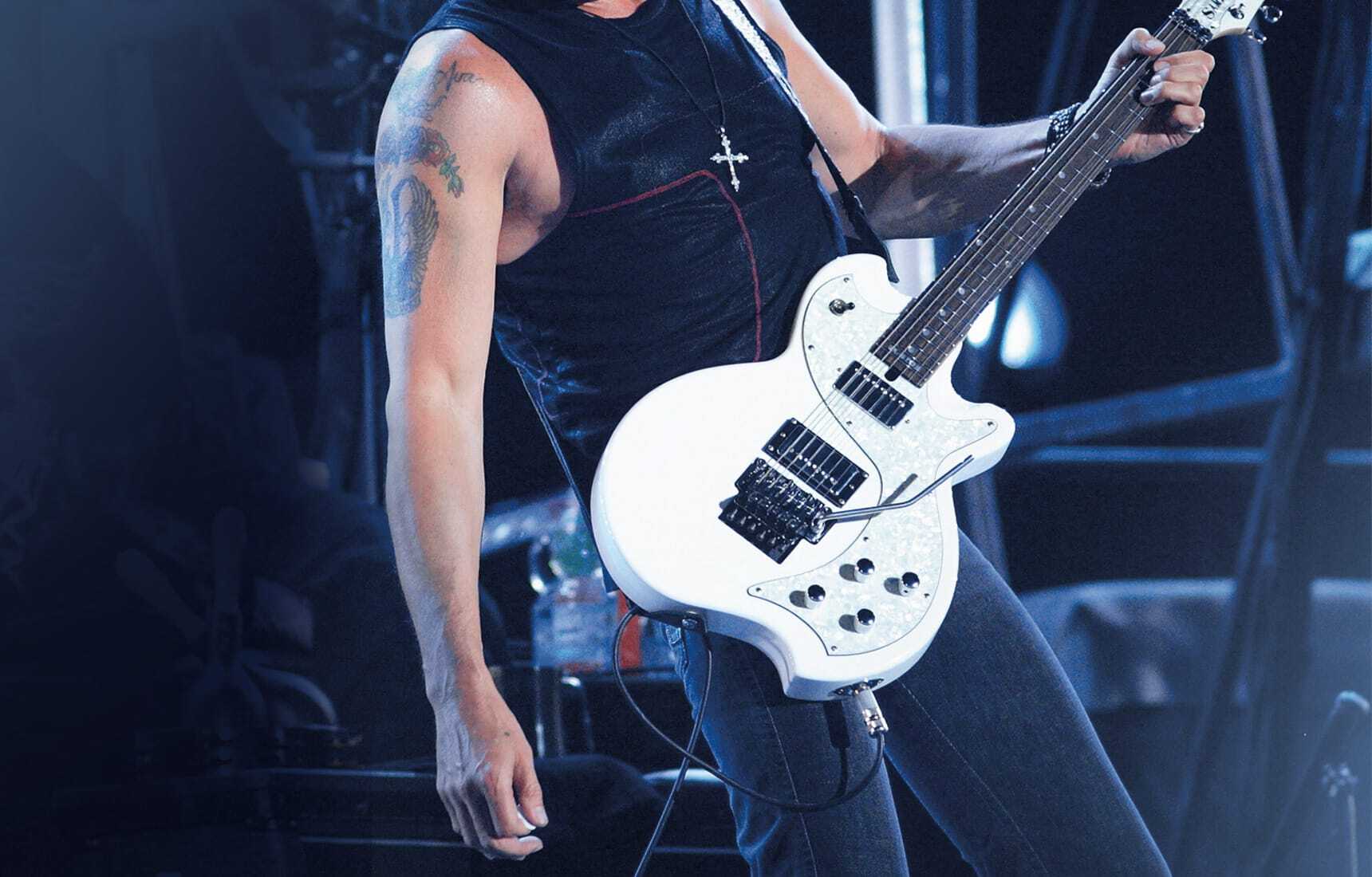
Table of contents
1. Protruding tools rattle during roughing
2. Solid carbide milling cutter from Gühring with optimised geometry
3. Outdoing the competition in high-volume milling
Experiencing vibrations during milling? This was a huge problem for a Japanese manufacturer of guitar parts: The long protruding tools started rattling during machining and led to a poor component finish. Gühring had the solution: The RF 100 Speed does not only stand out thanks to its high running smoothness, but also thanks to 25 percent longer tool lives.
Heartache, regret and a bed full of roses – this is Jon Bon Jovi lamenting his love life. Meanwhile, an electric guitar is screaming in the background: The notes are vibrating, resulting in quite a painful sound. Guitarists create this special lamentation effect by pulling a metal lever on the instrument’s lower tailpiece. This small movement changes the tension of the guitar strings, thereby adjusting the pitch.
So the aim of the component known as the vibrato arm is to make the music vibrate. Quite in contrast, vibrations are the last thing that are wanted during the production of this vibrato system. However, they were precisely the reason why Gotoh Gut Co. in Japan were experiencing problems. Since its creation in 1960, the company has made a name for itself on the global market. Nowadays, metal parts for string instruments are produced on eight machining centres and 28 CNC lathes. One of these products is a steel (SS400) vibrato block.
