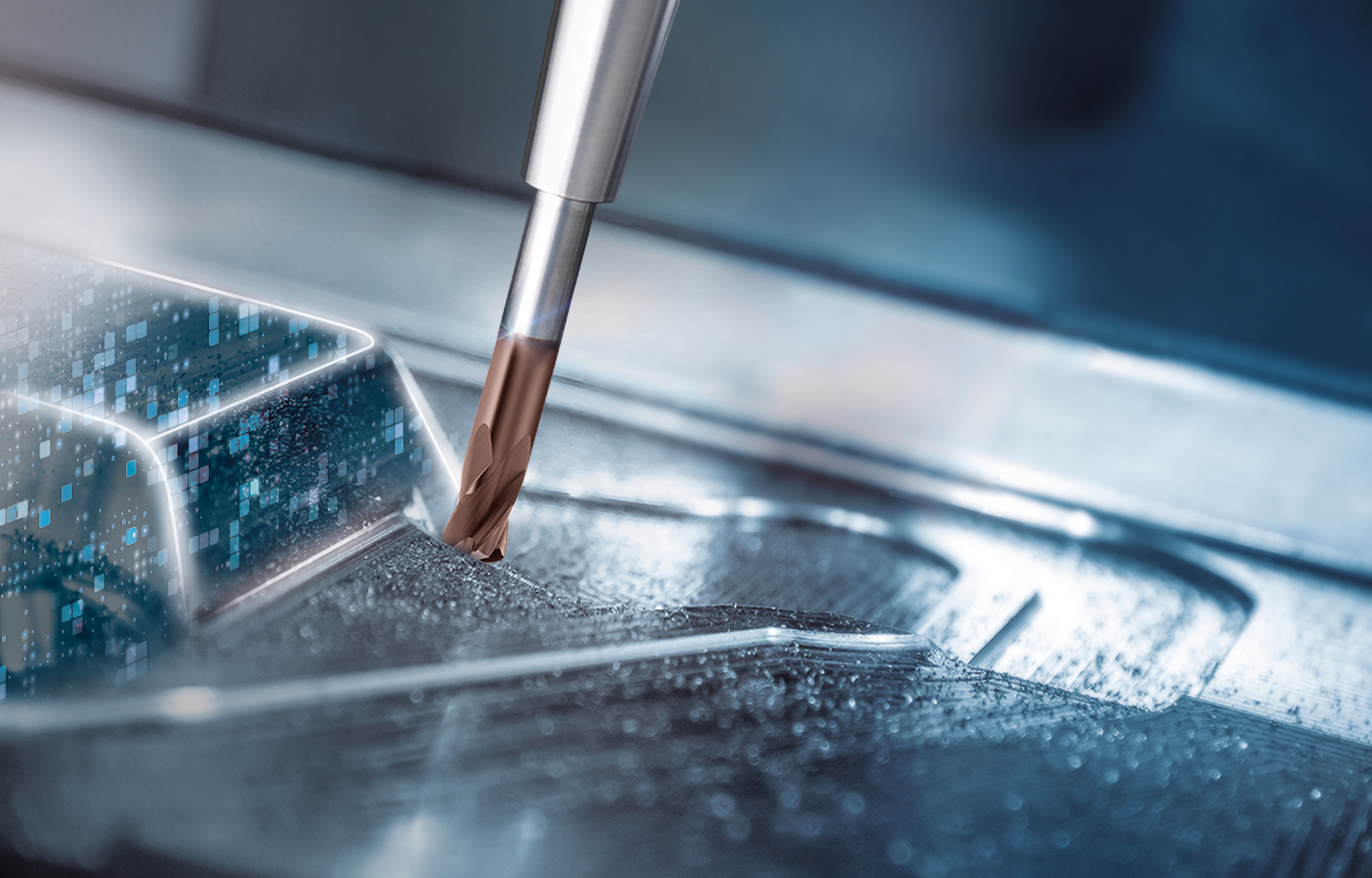
Tools for punching sheet metal have to withstand a lot. Hago Feinwerktechnik GmbH therefore uses materials of up to 66 HRC in its own toolmaking facilities. In order to incorporate threads and contours into these materials, the company relies on cutting tools with complete process reliability. Here, two Gühring tools not only impress with low wear, but also with considerable cost savings – a real competitive advantage for Hago.
