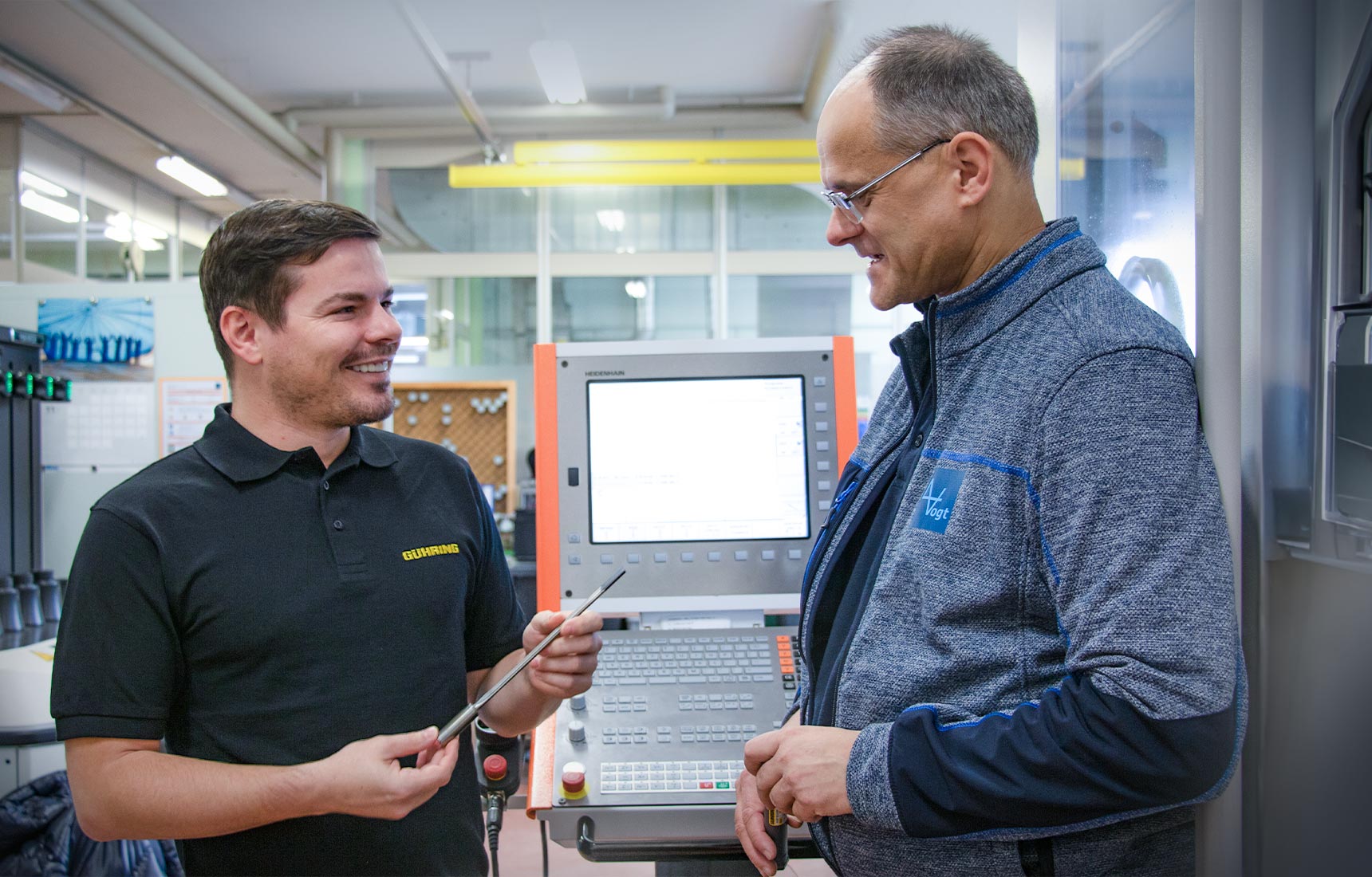
Table of contents
1. From the steel block to form insert
2. Top tools for hard machining
3. Process cut by three weeks
Competitive pressure in the mould and die sector is forcing Vogt AG to evolve. By using hard machining techniques, the company is significantly reducing its lead times. Tools from Gühring play a decisive role in this process by offering innovative solutions for machining hardened steel. As a result, Vogt has managed to shorten its manufacturing processes by three weeks while improving the quality and accuracy of the manufactured parts.
Speed is important in all industries, but the competitive pressure and thus the time pressure are especially great in mould and die. Vogt AG Verbindungstechnik, which specialises in the manufacture of punched and plastic parts as well as fine tube and wire articles for the electrical industry, is experiencing this too. The company produces over two billion parts a year in Lostorf, Switzerland (canton of Solothurn), including standard items and custom-made products.
