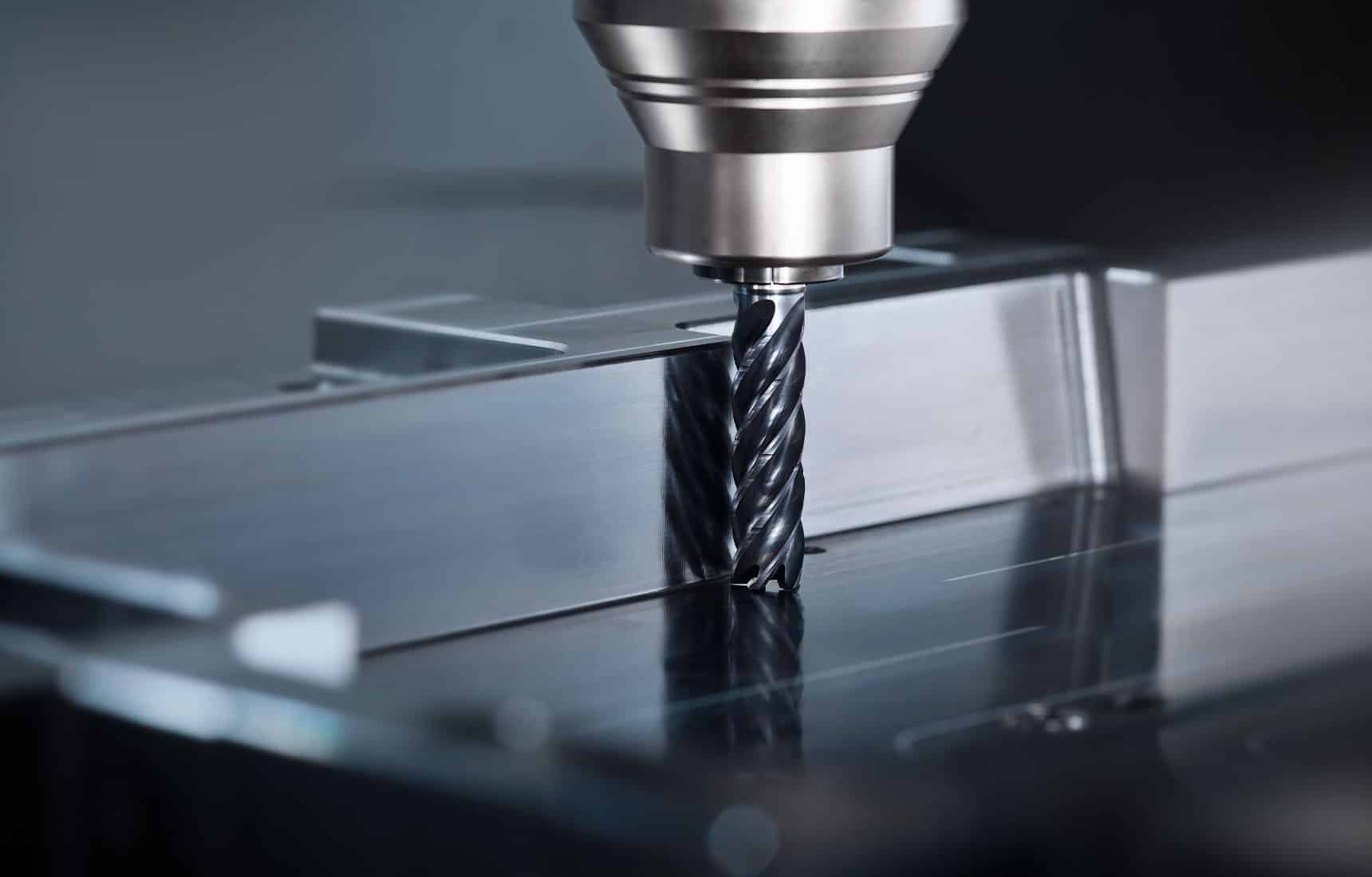
Contents
1. How does trochoidal milling work?
2. Dynamic trochoidal milling with the RF 100 Speed P
3. Trochoidal milling in hard machining with the G-Mold 65 U
4. Profile milling with the G-Mold 55 B ball nose end mill
Time is money. This applies to all industries, but in particular to the field of mould and die. Competitive pressure is high here, and in order to remain economical, manufacturing cycles need to keep getting shorter. One milling strategy has proven its worth here: “Gühring Trochoidal Cutting” or, for short: GTC milling.
This dynamic milling strategy is a form of trochoidal milling and is being used more and more, especially in the machining of die and injection moulds, because – in addition to short machining times – the technology also impresses with the best possible part contours and high surface qualities. However, the machining of thin-walled components and the production of difficult 3D shapes or free-form cuts are typical examples for the use of GTC milling cutters. All this can be achieved in even the hardest and most difficult-to-machine materials or under adverse diameter-to-length ratios – usually without the need for rework.
How does trochoidal milling work?
