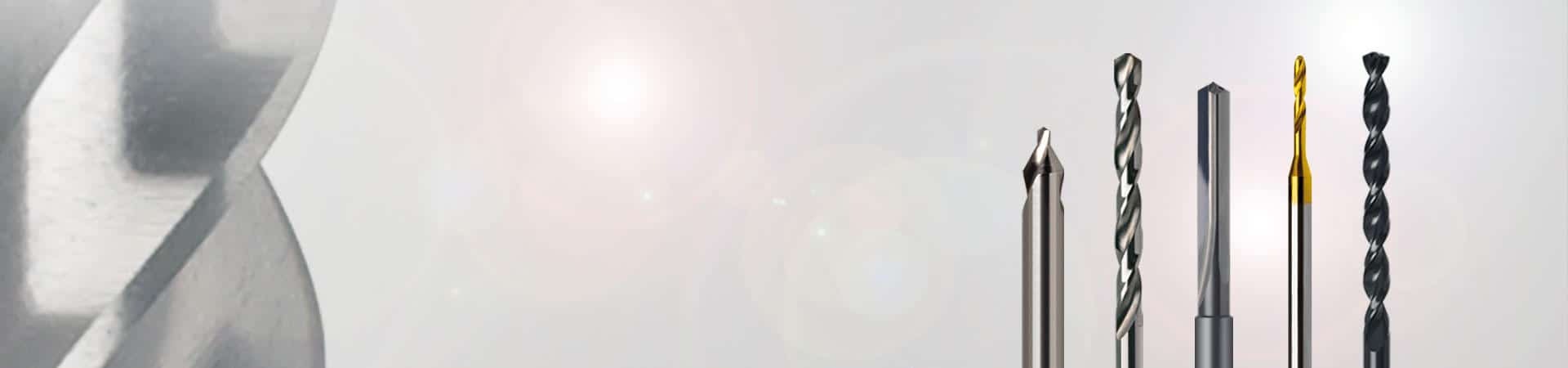
Drills – drilling tools
Sophisticated drill technology
Gühring produced the first HSS drill in 1898 and has remained true to its beginnings. Our variety of drilling tools is unparalleled on the market. The product portfolio ranges from the smallest 0.05 mm diameter to special solutions with a diameter of 180 mm, from HSS to solid carbide or PCD.
Metal drills – we set standards for the future
With over 600 patents worldwide, Gühring is a key driver of innovation in the field of metalworking. Ever more high-performance materials and complex components require increasingly efficient tools to meet the extreme demands of machining.
Downloads / Links
General Catalogue
BT 800
RT 100 InoxPro
RT 100 XF – Machining of steel materials
GU 500 – Universal drill
HT 800 WP – Interchangeable inserts drilling system
StepPower – Drilling by hand
BT 800
RT 100 InoxPro solid carbide drill
RT 100 XF solid carbide drill
GU 500 universal drill
FB 200 U flat drill
To our product highlights
What drills are available?
Gühring produced the first HSS drill in 1898 and has remained true to its beginnings. Our variety of tools is unparalleled on the market. The range of drilling tools includes the following types of drills:
- HSS and solid carbide twist drills
- Step drills, core drills, countersinking drills and countersinks
- Centre drills and NC spot drills
- Micro drills with diameters up to 0.05 mm
- Deep hole drill for diameter/length ratios up to 80xD
- Interchangeable insert drilling systems
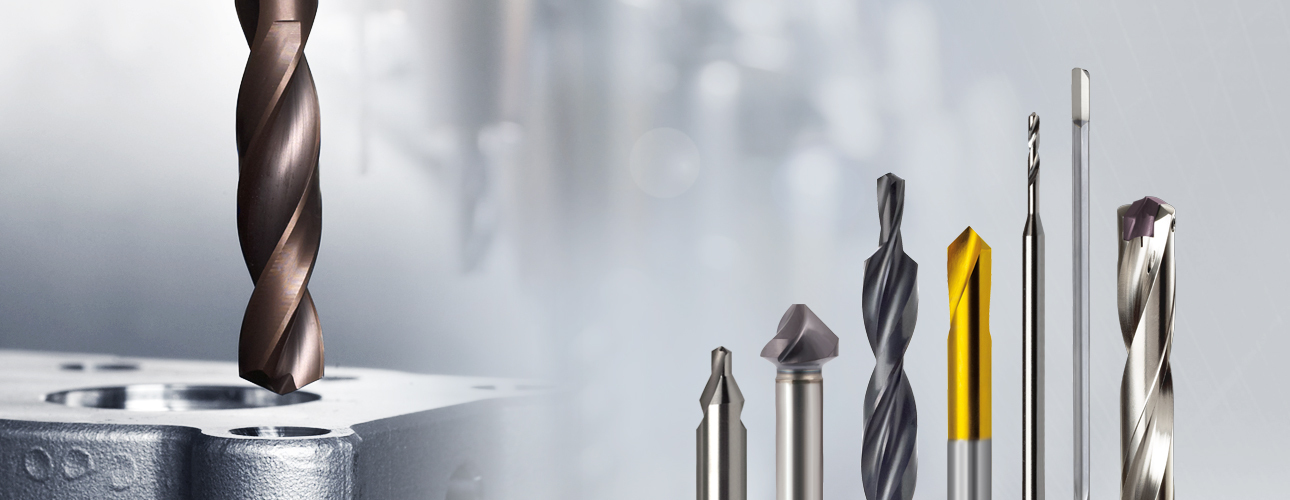
Identifying metal drills: How do I recognise a metal drill?
Steel drills are twist drills and are sometimes referred to as spiral flute drills. The front of the drill is tapered with two sharp cutting edges. A characteristic feature of steel drills is the sharp tip, which can easily drill through metal. The spiral flutes run out up to the shank to remove the chips.
Which drills are suitable for stainless steel?
Type VA solid carbide or HSS drills are used for machining tough materials such as stainless steel. Gühring offers a material specialist here: The RT 100 VA solid carbide drill with a 140° point angle and 30° helix angle. Tools with adapted geometry are used to machine stainless steels, which reduce temperature development and also generate short chips in these long-chipping materials. Solid carbide drills with a suitable hard material coating should be used for optimal results.
Which drill is suitable for hardened steel?
Hardened steel is steel that is heated to a temperature of 750 to 1050 °C to increase its mechanical resistance. We recommend using a solid carbide drill with Signum coating, such as the RT 100 HF Ratio drill from Gühring.
The microstructure of the Signum coating is characterised by extremely fine TiAlN nanocrystals embedded in a glass-like, high-temperature-resistant silicon nitride matrix. This results in a high hardness.
Grinding drills
The manufacturing process for drills also includes grinding the cutting edges. The cutting edge microdesign indicates whether the cutting edge is sharp (jagged) or rounded under the microscope. High-quality drills avoid cutting edge roughness, thus increasing their stability and surface finish quality. Procedures for cutting edge preparation include: Wet blasting, micro blasting, drag finishing and robotic brushing.