Vogt AG also manufactures the injection moulding tools and fixtures for the production of these articles within its own toolmaking – at least in part. Previously, all components were soft-machined, then externally hardened and finally finished at Vogt AG. However, this approach led to very long throughput times. “Our main goal was to shorten this throughput time and reduce the effort involved in reworking”, explains Ronny Herrmann, who heads toolmaking at Vogt AG.
“Our main goal was to shorten this lead time and reduce postprocessing effort.”
His vision is to make everything – from the hardened blank to the finished injection moulding tool – in-house and in one process step. This would save the company weeks in toolmaking and enable them to start producing the actual products sooner. “If the complete machining is done as hard machining, this is a higher expense, but the processing times are shortened overall”, says Rolf Ehler, Product Manager for Milling Tools at Gühring.
From the steel block to form insert
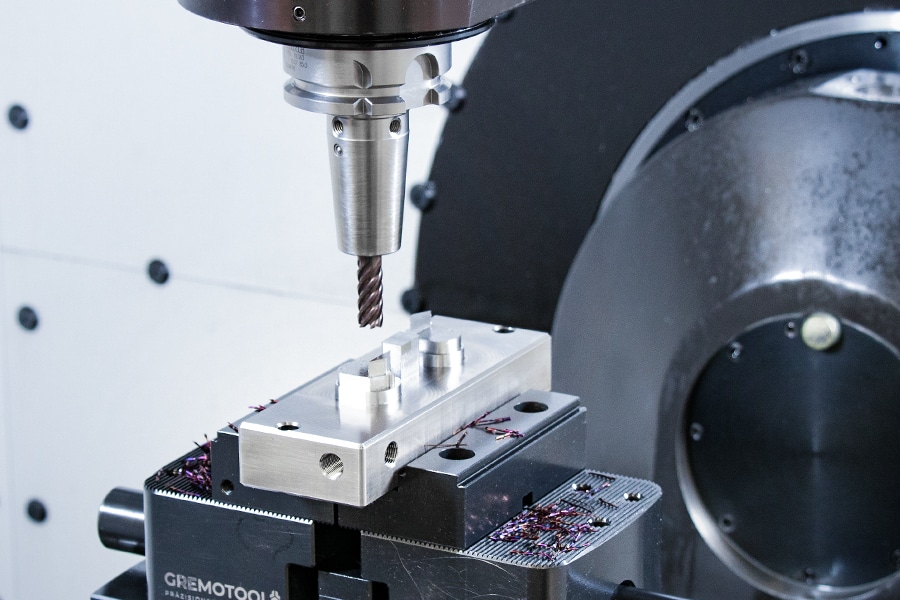
Vogt AG is perfectly equipped for this with a modern 5-axis milling centre and automation. But turning a hardened steel block with a hardness of 54 HRC into a finished mould insert for an injection moulding tool is only possible with high-performance tools. So when Ronny Herrmann learned from his Gühring sales representative about the new G-Mould range – a milling cutter range specially for mould making – he was all ears. The new tool range has been specially designed for applications in tool and mould making and offers innovative solutions especially for hard machining.
Gühring does not only supply the right tools for this purpose, but also always a functioning process including cutting data. Rolf Ehrler and Ronny Herrmann put together all the necessary tools for machining and discussed the machining strategy and possible problems during the production of the mould insert. For example, the machinists faced challenges with two deep drilled holes with an eight-millimeter diameter and a depth of 137 millimeters as well as several deep and narrow cavities.
Top tools for hard machining
Vogt AG relies on a milling cutter from the new Gühring mould making tool range for roughing the pockets and slots in the form insert: The G-Mold 65 U solid carbide end mill is the perfect choice for this type of component with hardnesses up to 65 HRC and is used here in the 12 cm diameter design. Even deep and narrow cavities are no problem for the four-fluted ratio end mill, which has a neck clearance. It also gives Vogt AG a real time advantage, as the tool is particularly suitable for dynamic GTC milling with low lateral infeed. Its special flute profile with a strong core increases stability, while a particularly hard Signum coating ensures temperatureresistant performance and longer tool lives.
