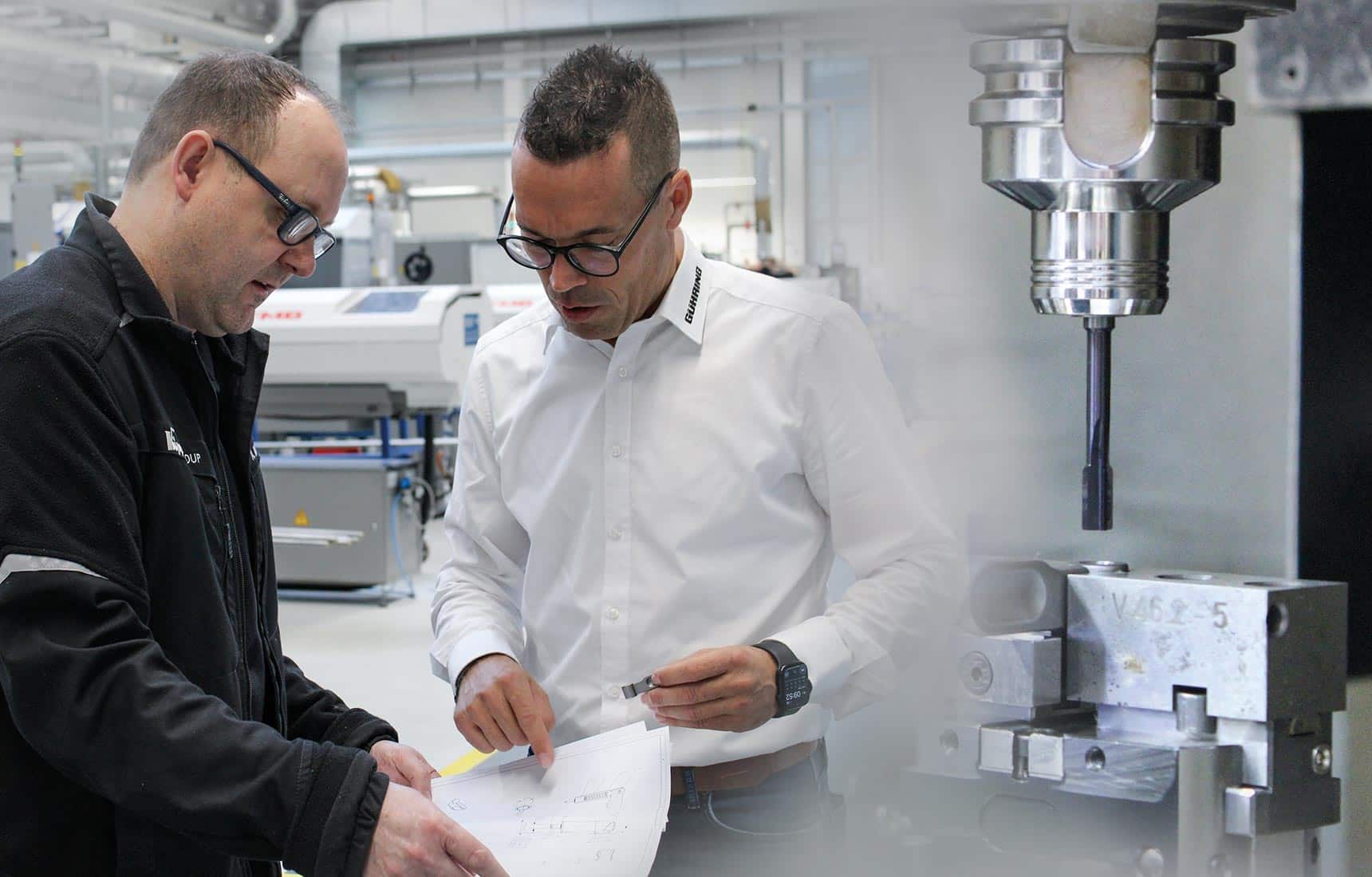
Contents
1. Cast component presents a challenge for KIPP
2. A Gühring high-performance reamer has the answer
3. The courage to push ahead pays off
4. Overcoming challenges together
Perfect dimensional accuracy, reduced machining times and a 100-fold increase in tool lives – KIPP is achieving all this with the high-performance HR 500 reamer from Gühring. The family-run company from Sulz am Neckar in Germany was facing a challenge when it came to producing precise fits: µ-level precision when machining difficult materials such as cast steel places high demands on the tools used to produce the exact through-holes. With the HR 500, KIPP no longer has to worry about poor dimensional accuracy or short tool lives.