Would you like to find out more about drilling and the drilling tools from Gühring?
The Gühring Academy offers comprehensive knowledge from the world of metal machining.
The online learning units are prepared in a practical and interactive manner and can be accessed online around the clock.
Twist drill
What are twist drills?
Twist drill is a generic term for various types of drills, such as metal drills, plastic drills, wood drills, universal drills, masonry and concrete drills. All twist drills have a common characteristic: The helical flutes that give the drills their name. Different twist drills are used depending on the hardness of the material to be machined. These can be divided into three types of twist drill.
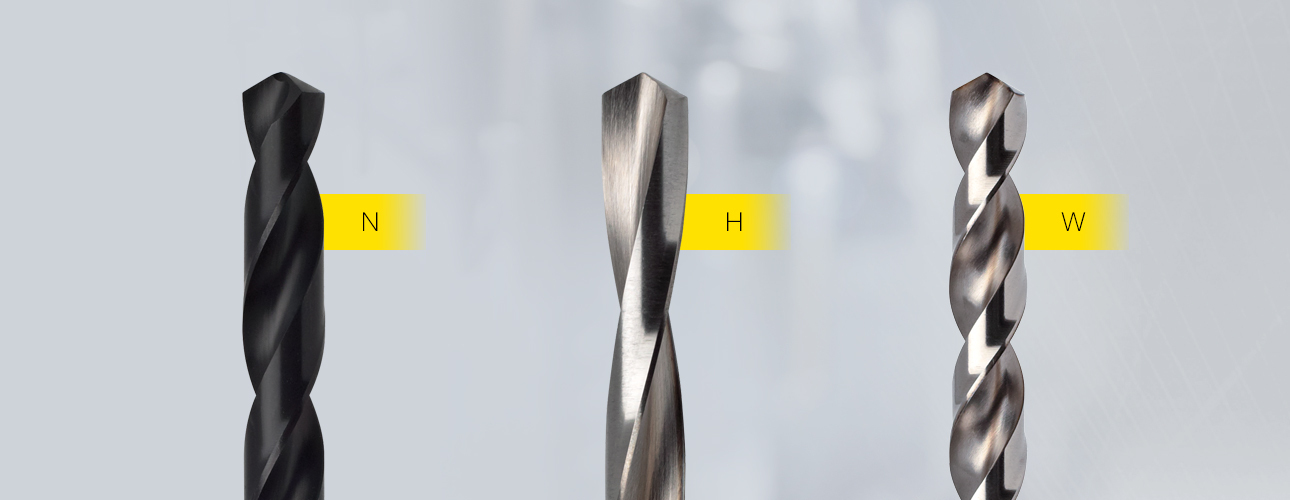
Typ N | Typ H | Typ W |
---|---|---|
|
|
|
What are the advantages of the twist drill?
The design of the twist drill offers several advantages: The guide chamfer ensures good guidance of the drill on the workpiece, providing additional stability. The drill can be easily centred thanks to its favourable cutting angle. Chip removal takes place automatically with the twist drill and is supported by the supply of cooling lubricant through integrated coolant ducts in some cases. The twist drill can also be reground several times. Find out more about tool refurbishment.
Clearance angle twist drill
The angles between the workpiece and the cutting edge influence the machining process and vary depending on the material to be machined. A distinction is made here between the clearance angle (alpha), the wedge angle (beta) and the rake angle (gamma). The clearance angle is ground on the tool to enable cutting to take place at all and is therefore decisive for maximum feed. It also influences the friction between the clearance rake area of the cutting wedge and the cut surface of the workpiece. A small clearance angle is suitable for hard and short-chipping materials, such as high-alloy steel.
Grinding the twist drill
The enormous range of materials to be machined requires a wide variety of point grinds.
With form A, the transverse cutting edge is sharpened to reduce the axial forces. This means that the transverse cutting edge is reduced at defined angles in additional operation with a grinding disc.
Form B is suitable for long-chipping materials such as structural steel and high-strength steel. It is a combination of form A and a main cutting edge correction. The positive rake angle is corrected and the cutting wedge is ground “blunt”. This increases resistance to chips when drilling into solid material. Chip packages form on the corrected surface, which are broken and transported away via the flutes.
Form C corresponds to split point grinding. In this type of grinding, two surfaces are ground to each other so that they cross in the area of the transverse cutting edge. This ensures excellent centring properties and lower feed forces. This means that the split point grinding can be used to create more precise hole diameters and a perfect round hole.
Form D is a combination of form A and an additional point angle, which is usually 90°. It removes the cutting corner, creating two new, less sharp cutting corners. This makes the tool less sensitive to shocks and increases its tool life. This grinding is mainly used in metal processing for grey cast iron, malleable iron and forgings.
With form E, a so-called centring point is ground. This geometry offers excellent centring properties and an accurate bore with low burr formation. This grinding is used for thin-walled workpieces, sheets and soft materials.
Twist drill set
Twist drill sets from Gühring are available in different versions and with different surface treatments. For installers and craftsmen, sets with the most common drill dimensions are available, which can be supplied with Bakelite stands and cassettes.
Solid carbide drill
What is carbide?
Carbide is a sintered material, which means that it has been heated under pressure. It is a mixture of various carbides and cobalt. This is why we also use the term sintered carbide metals.
Uses of the carbide drill: Where is carbide used?
Carbide is mainly used as a cutting material for tools such as drills, lathe tools and milling tools. Due to the increased cutting values, tool life and improved drilling quality, carbide tools are ideal for series and large-scale production on CNC machines with stable clamping. However, the purchase price for carbide tools is significantly higher than for HSS tools. Carbide is therefore not always the most economical solution for machining. High-speed steel tools are particularly preferable for use in unstable conditions and with small batch sizes.
What is a solid carbide drill?
With solid carbide drills, the tool body and cutting edges are made of different cutting materials. With a solid carbide drill, on the other hand, the manufacturer produces the entire tool from carbide. Solid carbide drills are suitable for particularly demanding machining tasks where high wear resistance and efficiency are required. The production of a perfect solid carbide drill starts with the composition of the cutting material. That’s why Gühring manufacture their own carbide.