These milling strategies are among the most modern and effective cutting methods. The basic principle of trochoidal milling is based on maximum tool utilisation: The process uses a small cutting width (ae) and the maximum cutting depth (ap). By using the tool’s entire cutting edge length, it is able to unleash its full power. This is particularly important in the area of mould and die, where enormous quantities of high-strength steel have to be machined. In trochoidal milling, the tool wrap is low, which improves the thermal effect on the tool cutting edge and ensures low mechanical stress. In addition, this procedure leads to longer tool lives as the wear is evenly distributed over the entire cutting edge.
However, not every milling cutter is suitable for this style of dynamic milling. This calls for high-quality solid carbide tools that can withstand machining at extremely high cutting speeds and significantly accelerated feed rates. We present three such tools for different applications in mould and die.
Underlying principles & objectives of GTC milling
Maximum tool utilisation
- Utilisation of the entire cutting edge length
- Full power delivery
- Increased tool lives
- Balanced wear
Modification of cut index
- Low cutting widths ae
- High cutting depths ap
High process reliability
- Low tool wrapping
- Improved thermal conditions at the tool cutting edge
- Lower mechanical load
Maximum chipping volume
- Saved time / machine costs
3 tools for dynamic milling in mould making:
Dynamic trochoidal milling with the RF 100 Speed P
The RF 100 Speed P is specially adapted for machining steel, high-strength steel and cast materials and ensures maximum metal removal rates and outstanding process reliability for roughing and finishing up to 48 HRC. The solid carbide milling cutter is perfectly suited for trochoidal milling. The entire cutting edge length of the roughing end mill is used with a small cutting width (5-15% ae).
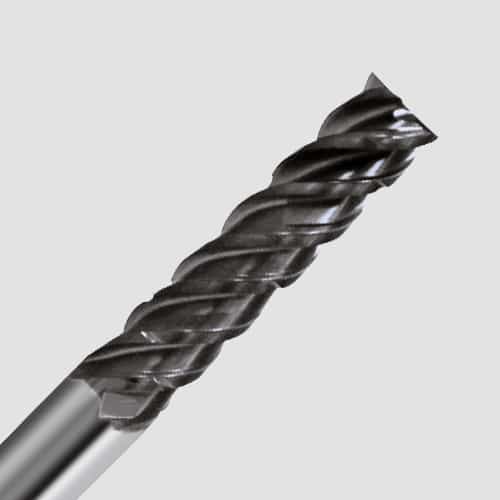
In this way, extreme metal removal rates and significantly higher feed rates can be achieved and the cutting forces that occur are much, much lower. In real life, this tool, used in the dynamic GTC process, can cut the machining time by more than half compared to a conventional round plate milling cutter head.
Tool | RF 100 Speed P, Ø 16 mm |
Component | Form insert for injection moulding tool |
Material | Tool steel (1.2085) |
Cutting speed | Vc = 246 m/min |
Rotational speed | Vf = 4600 U/min |
Feed rate | n = 4900 mm/min |
Feed rate per tooth | fz = 0,22 mm/Z |
Metal removal rate | Q = 171 cm³/min |
Cutting depth | ap = 53 mm |
Radial contact width | ae = 0.75 mm |
Trochoidal milling in hard machining with the G-Mold 65 U
However, many moulds and tools are also machined in a hardened state. Dynamic milling strategies such as GTC are also very effective during hard milling, as the contact time between the cutting edges and the tool is significantly shorter than in conventional milling applications. This in turn has a very positive effect on tool life. However, due to the hard material, only two to a maximum of five percent of the lateral infeed can be used here.
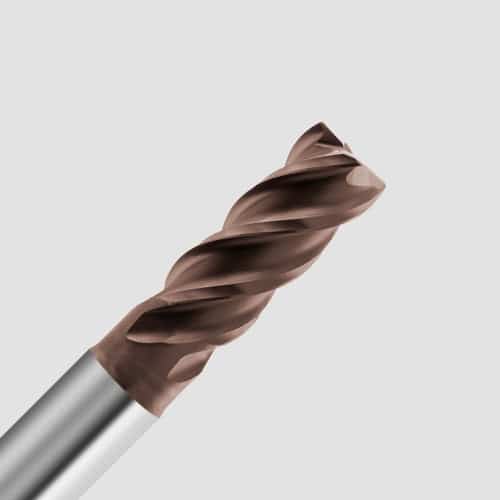
The G-Mold 65 U from Gühring is particularly suitable for the GTC milling of hardened moulds and mould inserts. Its precise geometry ensures high contour accuracy during dynamic milling. This means that complex moulds and contours can be machined with the highest level of precision. At the same time, the end mill has an FEM-optimised radius angle transition, which ensures high radial stiffness and low deflection. This ensures stable milling results and minimises vibrations. In materials such as heat-treated steel with up to 65 HRC, the G-Mold 65 U manages to halve the runtime during pre-finishing when used in a GTC milling process.