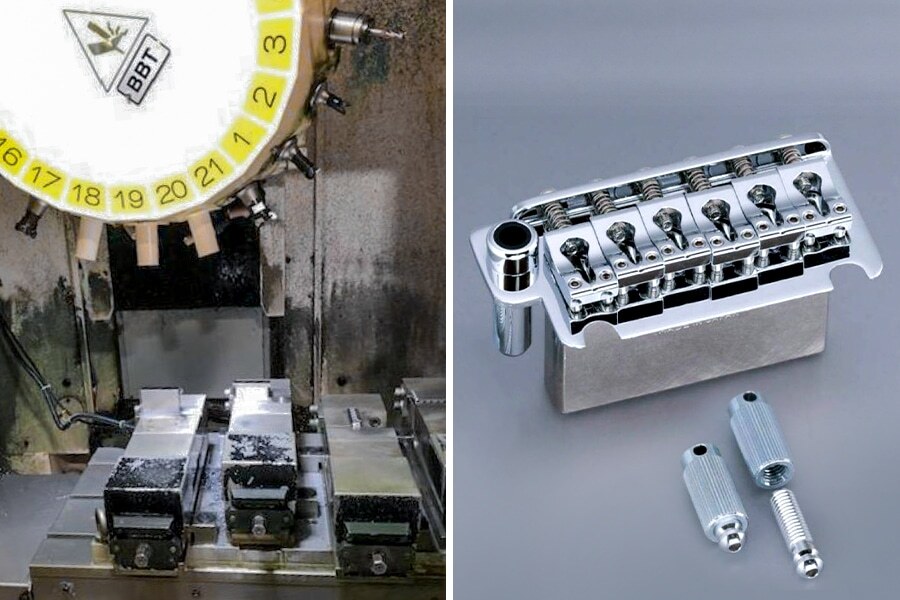
Protruding tools rattle during roughing
At Gotoh, the component’s lateral contour is finished on a vertical machining centre with external cooling, requiring a very high cutting depth of 42 mm. This can only be achieved with a long protruding tool– but this presents it own problems: During machining, the tool starts rattling, resulting in a poor component finish. A competitor relied on a five-fluted milling tool, but the rattling was too strong and machining had to be stopped. “The surface quality was not good due to the long tool length and the slight occurrence of rattling marks”, recalls Yoshiyuki Yamada, a Gühring sales representative. “The customer asked us to solve this problem.”
Solid carbide milling cutter from Gühring with optimised geometry
Gühring has the perfect solution to vibrations during milling: the RF 100 Speed. The solid carbide end mill is particularly well known for its high rigidity, which Gühring achieves through a coordinated flute profile with a high core factor. This enables the milling cutter to absorb the vibrations when milling. The RF 100 Speed also features a high helix of 48° and an unequal blade pitch – both of which promote a smooth, quiet cut.
Because only four cutting edges are used, there a fewer cutting edges in contact with the workpiece than in the competitor’s five-fluted concept; this significantly reduces radial forces and thus the creation of vibrations. The long design of the tool features chip breakers to cut the chips down to short lengths, ensuring smooth chip removal during high-performance machining.
Outdoing the competition in high-volume milling
Working in collaboration with Gotoh, our technical sales team opted for high-speed cutting with the RF 100 Speed, as this is the best way to produce the best surface finish. More than twice the cutting speed and a 20 percent higher feed rate are now achieved when machining the vibrato block. At the same time, the RF 100 Speed impresses with significantly longer tool lives than the competitor’s tool: Using a Gühring milling cutter, the customer is now able to produce 25 percent more components than before.
Our tool immediately ensured a reliable process.
Werkzeug | RF 100 Speed P, Gühring, 4 cutting edges Ø 10 mm |
5 cutting edges, Competitor, Ø 10 mm |
Component | Vibrato block | Vibratio block |
Material | SS400 (JIS G 3101) | SS400 (JIS G 3101) |
Cutting speed | vc = 270 m/min | vc = 120 m/min |
Speed | n = 8600 U/min | n = 3822 U/min |
Feed | Fz = 0,055 mm | fz = 0,1 mm |
Feed rate | vf = 1892 mm/min | vf = 1528 mm/min |
Lateral infeed | ae =0,2 mm | ae = 0,2 mm |
Cutting depth | ap = 42 mm | ap = 42 mm |
Tool life | 250 parts | 200 parts |
25 % more components possible with one tool at 20 % higher feed rate |
This was made possible by an innovative combination of optimised micro-geometry and the high-temperature-resistant SuperA coating, which has an excellent combination of hardness and oxidation resistance. With the RF 100 Speed, Gühring has succeeded in bringing stability into the machining process. And, most importantly: The surface quality of the manufactured components is very high. Yoshiyuki Yamada is satisfied: “Gotoh was facing problems that could not be solved with competitors’ tools. However, the tool we proposed immediately ensured a reliable process.”
Technical advice and support are also available quickly and directly via our service hotline 00800 2607 2607
We can also be reached on WhatsApp: +49 172 658 53 53. Save the number!
You might also be interested in:
Experts in stainless steels: 3 tools for stainless steel machining
With the new high-performance tools for stainless steel machining, Gühring offers the optimal solution. Special coatings and adapted geometries guarantee the highest cutting values and extended service life. This means that the most demanding machining tasks can be mastered in a wide range of industries.
Six times higher metal removal rate: New micro-precision milling cutter for ISO-N materials
The RF 100 AL Micro offers an outstanding combination of precision, efficiency and process reliability, making it the first choice when machining aluminium, copper and brass. With its innovative properties this tool raises the bar for micro-machining.
Finger on the pulse: Pocket milling in grade 5 titanium
A customer uses grade 5 titanium to make the case for pacemaker batteries, but machining the material is challenging. Gühring has the solution: The G-Mold 65 HF solid carbide end mill enabled it to extend the tool life 73 times over.