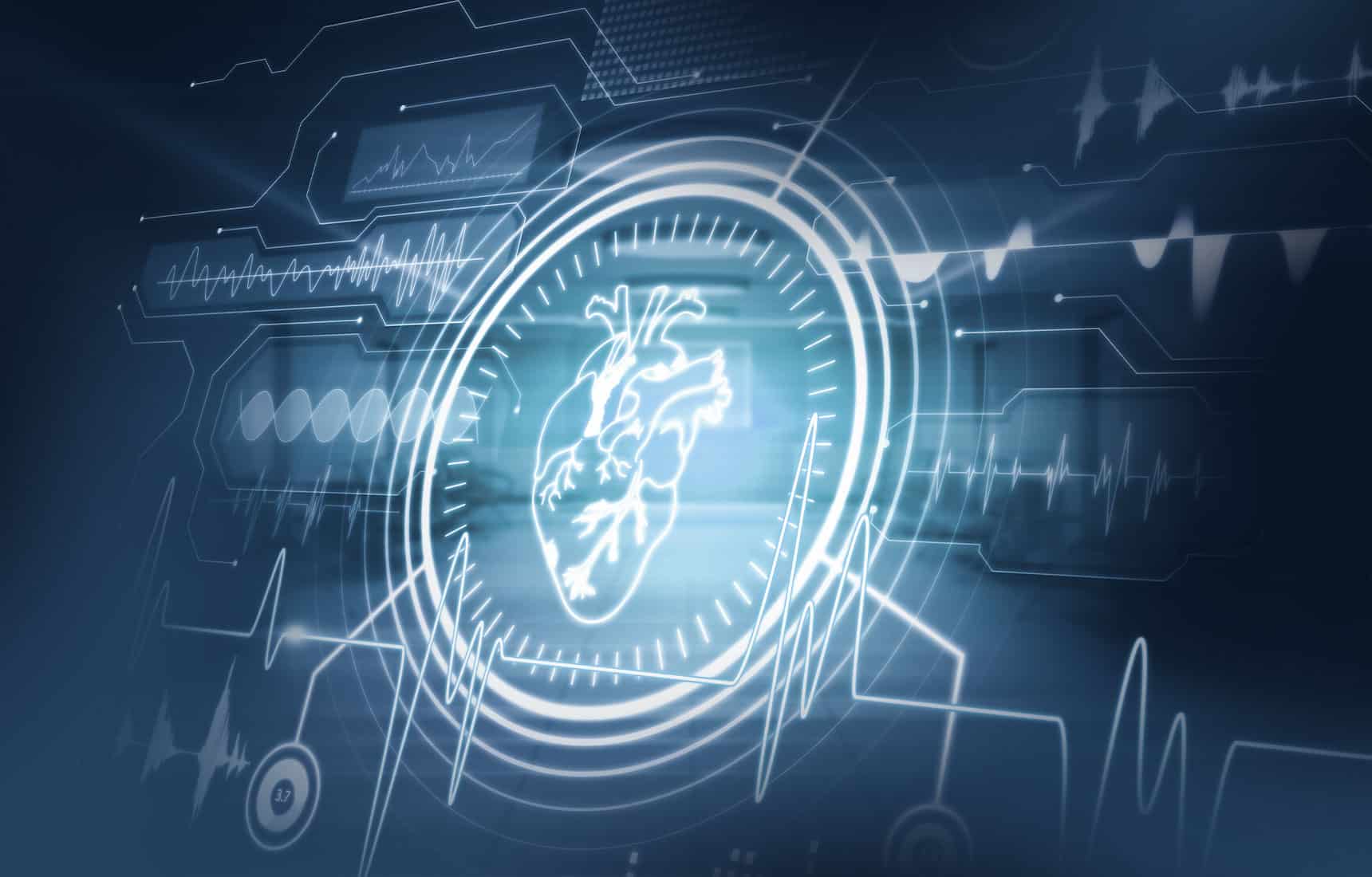
It may just be a small battery case, but it’s crucial for many people’s lives. That’s because it is installed in a pacemaker and keeps our internal motor running. However, only perfectly machined parts can guarantee the durability and efficiency required. So, it’s good that, here at Gühring, our hearts beat for precision machining.
