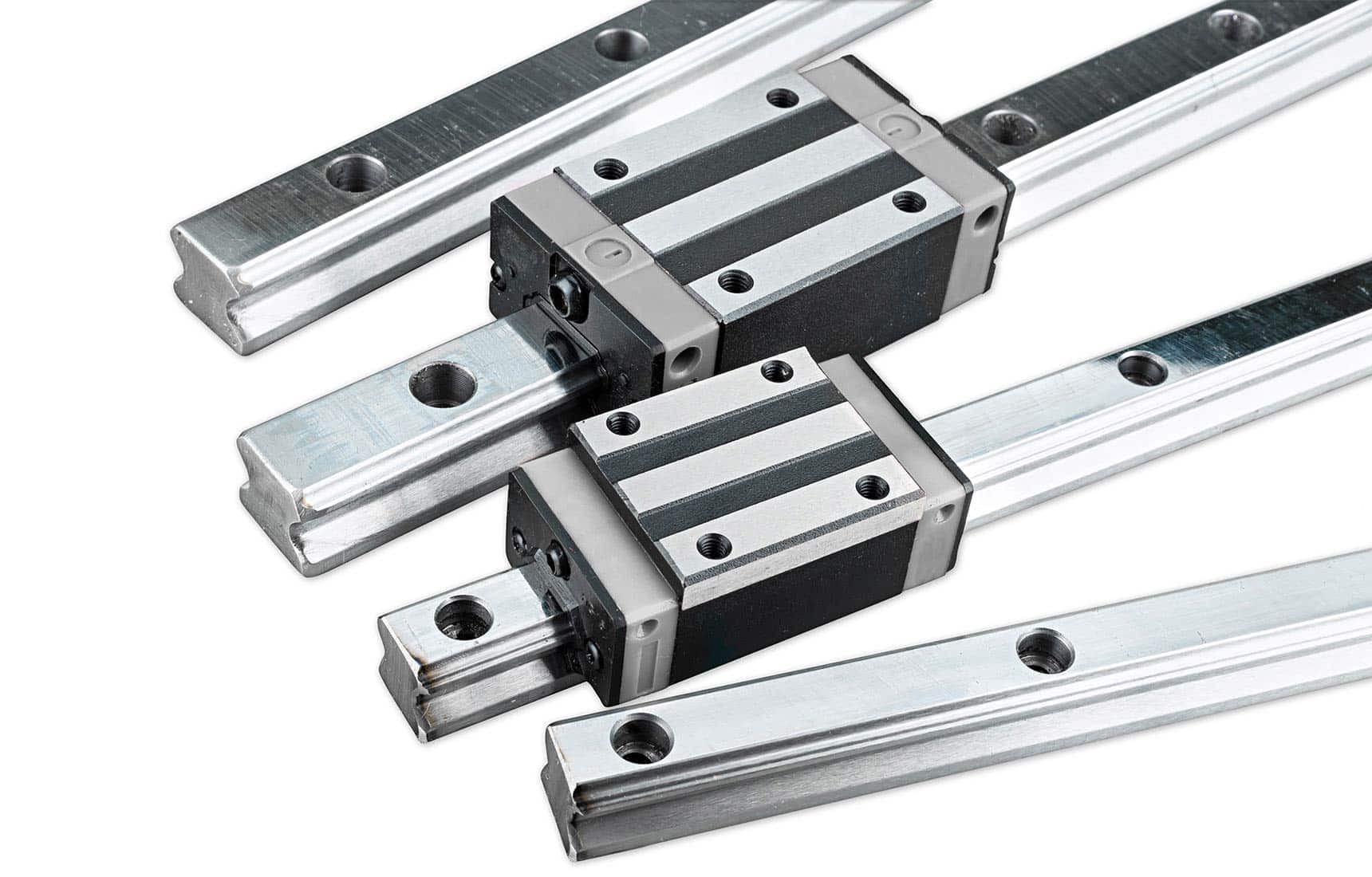
124 kg of steel machined
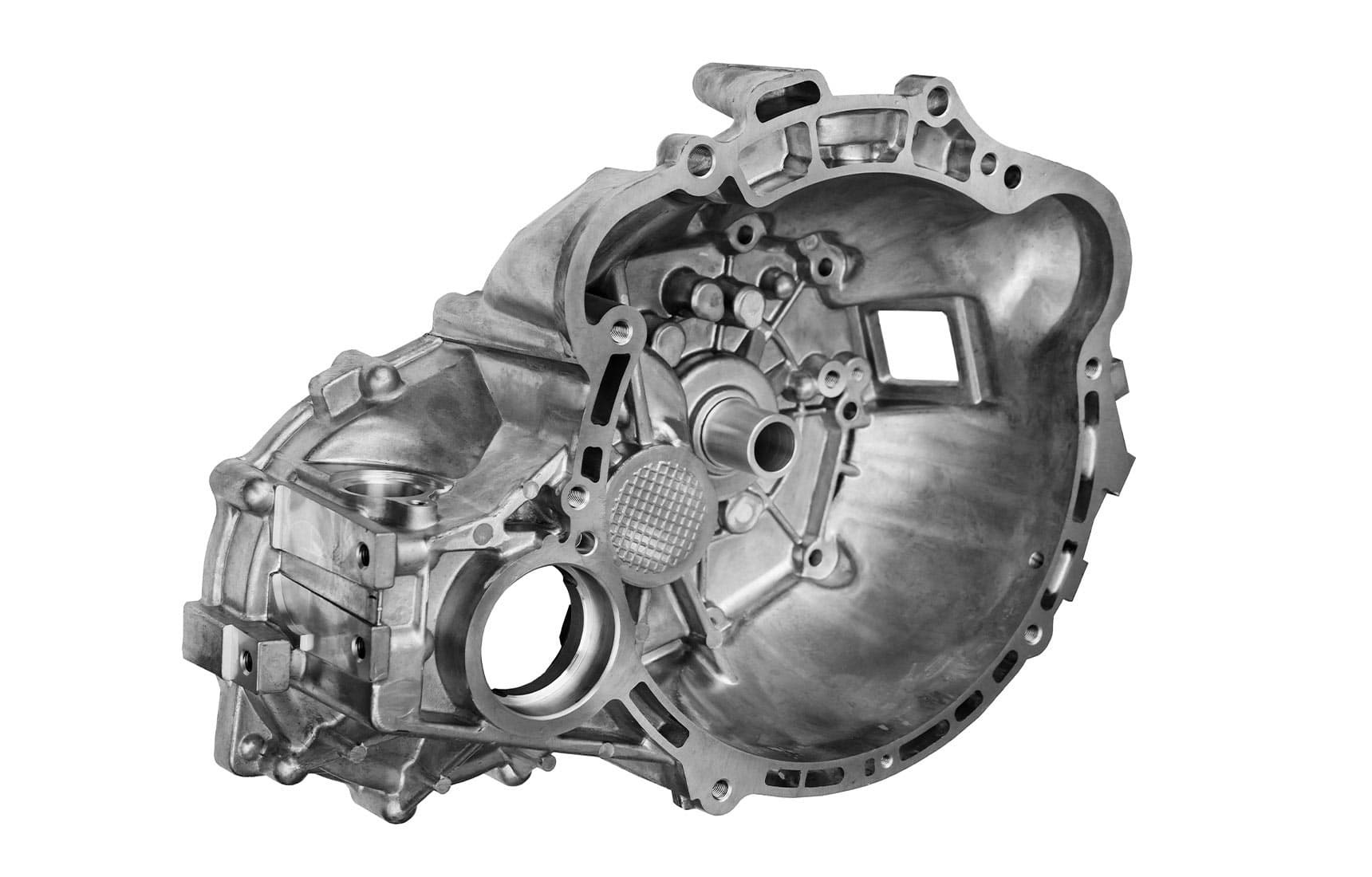
400 min. milling cast iron
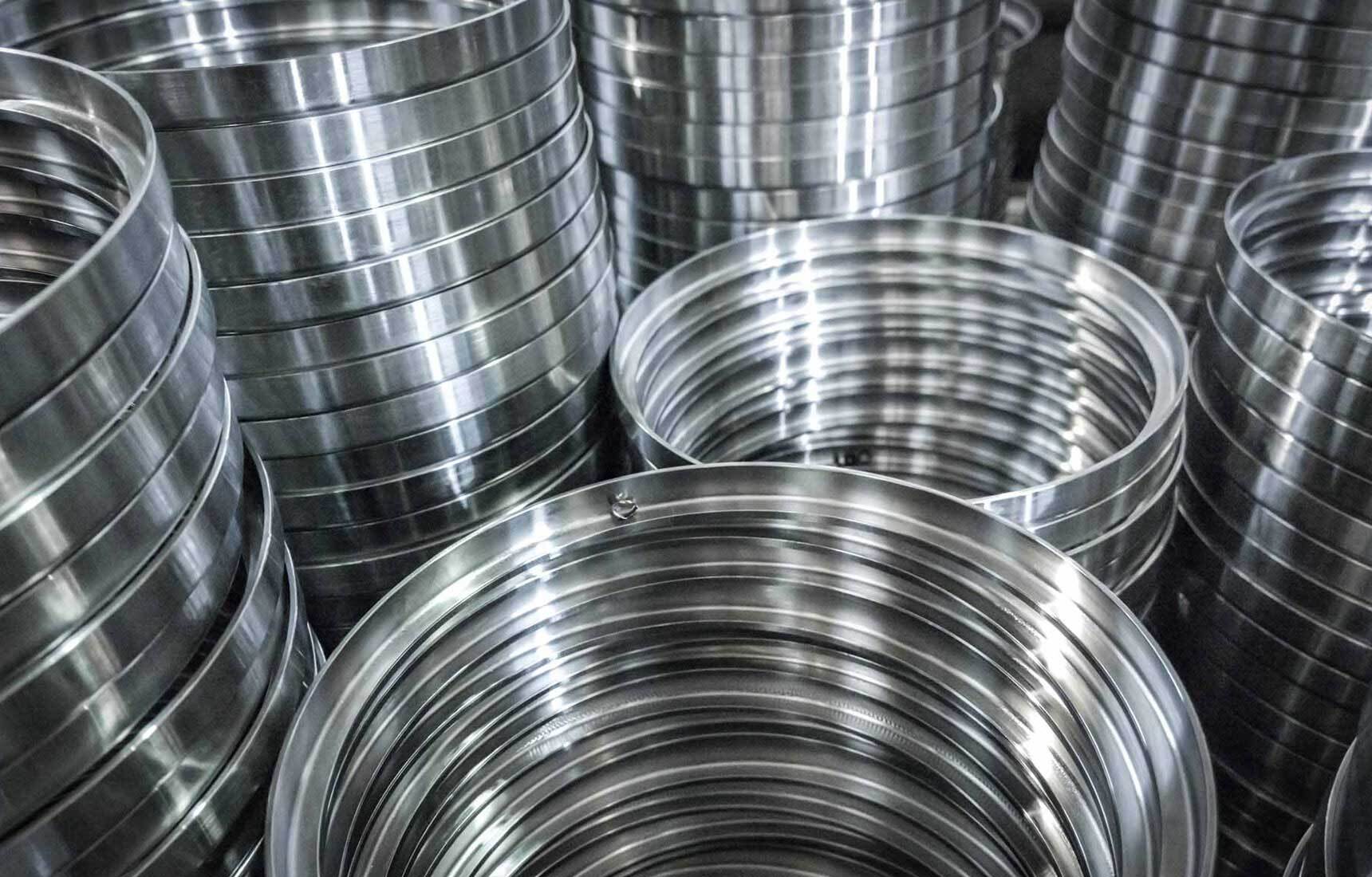
285 %
longer tool life
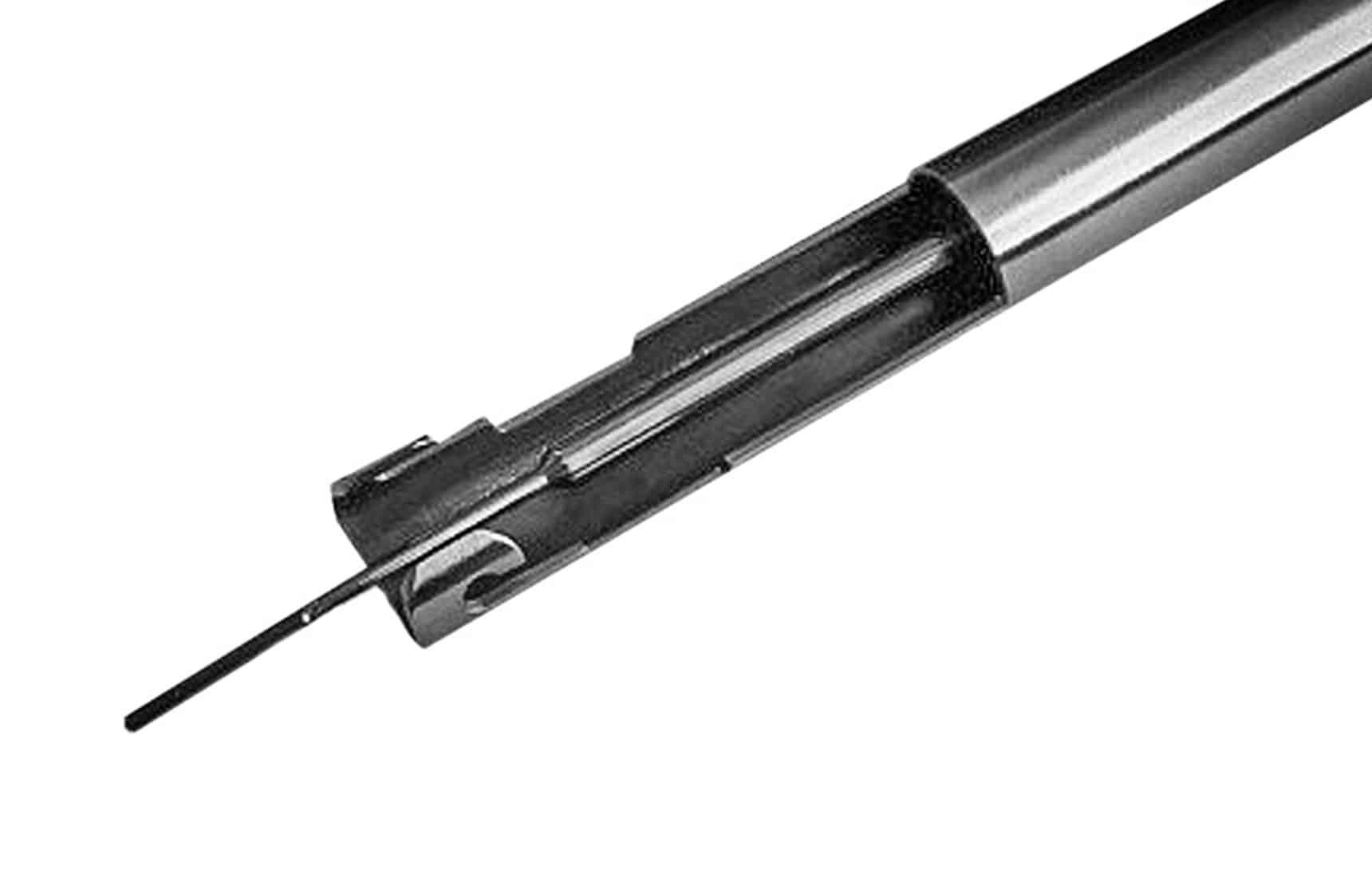
-14 tools
per week
Application 1: 50 % less machining time with double the tool life
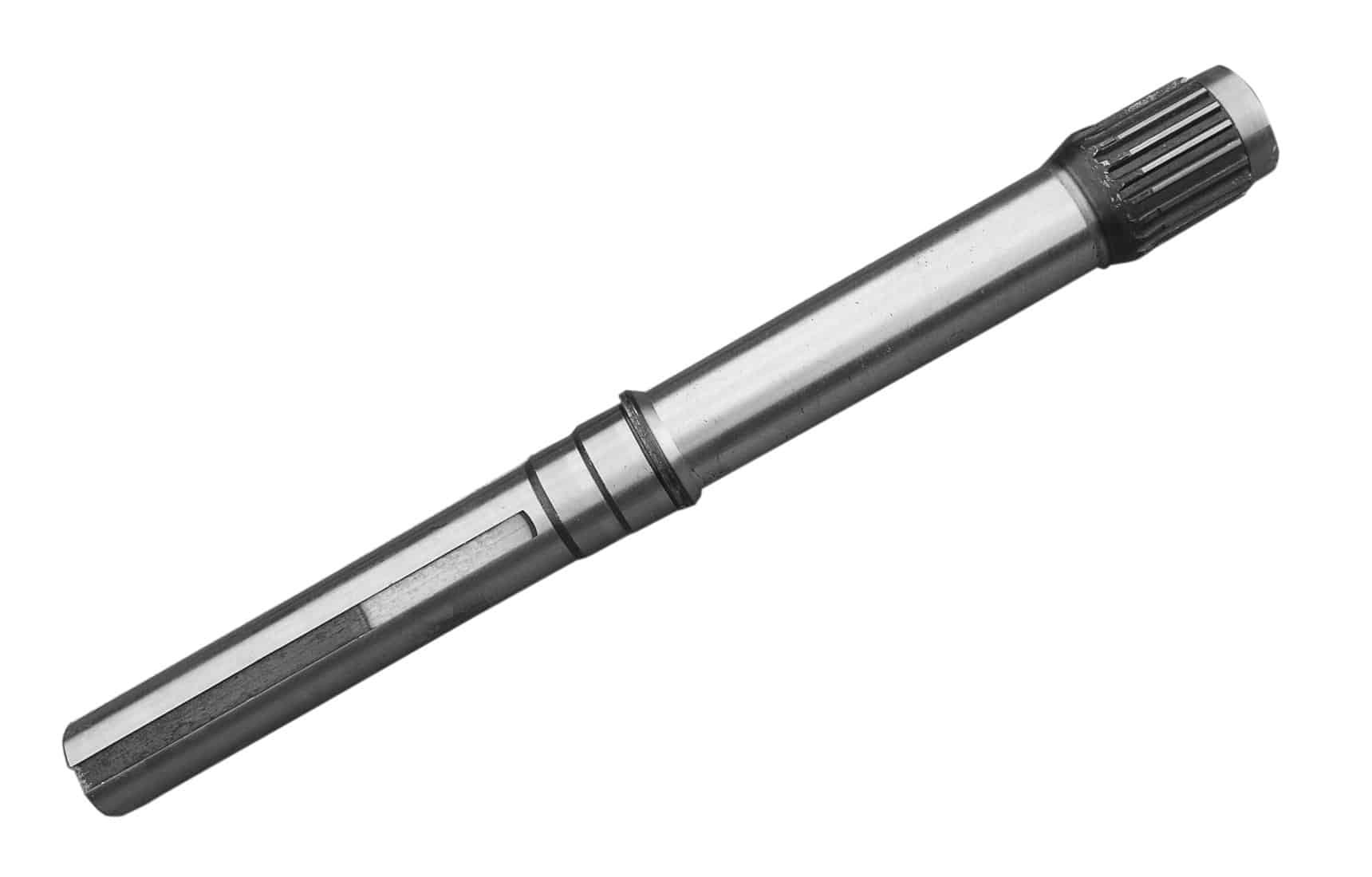
A Korean company manufactures parts for the automotive industry. However, when roughing a shank for a steel drive shaft (15CrMo5), its previous tool concept had reached its limits, as the high machining times were uneconomical over the long term.
Gühring was able to offer a significantly more efficient process here. The Gühring experts advised the customer to use the new RF 100 Sharp with a diameter of 6 mm (art. no.: 6478) with the GTC strategy (Gühring Trochoidal Cutting). This state-of-the-art milling strategy relies on a high cutting depth (ap) as well as the lowest possible and consistent tool wrap due to a reduced radial infeed rate (ae). The result is a significantly faster cutting speed, which enables high material removal rates to be achieved. The particularly easy-cutting RF 100 Sharp high-performance milling cutter unleashes its full potential here and at the same time its AlCrN coating offers a high level of wear protection – even with aggressive cutting parameters. This also pays off in the aforementioned example: Thanks to the tool change, the customer has been able to reduce its machining time by 50 percent. At the same time, the milling cutter achieves double the tool life: With one tool, 20 parts are now produced instead of the previous 10.
GÜHRING | COMPETITOR |
Vc = 89 m/min | Vc = 72 m/min |
Fz = 0,08 mm/z | Fz = 0,046 mm/z |
Ae = 0,5 mm | Ae = 0,5 mm |
Ap = 4 mm | Ap = 4 mm |
n = 4.722 U/min | n = 3.820 U/min |
Vf = 1.511 mm/min | Vf = 703 mm/min |
Application 2: 124 kg machining volume – despite unstable conditions
When machining steel supporting strips (16MnCr5), a contract manufacturer faced a challenge: The very long machine components could not be clamped stably. In addition, the deep slots required a tool with a long projection length. However, both can lead to vibrations during milling, which promote rapid tool wear.
Gühring was able to offer a significantly more efficient process here. The Gühring experts advised the customer to use the new RF 100 Sharp with a diameter of 6 mm (art. no.: 6478) with the GTC strategy (Gühring Trochoidal Cutting). This state-of-the-art milling strategy relies on a high cutting depth (ap) as well as the lowest possible and consistent tool wrap due to a reduced radial infeed rate (ae). The result is a significantly faster cutting speed, which enables high material removal rates to be achieved. The particularly easy-cutting RF 100 Sharp high-performance milling cutter unleashes its full potential here and at the same time its AlCrN coating offers a high level of wear protection – even with aggressive cutting parameters. This also pays off in the aforementioned example: Thanks to the tool change, the customer has been able to reduce its machining time by 50 percent. At the same time, the milling cutter achieves double the tool life: With one tool, 20 parts are now produced instead of the previous 10.