Product highlights solid carbide drill
RT 100 XF solid carbide drill
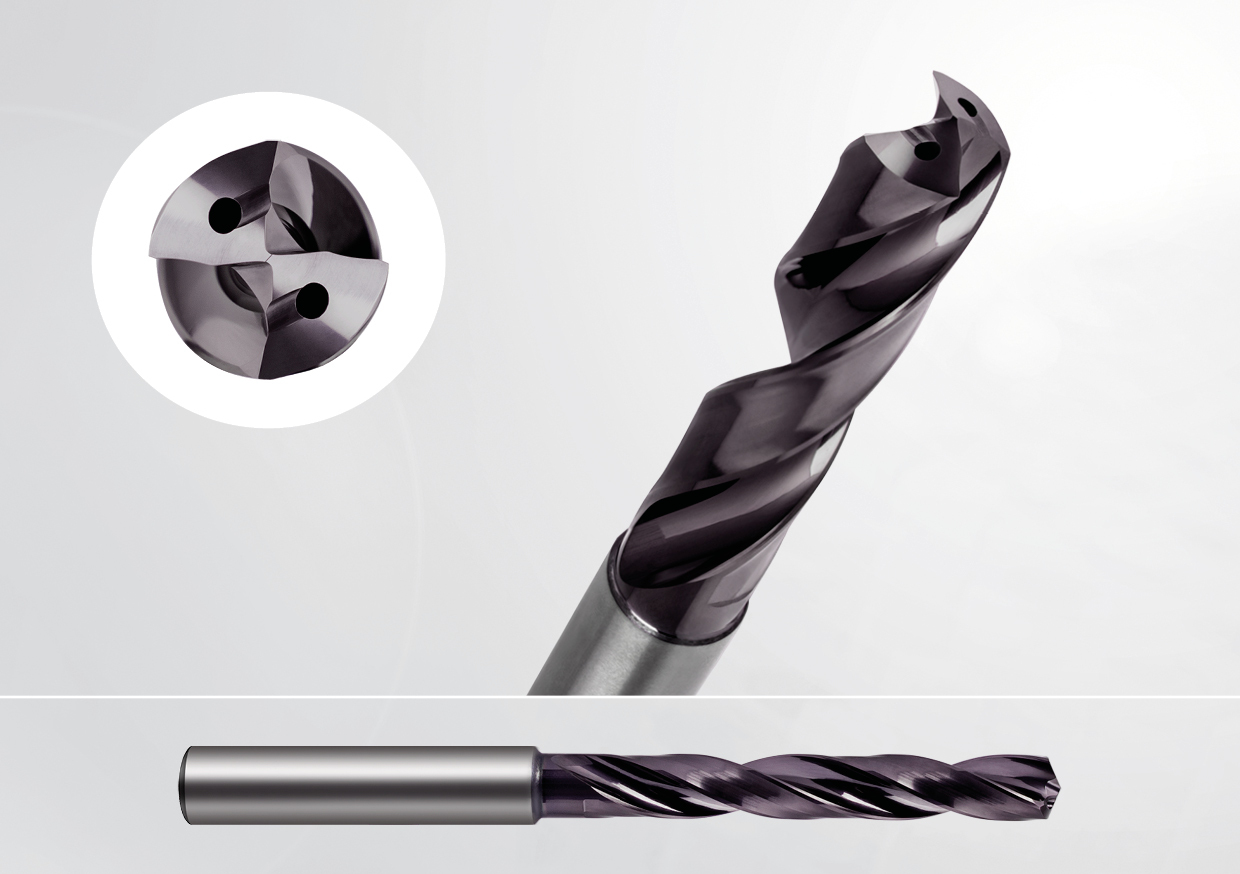
The RT 100 XF impresses with extreme performance, flexibility and a wide range of applications. In our standard range, it is the tool for outstanding machining performance.
Your advantages with the RT 100 XF:
- Optimisation of all tool parameters for extreme feeds and incredible removal rates
- Maximum performance utilisation thanks to in-house high-end finishing
- Shortening of cycle times in series production, even for materials that are difficult to machine
RT 100 U universal drill
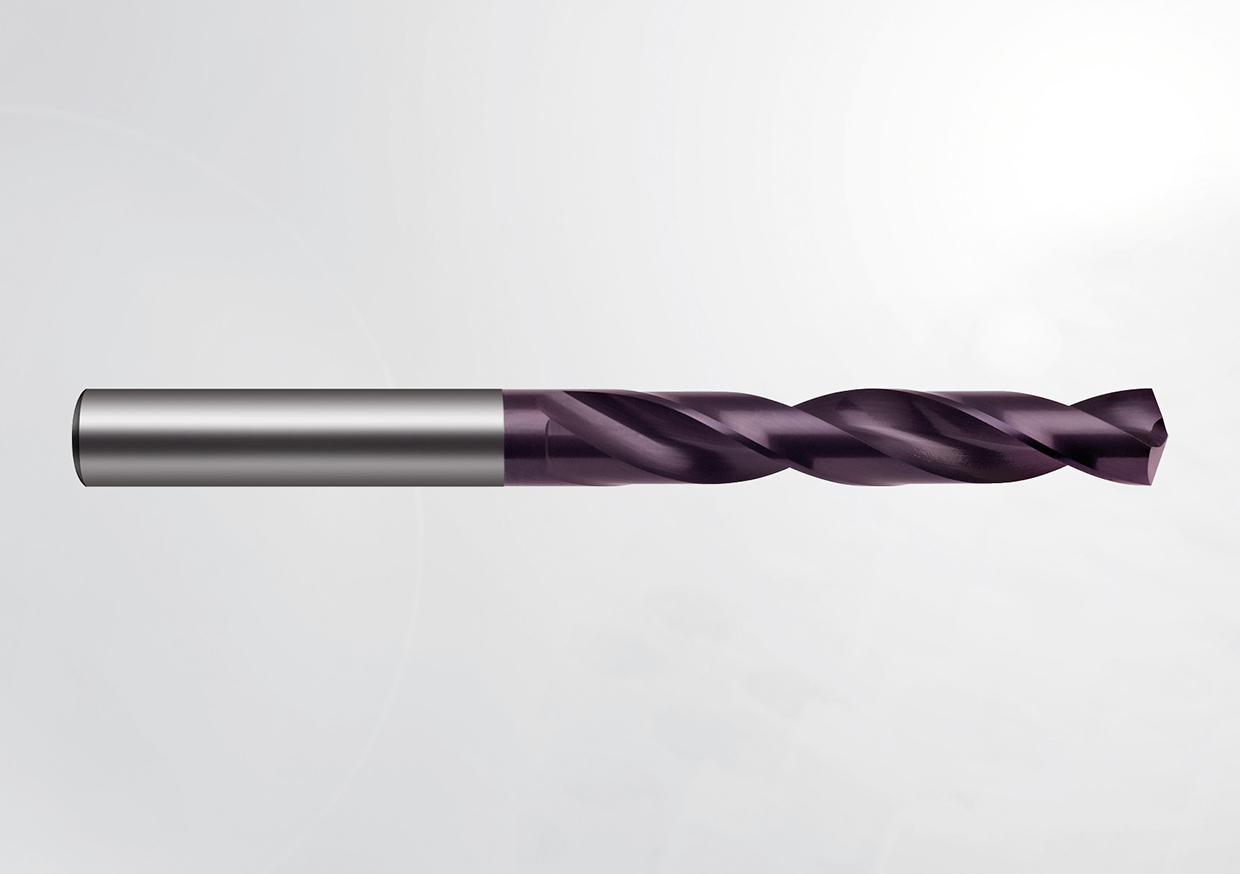
RT 100 U universal drill – the Gühring all-rounder for steel drilling
The universal RT 100 U is ideal for processing steels up to approx. 1400 N/mm², short and long-chipping materials as well as high-alloyed and stainless steels. The Ratio drill can deliver the highest cutting data and generate short chips.
