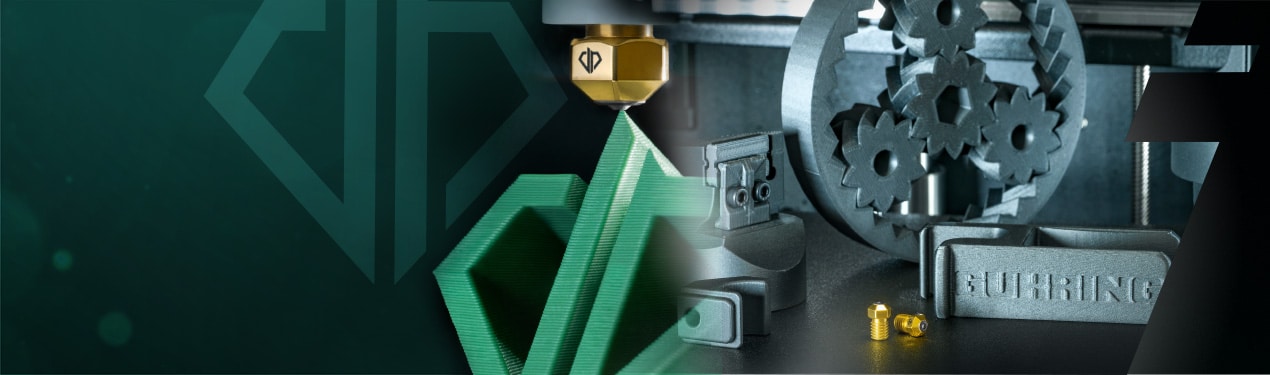
CR-3D is a leading complete supplier in the field of additive manufacturing and develops and produces all necessary components for 3D printing in industrial environments. What began as a garage start-up recently started filling a hall with over 700 square metres of production facilities – equipped exclusively with state-of-the-art 3D printers. Gühring supplies the heart of this new type of machine: the diamond printer nozzle.
“Four years ago, it was still a garage startup, just me and a computer,” recalls Christian Reil. “Today we offer 30 different printer models. And we are the only 3D printer manufacturer on the market that produces exclusively in Germany.” The engineer founded the CR-3D brand in 2016: “I was already obsessed with 3D printing during my studies and this technology has been with me ever since. That’s why I want to continue to promote and establish it on the market.” The process is extremely versatile and flexible. Be it metal, clay or chocolate – 3D printing knows no bounds.
But this calls for 3D printers that anyone can use – the 14-year-old amateur crafter or the dental assistant, who uses them to print parts for oral surgery directly in the practice. And there’s something else that’s important: The printer, software and filament, i.e. the material that is printed, must work together perfectly. That’s why Reil offers everything from a single source. “We offer many standard plastics for 3D printing, but also metal filaments and technical materials that contain carbon or glass fibres and can be used to print extremely stable components.” However, these components are extremely abrasive, which is why the printer nozzle must also be as wear-resistant as possible for this type of printing job. And that’s exactly the one thing Reil was missing.
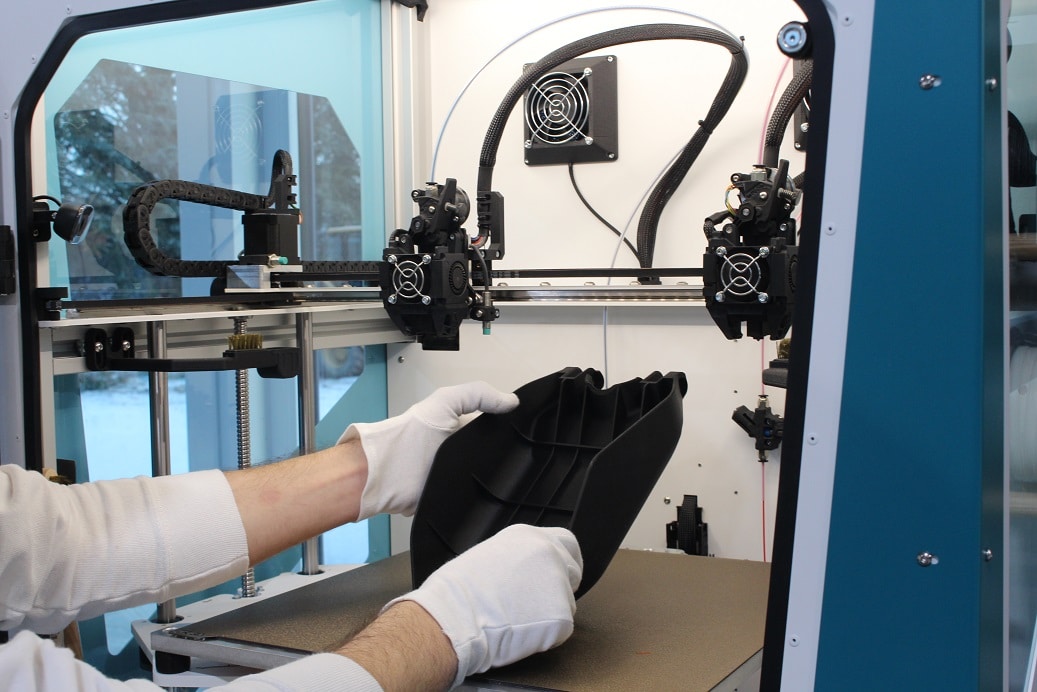
The nozzle with the black diamond
The cooperation between Gühring and CR-3D began with a Facebook post: “Looking for reliable partners who can produce nozzles for our 3D printers from different materials (brass, steel, tool steel, etc.),” wrote Christian Reil. “WhenI read the ad, I immediately knew that the Dianoz nozzle would fit in perfectly here,” recalls Peter Hartmann, who had recently developed the Gühring diamond nozzle with his team. The components that Reil is able to print at its production facilities in Cham are 5 millimetres to one metre long. The Dianoz is the first diamond-tipped printer nozzle on the market. As the hardest natural material in the world, diamond offers the best wear protection – including as an insert in the nozzle tip.
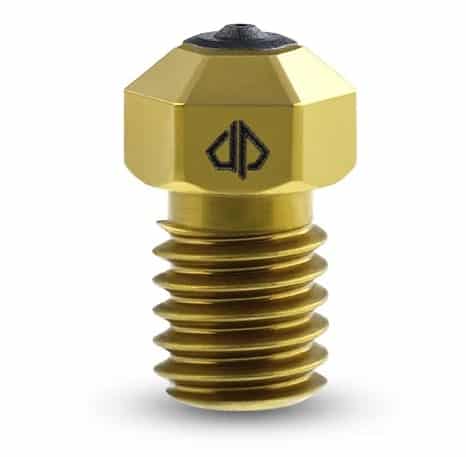