Clamping technology, standard elements and operating components – these are the specialities of HEINRICH KIPP WERK GmbH & Co. KG. The family-run company, which made its name with the classic KIPP clamping lever, employs 500 people and manufactures standard parts and assemblies for the areas of industry, mechanical engineering and plant construction. Its exceptionally high standards of ergonomics, stability and precision always come first. This also applies to its production of precise fits in cast steel, which pushes conventional reamers to their limits – and poses real challenges for KIPP.
Cast component presents a challenge for KIPP
The grip is a small cast-steel product that, after production, is assembled to create a complete device, known as the cam-action indexing plunger. This can be used to lock and unlock machine doors manually, for example. After the grip has been inserted into a threaded sleeve with a spring assembly, a bolt is pressed into the grip’s fit.
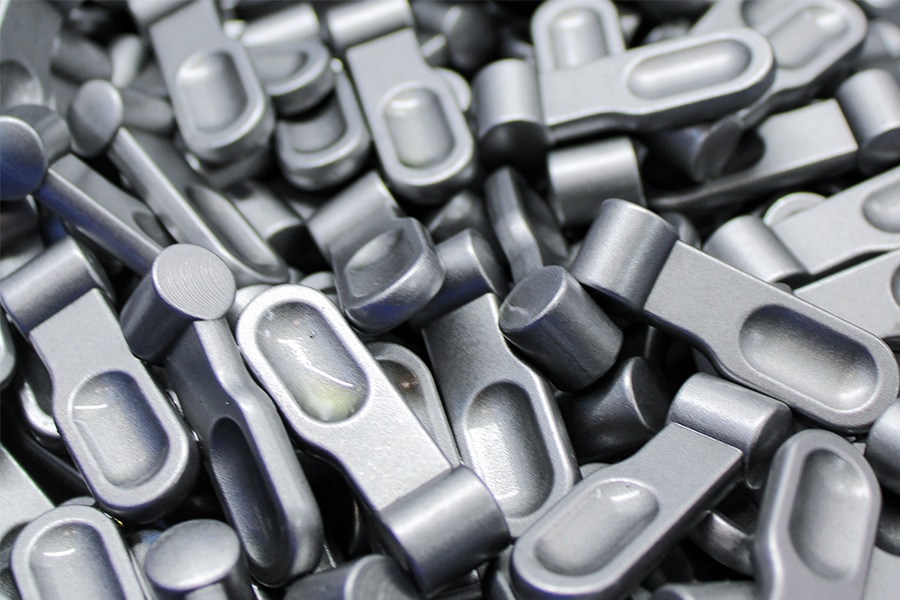
There is no room for large tolerances: As it is a press fit, the hole must be perfectly matched to the bolt. For the H7 fit with a tolerance range of + 5µ, it first has to be pre-drilled and then machined with a reamer. A 3-axis STAMA milling machine is used for this purpose.
However, it is all easier said than done: Two different materials are used to manufacture the products, which does not make things easy for the reamers: Stainless steel 1.4308 and quenched and tempered steel C 45. “When it comes to dimensional accuracy in particular, cast materials are always somewhat problematic because the exact composition of the alloy can vary,” explains Alexander Wolber, who is responsible for tool coordination at KIPP. “The materials have hard and tough properties, which makes them difficult to machine.”
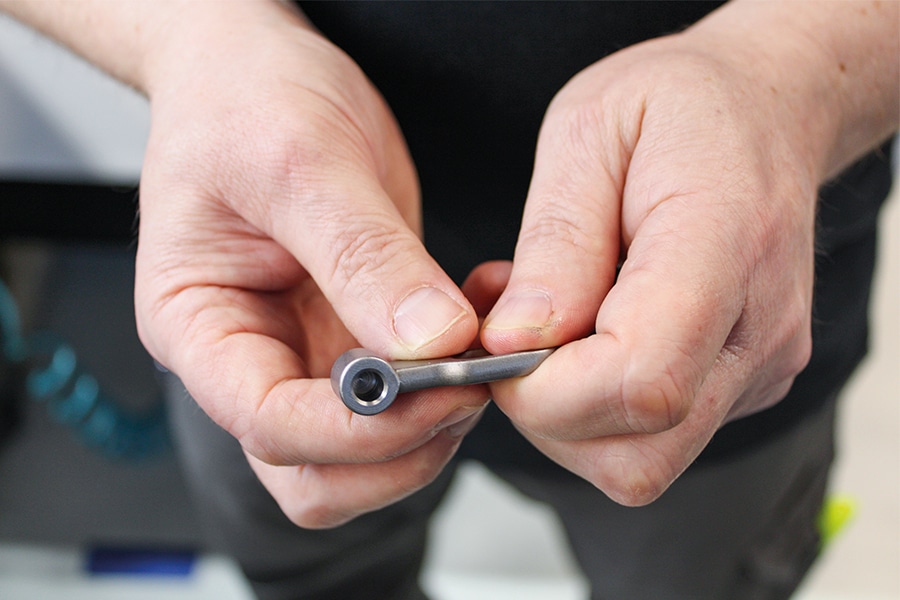
And KIPP is all too familiar with these difficulties: “First we used HSS reamers for the grip’s fit, but that didn’t work out at all,” recalls Alexander Wolber. But even a competitor’s solid carbide reamers delivered results that were far from satisfactory. The tools reached the end of their tool life after a maximum of 20–40 components.