Your advantages with the RT 100 U:
- Optimised cutting edge geometry for high performance
- Precise alignment of holes thanks to it’s special point thinning and 2-facet point grinding
- Excellent self-centring thanks to 140° point angle
RT 100 T deep hole drill
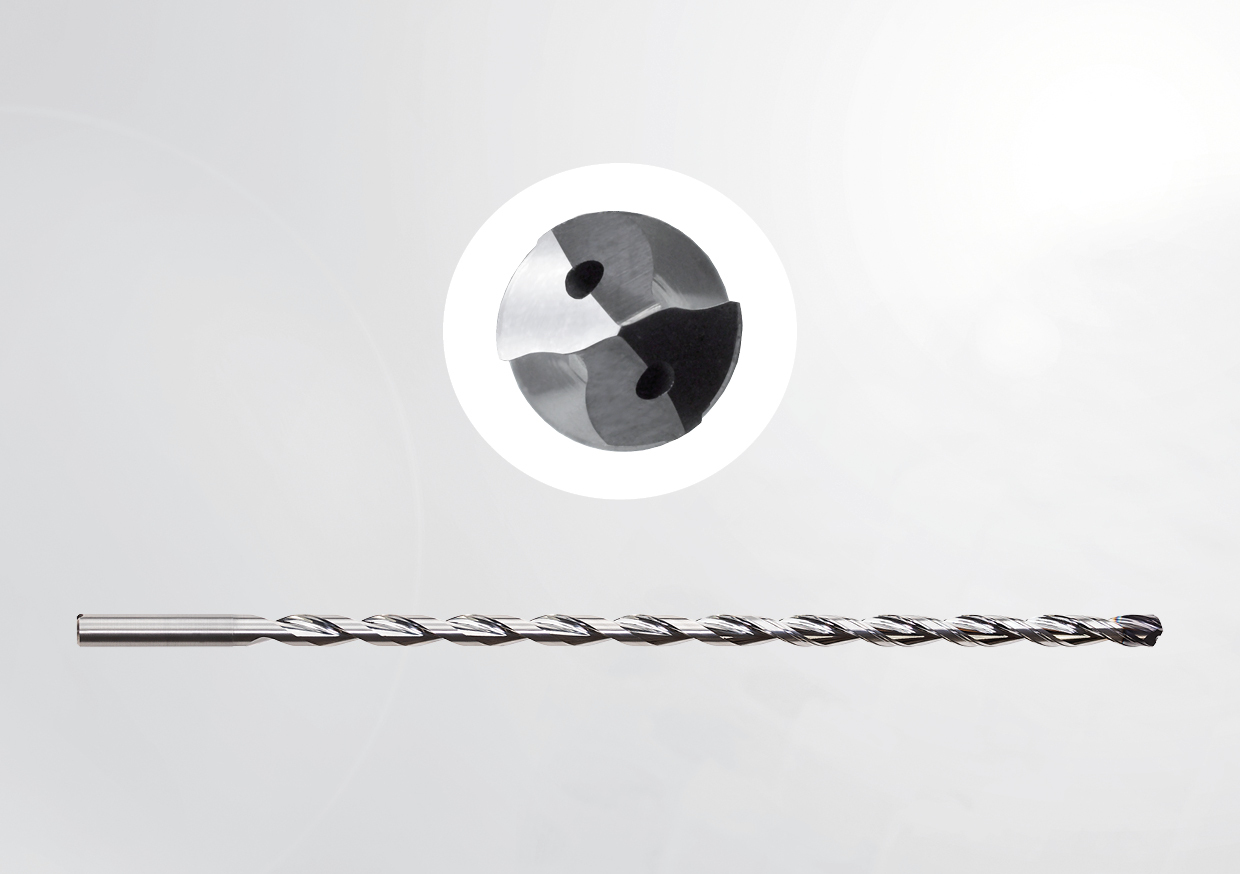
RT 100 T deep hole drill – for the highest demands on the smallest holes
With the RT 100 T standard range, Gühring offers an extensive range for deep drilling up to 40xD. The solid carbide high-performance drills offer maximum cost-effectiveness and efficiency for your production processes and are also available as a special solution for individual requirements.
Your advantages with the RT 100 T:
- Safe chip removal thanks to specially adapted flute geometry
- Optimum supply of lubricant to the cutting edges thanks to maximum cross section of the coolant ducts
- Effective wear protection: head coating with the Gühring A layer (TiAlN)
- Shortest processing times due to high feed rates
Find out more: Deep hole drilling
RT 100 T in the online shop
EB 100 M single-fluted deep hole drill
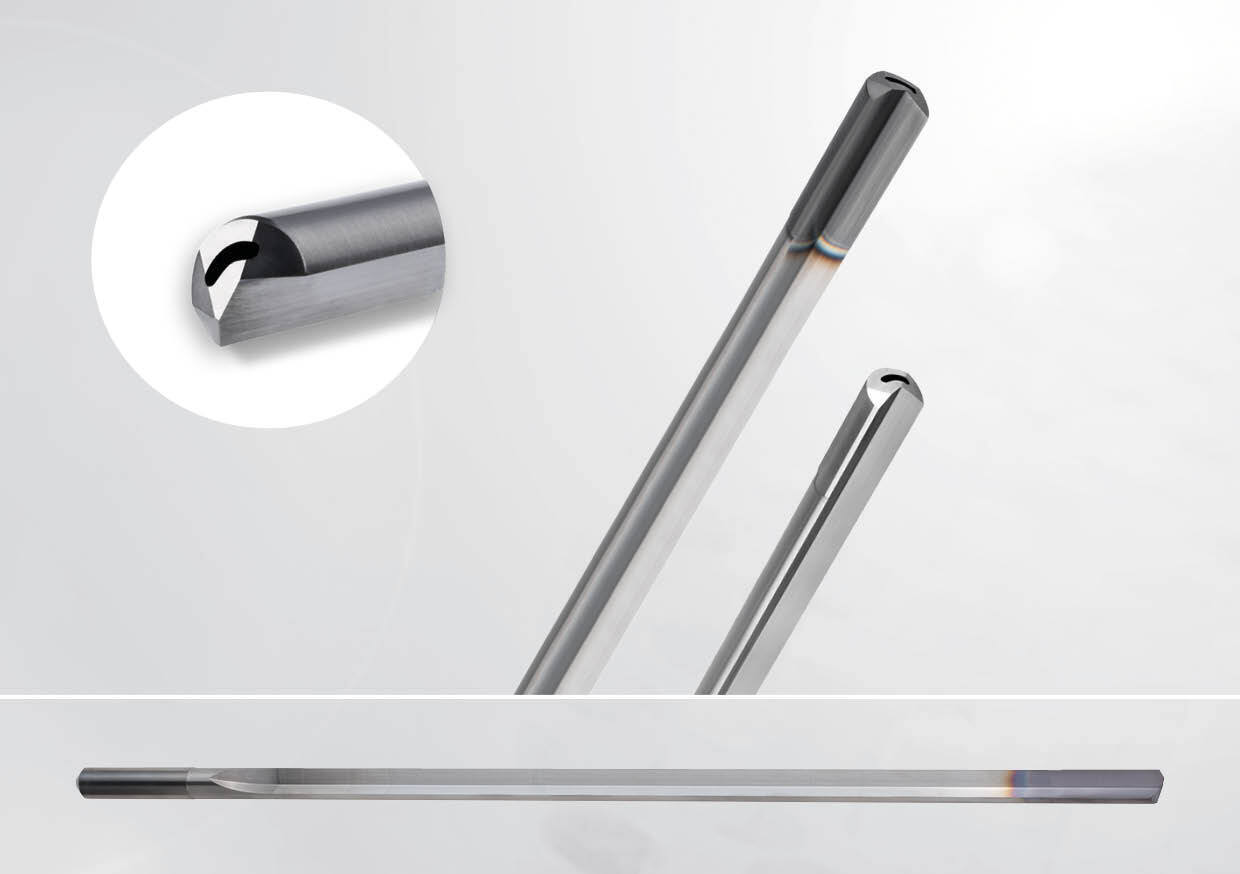
EB 100 M single-fluted deep hole drill – monolithic for more performance
The EB 100 M is the perfect choice for deep hole drilling with particularly tight drilling tolerances. Gühring does not use a solder joint in the design, which gives the tool greater stability. This means that up to 30 percent higher feed rates are possible with the robust drilling tool.
Your advantages with the EB 100 M:
- High-quality solid carbide version: suitable for almost all materials
- Deep hole drilling up to 80xD possible with just one tool
- MQL shank end ensures reliable lubrication
Find out more: Deep hole drilling
EB 100 M in the online shop
HSS drill from Gühring
Conventional, but essential: The HSS/HSCO drilling tools