Almost no other sector has to deal with as much cost and competitive pressure as mould and die. Paul Preiser, who is in charge of component production at Hago Feinwerktechnik, is well aware of this: “We are always interested in alternative solutions and try to be involved at an early stage in new technologies in order to secure a competitive advantage for the company.” Like about 50% of companies in the field of mould and die, Hago deals with sheet metal processing. Based in Küssaberg (Waldshut district), the company produces sheet metal parts for the automotive industry using punching technology.
When Paul Preiser took over his department a few years ago, he noticed that there were huge costs in the field of cutting tools. His first step: To get things in order. “I was looking for a way to bring a more systematic approach to the tool management field,” he recalls. He then came across some tool management cabinets from Gühring at another local company.
Today, three of these tool cabinets ensure that all cutting tools are organised, locked and stored in their drawers with controlled dispensing. But that was just the beginning. He then started to analyse the cutting tools: “Where can we make improvements? What tools can we do without?” For him, it was clear what was need ed: He wanted Hago to use tools that were specially made for mould and die.
Hardly any wear, no matter how hard
Punching tools are subject to high requirements as they are used on presses with a pressing force of up to 1200 tonnes and must guarantee reliable, stable and reproducible processes. Hago therefore relies on steels with degrees of hardness between 56 and 66 HRC (e.g. cold work steel 1.2379 and powder steel). However, it was precisely this variety of materials that posed difficulties for the employees in the toolmaking department. For example, a competitor’s thread milling cutter performed well in one material, but on an alloy with 66 HRC it eroded the teeth away – literally. After just four threads, the gauge was no longer accurate.
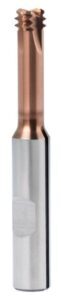
This is where Gühring and its micro thread milling cutter came in: Its coating is specially developed for hard machining in mould and die. This was reflected in the tool life in particular: The Gühring thread milling cutter created twelve threads instead of just three. As a result, Hago saves three times as much on tool costs: Firstly, because less wear reduces the need for tools, secondly because all materials can now be machined with just one tool and thirdly, because the thread milling cutter is a combination tool which produces the core hole and thread in one step and without a tool change cycle. “For us, the focus was on the cost aspect,” says Paul Preiser. “We have achieved cost savings of around 20% using the Gühring thread milling cutter for this machining operation.” Today, the tool is used for all threads in the field of hard metals at Hago.
High-feed milling in the premier class
But this is not the only machining operation at Hago for which Gühring was able to offer a more economical alternative: “A competitor’s product was used for hard milling,” recalls Oliver Mattes, who has been advising Hago as a sales representative for over ten years. “But we were convinced that we could do better.” Hago agreed to a test and was able to mill pockets with a target depth of 35 mm. The challenge? Despite the very hard material with 62 HRC, it exceeded the tool life of the competitor’s tool. Gühring engineers had an ace up their sleeve here, too. A carbide developed especially for mould and die that is significantly finer and 200 HV harder. This ultra-hard substrate guarantees very good edge stability and, with it, process-reliable tool life in hard machining.