Tool | G-Mold 65 U, Art-Nr.: 6944 12,000 |
Material | Hardened steel (1.2347), 54 HRC |
Feed | Fz = 0.06 mm |
Cutting speed | Vc = 120 m/min |
Cutting depth | ap = 17.0 mm |
Lateral infeed | ae = 0.6 mm (0.05xD) |
Speed | n = 3180 U/min |
Feed rate | Vf = 760 mm/min |
The cooling holes in the form insert are made precisely with the EB 100 single-fluted gun drill with a diameter of eight millimeters. The powerful tool effortlessly masters this drilling process to the desired depth of 137 mm and is characterised by particularly tight drilling tolerances. This performance results from the optimal combination of carbide, geometry and the high-quality SuperA coating, making the drill ideal for demanding hard machining. The solid carbide design of the EB 100 reduces tool vibration while ensuring excellent stability during the drilling process. The brazed version of the EB 100 offers outstanding concentricity values.
Tool |
Solid carbide deep hole drill EB 100 Art. no. 5638 8.000. flute length 160 mm |
Material | Hardened steel (1.2347), 52-54 HRC |
Feed | Fz = 124 mm |
Cutting speed | Vc = 20 m/min |
Feed rate | F = 0.008 mm/U |
Gühring tools were also used for milling the M6 fastening threads and for hard reaming. These tools had very long tool lives and surface finishes.
Process cut by three weeks
By manufacturing its tools and moulds in hard machining now, Vogt AG was able to significantly reduce the throughput time and thus shortened the process by as much as three weeks. In addition, there are no entire process steps, such as grinding in reworking. The time saving in subsequent, cost-intensive process steps is also particularly relevant. This means that the effort required for countersink eroding is significantly lower, because Gühring tools enable pre-milling close to the contour during hard machining. Thanks to Gühring, Vogt was even able to improve the quality and accuracy of the component – an important aspect, because only a perfectly manufactured mould insert can ultimately produce high-quality products.
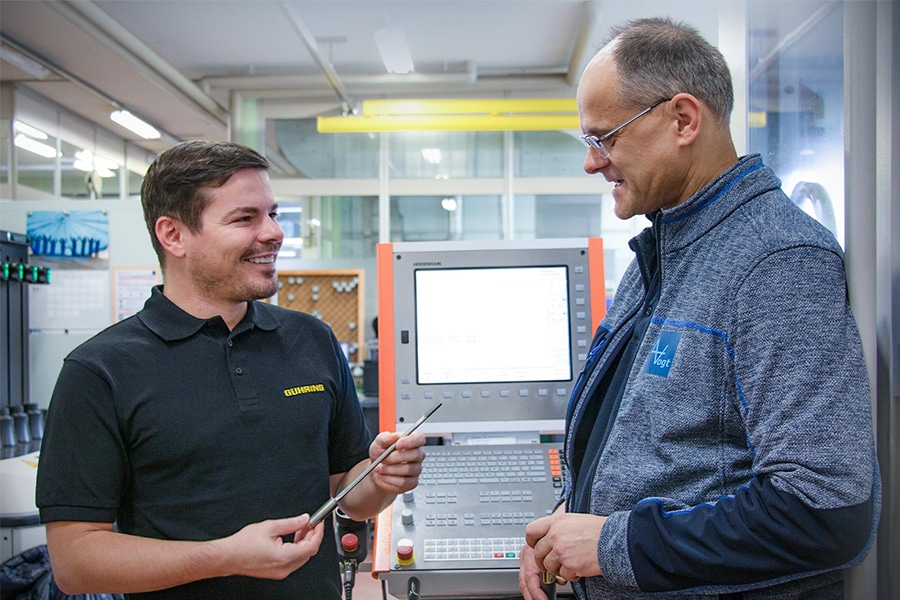
Albert Kodraj (Gühring) und Ronny Hermann (Vogt).
For Ronny Herrmann, the hard milling pilot project fully met all expectations, and one thing is clear to him: “Hard machining will be expanded even further in the future, and Gühring will continue to be our partner in tool procurement.” The project showed that “as a tool manufacturer with a great deal of expertise, Gühring also offers solutions for problems one does not encounter everyday.”
Technical advice and support are also available quickly and directly via our service hotline 00800 2607 2607 We can also be reached on WhatsApp: +49 172 658 53 53. Save the number!
You might also be interested in:
Finger on the pulse: Pocket milling in grade 5 titanium
A customer uses grade 5 titanium to make the case for pacemaker batteries, but machining the material is challenging. Gühring has the solution: The G-Mold 65 HF solid carbide end mill enabled it to extend the tool life 73 times over.
Fast and dynamic: Trochoidal milling in mould making
One milling strategy has proven to be particularly successful for mould making, where sometimes very hard materials have to be machined in the shortest possible time: GTC milling. This form of trochoidal milling results in particularly long tool lives during machining.
Cross holes? Not a problem! With the right deep drilling strategy
The machining of intersecting deep holes can be tricky: This is because the cooling process is interrupted, creating an adverse spot drilling or guidance situation. Gaps can only be bridged with the right strategy.