Carbide or HSS drill? The skills of the cutting materials are clearly distributed – and carbide has by no means been able to win over all application areas as a cutting material for drilling tools. Especially in small and medium series production, in unstable machining conditions and whenever toughness is required, users still rely on high-speed steel (HSS/HSCO) drilling tools. With an enormous range of products and an exceptionally high degree of vertical integration, the HSS/HSCO drilling tool products area from Gühring is unparalleled worldwide. Gühring has been manufacturing HSS drills since 1898 and continues to do so to this day.
What are HSS drills?
HSS drills are steel drills that are characterised by their universal application possibilities. Especially in small and medium series production, in unstable machining conditions and whenever toughness is required, users still rely on high-speed steel (HSS/HSCO) drilling tools.
Differences in HSS drills
High-speed steel is divided into different quality levels depending on the hardness and toughness. Alloy components such as tungsten, molibdenum and cobalt are responsible for these properties. Increasing alloy components increases the tempering resistance, wear resistance and performance of the tool, as well as the purchase price. This is why it is important to consider how many holes are to be made in which material when choosing the cutting material. For a small number of holes, the most cost-effective cutting material HSS is recommended. Higher-quality cutting materials such as HSCO, M42 or HSS-E-PM should be selected for series production.
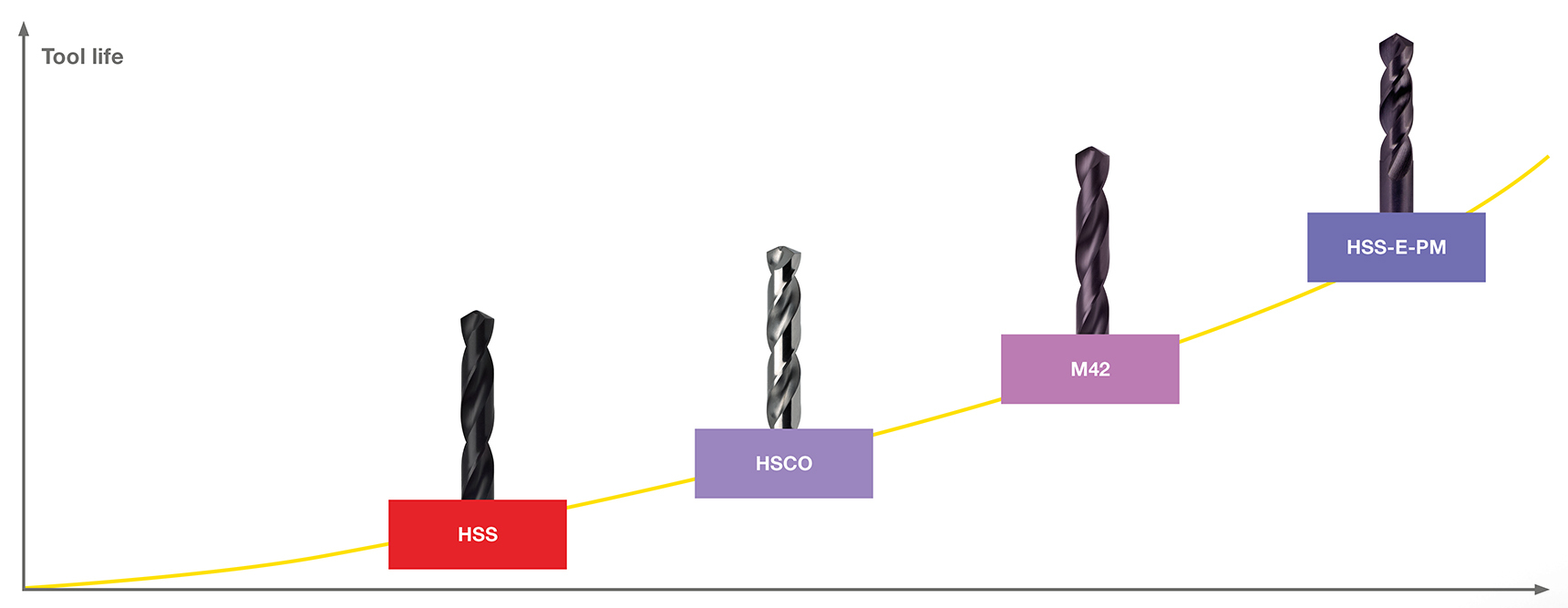
HSS grade | HSS | HSCO (also HSS-E) | M42 (also HSCO8) |
PM HSS-E |
---|---|---|---|---|
Description | Conventional high-speed steel | Cobalt alloyed high speed steel | 8% cobalt alloyed high speed steel | Powder metallurgically produced high-speed steel |
Composition | Max. 4.5% cobalt and 2.6% vanadium | Min. 4.5% cobalt or 2.6% vanadium | Min. 8% cobalt | Same ingredients as HSCO, different production |
Use | Universal use | Use for high cutting temperatures/unfavourable cooling, stainless steel | Use with difficult-to-cut materials | Use in series production and for high tool life requirements |
How are HSS drills manufactured?