Vc = 140 m/min |
Fz = 0,055 mm/z |
Ae = 2,5 mm |
Ap = 18 mm |
n = 2785 U/min |
Vf = 613 mm/min |
Q = 25,57 cm³/min |
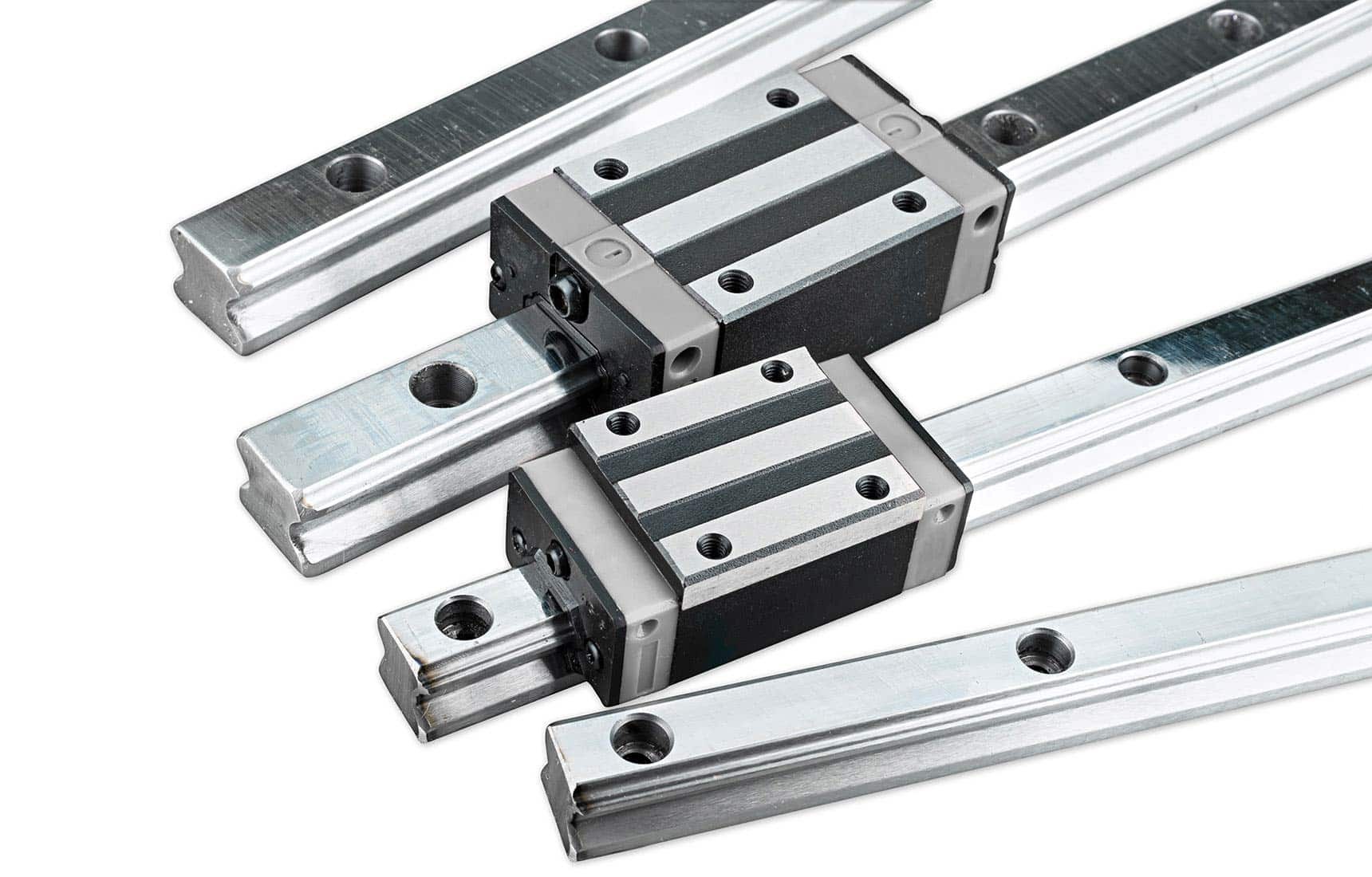
Application 3: 400 minutes of milling and no end in sight
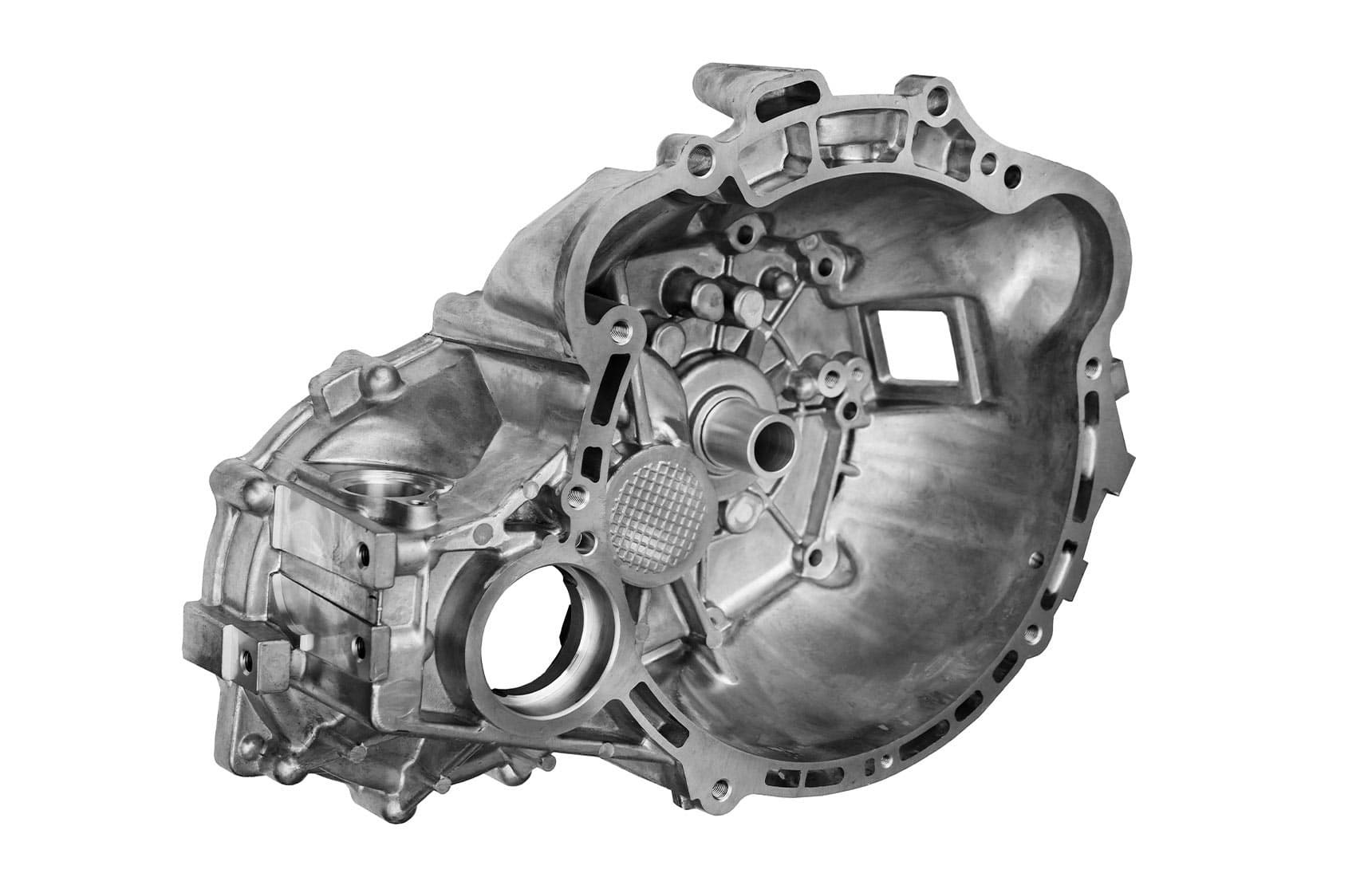
Covers for gearboxes are manufactured in a medium-sized company. The gearbox housing covers are made from GGG40 with a tensile strength of 400 N/mm². The material is typical for powertrain components. However, due to its high degree of toughness, typical casting wear quickly occurs.