Like many companies in the medical field, the Japanese company Microcut Co.,LTD also relies on the material grade 5 titanium (Ti6Al4V). A battery case made of this material does not feel heavy when installed in the body, yet is extremely durable. What is more, the titanium alloy is biocompatible, does not cause reactions or allergies, does not corrode and is not magnetic. But grade 5 titanium also has its pitfalls – especially when it comes to machining.
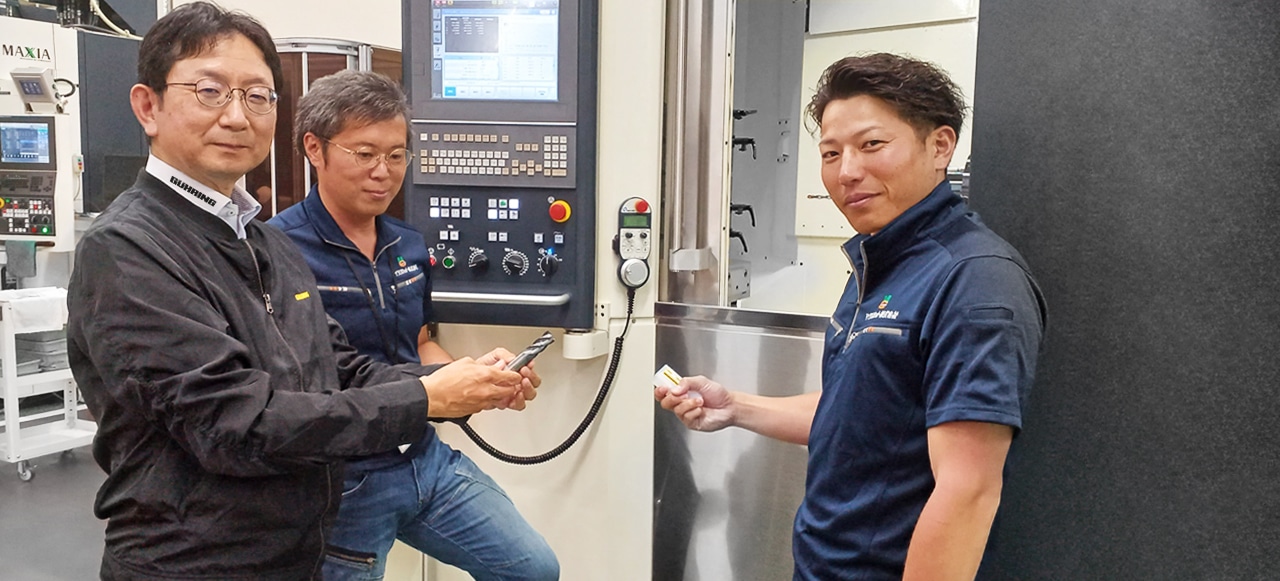
Field sales representative Shinji Fukai (left) presents the G-Mold milling cutter to the managers of Microcut.
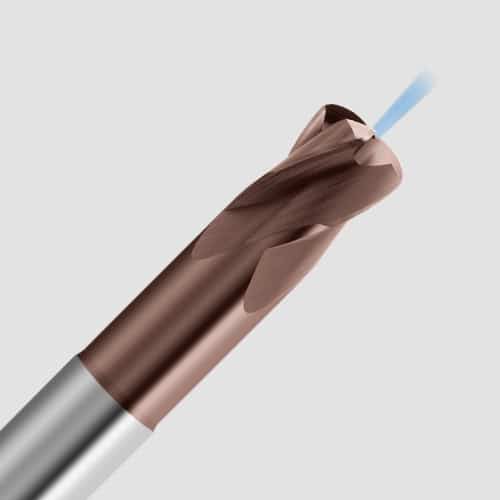
Goal: Faster milling with less wear
Microcut could not ignore this when milling pockets into the components. After just 32 workpieces, a competitor’s tools were worn out despite being coated. For this reason, the company approached Gühring with the challenge of delivering a tool solution for better tool lives and machining times.
Gühring provided the solution in the form of the G-Mold 65 HF solid carbide end mill. Equipped with internal cooling and a Signum coating known for extremely high wear resistance, this milling cutter promised a significant improvement to tool life and machining efficiency. “We recommended the G-Mold 65 HF here, which can be used at high feed rates, making it extremely efficient,” explains sales representative Shinji Fukai.