Depending on the type of production, a distinction is made between roll-forged twist drills (HSS-R drills) and twist drills with a ground drill point (HSS-G drills). A HSS-G drill is ground from the solid material. HSS-G drills enable higher accuracy and more precise working with lower tolerances than HSS-R drills.
Gühring tools for special applications
Gühring’s portfolio includes a variety of different drilling tools. This also includes step drills, centre drills and countersinking drills, which are outlined in more detail below.
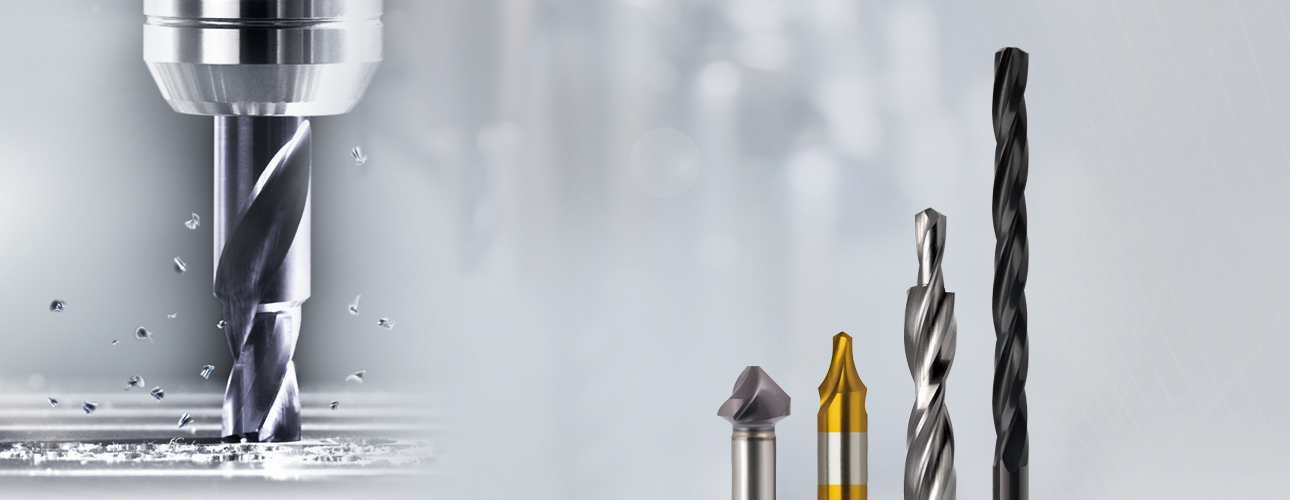
What step drills does Gühring offer?
HSS step drill / Gühring step drill
Gühring manufactures high-quality step drills from high-speed steel (HSS). This high-alloy tool steel has high wear resistance and ensures precise and cost-saving drilling.
Gühring offers numerous steel drills in different versions. A distinction is mainly made here between the two centring forms D and DR in accordance with DIN 332. In addition to the standard option “bright” surface, there is also the option of surface treatment “steam-treated” for wear-reduced drilling. Gühring step drills are available with cylindrical shanks and Morse tapers for clamping into standard drill chucks.
Why step drilling?
Step drills are often used in metalworking for drilling screw head counterbores and tapped core holes with counterbores. They are also suitable for stepped holes with high surface finish qualities.
With a step drill, several machining steps can be combined in one and bores with two or three diameters can be drilled in a single operation which saves on tools. A major advantage of the step drill compared to drills is the saving of operations and tools.
Centre drill
What are centre drills?
Centre drills are profile drills which create locating holes for turning or grinding between centres. Centre drills are often made of high-speed steel (HSS). The geometry of these drills is characterised by the short projection length and the stepped profile. At the front, the additional centring point, which also forms the nominal diameter of the tool, ensures a high centring in the bore.
How does a centre drill work?
The locating holes have high accuracy requirements. The centre drill can reduce the runout of the drill with its short tool length and small centring point for better positioning accuracy.
Countersinking drill
What are countersinking drills?
Countersinking is used to deburr bores, i.e. the sharp protrusion on the surface of the workpiece is removed. Screw heads are also countersunk with a countersink. Countersinking drills usually have a countersink angle of 60, 75, 90 or 180 degrees. They are available with or without guide pins. Typically, countersinks have three or more cutting edges.
What countersinking drills are available?
Countersinking tools are divided into:
- Countersinks
- Flat countersinks or face countersinks
- Profile countersinks
Core drill
Core drill: What is a core drill?
Core drills are used to enlarge pre-drilled, punched or cast holes to the desired finished dimension. Core drills can also be used to improve out-of-roundness, misalignment or surface defects in the drilled hole. Core drills therefore optimise the initial bore. If the hole is then to be machined with a reamer, core drills ensure the necessary size.
Gühring core drills
Gühring offers a wide range of core drill tools for machining different materials, with Gühring core drills designed as type N. The type N cutting wedge is versatile due to its helix angle of approx. 30°.
Micro drilling tools
Microprocessing is becoming increasingly important in all industries, from medical technology to the high-tech industry. Drilling is a key part of this. The smaller the components become, the higher the demands on the precision, repeatability and cost-effectiveness of the process.
