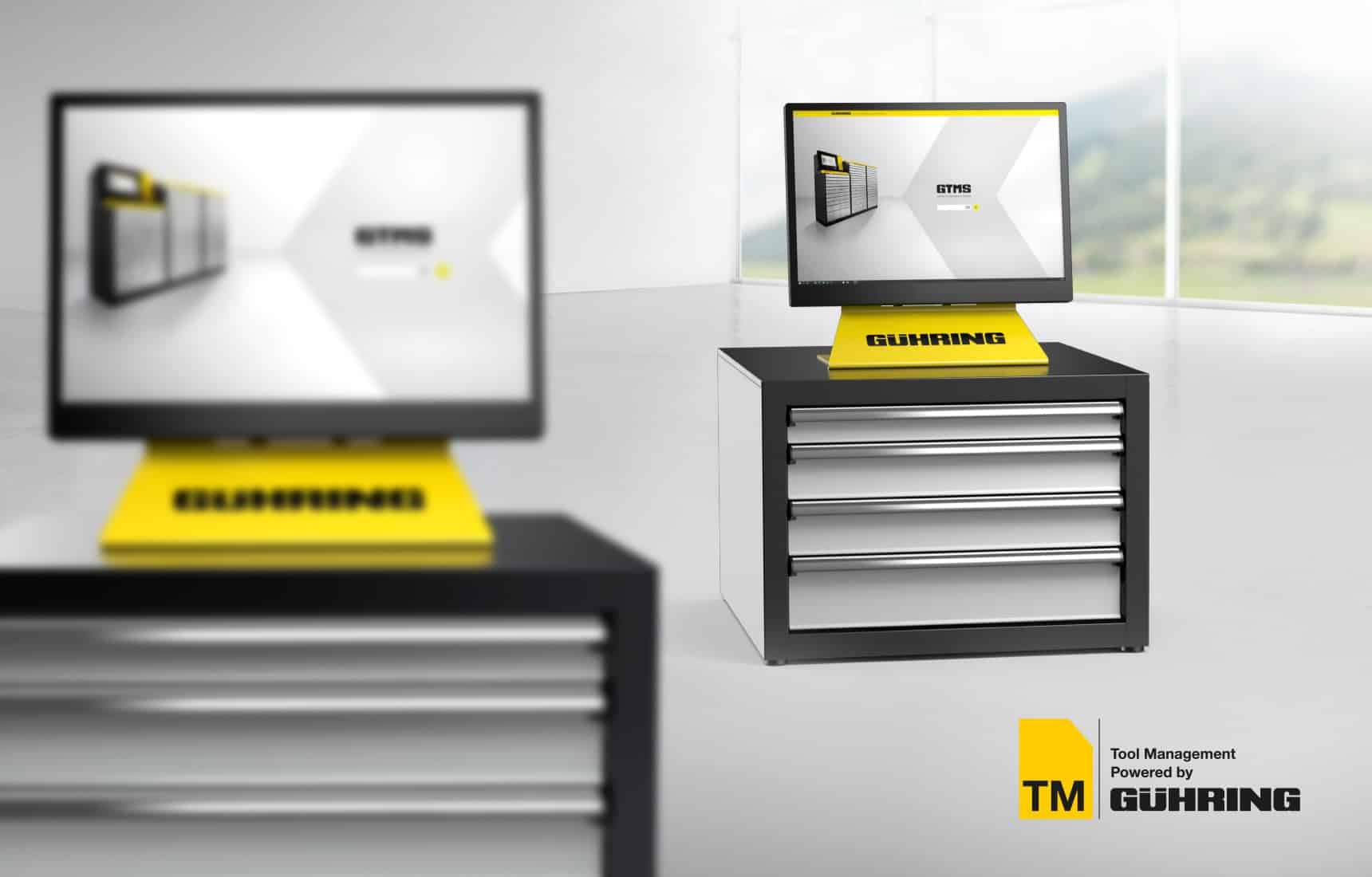
Inhalt
1. For small operations and large series production: How to use the Minibox in manufacturing
1a. Advantages of the Minibox for tool management
2. Equipment: Software and hardware for digital tool management
2a. Keep track with our software
2b. Technical details for the tool cabinet
3. FAQs: The most important questions on the topic of tool management
TM cabinets from Gühring offer simple solutions for managing tools. The new TM Minibox now expands the cabinet portfolio and makes tool management even more flexible. With the compact box, you always have the tool to hand wherever you need it. And the pre-installed logistics software digitalises the most important processes in your manufacturing.
