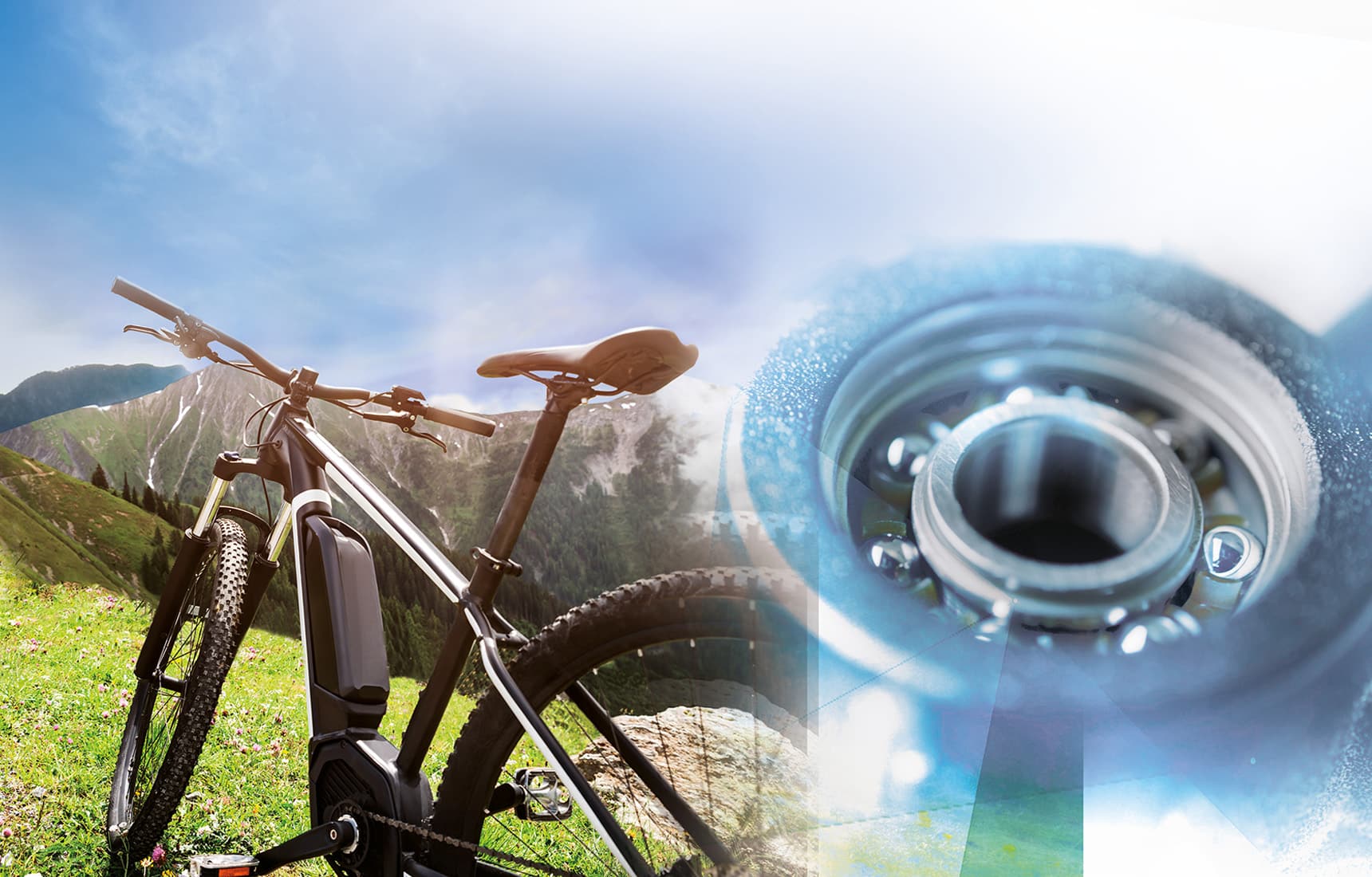
Contents
1. Wear due to magnesium dust
2. Gühring delivers the special solution
3. Ready for the future
4. The machining process in detail
A customer encounters wear problems during the production of magnesium parts for electric motors: Fine magnesium dust affects tools and surfaces. With special diamond tools featuring intelligent geometry optimisation, Gühring dramatically increases tool life: from weeks to a year. Dynacast saves costs and time, while Gühring demonstrates its expertise in the special field.
All you hear is the chirping of the birds and the noise of the electric bike on the trail. When cycling in nature, one thing is extremely annoying: engine noise. To avoid this, the manufacturing of components in electric motors requires the highest precision – and this in series production. At 1,000 units per week, stable processes are essential.
With around 450 employees at its Austrian location south of Vienna, Dynacast manufactures parts made of die-cast zinc, magnesium and aluminium. Dynacast parts are used in industries where precision, durability and lightweight construction are critical. “That’s why high quality is so important”, says Markus Beier, Production Manager at Dynacast. This also applies to housing parts for electric motors the size of an A4 sheet. The focus is on lightweight construction – a trend that relies on special materials such as magnesium. But casting and machining magnesium is challenging, especially when large batches of more than 1,000 pieces per week are produced, as is the case with Dynacast.