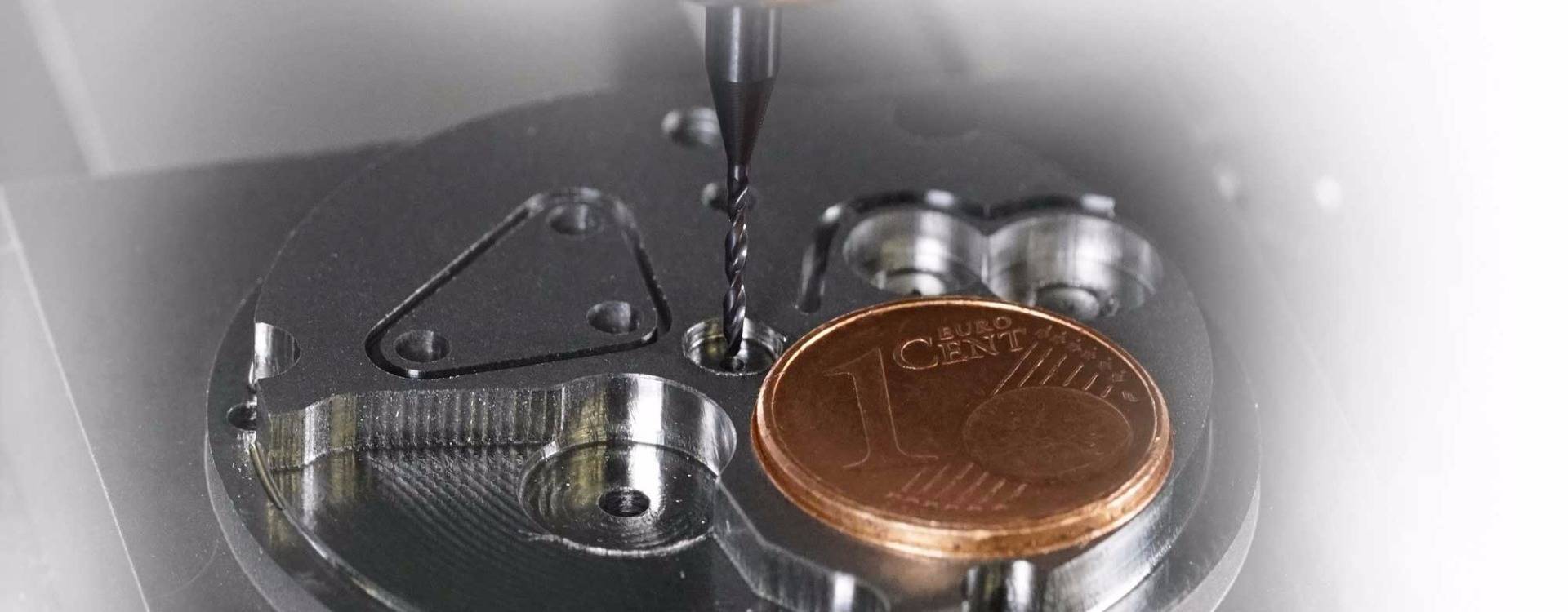
Solid carbide ExclusiveLine micro-precision drills
also with internal cooling
The solid carbide ExclusiveLine micro-precision drills, with and without IC, enable high-performance machining of almost all materials. The tools are available with internal cooling from a diameter of 1.00 mm and without internal cooling from a diameter of 0.50 mm. There are two types to choose from: A universal variant with maximum performance in steel materials and a type VA, specifically for machining stainless steels, special alloys and titanium. The application-specific point geometry, high-end coatings and the right carbide selection ensure the highest performance in terms of cutting values and tool life.
- For maximum performance with the highest cutting values and tool life
- Specialist for use in steel materials
- Type VA special geometry for use in stainless steels, special alloys and titanium
- Internal cooling from diameter 1.00 mm
Application example 1:
Series production
Material: Alloyed case hardening steel 16MnCr5
Internal cooling with 8% emulsion
- d = 2,5 mm
- Vc= 120 m/min
- n = 15.279 rpm
- fn= 0,14 mm/rev
- Vf= 2.139,06 mm/min
Application example 2:
Series production
Material: Stainless steel X6CrNiTi18 10
Internal cooling with 12% emulsion
- d = 1,5 mm
- Vc= 80 m/min
- n = 16.980 rpm
- fn= 0,045 mm/rev
- Vf= 764 mm/min
Solid carbide micro-precision drill
Gühring solid carbide micro-precision drills without coolant ducts cover the diameter range from 0.1 mm to 3.0 mm. With the solid carbide micro-precision drills, extremely good cutting parameters and long tool life can be achieved under stable machining conditions and high machine performance. Among other things, the use of ultra-fine carbide, which offers extremely high hardness and heat resistance as well as extreme wear resistance, enables the outstanding performance of the solid carbide micro-precision drills.
- For stable machining conditions
- Higher cutting parameters and tool life
Application example:
Series production on rotary transfer machine
Material: Quenched and tempered steel 42CrMo4
with external cooling 10% emulsion
- d = 1,2 mm
- Vc = 65 m/min
- n = 17.242 rpm
- fn= 0,06 mm/rev
- Vf = 1.035 mm/min
HSS-E-PM micro-precision drills
The Gühring HSS-E micro-precision drills made of high-performance powder metallurgical HSS-E steel are characterised by very high wear resistance and high toughness and cutting edge stability, this is particularly important in unstable machining conditions. The powder metallurgically manufactured HSS-E steel has a very homogeneous microstructure, which has a positive effect on the consistent high performance of the micro-precision drills.
- More reliable machining in unstable machining conditions with this HSS-E drill
- Wear-resistant HSS-E-PM and high cutting edge stability
Application example:
Series production on multi-spindle machines with HSS-E drills
Material: Stainless steel 1.4301
with external cooling 10% emulsion
- d = 2,0 mm
- Vc= 15 m/min
- n = 2.387 rpm
- fn= 0,03 mm/rev
- Vf= 71,61 mm/min
Benefits and areas of application
Gühring offers the optimal solution for series production of large batch sizes in machine conditions with the highest performance and internal cooling, as well as for machining tasks with smaller batch sizes or with limited machine performance and difficult machining conditions.
Program scope
The comprehensive Gühring micro-precision drill range, consisting of solid carbide and HSS-E-PM micro-precision drills, covers the entire diameter range from 0.05 mm to 3.0 mm in the HSS range and from 0.10 to 3.00 mm in the solid carbide range. The tools are available in lengths from 3xD to 15xD. Tools with internal cooling are available in the standard range from a diameter of 1 mm.