The RF 100 Sharp mills easily through all materials with a tensile strength of 300 to 900 N/mm². A very sharp rake angle of 12° is ideal for reducing cutting pressure and cutting forces. To manufacture the gearbox cover, the customer used the milling cutter with a diameter of 16 mm (art. no.: 6479) with the GTC strategy. The result is a high machining volume of 128.95 cm³/min. The tool lives are also impressive: After 400 minutes of use, the tool is still good to use.
Vc = 200 m/min |
Fz = 0,125 mm/z |
Ae = 2,4 mm |
Ap = 27 mm |
n = 3979 U/min |
Vf = 1990 mm/min |
Application 4: 285 % longer tool life than the competition
A customer from Korea manufactures particularly thin-walled support rings made of quenched and tempered steel (C45E). However, tool wear was too high when roughing these components, as the interface of a competitor’s modular tool proved to be unstable.
This was where the four-fluted version of the RF 100 Sharp with a diameter of 20 mm (art. no.: 6478) came in. The monolithic, easy-cutting tool exhibits high stability during milling, which is further reinforced by its particularly tough carbide material. As a result, the Gühring tool achieved a 285 % longer tool life in Korea than the competitor’s modular six-fluted cutter: Instead of 70, as many as 200 components can be produced with the new solid carbide milling cutter.
Number of teeth: Z4 | Number of theeth: Z6 |
Vc = 100 m/min | Vc = 100 m/min |
Fz = 0,105 mm/z | Fz = 0,07 mm/z |
Ae = 1,6 mm | Ae = 1,6 mm |
Ap = 18 mm | Ap = 18 mm |
n = 1591 U/min | n = 1591 U/min |
Vf = 668 mm/min | Vf = 668 mm/min |
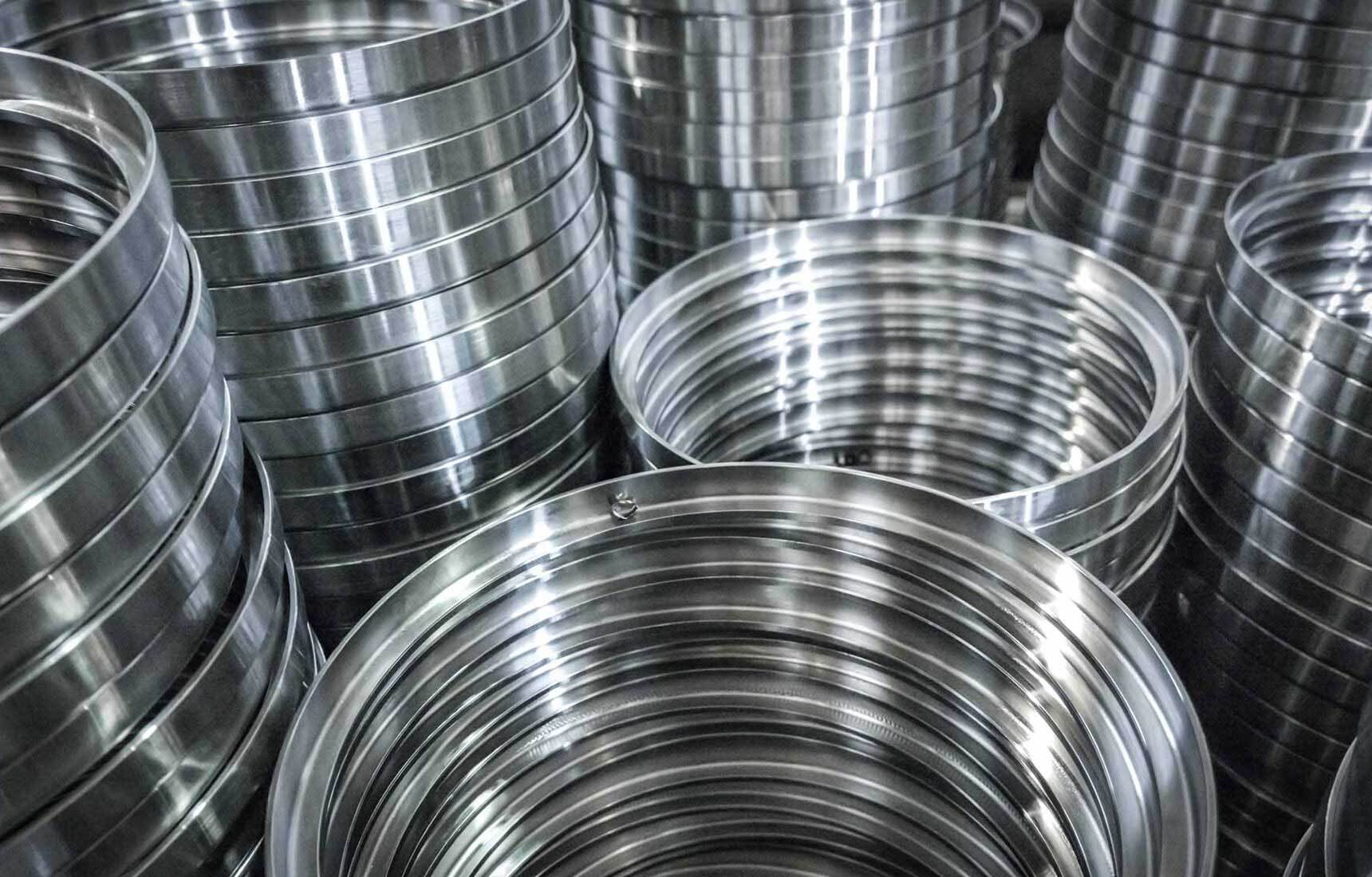
Application 5: Save 14 tools per week when machining titanium
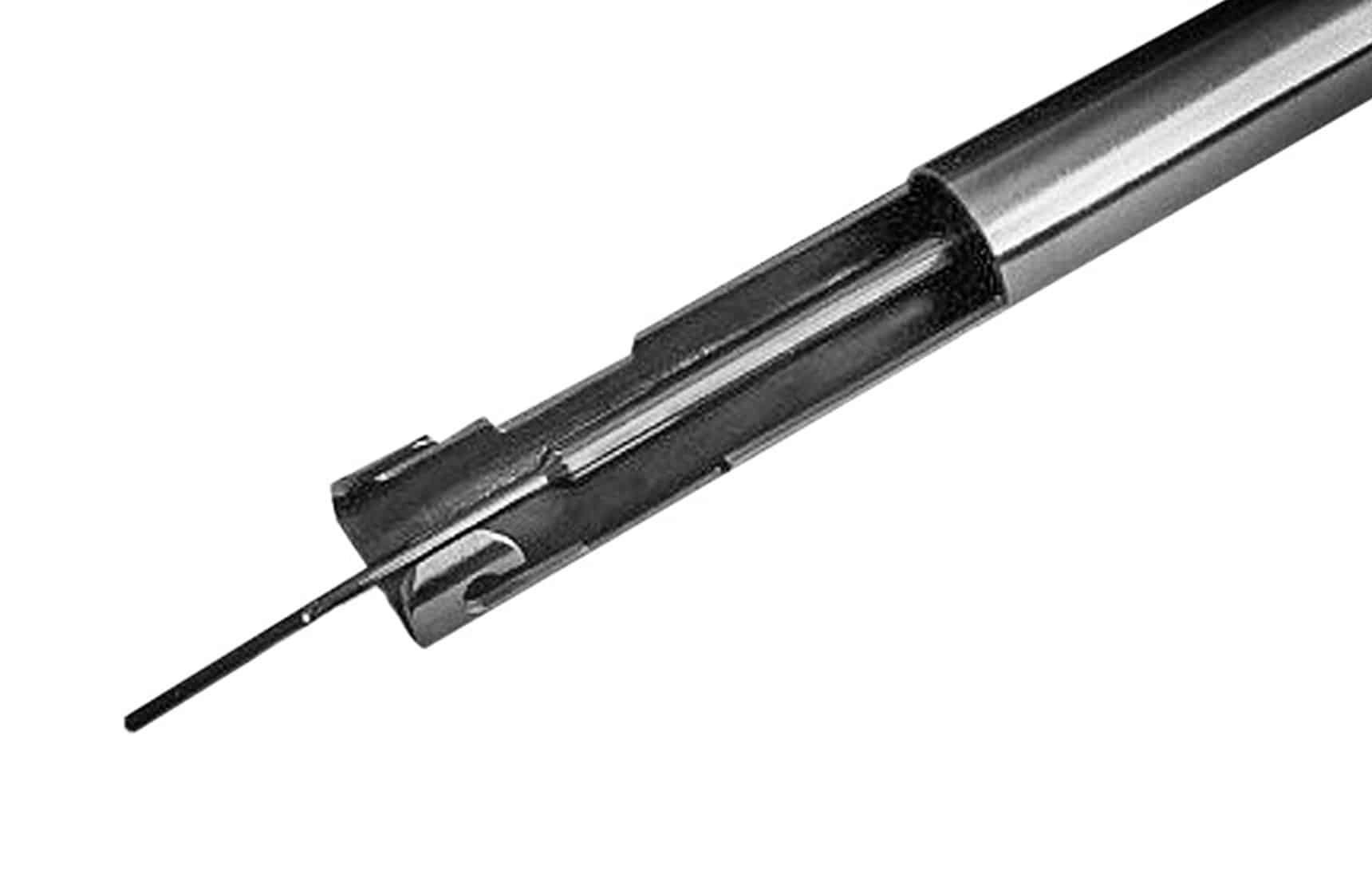
A customer from Korea manufactures particularly thin-walled support rings made of quenched and tempered steel (C45E). However, tool wear was too high when roughing these components, as the interface of a competitor’s modular tool proved to be unstable.