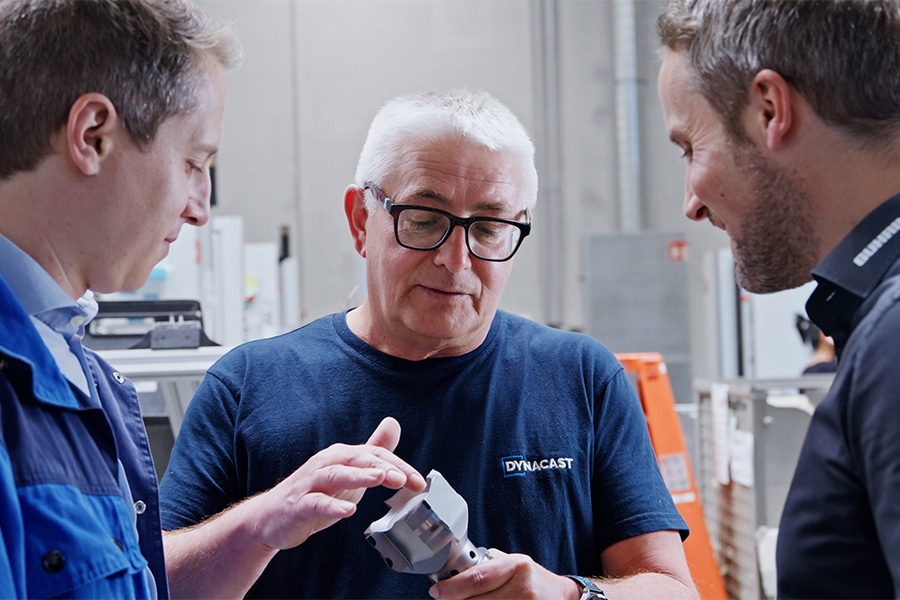
This is where stable processes are fundamentally important. The good thing is that Dynacast has a strong partner at its side: “Ever since we have been manufacturing magnesium housings, we have been working with Gühring”, notes Markus Beier. “Whenever we have a problem, Gühring is there and we tackle the issue together.”
Wear due to magnesium dust
This was also the case when Dynacast reached its limits when machining a stator hole on an electric bike motor housing. The die-cast part made of magnesium was pre-cast close to the final shape. Despite the stock removal of only approx. 1 mm per side, the wear on the PCD reamer was enormous: “For some tools, it only took us two to four weeks to send them for refurbishment”, recalls Markus Beier. “Such short tool lives are not satisfactory for us.” The wear also affected the surfaces on the stator bore. When looking into the machine, the reason was also quickly found: A white construction film was visible in the machine area and on the tools. After investigations at the University of Leoben, it was determined that this was magnesium dust.
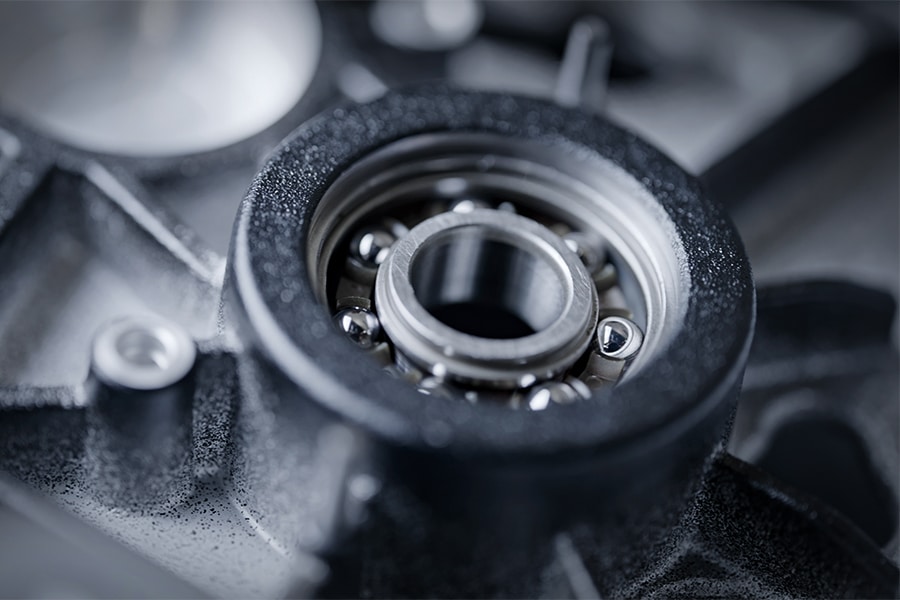
This microdust is released during machining and deposited everywhere – including on the cutting edges of the PCD reamers. Here, the fine dust particles acted like small sand grains that rub the material off the cutting edges. As a result, the otherwise wear-resistant PCD cutting edges rounded off within a very short time, which is why the tool lives were significantly shorter than planned: After about 150 m, it was already over. In addition, this wear on the cutting edge generates such a high cutting pressure that the diameter in the component was 0.1 millimetres smaller than the diameter on the reamer.