“In parts made from cast materials, removing chips is a real issue. In some cases, we experienced built-up edges, while in others, the tools even broke off,” recalls Wolber. “Due to the rapid rate of wear, it was almost impossible for us to maintain the required dimensional accuracy.” These difficulties were topped off by high tool costs, because KIPP not only produces grips in four different sizes, but also in high quantities: Even with a tool life of 40 components, KIPP would need 1,500 reamers to produce the 60,000 grips that need to be produced each year. It was clear that a different tool solution had to be found.
A Gühring high-performance reamer has the answer
“There are no problems, only challenges,” says Jürgen Knorr, sales representative at Gühring. When Alexander Wolber presented the situation to his contact at Gühring, it didn’t take long for a solution to be found: “The HR 500 offers a decisive competitive advantage: our tool lives are now multiple times longer and we can move much faster,” explains Jürgen Knorr. “To put it simply: the HR 500 does its job.”
The company is using the universal blind hole variant (art. no.: 1675), which is available in intermediate dimensions of Ø1.97–20.1 mm. This means that steels, stainless steels, special alloys and hardened steels up to 63 HRC can be machined easily and precisely. As such, this version is suitable for both materials that KIPP uses for its grips. But what advantages does this reamer offer compared to conventional solid carbide reamers? The answer lies in the perfect combination of geometry, coating and cooling. The extremely unequal blade pitch ensures a smooth cut and high surface quality, while the central coolant supply with front-side outlets ensures good chip removal in the blind hole.
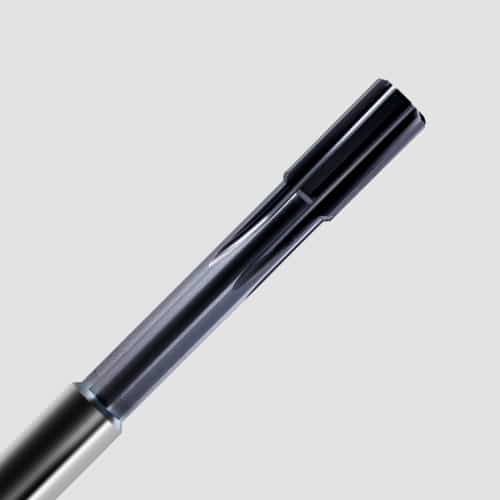
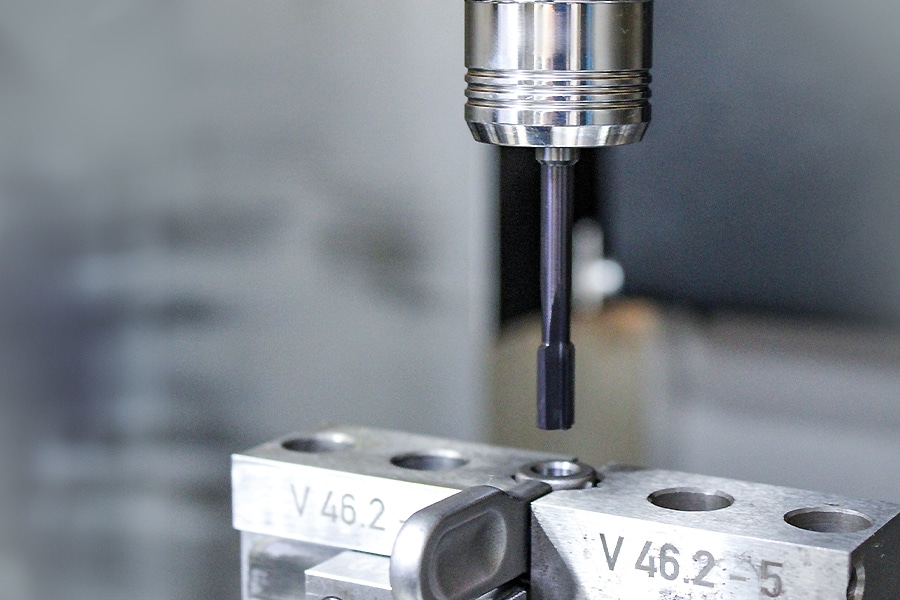
The TiAIN nanoA coating protects the tool from wear and ensures long tool lives. Thanks to these properties, the HR 500 impresses compared to conventional solid carbide reamers with extreme levels of performance. Shortly afterwards, KIPP began its initial trials with the high-performance reamer from Gühring.