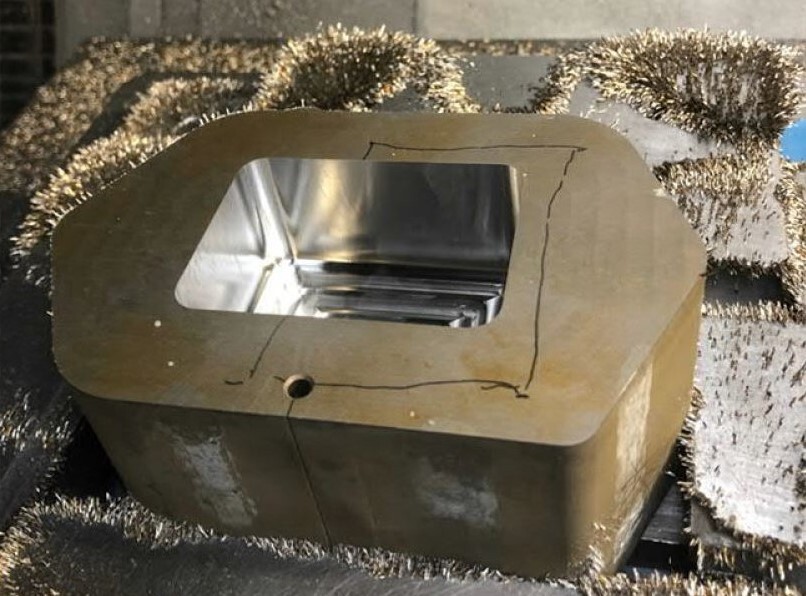
The result is a completely new tool solution for mould and die: With its innovative high-feed design, the HPC radius milling cutter G-Mold 65 HF ensures maximum feed rates at low cutting depths. Central internal coolant ducts increase process reliability when roughing hard materials up to 65 HRC and deep cavities. This has also been demonstrated at Hago: With the G-Mold 65 HF, Gühring reached the target depth of 35 mm in 84 minutes. Despite high cutting values, the tool showed little wear after machining. Once the milling cutters have reached the end of their tool life, Hago has them re-ground directly at Gühring to save tool costs.
Developing alternatives together
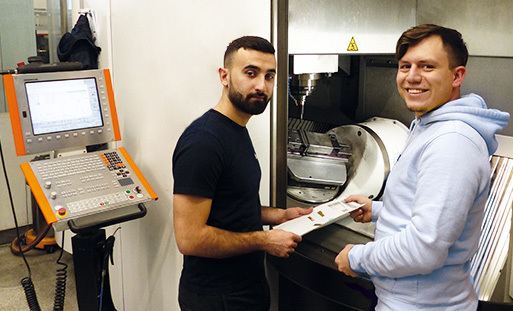
Gühring and Hago have far from reached the end of their search for economic alternatives. “Further tests will definitely follow,” promises Oliver Mattes. At each of his visits, he and Paul Preiser think about which machining operations can still be optimised with the help of Gühring. Paul Preiser also appreciates this successful collaboration: “It is important for us to have a partner that we know personally and with whom we can draw on shared experience.” He found such a partner in Gühring. “We are very happy with our relationship with Gühring. If we have any problems, the sales team can be reached at any time and help us to look for an approach that can be tested here as a solution.”
Have we piqued your interest?
Then arrange your personal consultation appointment now:
Technical advice and support are also available quickly and directly via our service hotline 00800 2607 2607
We can also be reached on WhatsApp: +49 172 658 53 53. Save the number!
You might also be interested in:
Modular drills: Their advantages and how you can benefit from them
Modular drilling systems such as the BT 800 from Gühring offer full performance at lower costs. Thanks to interchangeable drill heads, you save time, storage space and money – ideal for flexible applications with the highest demands on cost-effectiveness.
Threads for giants: Crane manufacturer relies on modular fluteless tap for blind holes
An innovation – the new modular fluteless tap from Gühring – has made it possible to solve deep-seated challenges in the production of blind hole threads at Karl Georg and to raise process reliability to a new level.
30% more tool life: With this parting off plate you achieve maximum performance in high-grade steel
30% more tool life when parting off: The new 2 mm parting off plate from Gühring’s System 222 impresses with excellent chip control, high process reliability and a perfect surface finish on ISO-M materials such as high-grade steel.