73 times longer tool life
Even after the first tests using the previous cutting parameters, the result was impressive: The tool life of the G-Mold 65 HF was 15 times longer than that of the competitor’s tool. But that was just the beginning. After the customer had adapted their cutting parameters to the new high-performance tool, they increased the tool life 73 times over with the G-Mold 65 HF compared to the competitor’s tool.
Here, the G-Mold 65 HF demonstrated its strengths by being able to operate at high feed rates and with maximum efficiency. Gühring was also able to achieve an advantage for the customer with regard to machining time: With the G-Mold HF, the feed rates were doubled and cutting speeds increased by 25 %, which significantly reduced machining time.
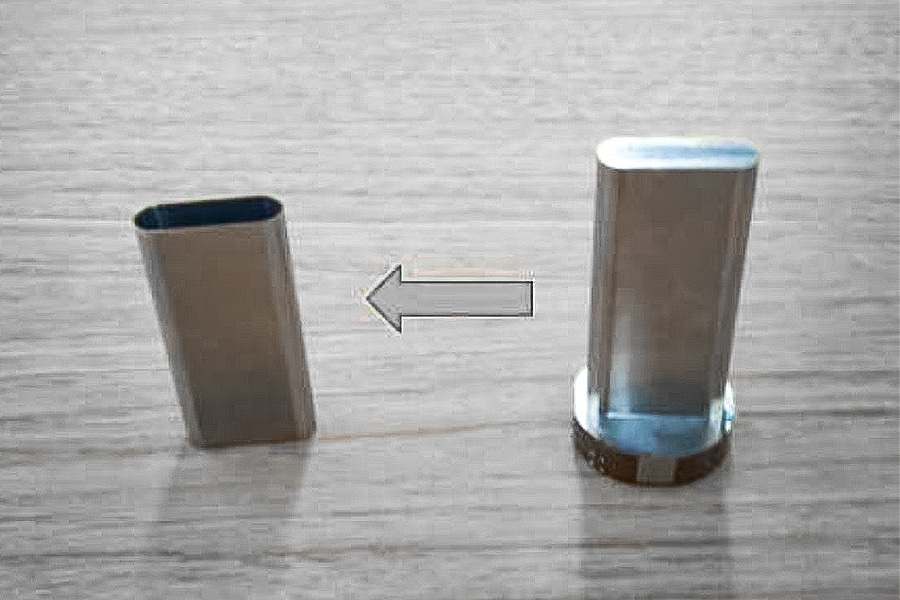
Information on the machining setup
- Horizontal machining centre MAKINO a61nx
- Tool clamping: HSK A63
- Cooling: Internal cooling, oil-based coolant
G-Mold 65 HF, high-feed milling cutter, 4-fluted with internal cooling | Competitor’s 4-fluted cutter |
Vc = 100 m/min | Vc = 80 m/min |
fz = 0. 1 mm | fz = 0. 05 mm |
Vf = 3184 mm/min | Vf = 1273 mm/min |
n = 7961 U/min | n = 6368 U/min |
ae = 4.0 mm | ae = 4.0 mm |
ap = 0.3 mm | ap = 0.3 mm |
Parts / milling cutter = 2336 | Parts / milling cutter = 32 |
Technical advice and support are also available quickly and directly via our service hotline 00800 2607 2607. We can also be reached on WhatsApp: +49 172 658 53 53. Save the number!
You might also be interested in:
Fast and dynamic: Trochoidal milling in mould making
One milling strategy has proven to be particularly successful for mould making, where sometimes very hard materials have to be machined in the shortest possible time: GTC milling. This form of trochoidal milling results in particularly long tool lives during machining.
Mould and die: hard machining shortens processes
Competitive pressure in mould making is forcing Vogt AG to shorten its lead times by means of hard machining. Tools from Gühring offer innovative solutions for machining hardened steel up to 54 HRC.
Cross holes? Not a problem! With the right deep drilling strategy
The machining of intersecting deep holes can be tricky: This is because the cooling process is interrupted, creating an adverse spot drilling or guidance situation. Gaps can only be bridged with the right strategy.