The courage to push ahead pays off
“Our first attempts were relatively unsuccessful because we approached the new tool with low feed rates,” smiles Wolber. “We weren’t used to reamers working with these high feed rates.” A reasonably common occurrence as Jürgen Knorr well knows: “The HR 500 facilitates significantly higher feed rates. This scares off lots of customers at first, because they tend to work with slow feeds when reaming.” And for good reason: Feed rates that are too high during reaming can result in poor surface finishes, tool breakage or even damage to the machine. Thanks to the HR 500, KIPP doesn’t have to worry about this.
However, the courage to push ahead pays off: “We were not only able to achieve excellent dimensional accuracy, but we are also able to machine much faster,” reports Alexander Wolber enthusiastically. Compared to the competitor’s reamers, KIPP can produce the fit at a feed rate of 0.6 mm/rev instead of 0.125 mm/rev. And the HR 500 is also an absolute game changer when it comes to tool lives: “We used to be able to produce 20–40 grips per reamer. The HR 500 can handle up to 4,000 grips without any detriment to the dimensional accuracy,” says Wolber.
Tool | Carbide reamer Ø 6mm | HR 500 Ø 6 mm |
Feed | f = 0.125 mm/U | F = 0.6 mm/U |
Feed rate | Vc = 6 m/min | Vc = 103 m/min |
Speed | n = 320 U/min | n = 5500 U/min |
Overcoming challenges together
By switching to the high-performance reamer from Gühring, KIPP is not only reducing its machining time, but also saving on tool costs – and does not have to worry when it comes to meeting the tight tolerances.
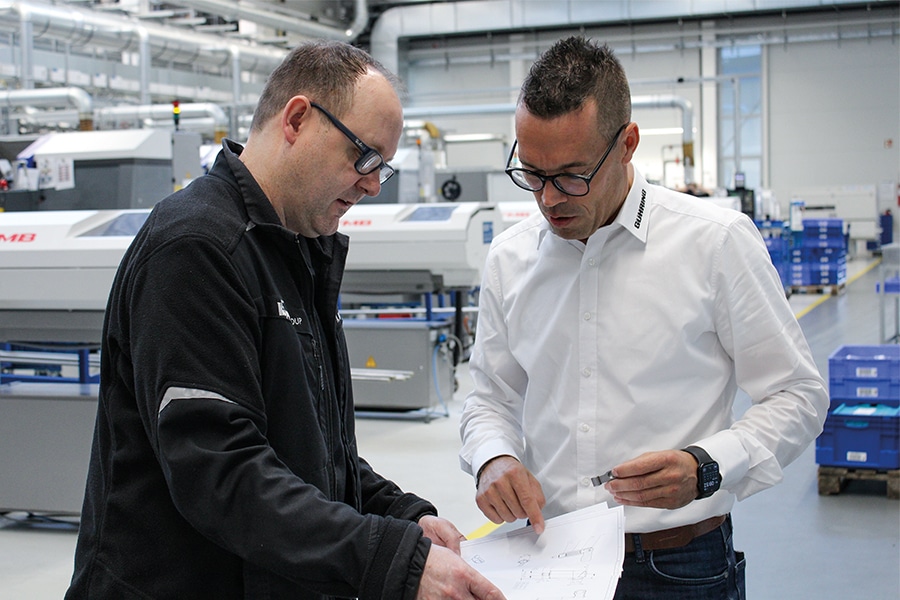
KIPP is now using a number of different Gühring reamers. In addition to the HR 500 range, these also include special tools that are specifically tailored to the customer’s requirements. One thing that KIPP particularly appreciates about working with Gühring is having a fixed, reliable contact person who is not afraid of challenges: “Jürgen Knorr is always ready to lend us his ear. If there’s a problem, he quickly makes time to pop over and provide us with expert advice. Our working relationship is going very well,” says Wolber.
Technical advice and support are also available quickly and directly via our service hotline 00800 2607 2607. We can also be reached on WhatsApp: +49 172 658 53 53. Save the number!
You might also be interested in:
Threads for giants: Crane manufacturer relies on modular fluteless tap for blind holes
An innovation – the new modular fluteless tap from Gühring – has made it possible to solve deep-seated challenges in the production of blind hole threads at Karl Georg and to raise process reliability to a new level.
New market standard: The perfect fit for any diameter range
Gühring is expanding the diameter range of its high-performance reamer, the HR 500, by dimensional increments of +-0.05 mm. The result: With the new fixed-size reamers in 5µ increments, Gühring covers all tolerance ranges with a precision-fit.
Mill products yourself instead of buying-in expensive ones: How a Swabian company is cutting costs
A 130 % price increase for a blank presents economic problems for a customer. The solution? Do-it-yourself – with a brand-new machining strategy and tools from Gühring. The result: 50 % savings per component.