For small operations and large series production: How to use the Minibox in manufacturing
When it comes to large series manufacturing where numerous machine lines are controlled by software such as Gühring Tool Management Software (GTMS), an efficient system has proven successful: A central warehouse with a large TM cabinet manages and maintains all data. At the same time, tools are also managed on a decentralised basis: at the machine, exactly where they are needed. The new Minibox is perfect for this: Using its touch monitor the machine operator records the booking directly in GTMS. Small companies also benefit from the Minibox. The entry-level model is a simple way to start using digital tool management. Tools and accessories always close at hand – the Minibox makes this possible.
Advantages of the Minibox for tool management
- Electronically locked drawers for controlled dispensing
- Function to book removals & returns directly from the TM Minibox
- Tool movements and storage locations can be fully tracked
- Ability to keep an eye on tool stocks and reorder automatically
- Reduction of travel times thanks to compact, decentralised storage units on the machine
Equipment: Software and hardware for digital tool management
Keep track with our software
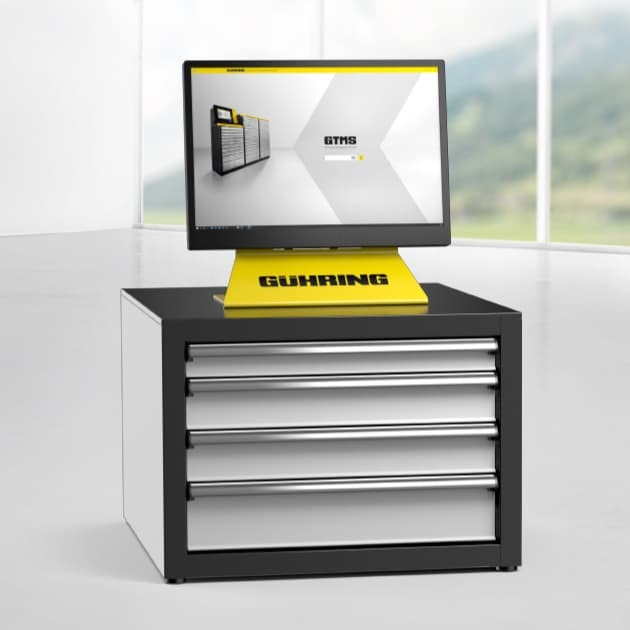
When you purchase a TM Minibox, you also receive the GTMS Basic logistics module as standard. As a result, our software supports you in managing your master data, creating evaluations and handling intralogical processes cleanly:
- Manage master data: User data, cost units, partners & suppliers, article data
- Book tool movements
- Manage inventory
- Deal with the order process
- Evaluate logistics data: Booking data, inventory overview, a number of individual reports included, data export
GTMS Basic, which is located on the cabinet system, can be set up individually and expanded with additional modules.
Technical details for the tool cabinet
The Minibox has four drawers with front heights of 60 cm, 90 cm and 120 cm. Just like its “big brothers”, the drawers of the Minibox can be locked and unlocked electronically.
Basic technical data
Weight | 75 – 95 kg (depending on equipment) |
Width | 630 mm |
Depth | 700 mm |
Height | 880 mm |
Load capacity | 75 kg / drawer |
Electrical connection data
Operating voltage | 110 – 230 V AC at 50 / 60 Hz |
Power consumption | 250 W |
Back-up fuse | 16 A | FI / LS max. 30 mA |
Have we piqued your interest?
More information about the new TM Minibox can be found in our data sheet.
FAQs: The most important questions on the topic of tool management
Gühring tool management: What is tool management?
With digital tool management, you can optimise the storage, refurbishment and use of tools in manufacturing facilities. This offers companies many advantages, such as cost savings resulting from more efficient use of tools or faster production processes from minimised machine downtimes.
What is tool management in the manufacturing industry?
Tool management is the systematic organisation, tracking and management of tools and operating resources in manufacturing to minimise downtimes and maximise productivity.
How can tool management help to reduce costs?
Targeted tool management can reduce replenishment times, optimise inventory levels and avoid unnecessary purchases, leading to significant cost savings.
What are the biggest challenges in tool management?
Challenges include optimum tool procurement, the safeguarding of tool quality and adjustment to changing production requirements.
How do you measure the success of tool management?
Success can be measured using KPIs such as tool availability and the reduction of machine downtimes.
You might also be interested in:
Test equipment management: Software stays on top of measuring equipment
Wherever components are manufactured with high precision, regularly calibrated measuring instruments are essential. This company has switched to digital measuring equipment management with GTMS – and is saving itself a lot of time as a result.
6 reasons why your production needs a tool management system
Searching for tools takes an incredible amount of time. All tools have their place in our tool management cabinets. Tidy, locked, with controlled dispensing. In this article, you will find out how to revolutionise your production and save costs.
Hand over your Tool Management to us!
Our tool managers take care of your tool management, including logistics, procurement and scheduling. They also uncover optimisation potential that can reduce tool variety as well as process and tool costs – for additional efficiency in your business.