At the same time, it conducts heat extremely well, ensuring even material extrusion and smooth surfaces. No other material can combine these two properties so well. This makes the Dianoz nozzle perfect for printing abrasive filaments in fused deposition modelling (FDM). Hartmann sent a diamond nozzle to Christian Reil. That was over a year ago – and it’s still running. Since then, 50 kilograms of carbon fibre filament have passed through this nozzle without it showing any signs of wear, let alone having to be replaced. This is despite the fact that the printed material is an extremely abrasive material, 20% of which is filled with very long and hard glass fibres. “With this material, a standard steel nozzle would have come to an end after around ten kilograms, and a brass nozzle after just 30 gram,” explains Reil.
Less wear saves time
As soon as the nozzle becomes shorter due to wear, the distance to the printing bed is no longer correct and the surface suffers. The printing process then often has to be aborted or unstable components are created. Particularly when high-quality filaments such as carbon fibres are printed, this wear-related waste is expensive and must be avoided at all costs. In addition, changing nozzles is time-consuming as the printer platform needs to be completely recalibrated, time that can be saved with Dianoz. “Since we have got to know the Gühring nozzle, there are no more 10-euro nozzles on the printers in our production facilities, which means no more constant replacement. Whether I’m printing a standard material or a highly abrasive filament: The nozzle can do both very well, so I don’t just save myself a few nozzle changes a year, but also the time and frustration involved,” says Reil enthusiastically. He also recommends the Dianoz nozzle as an upgrade for his customers’ printers. “The nozzle is a good fit with my approach to giving the customer the best possible solution.”
You might also be interested in:
Combating wear with diamond: Magnesium machining in e-mobility
A customer encounters wear problems in the production of magnesium parts for electric motors: With special diamond tools, Gühring increases the tool life from weeks to a year. This saves the company time and money.
Universal talent for aluminium: The new PCD Diver
Maximum machining rates and neverending tool lives in aluminium: The new PCD Diver from Gühring promises both. Thanks to its innovative geometry, the tool guarantees top quality with low power consumption and high stability.
Be it ceramic or carbide: Diamond nozzle has been printing without wear for three years
AIM3D encountered a problem when 3D printing with carbide: The nozzles only lasted for a short time. A new diamond nozzle from Gühring changed everything.