This was where the four-fluted version of the RF 100 Sharp with a diameter of 20 mm (art. no.: 6478) came in. The monolithic, easy-cutting tool exhibits high stability during milling, which is further reinforced by its particularly tough carbide material. As a result, the Gühring tool achieved a 285 % longer tool life in Korea than the competitor’s modular six-fluted cutter: Instead of 70, as many as 200 components can be produced with the new solid carbide milling cutter.
Vc = 58 m/min | Vc = 58 m/min |
Fz = 0,0066 mm/z | Fz = 0,0066 mm/z |
Ae = 2 mm | Ae = 2 mm |
Ap = 4 mm | Ap = 4 mm |
n = 9.231 U/min | n = 9.231 U/min |
Vf = 244 mm/min | Vf = 244 mm/min |
To be continued!
Every two weeks, we will present a new component that our customers have successfully processed with the RF 100 Sharp. Don’t want to miss anything? Then sign up for our newsletter here.
Have we raised your interest?
Then arrange your personal consultation now.
Technical advice and support are also available quickly and directly via our service hotline 00800 2607 2607
We can also be reached on WhatsApp: +49 172 658 53 53. Save the number!
Das könnte Sie auch interessieren:
Modular drills: Their advantages and how you can benefit from them
Modular drilling systems such as the BT 800 from Gühring offer full performance at lower costs. Thanks to interchangeable drill heads, you save time, storage space and money – ideal for flexible applications with the highest demands on cost-effectiveness.
Threads for giants: Crane manufacturer relies on modular fluteless tap for blind holes
An innovation – the new modular fluteless tap from Gühring – has made it possible to solve deep-seated challenges in the production of blind hole threads at Karl Georg and to raise process reliability to a new level.
30% more tool life: With this parting off plate you achieve maximum performance in high-grade steel
30% more tool life when parting off: The new 2 mm parting off plate from Gühring’s System 222 impresses with excellent chip control, high process reliability and a perfect surface finish on ISO-M materials such as high-grade steel.
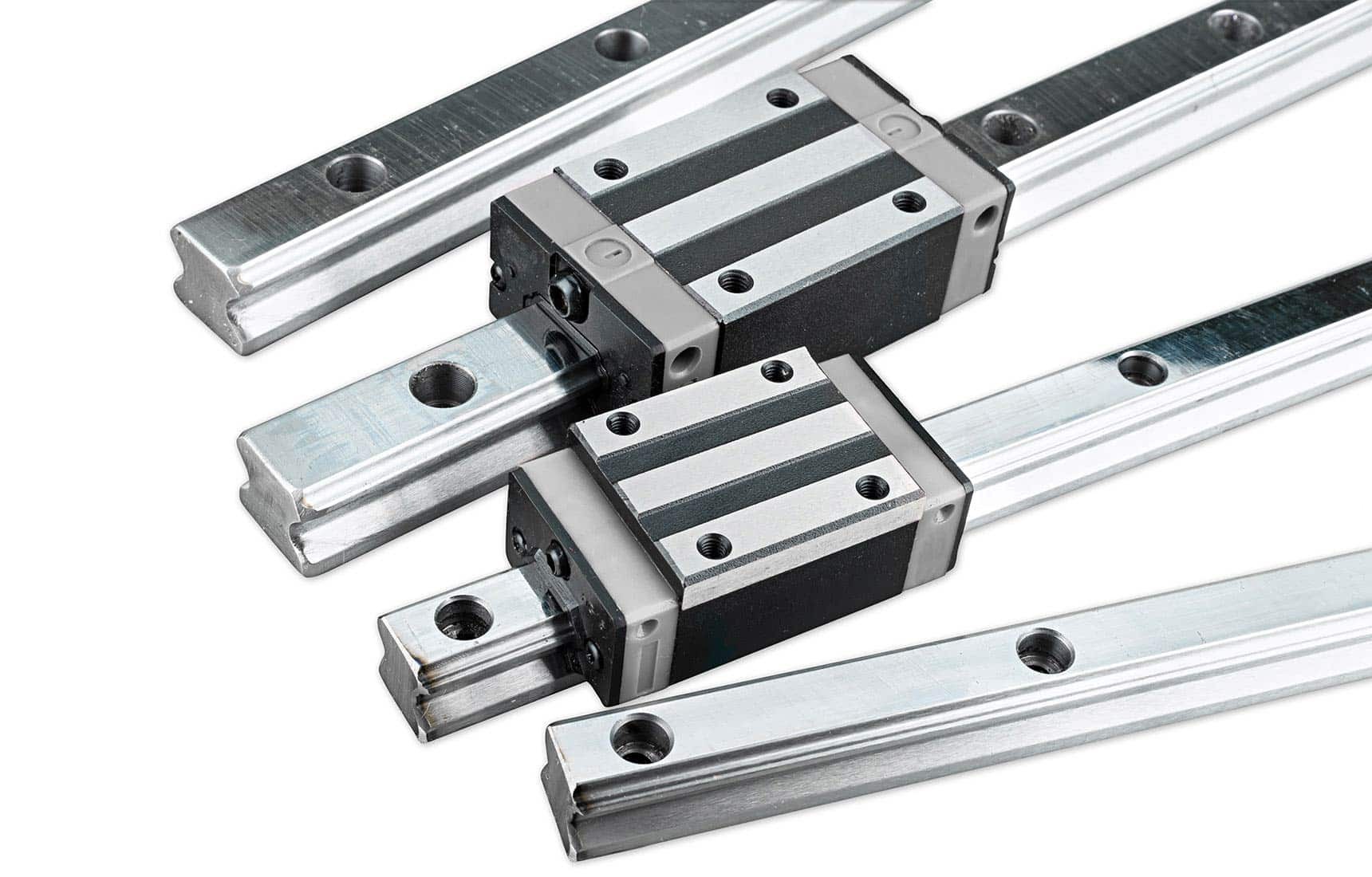