Tool | G-Mold 65 U, Ø 12 mm |
Component | Form insert for injection moulding tool |
Material | Hardened steel (1.2347), 54 HRC |
Cutting speed | Vc = 120 m/min |
Rotational speed | n = 3180 U/min |
Feed rate per tooth | Fz = 0.06 mm |
Feed rate | Vf = 760 mm/min |
Cutting depth | ap = 17.0 mm |
Radial contact width | ae = 0.6 mm (0.05xD) |
Profile milling with the G-Mold 55 B ball nose end mill
During hard machining in mould and die processes, stock on the component often has to be removed quickly and evenly. Under optimal conditions (HSC), dynamic milling can be used here. While most competitors only offer two-fluted milling cutters for this purpose, the G-Mold 55 B is available as a four-fluted variant. By spreading the process over twice the number of cutting edges, the machining time can be almost halved.
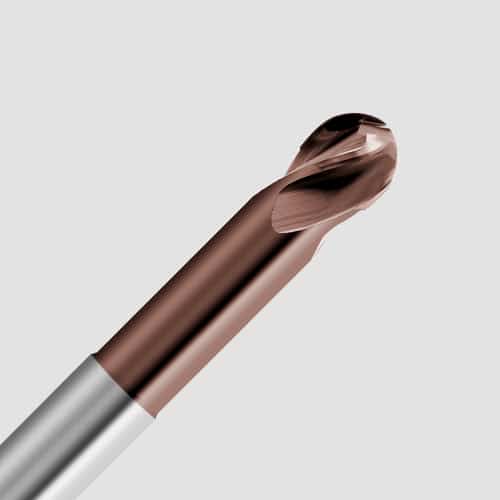
A dynamic milling strategy also offers significant productivity advantages for 3D machining with spherical or toric milling cutters. Here, milling is also carried out with very tiny infeeds, taking into account the effective tool diameter. The total feed rate is increased at the same time. For cutting depths ap < 0.2xD, the effective diameter Deff actually engaged must be used to calculate the rotational speed. To increase the tool life, we recommend machining with the spindle tilted.
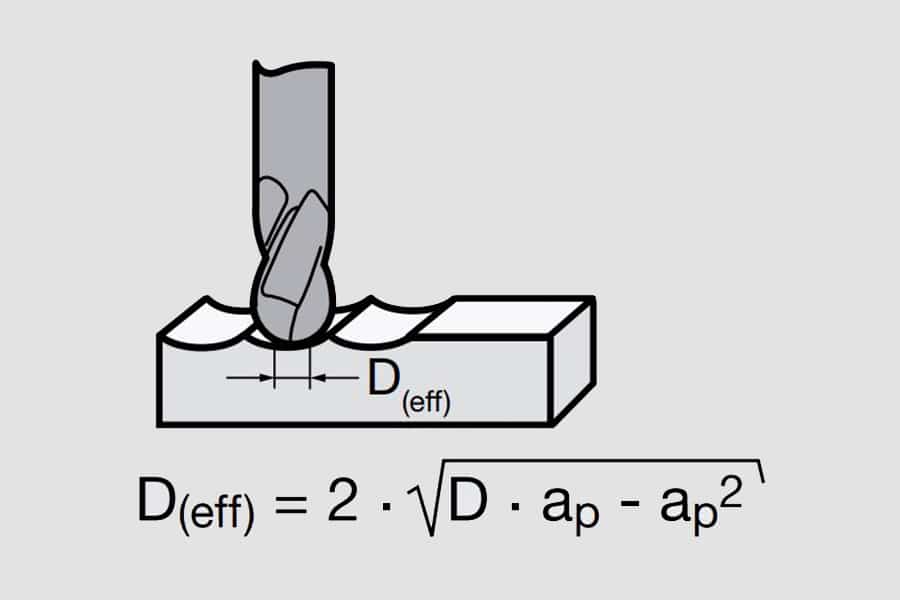
Tool | G-Mold 55 B, Ø 6mm |
Component | Formplatte für Spritzgusswerkzeug |
Material | Hardened steel (1.2083), 52 HRC |
Cutting speed | Vc = 180 m/min |
Feed rate per tooth | Fz = 0.1 mm/Z |
Feed rate | F = 382 mm/sec |
Rotational speed | n = 9950 U/min |
Cutting depth | ap = 0.15 mm |
Radial contact width | ae = 0.15 mm |
Technical advice and support are also available quickly and directly via our service hotline 00800 2607 2607 We can also be reached on WhatsApp: +49 172 658 53 53. Save the number!
You might also be interested in:
Experts in stainless steels: 3 tools for stainless steel machining
With the new high-performance tools for stainless steel machining, Gühring offers the optimal solution. Special coatings and adapted geometries guarantee the highest cutting values and extended service life. This means that the most demanding machining tasks can be mastered in a wide range of industries.
Six times higher metal removal rate: New micro-precision milling cutter for ISO-N materials
The RF 100 AL Micro offers an outstanding combination of precision, efficiency and process reliability, making it the first choice when machining aluminium, copper and brass. With its innovative properties this tool raises the bar for micro-machining.
Finger on the pulse: Pocket milling in grade 5 titanium
A customer uses grade 5 titanium to make the case for pacemaker batteries, but machining the material is challenging. Gühring has the solution: The G-Mold 65 HF solid carbide end mill enabled it to extend the tool life 73 times over.