Gühring delivers the special solution
A special solution was needed here and Gühring was able to deliver this thanks to its high level of expertise in the special field. “In two optimisation rounds, we converted the tool in such a way that its geometry counteracted excessive wear”, explains Matthias Helbig, Application Manager for E-Mobility at Gühring. Instead of developing completely new tools, the aim here was to conserve resources so that the basic body of the reamers could be reused. The solution is a wear compensation cutting edge: Five adjustable cutting edges can be moved via an expansion joint. This means that the customer can quickly and easily readjust the diameter if the diameter falls below the specified value.
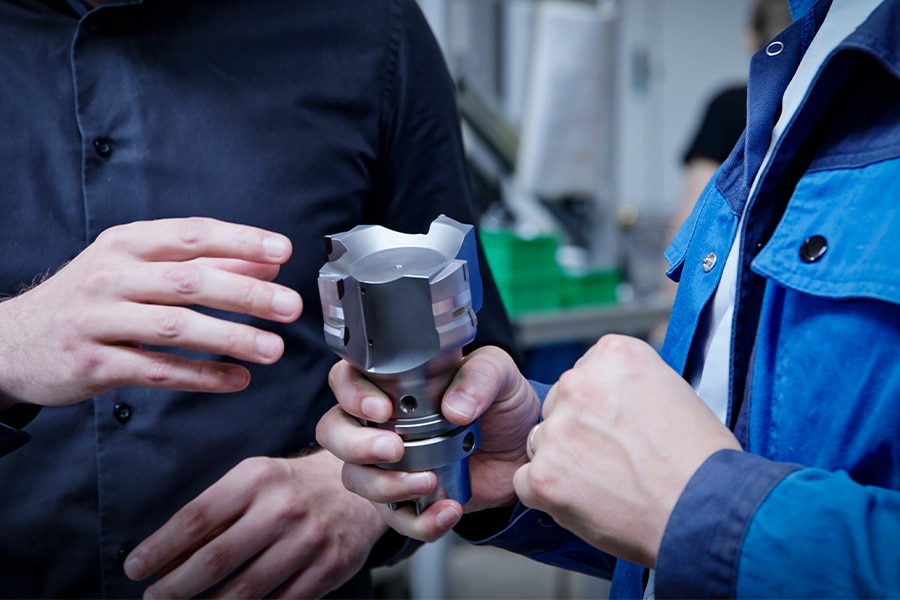
Ready for the future
The result is impressive: “Thanks to the joint development, we have managed to get to a tool life of around twelve months from two to four weeks”, says Markus Beier happily. “And this improvement in tool life has had a very positive impact on us financially.”
This improvement in tool life has had a very positive impact on us financially.
Because Dynacast now has massive savings in tool costs and saves machining time thanks to fewer tool change cycles, the company’s manufacturing can be much more cost-effective. In addition, the revised Gühring tools ensure greater process reliability and consistently high quality. Thanks to this success, Markus Beier has a positive outlook on the future: “I believe Dynacast will remain a major player in the housing market because we are far from finished with our innovations and die casting technology.” He wants to continue working closely with Gühring in the future, because “this collaboration has proved to be very fruitful so far, and together we have developed great ideas and technical solutions.”
The machining process in detail
Information on the machining setup:
- horizontal machining centre, 2 machining spindles
- tool holder HSK-A 63
- Cooling: external emulsion cooling
- workpiece clamping: 2 clamping positions
Cutting data:
Werkzeug |
PCD reamer (special tool), Ø 90.05 mm, 5+1 teeth, adjustable via expansion slot |
Material | Magnesium AZ91 |
Speed | n = 2.475 rpm |
Feed rate | vf = 1.190 mm/min |
Cutting speed | vc = 700 m/min |
Feed per revolution | Fu = 0.48 mm/rev |
Machining time | t = 1.2 sec/component |
Tool life | 4.500 m |
Technical advice and support are also available quickly and directly via our service hotline 00800 2607 2607. We can also be reached on WhatsApp: +49 172 658 53 53. Save the number!
You might also be interested in:
Diamond nozzle: 50 kg Carbon – limitless printing
CR-3D is a leading complete supplier in the field of additive manufacturing and develops and produces all necessary components for 3D printing in industrial environments. Gühring supplies the heart of this type of machine: the diamond printer nozzle.
Universal talent for aluminium: The new PCD Diver
Maximum machining rates and neverending tool lives in aluminium: The new PCD Diver from Gühring promises both. Thanks to its innovative geometry, the tool guarantees top quality with low power consumption and high stability.
Be it ceramic or carbide: Diamond nozzle has been printing without wear for three years
AIM3D encountered a problem when 3D printing with carbide: The nozzles only lasted for a short time. A new diamond nozzle from Gühring changed everything.