Interchangeable insert drilling systems for steel processing
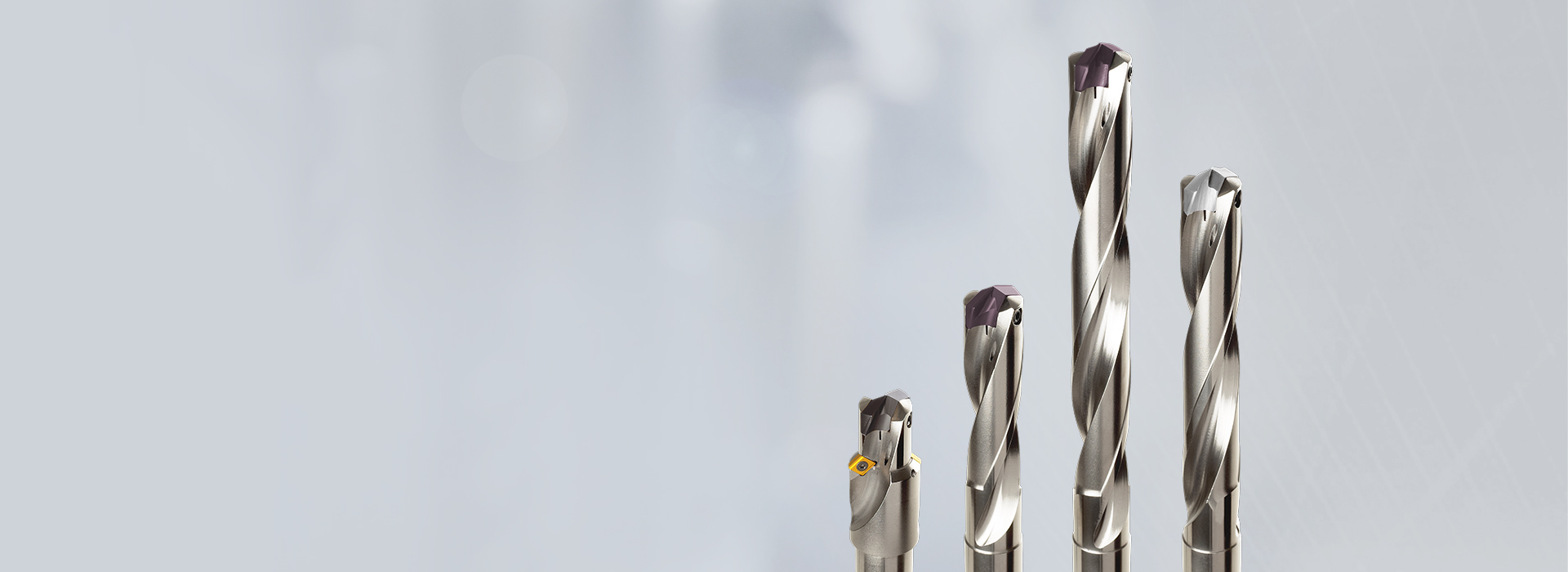
HT 800 WP for machining steel beams
Steel beams are usually prepared for assembly on special drilling/sawing machines. The clamping conditions on these machines are usually unstable. This places particularly high demands on the drilling tools. Gühring offers interchangeable inserts that are specially designed for processing steel beams. The point geometry of these indexable inserts ensures optimum centring properties and thus compensates for the unstable machining conditions. The high point angle in the outer area of the indexable inserts guarantees minimised burr formation.
Gühring has also expanded its range of indexable inserts for machining C-steels. Their stable cutting wedge ensures high wear resistance without increasing the process forces. The concave-shaped cutting edge ensures optimal chip breakage of long-chipping steels.
These carbide special drilling tools are based on the HT 800 WP tool system. The HT 800 consists of a wear-resistant steel beam, the replaceable cutting body and a locking screw with clamping principle. Thanks to the pin and fitting hole, the interchangeable insert has minimal play and sits firmly in the carrier. The innovative clamping principle achieves the highest process reliability for holes up to 10 x D. The modular system makes it easy to change inserts directly in the machine. There is no need to change tools or reconfigure the machine afterwards.
The cutting material, geometry and surface of the interchangeable inserts are perfectly matched to the respective area of application. This means that the HT 800 achieves holes of the same quality as a solid carbide drill with an optimised flute profile. The indexable inserts can be used in the standard holders 1xD, 1.5xD, 3xD, 5xD, 7xD and 10xD. In the diameter range from 26.00 to 40.00 mm, the inserts can also be reground.
Interchangeable insert drilling systems for steel processing
Gühring has also expanded its HT 800 range for machining C-steels. The stable cutting wedge of the special indexable inserts ensures high wear resistance without increasing the process forces. The concave-shaped cutting edge ensures optimal chip breakage of long-chipping steels.
The indexable inserts delivered remarkable results:
- Market segment: Automotive
- Component Bushing
- Drilling depth: 24 mm, through-hole
- Diameter range: 19.5
- Material: C40
- Tool life: 6000 holes
- Tool life: 144 m
- Cutting speed Vc: 120 m/min
- Feed per revolution f: 0.35 mm/rev
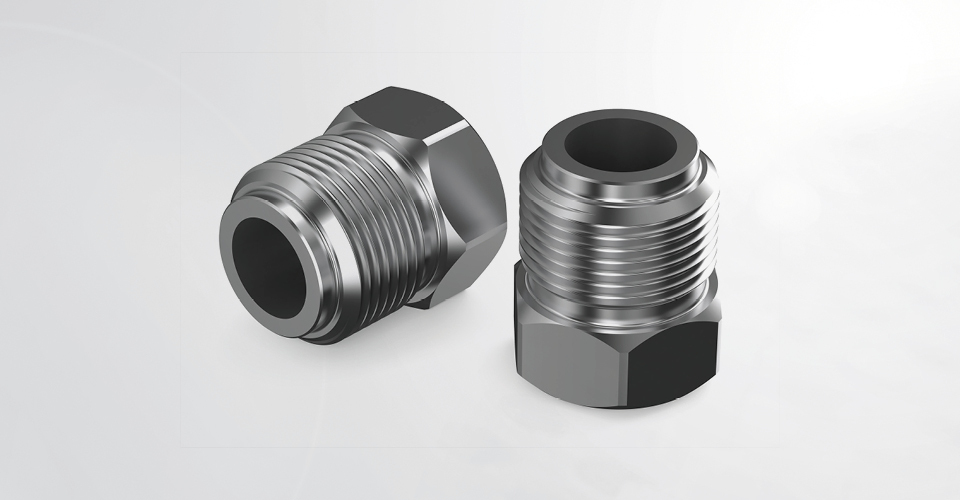
The HT 800 consists of a wear-resistant steel beam, the replaceable cutting body and a locking screw with clamping principle. Thanks to the pin and fitting hole, the interchangeable insert has minimal play and sits firmly in the carrier. The innovative clamping principle achieves the highest process reliability for holes up to 10 x D. The clamping screws with screw lock improve the grip, even during machining with high vibration loads.
Indexable insert drill
Indexable insert drills consist of a base body made of tool steel with chip surfaces and flutes as a holder for one or more interchangeable indexable inserts.
Carbide inserts
In the case of interchangeable inserts, the carrier/holder is made of a soft, inexpensive material and the insert is made of carbide. This is particularly worthwhile for very large drilling diameters. Indexable inserts are clamped or screwed into a tool holder for use in metal machining. They usually have several cutting edges. If a cutting edge wears out, the insert is simply rotated.
How are carbide cutting inserts manufactured?
Indexable inserts are manufactured using a sintering process. In this process, carbide powder is pressed into shape and heated to approx. 1500 degrees Celsius, which melts the powder into carbide. After sintering, the geometry and size of the indexable insert are determined in a grinding process. Finally, the indexable inserts can be coated with different coatings.
CLAMPING SYSTEM
Precision is setting-up matter
REAMERS
Perfect reaming in all diameters
COUNTERSINK TOOLS
Quick, clean & fully automated deburring